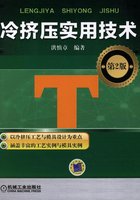
6.3 高速冷挤压
近几年来,在低速冷挤压的基础上,高速锤上的冷挤压工艺得到了很快的发展。目前,高速冷挤压已广泛应用在机械制造、汽车制造和宇航工业中。高速冷挤压的材料有纯铝、铝合金、纯铜、铜合金、碳素钢、低合金结构钢及不锈钢等。高速冷挤压所制的零件,其形状呈薄片、细长轴,如叶片、顶针等。
一般机械传动的冷挤压压力机的滑块运动速度约为0.1~0.4m/s,而高速锤的滑块运动速度可高达10~24m/s。
1.高速冷挤压的特点
高速冷挤压与一般挤压工艺相比,它不但具有低速冷挤压的优点(如节约原材料、提高劳动生产率、提高零件的尺寸精度和力学性能,以及降低表面粗糙度等),而且还有下面一些特点:
(1)冷挤压件表面粗糙度值低 在高速锤上进行冷挤压所得零件的表面粗糙度值是较低的。在入口角为180°的平凹模上,以羊毛脂润滑,对有色金属两种挤压速度进行冷挤压。在低速冷挤压时,曾发现润滑层脱落,零件表面出现刮伤;而在高速冷挤压时零件表面质量较为理想。有的单位用磷化后皂化作为钢的高速冷挤压润滑,用磺化油脂作为有色金属高速冷挤压的润滑,都得到了满意的结果。高速冷挤压能够得到表面粗糙度值低的制件,是由于在高速下摩擦因数的降低。室温下不同滑块速度的摩擦因数见表6-33。一般情况下,摩擦因数随变形速度的增加而降低。另外,在高速挤压时润滑剂来不及挤出,润滑条件好,从而减小了摩擦力,这不仅可以延长模具寿命,而且使制品表面光洁。
由图6-33可知,在不用润滑的情况下,高速时摩擦因数也相当低,这可能是由于高速下温度升高在摩擦面上形成氧化薄膜的缘故。
(2)金属流动均匀 与低速相比,高速冷挤压时由于摩擦因数随着变形速度的提高而降低,使金属变形趋于均匀,表现为变形区小,死角区小,坐标网歪扭少。图6-34所示为纯铜在低速和高速(19.5m/s)下冷挤压时的金属流动图。从图6-34可知,变形速度的提高有利于金属均匀流动。在钢铁材料冷挤压时,高速变形同样有利于金属的均匀流动。
图6-33 室温下不同滑块速度的摩擦因数
图6-34 纯铜在不同速度下的金属流动图
a)低速 b)高速
(3)挤压件平直 在高速下进行冷挤压,由于“自直效应”的作用,所得到的挤压件都较低速平直。如高速锤的打击速度为15m/s,而毛坯的挤压比为10时,那么金属的流动速度将达到150m/s。因此,它具有很大的动能,且高速变形是在极短的时间内完成的。这样,已挤出部分的金属具有很大的惯性力,这对后续部分金属产生了一个“拉直作用”。即使零件的横截面形状较复杂,挤压后也可以得到很直的零件。
(4)挤压件力学性能好 高速冷挤压件的抗拉强度比低速时高,而断面收缩率比低速时略低,如图6-35和图6-36所示。这是由于金属高速冷挤压时加工硬化现象比低速要好。
(5)挤压件的尺寸精度 应该指出,高速冷挤压件在长度方向上略有斜度,先挤出来的前端尺寸往往大于后端。用直径φ25.4mm的毛坯正挤压成φ0.254mm×30.5mm的工件,前后端直径差约为0.05mm。这是由惯性力引起拉直作用的缘故。在编制高速挤压工艺时,要注意到这一现象。
应指出,高速挤压还存在如下缺点:
(1)挤压件易被拉断 设高速挤压的凸模以v0=17m/s的速度运动,挤压比G=15,则被挤出的金属应以v0G=17×15m/s=255m/s的高速向前运动,而凸模在千分之几秒后突然停顿下来,这样一来,前端已流出的高速部分便对未流出的低速部分产生一个拉力。该拉力可以拉直挤压件,这是好的一面,但当此拉力很大时,就有可能拉断挤压件。由此可以看出,高速挤压细而长的零件是困难的,即使不被拉断,也会使挤压件的横截面变细。
图6-35 高速及低速冷挤压纯铝的抗拉强度
图6-36 高速及低速冷挤压纯铝的断面收缩率
(2)挤压件易过烧 由于高速变形的热效应比较显著,会引起零件局部地方温度上升到锻造加热温度的上限以上,不仅造成挤压件过烧,同时也降低挤压件强度。
2.高速冷挤压的单位挤压力
图6-37所示为凸模运动速度对单位挤压力的影响,试验用的毛坯尺寸为φ25.4mm×38.1mm。以15钢的室温正挤压为例(见图6-37d),在21m/s的高速下单位挤压力较低速冷挤压低,但当挤压速度继续增加以后,挤压力便随之而增加。有时在极高速下会出现第二个最低值,这可能是变形热效应的原因。从图6-37可以得到不同材料高速冷挤压时的合理打击速度:纯铝为8~12m/s,纯铜为18~22m/s,低碳钢为22~26m/s。
在高速锤上采用温热挤压可以使挤压力降低,模具寿命可显著地提高。
图6-37 凸模运动速度对单位挤压力的影响
a)纯铝正挤压,5400J能量 b)纯铝反挤压,2700J能量
图6-37 凸模运动速度对单位挤压力的影响(续)
c)纯铜正挤压,10800J能量 d)15钢正挤压,13500J能量