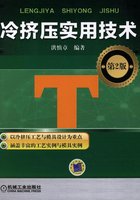
2.1 原材料的形态及其要求
2.1.1 原材料的形态
根据冷挤压件的形状、尺寸以及所采用冷挤压工序的不同,冷挤压用原材料的形态可分为:线材、棒料和板料三种。
1.线材
线材主要作为镦挤螺栓之类零件的原材料。由于可以进行连续送料,因此生产率很高,但受冷挤压设备吨位以及过大的直径线材不能盘绕成卷捆状的限制,线材只能用于生产较小的零件。一般情况下,冷挤压所使用线材的直径为φ3~φ25mm,个别情况下,也有达φ35mm的。
线材主要在连续多工位自动冷挤压机上加工,故材料利用率很高。但工序之间不能进行中间退火,端面的切断面也难以润滑,因此,模具工作部分的磨损较大。
2.棒料
冷挤压生产中最常用的一种形态是棒料。棒料主要作为形状复杂、尺寸较大零件的原材料和用于非连续性生产。它与线材相比,生产率较低,但可以进行中间退火处理及表面润滑处理。
棒料的材料利用率也较高,采用锯切备料的材料利用率可达70%~90%,采用剪断备料是100%。
由于当毛坯的长径比小于或等于3/4时,下料是困难的,因此,用棒料作为原材料,必须限制长径比不得小于3/4。
3.板料
当毛坯的长径比小于3/4时,必须选用板料作为原材料。由于板料多用冲裁法进行下料,因此,尺寸误差小,重量偏差小。但材料利用率较低,一般为40%~60%,故经济效益较差。
2.1.2 对冷挤压材料的要求
冷挤压的材料主要根据工件规定或要求的强度来决定,另外,还应当考虑到材料所能达到的最大的变形程度和模具的使用寿命,以及是否需要多次挤压和特殊的设备等。因此,适合于冷挤压的材料,应当具有较高的塑性,不但冷态塑性好,而且变形时的硬化程度也不太强烈。随冷作程度的增加,变形阻力上升较慢些,这样的变形条件是最有利的。
通常认为,当材料同时具有低加工硬化速度和低硬度时,就具有最佳的冷挤压性能。材料的这种性质是由其成分所决定的,而材料的成分则又是根据对产品零件的要求来选择的。因此,必须使材料的成分合适,并采用适当的软化热处理,以达到经济效果最好。
目前,很多材料是可以冷挤压加工的,而适于冷挤压的材料主要为低碳钢、中碳钢和低合金钢。镍含量较大的各种钢种,一般不进行冷挤压加工,因为冷挤压这类钢的模具会剧烈磨损,并且需要很多加工工序和大型的专用冷挤压机。采用尽可能少的成形工序和中间退火工序,确保模具的使用寿命,冷挤压出满足产品性能和使用要求的最后形状,使其达到最大的技术经济效果,是确定冷挤压材料的基本原则。
由于冷挤压成形会产生显著的不均匀变形,因此,为了获得优质的冷挤压件,除了采取一些有效的工艺措施以外,还要求冷挤压件所用的原材料具有较高的质量和良好的性能。关于冷挤压件原材料的质量高低和性能好坏的评价问题,可以采用如下一些指标来衡量。
1.材料的塑性
金属冷挤压同冷镦、冲压、锻造、轧制等压力加工工艺一样,都是利用金属材料的塑性。塑性是决定于变形过程中金属的综合性能、温度以及应力状态的特性。
很多研究表明,只要有适当的变形条件,包括合金钢在内的难变形材料的塑性可以得到很大的提高,就能使低塑性及形状复杂的零件冷挤压成形。因此,为了提高材料的塑性,要尽可能在较明显的各向压应力作用下进行冷挤压成形加工,而且要避免这样的变形方案,即在挤压件的个别部位产生显著的应力。因为拉应力所起的作用越大,且压应力所起的作用越小时,材料在变形时表现出的塑性越低。引起开裂的主要原因之一,就是在材料变形的个别地方出现拉应力。拉应力多数是在材料不与模具进行直接接触,或在具有一定的悬空情况下进行自由成形时产生的。因此,使工件与模具最大限度地接触,借助于接触压力所产生的附加压应力,可以大大提高变形材料的塑性。
随着碳含量的上升和合金成分的增加,材料的塑性减小,而强度增高。钢中碳的质量分数每增加0.1%,它的强度就提高60~80MPa。碳的质量分数大于0.3%以上的碳钢、合金钢及轴承钢、不锈钢等材料的塑性较低。铁的杂质和硫、磷含量可使塑性降低。因此,这些有害杂质含量应控制在一定的范围内(质量分数不大于0.035%)。
晶粒大小对冷挤压加工性能的影响有这样的一般规律:金属与合金的晶粒尺寸增加时,它的强度降低,塑性和挤压性能提高。冷挤压材料的晶粒很小时,其塑性较低,弹性较高。过大的晶粒易使挤压零件的表面粗糙和经常引起裂纹。合理的晶粒平均直径为φ0.02~φ0.06mm,同时要求材料有尽可能均匀的晶粒结构。
在工程应用上,材料的塑性可以用伸长率A和断面收缩率Z来衡量。虽然这两个指标不能全面地说明材料的塑性,但是它们是有应用价值的指标,并且容易确定。一般认为A、Z值越大,材料的塑性越高,冷挤压加工时的工艺性越好。
对纯铝1070A、硬铝2A11和低碳钢(15钢)三种材料的性能进行比较(见表2-1),不难看出,纯铝是一种塑性很好的材料,它的伸长率A可达35%~40%,断面收缩率Z达到70%~90%,抗拉强度Rm也较低,只有80~100MPa。它可以承受各种冷、热塑性成形加工。但是,当纯铝与铜、镁等组成多组元的合金后,组织与性能就将完全改变。如硬铝2A11的伸长率与断面收缩率就很低,甚至不如低碳钢。由于硬铝的伸长率小于20%,故称为低塑性材料。硬铝合金冷挤压时虽然所需挤压力不大,变形也并不困难,但是冷挤压中极易产生开裂现象,这就是由于硬铝塑性较差的缘故。
表2-1 各种材料的力学性能
总之,塑性越高,材料的变形能力越好,越能承受较大的变形。对于塑性较低的材料,为了不超出极限变形程度,就可能要增加加工次数,减小每次加工的变形量。因此,塑性的高低是决定变形工序次数的主要依据。
材料塑性的高低可采用各种不同的试验方法来测定。其中最常用的是压缩试验法。它是通过测定压缩圆柱形试样直到试样外面发生裂纹的极限变形量(压缩率)来表示塑性高低的。由分析可知,影响塑性的因素较多。现考虑试样高径比、接触面的润滑条件以及模具的约束条件等因素的影响,采用压缩试验法求得45钢的极限压缩率,如图2-1所示。由图可知,当高径比h0/d0增大时,极限压缩率也增大,即塑性升高;而当润滑条件变坏时,极限压缩率就会下降,即塑性降低。
图2-1 45钢的极限压缩率
-----斜向裂纹 ——纵向裂纹
2.材料的变形抗力
材料的塑性和变形抗力标志着材料的变形性能。变形抗力就是材料塑性变形所需要的应力。冷挤压时材料的变形抗力越小,加工时所需的单位挤压力也越小。随着变形抗力的增加,材料的伸长率和断面收缩率都下降。当材料的变形抗力足够大时,就有可能引起模具或冷挤压设备损坏的危险。因此,材料变形抗力的大小是衡量能否进行冷挤压加工的决定性指标。例如,在当前的技术条件下,冷挤压碳的质量分数在0.45%以上的碳钢是困难的,这是由于这些碳钢的变形抗力较大,有可能超出模具的许用单位压力的缘故。
通常情况下,变形抗力随着变形程度的增加而变大。不同材料的变形抗力是截然不同的,有色金属及其合金挤压时的变形抗力就比较小。对于碳钢和合金钢来说,随着碳含量和合金元素含量的增加,变形抗力明显增大。随着变形程度的提高,有色金属及其合金变形抗力上升的幅度较小,而碳钢和合金钢都有明显的上升。
因此,冷挤压材料的变形抗力越小越好。通过改进模具结构,提高软化处理的效果,选用塑性较好、具有低硬化速度的材料,都可能达到冷挤压加工时变形抗力低的目的。
材料变形抗力的大小一般是用各种不同的试验方法测得的。普通的拉伸试验测得的强度指标和塑性指标预测成形性能是有困难的。例如,拉伸试验曲线的最大应变量受到出现细颈的限制,一般对数应变ε≈1。而三向压应力状态的变形,其对数应变值往往超过1很多,因此要较精确地确定冷挤压(冷锻)时的金属变形抗力,就需要用压缩试验求出真实应力-应变曲线。压缩真实应力-应变曲线的应变量可达ε=2。压缩铜试件时,甚至可达ε=8~9的变形程度。
为了消除压缩时产生凸肚的影响,可以采用反复切削-镦粗试验方法,测得的各种碳钢的变形抗力曲线,如图2-2所示。图中纵坐标变形抗力σ是载荷除以试样的瞬时横截面积所得到的实际平均压缩应力;纵坐标HV0.1表示的是显微维氏硬度值。比较σ值与HV0.1值可知,HV0.1值正好等于σ值的2.5倍。因此,原材料的变形抗力值一般可根据显微维氏硬度测定结果推算出来。从图2-2还可以看出:变形抗力值随压缩试验的进行而增大,因此,在考虑原材料变形抗力对冷挤压变形的影响时,应把变形抗力和加工硬化联系起来一并考虑。如对于12Cr18Ni9不锈钢等冷作硬化敏感性特别大的钢,采用一般的冷挤压方法加工是很困难的。
图2-2 碳钢的变形抗力曲线与显微维氏硬度
3.材料的加工硬化
冷挤压后,所有阻止金属变形的各项指标都有不同程度的增高:弹性极限增加100%~300%,抗拉强度增加30%~120%,硬度增加60%~150%,即金属产生了加工硬化现象。相反,塑性指标都有所下降:伸长率减小20%~90%,断面收缩率减小20%~60%。变形程度不同的挤压加工过程,硬化程度也是不同的。加工硬化的材料变得硬而脆,塑性变形的能力降低,也就是说,加工硬化会阻碍金属的继续变形。
但是,如果这一变化比较缓慢,即随冷作硬化程度的增加,变形阻力上升较慢,强度、硬度上升和断面收缩率、伸长率下降的幅度都不大,即冷挤压时显示出不大的应变硬化性。这样,继续变形又将成为可能,而使金属达到较高的变形程度。这一点在选择材料时是很重要的。
因此,选择时效硬化敏感性较小和具有低加工硬化速率的材料,对冷挤压变形是十分有利的。低的加工硬化指数被认为是良好的可成形的指标。
4.材料表面质量
材料的表面缺陷对冷挤压件的质量影响很大。这是由于冷挤压加工与切削加工不同,冷挤压时,材料的表面缺陷会保留或扩大成冷挤压件的表面缺陷。
为了避免冷挤压时表面开裂,提高挤压件的表面质量,良好的材料表面状态是十分重要的。普通热轧棒料的表面大多数不能满足冷挤压工艺的特殊要求,冷挤压生产一般用冷拉优质结构钢和深冲钢等。为了提高挤压件的尺寸精度和降低表面粗糙度,采用表面磨光的材料较为有利。材料的表面缺陷,如杂质、夹灰、擦伤、裂纹等,一般都零星地遍布在材料表面上,即使是合格的材料,加工时也难免产生缺陷。因此,应需加强对材料的检查和验收。
为了查明材料表面有无缺陷,以及确定金属的冷挤压变形性能,通常采用冷镦粗试验、冷扭曲试验或腐蚀试验等进行鉴别。冷镦粗试样时,表面有深痕,内部有叠层、裂纹和夹灰的材料就会充分地暴露出来。
材料的表面缺陷容许极限是根据材料的种类、零件形状和用途等具体情况,按照实践经验来决定的。表面缺陷对镦挤工序的影响最大。一般来说,当材料表面缺陷深度大于0.1mm时,冷挤压时易使之扩大为裂纹。因此,当表面缺陷的深度大于0.1mm时,应当设法消除。
材料表面的脱碳对冷挤压件的质量和性能影响也较大。对钢在冷挤压前的退火处理,当加热到720°C以上时有可能产生表面脱碳的危险。脱碳层深度的一般要求是:脱碳环状面积为相应处横断面积的5%以下。表面脱碳层的最大允许深度如表2-2所示。
表2-2 脱碳层的最大允许深度 (单位:mm)
冷挤压工艺对材料表面的基本要求是:表面应洁净、光滑,不应有发裂、气泡、划伤、氧化皮等缺陷,并且钢的断口和酸洗试片的组织不应有分层、缩孔、非金属夹杂物和白点等。
5.材料的组织状态
晶粒大小和状态对于冷挤压变形能力的影响较大。对于碳钢冷挤压来说,随着碳含量的增加,材料的变形能力随之降低。即使是相同的材料,当经过适当的热处理造成不同的内部组织时,其塑性也会不同。图2-3表示的就是碳钢在不同组织状态时,裂纹发生率与压缩率的关系。由图可知,当压缩率相同时,曲线1组织的裂纹发生率比曲线2组织的大;当裂纹发生率为零时,曲线1组织的压缩率为70%以上,曲线2组织为65%以上,曲线3、曲线4组织各为50%左右。
应注意的是:仅从冷挤压性能来看,应以球化组织为最好;但从冷挤压后的切削加工性能方面来考虑,则以退火后的组织为最佳。因此,应综合考虑多方面的因素,选择合适的组织状态。
为了使钢材能更好地适应冷挤压的要求,对于钢材的结构、晶粒的形式与大小、夹杂物分布等都有一定的要求。
(1)晶粒形式 冷挤压的钢材需要有尽可能均匀的、球形的晶粒结构。对第一道冷挤压工序或中间冷挤压工序来说,这种晶粒结构都是最理想的。
(2)晶粒分布 钢材组织中除了铁素体以外,还有珠光体。碳含量越高,珠光体的数量越多。铁素体是软的基体,在软的基体中嵌有硬的珠光体颗粒。
图2-3 压缩率对裂纹发生率的影响
1—退火粗晶粒组织 2—退火细晶粒组织 3—球化微细晶粒组织 4—调质微细晶粒组织
(3)晶粒大小 钢材晶粒的大小对冷挤压也有一定的影响。晶粒太小,会使挤压力增大;晶粒太大又会使表面粗糙,发生明显的伤痕与裂纹。
冷挤压钢材合理的晶粒大小范围如下:
晶粒平均直径≈φ0.02~φ0.06mm
每平方毫米的晶粒数≈250~2300个
晶粒的平均面积≈400~4000μm2
(4)非金属夹杂物的分布 无论用什么方法冶炼的钢材,总会含有或多或少的非金属夹杂物。夹杂物的大部分是氧化物或硫化物,它们使金属原来紧密的晶粒结构发生间断。因此,夹杂物的数量、形式和分布情况对钢材的冷挤压性能有很大影响。
一般来说,细的、均匀分布的夹杂物危害不大,而粗的或细而局部集中的夹杂物则是很危险的。
冷挤压毛坯大多采用经过轧制的棒料或板料,在轧制过程中,这些夹杂物已沿变形方向被拉长了。
夹杂物的形式对冷挤压的影响较大。硫化物的夹杂物可以较好地随着变形方向变形,因此,较其他一些夹杂物的危害要小。氧化铝夹杂物,很难与钢的基体结合在一起,危害很大。
6.毛坯的尺寸精度
毛坯的尺寸精度不仅影响到挤压件的尺寸精度,而且对模具的使用寿命及压力机的精度也有直接影响,因此,应严格保证毛坯的尺寸精度。
毛坯的几何形状应对称,以保证冷挤压过程中能均匀地产生变形,避免产生应力集中的现象。毛坯端面与轴线的垂直度误差最大应不超过0.1mm,对于空心毛坯壁厚偏差也不应超过0.1mm。
7.硬铝棒料粗晶环对冷挤压的影响
当使用硬铝棒料作为冷挤压的原材料时,需要注意硬铝棒料粗晶环对冷挤压的影响。经淬火的硬铝棒料,常存在粗晶环组织。由于硬铝棒料由热挤压制成。在热挤压时,由于金属材料与挤压筒壁之间的摩擦,再加上金属与凹模之间的摩擦,结果使金属表面的晶体受到了很大的破碎,这种破碎的表面晶体存留在挤出来的棒料上,其厚度由棒料始端(最先挤出的一端)至末端(靠近挤压垫的一端)是逐渐增加的。棒料如果在热挤压以后,再进行热处理,经过集中再结晶后的晶粒大小,与原有的实际的变形程度有关。这样,硬铝棒料经热处理后,在其外层形成了大晶粒的结晶壳层,称为粗晶环。其厚度是由始端到末端逐渐增加的。
由于硬铝棒料存在粗晶环组织,所以在冷镦以后,外表面会出现明显的凸凹不平,呈严重的橘皮状。如经整形,外表面也无法填平。在经过剧烈的冷挤压变形后,可能沿晶间有开裂现象发生。
因此,用于冷挤压的硬铝棒料应将粗晶环限制到最低程度,同时不宜采用细料经冷镦来制取冷挤压毛坯。