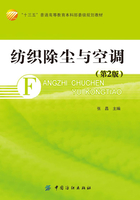
第一节 纺织车间的尘源及纺织粉尘的特性
一、纺织车间的尘源
纺织车间的粉尘是有机尘与无机尘的混合物。有机尘包括棉纤维、棉花叶茎壳等的碎屑、麻茎、动物毛、原毛中的草刺、细菌、真菌、淀粉浆料、化学纤维及化学染料等。无机尘包括泥土、砂子、游离二氧化硅等。纺织尘主要产生于纺织工艺过程中。
1.棉纺车间的尘源 在棉纺织厂的纺纱工艺中,棉纱用棉量大致为成纱重量的120%,即纺纱过程有20%原料成为棉尘。原棉纤维中粒径小于10μm的棉尘可分为三类:第一类是不与纤维抱合的棉尘,占40%~60%,可在清棉车间通过开清棉和混棉过程将它与棉纤维分离;第二类是与纤维轻度抱合的棉尘占20%~30%,可在梳棉机的刺辊、盖板、锡林、道夫的松解纤维过程中使之分离和排出;第三类是与纤维紧紧抱合的棉尘,占20%~30%,只能通过并条机的摩擦作用才能使之脱离纤维。由此可知,纺纱各过程均有棉尘产生。在棉纺织厂的织布工艺中,也会有粉尘产生。
(1)开棉。当开包机打开棉包时会在棉包附近散发尘土及短纤维。抓棉机的抓棉打手在棉堆上逐层抓棉时,会有尘土和短绒散发。开棉机的角钉、打手打击和开松棉块时,将散发出尘杂、短绒。其中较大者由尘格清除并落在机下成为车肚落棉,飘浮在空气中的尘杂与短绒随棉流进入下一机台。棉流经过豪猪式开棉机时,棉流中的短绒与尘杂经集棉尘笼过滤,由顶部的凝棉器把透过尘笼集棉层的短绒、尘土与杂质排入外接除尘设备中。在清棉机的双箱给棉机顶部,凝棉器风机可把短绒与细小尘杂排入外接除尘设备。而清棉机的单打手成卷机除在尘格处形成车肚落棉外,还把通过上下尘笼的短绒与尘杂排到外接除尘设备内。
(2)梳棉。梳棉机散发粉尘的主要部位有以下几处。
①刺辊对棉花进行分梳与除杂,在刺辊下部形成后车肚落棉。
②刺辊高速回转时在其罩壳内形成高压气流,气流中的细小尘杂与短绒在锡林后罩板下口处、刺辊罩盖与给棉罗拉相接处向外扩散。
③锡林后罩板上口处向外扩散棉尘。
④在锡林前上罩板上口的含尘气流由此向外泄出。
⑤在锡林前下罩板与道夫罩盖形成的锡林道夫三角区及两侧面形成的缝隙处,有一回转高压附面层气流通过开口向外扩散短绒与细小尘杂。
⑥道夫罩盖开口即四罗拉剥棉处附近,清洁刀在清除粘在轧辊上的飞花、杂质时,向外扩散粉尘。
⑦棉网通过机前大喇叭口汇集成的棉条进入棉条筒上部的圈条器入口(小喇叭口)时,因摩擦而产生短绒。
⑧锡林、道夫高速回转气流中的尘杂与短绒随着气流速度的下降而沉降在中车肚与前车肚,形成前车肚落棉。
(3)精梳。精梳机将棉条进一步梳理,当黏附棉纤维与尘杂的梳针回转至下方同毛刷相接触时,把棉尘刷掉形成精梳落棉。然后由尘笼集棉,再剥入尘斗内或用吸棉管把落棉吸排到外接除尘系统。另外,精梳棉条在圈条器喇叭口处由于摩擦还会产生短绒。
(4)并条。并条机高速回转的罗拉牵伸棉条时,在高速运动的松散纤维网中,一部分短绒及细小尘杂因失去罗拉的控制而游离出来。高速运动的棉条通过喇叭口与导条架时,也会由于摩擦产生短绒。
(5)粗纱。粗纱机的罗拉牵伸区有游离纤维产生,加捻的锭翼同粗纱表面摩擦会产生短纤维,短纤维随锭翼旋转气流而扩散,粗纱断头时锭翼惯性旋转使飘头被打而产生飞扬的纤维。
(6)细纱。细纱机中的纤维在牵伸区运动时,部分短纤维得不到良好控制而产生飞花,其量占该机总散尘量的80%~85%。其次,因高速回转的钢丝圈与纱表面摩擦以及锭子卷绕时也会产生短绒与尘杂。细纱机牵伸区和加捻区产生的棉尘在机下滚筒(滚盘)或锭带盘处,由于回转气流的冲击,棉尘将向周围扩散。
(7)捻线。捻线机在纱线加捻及卷绕时也会散发少量棉尘。
(8)络筒。络筒机退绕管纱时,在其上部锥面上会散发棉尘,机器速度越高,散尘量越大。
(9)整经。整经机上的筒子纱退绕时,会散发棉尘,纱在经轴上卷绕当其改变运动方向时也有棉尘散发,其中一部分棉尘伴随经纱一起被绕在经轴上。
(10)浆纱。浆纱机上过浆的经纱被卷绕到织轴上时,会因浆膜破裂产生粉尘。
(11)织布。织布机上经纱下分层交替运动时以及机件摩擦纱线时,有浆料粉尘和短绒散发。刷布机刷理布面时会产生短绒棉尘。验布、叠布机在布匹运动和抖动时,抖发其表面黏附的少量棉尘。
此外,棉纺织厂还有一些废棉处理机,虽然机台数量不多,但散发粉尘量也不可小视。
2.毛纺车间的尘源 在毛纺织厂中,选毛车间的粉尘产生量最大且有羊粪腥臭气味。开毛机的落杂以尘土为主。选毛台下汇集了大量的尘土、大杂质。梳毛机梳理已洗过的净羊毛时,其车肚下的落杂多为草刺、短毛;各工作辊处散发的多为毛短绒(飞毛)。
3.麻纺车间的尘源 麻纺织厂的拣麻、软麻和梳麻工艺过程中散发粉尘最多,粉尘的主要成分是泥土、麻皮、麻骨和少量短纤维。原麻拆包分理拣麻时有大量尘土、麻骨、麻皮理出。当在软麻机喂麻帘子上抖动松散并扑打麻束时,将会在软麻机两侧散发大量的粉尘。当喂麻帘子上的麻输送到轧辊挤轧软化时,又会在软麻机喂入口和输出口、轧辊四周和车肚内散发麻尘。梳麻机散发粉尘的部位是上部铺麻帘子的两侧及操作平台前。梳麻机的前后罗拉牵伸麻纤维时,会分离出许多短纤维和尘杂并落入车肚内。头梳的铺麻台、机台所有开口缝隙处均有麻尘散发。二梳的麻尘散发处主要在麻卷喂入部分。细纱、络筒、缝边等工序中产生的粉尘主要是麻短纤维和少量尘土。细纱机将麻条加工成经纱和纬纱时,沿整个机长的牵伸区内均散发尘屑和短纤维。络筒机在络纱时,纱线通过清纱张力装置,在锭子高速回转的气流作用下,使杂质向四周飞扬。麻织物缝边时也有较大量的粉尘产生。
纺织粉尘在车间里的扩散程度主要取决于车间里空气流动的作用。车间内飘浮在空气中的棉尘多半是被机械损伤的纤维梢部,这些纤维梢部在静止空气中的自由沉降速度大约为5cm/s。而纺织厂一般车间的空气流动速度为0.2~0.5m/s,精纺车间和织布车间的空气流动速度还要高,最高达1m/s左右。因此,当粉尘扩散到车间时,必将会在空中随风飞扬。
纺织粉尘扩散除空气流动作用原因外,还与某些纺织机械散尘处密封不好有关,有些纤维半制品的加工过程就暴露在流动空气中。人工清扫也会造成粉尘的二次飞扬。手工选拣原料、摆放半制品、人工推运等,也都是造成粉尘飞扬的原因。
二、纺织粉尘的性质
1.爆炸性和自燃性 棉、麻、毛纤维粉尘爆炸是指在空气中悬浮的纤维急剧氧化燃烧,同时产生大量的热和高压气流现象。爆炸时生成的气体受高温作用急剧膨胀而产生高压,形成冲击波。粉尘爆炸可分为反应引发和反应进行两个阶段。反应引发阶段的特点是,局部粉尘的表面受热,使表面分子分解或因干馏作用而产生含有粉尘分子的空气混合气体,当达到能使粉尘分子与氧分子化合的温度和压力时,遇到火源即能引起燃烧与爆炸。反应进行阶段的特点是,反应热促使粉尘进一步分解,并形成较大范围的混合可燃性气体,使燃烧的火焰进一步传播,从而发生爆炸。
燃烧与爆炸均为化学反应,其根本区别在于空间压力变化的程度。当单位时间单位体积内释放的能量较小时,释放的能量与散去的热量处于平衡状态,此时为燃烧。它所造成周围空气压力的变化很小。当提高释放能量或加快反应速度时,燃烧可以转化为爆炸。密闭空间比非密闭空间更有利于燃烧向爆炸转化。
棉纤维粉尘的沉积层与悬浮在空气中的棉纤维粉尘的起火过程不同。沉积在高温物体表面的棉纤维粉尘层,即使其表面温度是悬浮粉尘燃烧温度的1/2时就能引起燃烧,这种现象称为纺织粉尘的自燃。燃烧产生的热量成为粉尘引爆的关键因素。沉积层越厚,蓄热量越高,越有可能使粉尘爆炸和引起火灾,甚至引起连续爆炸。纯纤维尘处于沉积状态时的自燃温度,棉花为266℃,羊毛毡为205℃,漂白羊毛为525℃,粘胶纤维为280℃,锦纶为475℃,真丝为570℃。点燃需要的能量很小,只要2mJ能量在2s内即能点着纤维粉尘。如果纤维粉尘遇到有足够能量的点燃源,且点燃温度高于自燃点,并同时具备爆炸的粉尘浓度和供氧充足两条件时,就有可能燃烧,甚至发展成爆炸。
2.黏附性 粉尘粒子彼此附着或附着在固体表面上的现象称为黏附。克服附着所需要的力称为黏附力。单根棉纤维一般是呈天然转曲状态。纤维间自然接触后,由于表面摩擦力和分子间吸引力的作用,极易搭接一起。即使是构成棉尘的纤维梢部或纤维的碎段,彼此也能黏附。又因棉尘含棉蜡成分,使黏附性更加明显。特别是空气温度较高时纤维的黏附性更强。可以利用棉尘的黏附性,使棉尘由小粒集结成大粒棉尘而有利于除尘。但棉尘相互黏附容易凝聚成大块而在管道内沉淀,在气流输送时甚至会阻塞管道。因此在确定气流输送管道内的输送速度时必须考虑棉尘黏附性,特别是对潮湿的棉尘更不容忽视。
3.湿润性 粉尘粒子被水或其他液体润湿的现象,称作湿润性。粉尘可分为疏水性和亲水性两类。粉尘的湿润性与粉尘的比表面积有关,一般说来粉尘的比表面积越大且表面越粗糙,越容易在表面吸附气体分子形成气膜,从而阻碍液体对它的湿润。天然纤维的湿润性较好,在空气相对湿度较大的环境内加工时潮湿的棉尘纤维间的附着力增加,其粉尘更易沉降,有利于从含尘空气中分离。
4.带电性 纺织纤维的电阻很大,是电的不良导体,极易携带电荷而产生静电现象。常用质量比电阻表示纤维的导电能力。纤维的质量比电阻小,表示纤维的导电能力好,纤维的静电现象不显著。棉尘同锦纶织物滤材摩擦时静电现象明显且不易消失。如粉尘与除尘设备间有静电吸引,虽有利于提高除尘效率,但不利于清灰。而静电火花则会引起燃烧或爆炸,必须保持纺织机械接地良好,以便纤维上的电荷较快消失。潮湿的棉尘导电能力好,易消除静电现象。
三、纺织粉尘的参数
1.真密度和堆积密度 单位体积物质所具有的质量称为密度,单位常用kg/m3。纺织粉尘处于密实状态时的密度称为真密度,用ρp表示。纺织粉尘处于堆积状态下包括空隙体积在内的密度称为堆积密度,用ρa表示。粉尘在空气中的沉降或悬浮程度与粉尘的真密度有很大关系。在设计选择除尘器时必须知道粉尘的真密度。各种纤维粉尘的真密度为:棉1540kg/m3,羊毛1310kg/m3,丝1330~1450kg/m3,亚麻1500kg/m3,麻1500kg/m3,粘胶纤维1500~1520kg/m3,涤纶1380kg/m3,锦纶1140kg/m3,腈纶1170kg/m3,维纶1260~1300kg/m3,丙纶910kg/m3,氯纶1390kg/m3。纺织粉尘的堆积密度随纤维性质、形状、集合状态及压力等条件的变化而不同,因而准确数值不易确定。由于各种密度的尘粒混在一起,因而实用上多采用其概略数值。例如,纤维集合体中纤维所占有的空间一般为90%~96%,依此推算棉尘的堆积密度约为155kg/m3。
2.纺织尘粒径 单个粉尘粒子的尺寸用粒径表示,其单位为μm。由于纺织粉尘的形状没有规则,为便于工程计算需采用有代表性的尺寸来表示纺织粉尘的粒径。在工程上纺织粉尘的粒径多采用空气动力学直径。空气动力学直径定义为:在静止空气中,尘粒的沉降速度与沉降速度相同的密度为1g/cm3的圆球的直径。空气动力学直径da(μm)与粉尘实际直径d(μm)的关系为:

纺织粉尘的形状为自然卷曲的长柱形体。有研究表明,增加纤维长度很少增大纤维的动力学直径,纤维空气动力学直径增大与否主要取决于纤维的直径。有学者证明,纤维空气动力学直径仅与纤维断面直径有关。棉纤维空气动力学直径约比其真实直径大24%。
3.粉尘分散度 粉尘的分散度是研究粉尘对人体危害及研究除尘机理、设计与选择除尘器和输尘管路等的基本条件。粉尘的分散度就是粉尘粒径分布,它反应粉尘中不同粒径的尘粒各占总体数量(数量分散度)或质量(质量分散度)的百分数。纺织环境工程中多用质量分散度,质量分散度用各粒级尘粒质量占计测粉尘总质量的百分数表示,即:

式中:PWi——某(i)粒级尘粒的质量百分数;
Wi——某(i)的粒级尘粒的质量;
∑Wi——各粒级尘粒质量的总和。
4.含尘浓度 单位体积空气中粉尘的含量称含尘浓度,也称含尘量。空气中含尘浓度常用质量浓度或颗粒浓度表示。每立方米空气中所含粉尘的质量称为质量浓度,其单位为mg/m3。每立方米空气中所含粉尘的颗粒数称为颗粒浓度,其单位为粒/m3。
5.爆炸性指标 粉尘的爆炸性指标包括粉尘云的最低着火温度、粉尘爆炸浓度下限、粉尘云的最小着火能量、粉尘云的最大爆炸压力和最大压力上升速度等。粉尘云的最低着火温度是判断粉尘云着火特性的一个重要参数。它是在没有火焰、电火花等火源的作用下,粉尘云在空气中被加热而引起燃烧、爆炸的最低温度。单位体积空气中能够发生爆炸的最低粉尘量称为粉尘爆炸浓度下限。当可燃物浓度处于下限时,可燃物质点的火焰可以由一个质点传到另一个质点而引起爆炸。粉尘爆炸浓度下限与粉尘云内燃烧传播速度有关。粉尘云的最小着火能量是指在最易引燃粉尘的试验条件下,能引起粉尘云着火的最小能量。从爆炸下限起,爆炸压力随粉尘浓度增大而增高,达到最大值后随粉尘云浓度增大而逐渐降低,在无限浓度时爆炸压力接近于零。一般把测得的爆炸压力中的最大值称为爆炸最大压力,这时的最大压力上升速度也达到最大值。最大爆炸压力和压力上升速度最能代表爆炸威力,它是衡量粉尘爆炸性的主要指标,是制订防爆措施的主要依据。达到最大爆炸压力时的尘云浓度是最危险的浓度。表2-1列出了部分纺织粉尘爆炸性指标的参考值。
表2-1 部分纺织粉尘爆炸性指标参考值
