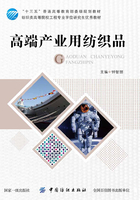
第二节 过滤与分离用纺织品工艺技术与专用设备
一、水刺耐高温过滤材料工艺与设备选择
采用两层梳理纤网与中间网格基布复合制得最终复合纤网,具体生产工艺流程如下:

水刺加固工艺是依靠高压水,经过水刺头中的喷水板,形成微细的高压水针射流对托网帘或转鼓上运动的纤网进行连续喷射,在水针直接冲击和反射水流作用力的双重作用下,纤网中的纤维发生位移、穿插、相互抱合,形成无数的机械结合,从而使纤网得到加固(图4-7和图4-8)。

图4-7 实验用水刺机实物图
水刺工艺是一种机械加固方式,水针直接冲击使表层纤维发生位移,相对垂直朝网底运动,当水针穿透纤网后,受到托网帘或转鼓表面的阻挡,形成水流的反射,呈不同的方位散射到纤网的反面(图4-9)。

图4-8 实验用水刺机结构图

图4-9 水刺加固原理图
水刺头是水刺非织造工艺中产生高压集束水针的关键部件,它由进水管腔、高压密封装置、喷水板和水刺头外壳等组成。高压水就是通过喷水板上的微孔向纤网喷射,使纤网得到加固。喷水板是一块长方形金属薄片,根据水刺头结构尺寸设计。喷水板上喷水孔的结构对水针集束性有很大的影响,选择良好的喷水孔结构,可减少水针的扩散程度,使水针能量集中,提高效率。
二、针刺过滤材料生产工艺
针刺过滤材料生产工艺一般流程如下:
纤维开松、混合→纤维梳理→成网→预针刺→主针刺→后整理→成品
针刺过滤材料生产工艺主要包括五个方面,分别是纤维开松、混合,纤维梳理,铺网,针刺加固,后整理。纤维开松、混合工序使压紧的纤维变得蓬松,并将不同批次的纤维混合均匀,除去一部分杂质,使纤维尽量成单纤维状态。纤维梳理将经过开松、混合好的纤维梳理得平行顺直,加工成薄薄的纤网。成网包括机械梳理成网和气流成网。将梳理后的纤网,经过铺叠交叉后,供针刺机加固。针刺加固包括预针刺、主针刺。预针刺是将蓬松的纤网初步加固使纤网的尺寸稳定,具有一定强力;主针刺是将预针刺过的纤网进一步加固,达到设定的强力要求。后整理包括烧毛、压光、热定型、拒水防油处理、乳液浸渍涂层等。
根据产品的不同用途采用不同的后整理工艺。影响针刺过滤材料品质的在线工艺参数包括生产速度、铺网层数、针刺频率等,影响的是针刺过滤材料的厚度、面密度等。
三、机织过滤布的结构设计与生产
机织过滤材料是用相互垂直的两个系统的纱线交织而成,这两个系统的纱线既可以是单丝或复丝,也可以是短纤维纺成的单纱或股线。由于纱线本身线密度较大,透气量很小,所以机织过滤布过滤的颗粒只能从经纬纱线间的孔隙通过。一般机织滤材的孔隙率为30%~40%,而且是直通的,因而对流体阻力较小,且机织滤材强力大,适合于压力降大的液体过滤。但机织滤材在过滤初期及清渣以后,过滤物中的颗粒很容易穿过滤材的孔隙,此时捕集效率较低。随着过滤的进行,颗粒逐渐沉积在滤材内部及表面,慢慢形成滤饼,靠这层滤饼的过滤作用,捕集效率才逐渐提高,此时,机织滤材只起着支撑滤饼的作用,但堵塞也很快发生。随着滤渣的清除,过滤效率又经历由低到高的变化过程。
常用的机织过滤布有平纹、斜纹和缎纹组织织物,特殊情况下也用纬二重、双层及管状组织织物。平纹组织交织点多,孔隙率小,纱线之间相对稳定,一般用于澄清过滤和较细颗粒的过滤。斜纹组织常用两上两下、两上一下、三上两下等组织和破斜纹组织及人字斜纹组织,其结构比平纹组织松,因而在相同紧密度下,透气率比平纹组织大,适用于真空过滤及离心过滤。缎纹组织织物经纬交织点少,经纬纱浮长较长,结构较松,质地柔软,表面较光滑,对滤渣的剥离性好,在干式过滤中易于清灰。缎纹组织常用五枚缎、八枚缎,堵塞少但捕集性差。冶金行业的布袋除尘器大多选用缎纹织物。为了使机织滤布直通的孔隙得以改善,可对织物表面进行起绒处理,起绒后的机织过滤布滤尘效果优于不起绒的机织滤布。
这类过滤布要求质地紧密,匀整光洁,孔眼方正,纱线条干均匀,过滤质量、速度、效果符合工艺要求,常用纯棉平纹织物。
黏胶化纤厂所用过滤材料,以棉织物为主,采用平布、单面绒、双面绒及府绸组合在一起,形成组合过滤布。其排列在各道工序中不完全相同,一般排列如下:第一道过滤:双面绒、单面绒、平布;第二道过滤:双面绒、单面绒、府绸、平布;第三道过滤:双面绒、府绸、平布。
这类过滤材料的主要指标是无毒性,过去常以棉为原料,为提高过滤效率及使用寿命,现正逐步改用丙纶、涤纶等,其品种有:丙纶长丝平纹组织滤布、丙纶长丝两上两下斜纹组织滤布、涤纶斜纹组织滤布、涤纶长丝平纹组织滤布。
矿业物质过滤有多种形式,滤材的强度、耐压性、耐化学性、耐腐蚀性、耐高温性及尺寸稳定性有差异,所以,必须选择合适的纤维原料、织物结构、织物规格及整理工艺。常用的品种如下:涤纶长丝平纹组织滤布、涤纶平纹组织滤布、涤纶长丝平纹。
大部分过滤布的紧密度较大,有时需要根据最大密度理论,求得最大密度以视产品能否顺利织造。最大密度取决于纱号、组织结构、纤维体积质量、纤维在纱线中的压缩程度和纱线在织物中的变形情况以及织机的机械性能等。
实际生产中,涤纶和丙纶长丝过滤布,还会出现静电严重的现象,这就要求要严格控制好车间内的温度与相对湿度,车间温度在春季、秋季、冬季应为22~24℃,夏季在28~30℃,相对湿度在70%左右为好。实践证明,车间温度较高、相对湿度较大时生产较为顺利。也可以在整经时加防静电油以及用定捻锅汽蒸长丝筒纱的方式或在织造时打蜡的简易方法来解决。否则会出现起毛、毛羽多等现象,严重影响产品产量和质量。
织机的选择有以下原则:要根据生产产品的厚重程度和产量大小来决定。因为机织过滤布大多用于石油工业,该用途的过滤布一般属于厚重型,织物平方米质量在800g~1000g,因此打纬力非常重要。从打纬力方面,普通织机经改造后能增加打纬力,适宜轻薄型或厚重型过滤布的生产,而一般的或早期引进的无梭织机,由于打纬力较小,只适宜于轻薄型过滤布的生产,其生产工艺与生产牛仔布工艺相近。过滤布的产量方面,由于过滤布主要用于工业过滤领域,其特点是品种多、产量较小。从经济方面分析,普通织机适合于小批量生产,变换品种方便,而用无梭织机由于生产技术以及双轴生产特点,其产量应定在上千米以上才具有可使用性。
四、针织气体过滤材料
(一)针织气体过滤材料的原料选择
针织过滤材料常用的纤维原料主要分为传统纤维和高技术纤维两类。传统纤维有棉纤维、涤纶等;高技术纤维又分为高性能纤维、功能性纤维和精细加工纤维。高性能纤维包括聚苯硫醚(PPS)纤维、聚四氟乙烯(PTFE)纤维等;功能性纤维包括阻燃纤维、驻极体纤维等;精细加工纤维包括超细纤维、纳米纤维和异形截面纤维等。影响过滤材料性能的因素主要包括纤维的种类、特性,纱线的捻度和纤维的分布等。
针织气体过滤材料材质的选择应从实际需要出发,综合考虑各种因素。
1.纤维种类的选择 纤维种类的选择需要从过滤材料的用途出发。对于特殊用途的过滤材料可以使用高性能纤维,如PPS纤维和PTFE纤维。PPS纤维是一种耐高温纤维,具有优异的耐热性、阻燃性,力学性能优良,尺寸稳定性好,在冶金工业等领域应用广泛,适宜于高温气体过滤;PTFE纤维具有极好的耐高温性能、极强的耐腐蚀性和耐水解能力,在冶金、化学和水泥工业具有乐观的应用前景。但是,这类高性能纤维往往刚性较大,韧性不足,进行针织编织时易磨损纤维并损伤成圈机件,因此在进行针织编织时可以对纱线进行特殊处理或改进机器。
普通用途的过滤材料可以选择精细加工纤维,如超细纤维和纳米纤维。超细纤维直径小,比表面积大,虽然其单丝强力不高,但是纱线的总强度较高,柔软性较好,适宜针织加工。由超细纤维制成的绒类针织过滤材料孔隙率高、孔径均匀,可应用于家用和产业用空调过滤器上。纳米纤维制成的过滤材料具有高性能,可以有效地过滤纳米级的尘粒。纳米技术目前还处于研究阶段,相信纳米纤维凭借其独特的性能必然会在将来的过滤材料领域得到广泛应用。
2.纤维性能的选择 纤维性能的选择需要从多方面考虑。
(1)一般纤维越细,其制成的过滤材料过滤效率越高。但是,针织用纱需要具有一定强力,纤维太细不利于针织加工且易遭到损伤而影响产品质量,同时全部由细纤维制成的织物纳污容量小、流体阻力大,不适宜作为过滤材料使用。
(2)用外表面光滑的纤维制成的过滤材料比用表面粗糙的纤维制成的过滤材料的流体阻力小,过滤效果好,同时,表面粗糙的纱线经过成圈机件时会产生较大的纱线张力,造成线圈结构不匀,成圈过程中与多种机件接触摩擦,会磨损机件。
(3)用纤维横截面叶片越多的纤维制成的过滤材料,其过滤效率越高。
(4)用卷曲纤维制成的过滤材料比用非卷曲纤维制成的过滤材料的过滤效果好。
纱线的捻度对过滤效率也有影响。捻度过高会使纱线的柔软性变差,织造时易造成疵点,也会使针织物线圈歪斜,影响过滤材料的质量;捻度过低,会使纱线强度不够,增加织造难度,影响生产效率。高捻度纱制成的过滤材料的空气阻力较低捻度纱制成的过滤材料的低,但是捻度增大会使织物间隙变大,过滤效率也会有所下降。
加工过滤材料时可以采用密度梯度法,或使用不同线密度的纤维,将细纤维尽量分布在滤饼的形成面,以提高过滤效率和防止过滤材料阻塞。
(二)针织气体过滤材料结构的选择
1.网格织物 网格织物是在成圈纱中织入衬经纱和衬纬纱,兼有机织和针织过滤材料的特点。网格织物既有类似机织物的结构,尺寸稳定性得到改善,又可使经纱、纬纱没有因交织而产生的织缩,具有良好的颗粒分离特性,其过滤效果远远优于普通种类的针织物,且生产效率高。纬编网格织物可直接按照过滤材料所要求的直径尺寸进行编织,省去缝纫工序,操作方便;经编网格织物生产速度快,尺寸稳定性更好,过滤效率更为稳定。使用耐高温纤维(如PPS纤维)的网格织物过滤材料能在高温下保持体积弹性,耐热冲击和机械振动,可用于冶金行业等高温环境。网格织物过滤材料中使用较为广泛的是衬经衬纬圆筒过滤织物,如图4-10所示。

图4-10 衬经衬纬织物
2.针织绒类织物 针织绒类织物表面的绒毛层可使织物的孔隙不呈简单的直通状态,尤其是使用超细纤维等特殊材料时,绒毛层的存在使绒类过滤材料的过滤效率和清灰性能优于普通针织过滤材料,孔径减小可以有效拦截流体中直径小于孔隙的尘粒。过滤时流体中的尘粒在通过绒毛层的弯曲通道时会受到扩散、惯性和拦截等作用而沉积下来,部分尘粒被阻挡在底部组织附近形成粉尘层,依靠粉尘层的作用,过滤效率(尤其是过滤初期)提高。毛绒织物过滤材料的孔隙度大、透气性能好、过滤阻力低、容尘量大,同时绒毛层表面清除粉尘更为容易,清灰性能好。对于针织绒类织物,一般密度越大、孔隙越小,则其过滤阻力越大、过滤效率越高;绒毛平均长度越长、过滤孔隙平均直径越小,则过滤效率和过滤阻力越高、容尘量越大,同时也更易受到过滤风速和尘粒浓度变化的影响,过滤稳定性不好。
与机织物和非织造布相比,针织绒类织物尺寸稳定性差,因此限制了该类过滤材料的发展。随着针织技术的不断发展,织造和后整理技术的不断完善,针织绒类织物必将在过滤材料领域迅猛发展。目前,作为过滤材料使用最为广泛的绒类织物是针织长毛绒织物(图4-11)。
3.针织弹性织物 针织弹性织物可分单向弹性织物和双向弹性织物,也可分为经编弹性织物和纬编弹性织物。单向弹性织物仅在纵向或横向有弹力,结合使用普通纤维,可充分发挥高弹性纤维的特点,适宜作为过滤材料使用;双向弹性织物纵横向均具有弹性,但是弹性过大使其孔隙尺寸不够稳定,无法作为过滤材料使用。经编弹性织物比纬编弹性织物的延伸性小,织物的尺寸稳定性好,但纬编织物可使用的原料范围更广。该过滤材料一般使用氨纶等高弹性纤维编织线圈,使用普通化学纤维编织毛圈,与普通结构的过滤材料相比,其孔径和透过率更小,阻拦能力更高。由于两种纤维弹性不同,在进行气体过滤时,气体从毛圈一侧流过,过滤材料表面的毛圈在气体的压力下紧贴过滤材料表面,降低了透过性,使过滤材料的透气率减小,阻拦能力提高。当气体出现回流现象时,过滤材料在纵横向受到拉伸,高弹性化学纤维编织的线圈伸长,普通化学纤维编织的毛圈部分随之伸直,使得过滤孔隙变大,有利于过滤材料表面沉积的尘粒脱落。通常作为过滤材料使用的是单面弹性织物,是单向弹性织物的一种,其反面分布毛圈,正面分布线圈(图4-12)。

图4-11 针织长毛绒织物

图4-12 弹性毛圈织物
4.三维间隔织物 三维间隔织物分为经编间隔织物和纬编间隔织物(图4-13)。经编间隔织物可以由经编双针床机器编织,纬编间隔织物可以在纬编横机和圆机上织成。与普通二维织物不同,三维间隔织物由上下两个表面层和中间一个间隔层组成。该特殊的三维立体结构使得间隔层中的纤维呈空间曲折分布,形成具有无数微小孔隙的纤维三维网状结构,因此,尘粒必须沿着过滤材料内间隔层的曲折网状路径进行过滤,随时都有可能与纤维发生碰撞而被截留。过滤材料可以对尘粒进行拦截、惯性、扩散和筛滤等各种效应的表面和内部分离,有效拦截比过滤材料孔径更小的尘粒。间隔层的存在还可以提高流体的流动速度,加快过滤过程,具有阻力小、透气性能好等优点。但是也同样由于上述原因,使得过滤不仅仅发生在过滤材料的表面,也发生在其内部孔隙之中,易造成过滤材料阻塞,使清灰工作难以进行,从而加大压力损失。

图4-13 三维间隔织物