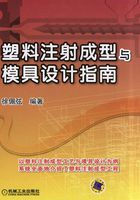
3.3 注射成型工艺
本节将讨论注射成型的主要工艺条件。注射充模和成型的过程和制品质量的关系,将在第5章中深入分析;本节叙述塑化计量和工艺,介绍物料温度、背压压力和螺杆转速选择和调度的方法,还陈述模具温度、冷却时间的确定和计算;然后介绍聚苯乙烯、聚丙烯、ABS、聚酰胺和聚碳酸酯五种塑料的工艺规程。
3.3.1 注射充模和成型的过程
注射加工的流动充模和冷却成型是塑料物理状态变化的过程。
1.注射充模
注射液压缸以高压将塑料熔体经料筒前喷嘴和注射模的浇口与流道,输入制品成型的型腔。这个熔体的传输过程可分为流动充模、保压补缩和倒流三个阶段。
(1)流动充模 图3-34是注射成型的压力与时间的关系曲线,也是三个位置的塑料熔体的压力随时间的变化曲线。第1曲线表示螺杆头前熔料的压力变化,也是注射液压缸的活塞推力的压力变化。微电脑控制注射机,可以测定并显示该曲线。第2条曲线表示喷嘴出口处熔料的压力变化。第3条曲线表示注射模中浇口出口处熔料的压力变化。压力可用压力传感器测出。
要理解熔体压力在流动充模中的压力变化,必需了解到:塑料熔体是高黏度的流体,而且具有明显的弹性;塑料熔体的密度随压力变化;在进入成型型腔前的流程中,由于料筒、喷嘴、流道与浇口的阻力,不断消耗注射压力;在流动充模的熔体传输过程中,料筒和喷嘴有一定的加热温度,而进入模具后低温的流道壁面对熔体有冷却作用。因此,塑料熔体的流动充模过程,不但是假塑性非牛顿流体质量和动量的传输过程,又是熔体能量变化的过程。
1)注射压力曲线。图3-34中,t0为螺杆开始推压熔体的时刻。在压力曲线1上,pi1为螺杆的注射压力,t2为熔体充满型腔的时刻,故时间段t0~t2为整个充模阶段。t1为塑料熔体冲出浇口,进入成型模腔的时刻。t0~t1为流动前期。在流动前期,喷嘴口和流道中熔体的压力急剧上升,梯度很大。在t1~t2注射充模的后期,型腔内塑料熔体被充满,pi2为切换的保压压力。控制t2的保压切换时刻十分重要,过早切换会使制品的密度不足。
图3-34 注射成型的压力-时间曲线
1—注射压力曲线 2—喷嘴出口处熔料的压力曲线 3—注射模中浇口出口处熔料的压力曲线
2)喷嘴出口处熔料的压力曲线。图3-34中,在流动前期流道中熔体的压力,由A上升至B点。B点对应喷嘴出口的保压压力pn2,显然,pi1-pn2为注射后期塑料熔体在料筒和喷嘴传输时的压力损失。而在模具内压力从pn1升至pn2。t3是螺杆后撤时刻。此时压力曲线1上螺杆头的注射压力急剧降至零。在t2~t3的保压期间,塑料熔体在保压压力下补充给模具的制件型腔。螺杆一旦后撤,流道中熔体压力自C点迅即下落至H点。在此期间,流道中熔体压力和温度下降很快,而制件型腔内的熔体压力较高。如果浇口有足够大的流通截面,塑料熔体会倒流至流道中。
3)浇口出口处熔料的压力曲线。图3-34中,自t1时刻熔体冲出浇口,压力在流动充模期间自D上升至E点。自E至F点,制件型腔内塑料得到压实和补缩。F点有螺杆后撤时的型腔压力pg1。在时间t1~t4期间,熔料充填并压实了制件型腔,而塑料熔体温度在下降。t4是截面狭窄的浇口中塑料冻结的时刻。自t4起制件型腔成为密封容器,停止质量传递。pg2是浇口冻结时刻的型腔中塑料的内压。从G点到I点,型腔内生产的注塑件,其内压和温度不断下降,形体冷却收缩。直到时间t5,模具的分型面打开。
(2)保压补缩 在整个充模阶段结束后,螺杆不能立即退回。必须在前段位置保持一定压力,螺杆缓慢推进。塑料熔体有补给型腔的保压流动,此时螺杆前端压力称保压压力,俗称二次注射压力。与注射充模阶段对型腔压实不同,此时型腔内熔体温度已下降,黏度升高,只是低速流动。而压力的传递起主导作用,影响注塑件的质量。产生保压流动的原因是模具壁间附近的熔体因冷却而产生体积收缩。在浇口冻结之前,熔体在保压压力下,产生补缩的流动。此时在注射机的料筒内,螺杆前端应有一定量的熔体,经喷嘴和流道系统至型腔末端,能够传输质量和压力。
保压阶段的压力是影响模腔压力和补缩程度的主要因素。较高的保压压力提高了模腔的内压,补进了较多物料,增大了制品的密度,也提高了注塑件内密度分布的均匀性。同时,熔体压力增大和持续保持,可提高熔合缝的力学强度,也可提高塑料与金属嵌件的连接牢度。但是,由于保压压力和流动是在成型物的温度在不断下降时进行的,较高的压力会在制品中产生较大的残余应力和大分子取向。使制品在使用期内容易翘曲变形,甚至开裂。
在一定的保压压力下,延长保压时间能向型腔中补进更多些熔料。其效果与提高保压压力相似。如果浇口的截面较大,又保持较长的保压时间,模腔中塑料凝固之后浇口才冻结,模腔的内压将缓慢下降。这有利保证薄壁深腔的大型注塑件的质量。反之,保压时间不足,浇口又不能及时冻结,则物料会从模具型腔中倒流,型腔内压力会下降很快。
(3)倒流 如果模具内的浇口没有冻结就撤除保压压力,则塑料熔体在较高的模具型腔压力作用下发生倒流。倒流使模腔压力很快下降。倒流将持续到浇口冻结为止。浇口冻结以后才结束保压是注射生产操作的失误。浇口冻结后制品的密度不会变化了。因此,使用不同的保压时间,对注塑件进行称量,可寻觅合适的切换时间。浇口截面的大小和形状决定了冻结的时刻。注射模内采用针点式的小浇口,一般不会发生倒流。大型的注塑件,采用主流道型的大浇口,保压时间可长达1~1.5min。保压时间对制品的密度和尺寸的精度有较大的影响。曾发生倒流的注射成型制品的密度不足,其表面有凹陷,内部有真空泡等缺陷。
2.冷却定型
(1)压力与温度变化 成型周期中型腔内熔体压力p与温度T的关系,可画出图3-35所示的典型的压力和温度关系曲线。该图是将模腔压力周期图上的时间t0t1…t4用型腔内熔体温度T0、T1、T2、T3、T4替代,并将纵横坐标轴对调。
图3-35上曲线DE时段为浇口尚未冻结,但保压补料已结束,因此存在倒流而使型腔压力急剧下降。从浇口冻结点E开始,型腔内的塑料量不再改变,所以型腔压力与温度沿着直线a变化。倘若保压于D点结束时,浇口早已冻结封闭,则模腔内的压力与温度沿直线b变化。
图3-35 型腔内熔体压力与温度关系曲线
浇口封闭后,型腔内压与温度的关系可用修正的状态方程描述。聚合物熔体密度ρ是温度和压力的函数。其表达式为
(p+π)(V-ω)=R′T(3-17a)
或
式中 p——型腔壁受到的压力(N/cm2);
π——各种塑料内压力常数(N/cm2);
V——塑料的比体积(cm3/g);
T——熔体的热力学温度(K);
ω——热力学温度为零时材料的体积容(cm3/g);
R′——修正的摩尔气体常数[N·cm3/(cm2·g·K)]。
若干聚合物的状态参量见表3-27。
表3-27 若干聚合物的状态参量(π、ω和R′)
式(3-17a)中,π、ω、R′皆为常数。因此,该方程是以V为斜率的直线方程。浇口冻结后,型腔内塑料的压力与温度沿着一条等容线或等密度线变化。冻结点不同,型腔内的塑料量不同,等容线的斜率不同。但所有等容线都通过p-T图的原点。即p=-π,热力学温度T为零。
(2)固化脱模 根据图3-35可以合理确定模具打开的温度和压力的条件。首先,型腔内的注塑件应该冷固到具有足够的刚度和硬度。开模时的温度应低于塑料的热变形温度。脱模温度Ts太高,在制件脱模后还会有较大的无模具约束的收缩。制件变形后,有较大形状和尺寸误差。因此,开模温度范围在Ts和模具工作温度Tm之间。通常,脱模温度Ts高于工作温度Tm,约5~10℃。如果出现制件在脱模时刚性差而受到损伤,应降低模具工作温度Tm后再调整开模温度。
其次,开模时型腔内的残余压力不能高于某个+pr值。太高会引起注塑件和凹模表面间过大的黏附力,使开模力增大。残余压力也不能小于某个负压值-pr。否则易出现缩孔和凹陷,使制品收缩率过大,对型芯包得过紧,致使脱模困难。上述的两组温度与压力限制条件,拟定了开模的合理区域。凡浇口冻结后型腔内塑料冷却的等容线通过这一区域,都属于优质的注射工艺。
3.3.2 物料的温度和塑化计量
影响注射成型质量的因素很多,在塑料原材料、注射机和模具确定后,注射工艺条件的选择与控制便是决定制品质量和生产率的主要因素。这里就物料温度、压力和时间的合理选择,进行一般性讨论。
1.物料温度
要区分塑料注射加工的注射温度和塑化温度。合理选择注射机料筒和喷嘴温度,保证塑料熔体在充填模具型腔时有适宜的流动性能。
(1)注射温度 注射温度是从注射机喷嘴射出的熔体温度。熔料的注射温度在流动充满模具型腔的过程中是不断下降的。下降的速率与模具型腔壁面的温度有关。表3-28列示了部分塑料熔体的注射温度与模具型腔壁的温度。塑料熔体是假塑性的非牛顿流体,它的黏度不但依赖温度和压力,还与流动剪切速率有关。因此,分析判断塑料熔体在模具中的温度分布和变化,最有效的工具是计算机辅助注射流动的数值分析和模拟。为调整和控制注射温度,可参考图3-36。该图列举有注射温度变化对注射成型工艺和制件质量的影响。
表3-28 部分塑料熔体的注射温度与模壁的温度
注:GR—玻璃纤维增强。
图3-36 注射温度变化对注射成型工艺和制件质量的影响
1—渐变(低压缩比)螺杆的塑化量 2—突变(高压缩比)螺杆塑化量 3—充模压力 4—充模流程长度 5—料流方向的冲击强度 6—与料流垂直方向的冲击强度 7—料流方向的收缩率 8—与料流垂直方向的收缩率 9—结晶型塑料的密度 10—通过浇口的压力损失 11—热变形温度 12—熔合缝的强度 13—料流方向的弯曲和拉伸强度 14—取向程度
(2)料筒和喷嘴的塑化温度 料筒和喷嘴加热是使塑料塑化和流动,但不能产生热分解。因此,料筒和喷嘴温度应控制在塑料流动温度Tf或熔点Tm,至塑料的热分解温度Td之间。料筒温度的分布,一般从料斗到喷嘴由低到高,以使塑料的温度平缓上升让其均匀塑化。
柱塞式注射机中塑化热量主要依靠热传导,因此要设定较高的料筒温度,比螺杆式的料筒温度高10~30℃。由于螺杆剪切塑化有较多的摩擦热,为防止塑料过热分解,有时靠近喷嘴前段的温度,略低于中段的温度。注射时塑料熔体在螺杆或柱塞的高压下高速通过喷嘴小孔,会产生摩擦热,使熔体温度升高约摄氏十度左右。因此,喷嘴设置温度通常略低于料筒的最高温度。表3-29是一些塑料的料筒和喷嘴设置温度的推荐方案。
表3-29 一些塑料的在螺杆式料筒和喷嘴处的温度设置
选择各种塑料适当的料筒和喷嘴设置温度时,还有以下的提示。
1)对于无定形的塑料,一般有较宽的注射温度范围,可用较低的料筒和喷嘴加热温度。可用提高注射速率方法,降低熔体黏度。对于结晶型塑料,注射温度的范围较窄,要严格控制料筒和喷嘴加热温度,避免发生热降解。
2)对于各种无机矿物质和纤维充填的塑料,视添加剂的比例,为提高熔料的流动性,要用较高的料筒和喷嘴温度。但对添加有机染料的塑料,加热温度要严格控制。
3)对于热敏性塑料例如聚氯乙烯和聚甲醛等,以及添加阻燃剂塑料,要严格控制料筒和喷嘴加热,应取较低设置温度。为防止塑料热降解,还必须控制其保持熔体状态的时间,这对用热流道注射成型尤其重要。
4)对于注射成型薄壁长流程复杂制品时,熔体流程比较大,要用较高的料筒和喷嘴加热温度,保证熔料能顺利流经狭长的型腔间隙。对带有金属嵌件的制件也需要较高的注射温度。厚壁注塑件的熔体注射温度可以低些,料筒和喷嘴设置温度选择下限。
5)为了避免喷嘴头的流涎现象,可以让加热温度略低于机筒的最高温度。但是,低黏度的结晶型塑料只能用阀式喷嘴。
2.塑化计量
固体粒状塑料在注射机的料筒内经压实、加热、剪切及混合等作用后,转变成熔体的过程称为塑化。物料经过塑化,要求达到所需的成型温度,具有合适的流动性;而且塑料熔体内必须组分均匀、密度均匀、黏度均匀和温度分布均匀,还要尽量避免聚合物及添加剂热分解,热分解物的含量应尽可能少。这样才能保证熔体顺利注射充填模具型腔,才有可能获得质量合格的塑料制品。
(1)螺杆式塑化 塑化质量主要由塑料的受热状况和所受的剪切作用决定。往复移动螺杆式注射机,螺杆转动对物料产生剪切作用,以机械力强化了塑化过程,同时又有摩擦热的生成,因而对塑料的塑化效果比柱塞式注射机要好得多。塑料在螺杆式注射机内熔融塑化过程,与螺杆式挤出机内的熔融塑化过程类似。但两者存在差异:挤出机料筒内物料的熔融是稳态的连续过程,移动螺杆式注射机料筒内,物料的熔融是一个非稳态的间歇式过程;在注射螺杆的塑化过程中,螺杆边旋转边后退,存在可调节的液压缸背压,螺旋槽的物料固体床解体比挤出螺杆早;在料筒前端的塑化熔料压力下,旋转螺杆后退时,存在有一定的反向压力流和漏流。
对于柱塞式注射机,固态塑料粒子在料筒内受到柱塞的推力,几乎不受剪切作用。塑化所需的热量,其大部分源自装有加热装置的高温料筒。塑料的热导率低,热传导很慢。在料筒径向方向上物料温度分布不均匀,近料筒壁的物料温度偏高,料筒中央的温度偏低,而且没有混合和剪切作用,塑料熔体的组分和黏度的均化程度低。在料筒的轴线上,柱塞对物料的压力,经过固态和半固态的粒子后,才传递到塑料熔体,因此,射出塑料熔体的温度不超过加热料筒和喷嘴的温度。而螺杆塑化的压实、剪切、混合和输送作用强,均化效果好。因此,射出塑料熔体的温度会超过料筒和喷嘴的加热温度。
计量是将塑化好的熔体定温、定压和定量射出料筒所进行的准备过程。这个计量过程是由注射机控制螺杆或柱塞,与塑化过程同时完成。计量的准确性不仅与注射机的控制系统精度有关,而且还受料筒和螺杆的几何要素的影响。很显然,计量精度越高,获得高精度的制品的可能性越大。
塑化能力的计算,可使用挤出理论中螺杆均化段的熔体输送能力的计算公式。常规螺杆塑化的熔料输出取决于正向流率QS。在注射机塑化时,螺杆承受有背压pb,又有压力流流率Qp和漏流流率Ql,见图3-37。完整的塑化体积流率有下式:
Q=QS-Qp-Ql (3-18a)
式中 Q——螺杆塑化的体积流率(cm3/s);
D——螺杆的直径(cm);
h3——螺杆均化段的螺旋槽深度(cm);
n——螺杆的转速(r/s);
θ——螺杆螺纹的升角(°);
e——螺杆上螺棱的轴向宽度(cm);
L3——螺杆均化段轴向长度(cm);
pb——注射液压缸给螺杆的塑化背压(0.1MPa);
δ——螺杆与料筒的间隙(cm);
ηh——螺杆的螺旋槽塑料的黏度(kg·s/cm);
ηδ——螺杆与料筒的间隙δ中塑料的黏度(kg·s/cm)。
图3-37 注射机螺杆塑化的流率和几何参数
由式(3-18)可知,均化段的几何参数对输出的体积流率和背压的影响:
1)在无背压的情况下,pb=0,则Qp=Ql=0。塑化量Q=QS,它与螺杆转速n和螺旋槽深h3成正比。
2)当螺杆与料筒的间隙δ=0,可略去漏流流率Ql。压力流流率Qp是螺旋槽深h3的三次方关系。槽深h3虽可提高输出流率Q,但使背压pb的调节作用减弱。
(2)热均匀性 塑料在柱塞式注射机中只依靠柱塞推动,几乎没有混合作用。物料的温度升高主要来自料筒的热传导。如图3-38所示,由于塑料的导热性能差,致使料筒壁附近的物料温度高些,料筒中央的物料温度低。此外,熔料在料筒中央处的流速高于外层,中央处物料在料筒中的停留加热时间短,这将进一步扩大径向温差。用这种温度分布不均匀的熔体成型的塑料制品,会有诸多的质量问题。料筒中装有分流梭后,仍然存在温差。因此,柱塞式注射机的料筒和喷嘴的加热温度要高些,让中央处的物料也能熔融。但这易造成料筒壁附近的物料热分解。如果延长物料在料筒中停留时间,则会降低注射生产率。在螺杆式注塑装置内,由于螺杆的剪切和混合作用,加速了料筒的热传导并产生摩擦热,物料升温快而且温度均匀。在塑化时螺杆的转速提高,剪切作用强烈时,物料的温度会超过料筒和喷嘴的加热温度,见图3-38所示。
图3-38 注射机料筒内塑料的温度变化曲线
a)轴向温度分布 b)径向温度分布 1—剪切作用强烈的螺杆式注射机 2—剪切作用平常的螺杆式注射机 3—柱塞式注射机的料筒壁附近 4—柱塞式注射机的料筒中央
3.背压压力和螺杆转速
背压压力和螺杆转速是不容忽视的工艺参数。保证各种塑料物料有优良的塑化质量,又有恰当的塑化时间,要考虑众多的因素。
(1)背压压力 背压压力是螺杆在预塑成型物料时,对其前端汇集的熔体所施加的反压力,也称塑化压力,简称背压。增大背压可驱除物料中的气体,提高熔体的密实程度。螺杆前端熔体的内压力增大后,螺杆后退速度减小,螺杆对物料的剪切作用加强,摩擦热量增多,熔体温度上升,塑化效果提高。
以式(3-18)分析,单增大背压pb会增加压力流流率Qp和漏流流率Ql,使塑化能力下降,必须同时提高螺杆转速n,才既能提高塑化效果,又提高塑化能力。背压增大后螺杆后退移动速度减慢,塑化时间延长是必然的。但物料塑化应该在注塑周期内完成计量。
背压的大小与塑料品种、喷嘴种类和塑化加料方式有关,并与螺杆转速相对应。螺杆的传动额定功率是有限的,过大背压和转速,会使螺杆转矩不足,传动系统过载。因此有以下三方面考量。
1)采用直通式喷嘴和后加料方式塑化时,开放式喷嘴在较长时间处于对空状态,容易发生流涎现象,因此而应该用较小背压。采用阀式喷嘴和前加料方式时,背压可取大些。
2)对于热敏性的塑料,例如硬聚氯乙烯、聚甲醛和聚三氟氯乙烯等,为防止塑化时剪切摩擦力过大引起热分解,背压应尽量取小值。
3)对于高黏度的塑料,例如聚碳酸酯、聚砜和聚苯醚等,在一定的背压下,螺杆以低转速高转矩剪切塑化。背压应随塑料品种调节大小,但不宜使用过大背压,以防止螺杆的传动功率超载。
(2)螺杆转速 塑化时螺杆的转矩和旋转速度是物料在输送中被剪切和混合的原动力。螺杆转速影响塑化能力和塑化效果。一般首先以塑料熔体的黏度考虑螺杆的转速。低黏度物料的转速较低。但是,它与背压、转矩和塑化能量有以下三方面的复杂关系。
1)提高螺杆转速增大塑化能力,缩短塑化时间,但是对塑化效果是不利的,会使物料的混合和均化质量下降。必须给以一定的背压,保证足够塑化时间,补偿塑化质量。
2)螺杆转速提高后,更大的传动转矩给力物料输送和剪切混合。背压提升也会提高螺杆的工作转矩。
3)在高转速、大转矩和高背压作用下,螺旋槽中物料剪切产生热量增大,熔料的塑化温度提升。在塑化能量中,机械剪切能量大于料筒外加热能。为防止熔体过热,可适当降低料筒加热温度。
通用注射机的塑化装置,按塑化热塑性塑料的黏度所需转矩设计螺杆直径。再按塑化速率(螺杆应有的圆周速度v=0.4~1.5m/s),由机械传动提供相应的加工转速。因此,加工人员理应选择的圆周速度v,根据螺杆直径确定转速n。对于直径为50~70mm的螺杆,常用注射机能提供的螺杆最高转速为400~500r/min,最大背压为20~30MPa,已经能满足各种热塑性塑料塑化所需的机械能。表3-30可供选择螺杆转速和塑化背压参考,但要以正确使用喷嘴类型和加料方式为前提,还需考虑塑料品级和塑化温度,权衡塑化能力和质量,进行修正调节。
表3-30 部分塑料的背压和螺杆转速(推荐)
3.3.3 模具的温度和冷却时间
模具的温度决定了各种成型制件的冷却时间。模具温度和冷却时间是密切相关的工艺参数,也是注射模的温度调节系统设计的前提。
1.模具温度
塑料熔体在型腔内凝固时将释放热量,与注射模进行热交换。模具温度调节系统是使整个成型型腔壁面,在整个批量生产中保持合适的温度。
(1)模具温度对注塑件质量的影响 高温塑料熔体在模具型腔内凝固成制品时,将释放大量的热量。为适应各种不同塑料品种,需将型腔壁维持在某一适当温度。模具温度对制件质量的影响如下所述。
1)模具温度过高,会使制品在脱模过程中和脱模后发生变形,使其形状和尺寸精度降低。
2)模具温度过低,会降低塑料熔体的流动性,使制件轮廓不清,甚至不能完全充满型腔。或在充模过程中,由于熔体前锋的温度降低过多而产生明显的冷接缝,导致制品的力学性能下降。过低的模温,还会使制品表面不光滑,产生各种表面缺陷。
3)低温充模时,如果熔体流速不是足够高,则制品内残余应力较大,易引起翘曲变形或应力开裂。特别是某些高黏度的塑料,此种现象尤为明显。
4)通常对柔性的塑料,如聚烯烃等,应该使用低的模具温度,以降低其制品的成型收缩率,提高制件尺寸精度,并缩短成型周期,提高生产效率。
5)对于某些结晶型塑料,例如聚甲醛等,使用高的模温有利于结晶过程进行。有利的结晶,能提高制品的密度和结晶度,避免其制品在存放或使用过程中尺寸发生变化。
6)对于熔体黏度高的刚性塑料,例如聚碳酸酯等,使用高模温有利于流动充模,可降低其制品的应力开裂现象。
注射模具温度的波动及分布不均匀,也会使塑料制品质量变坏。模温直接关系制品的成型收缩率。模温波动会使批量生产制品尺寸不稳定,从而降低制品尺寸精度,甚至出现尺寸误差过大的废品。这对成型收缩率较大的结晶型塑料影响更为明显。
模具型腔温度分布的不均匀,例如模具型芯壁和型腔壁面温差过大,会导致注塑件厚度截面上残余应力分布不均匀,固化后注塑件会出现变形翘曲。塑料件中局部范围残余应力过大会引起裂纹和开裂。这对刚硬的聚碳酸酯等制品尤为重要。
总之,如图3-39所示,提高模温能改善制品表面的粗糙度,使轮廓清晰,熔合缝不显现。提高模温有利于结晶型塑料的结晶过程,有利于高黏度熔体的充模流动,也有利于减小制品中残余应力;但是会延长冷却时间和注射成型周期,也会使脱模温度过高,使注塑件在脱模中受到损伤。
(2)模具温度对生产效率的影响 冷却时间在整个注射成型周期中约占50%~80%。在保证注塑件质量前提下,限制和缩短冷却时间是提高生产效率的关键。让高温熔体尽快降温固化,模温调节系统应有较高的冷却效率。注入模具的塑料熔体所具有的热量,由模具传导、对流和辐射,散传于大气和注射机的,仅占5%~30%。热量大部分由冷却水携走。缩短冷却时间途径有三个方面。
1)冷却水应处于湍流状态。模具冷却管道中冷却水应处于高速湍流状态,流速v=0.5~1.5m/s,甚至更高。雷诺数Re>4000,使冷却管道孔壁与冷却介质之间的传热系数提高。资料表明,湍流流体在Re>104时,其传热能力比层流高10~20倍。
2)扩大模具与冷却水的温差。在模温一定时,采用低温的冷却水。但倘若设计不当,会加剧模温分布的不均匀。采用低于室温的冷却水时,有可能使型腔表面凝聚大气中的水分。
3)增大冷却介质的传热面积。也就是尽量增大管道孔径和增加孔数,但是受到模具结构(例如脱模零件、镶块接缝)的限制。对于大型注射模,为提高制件的合格率,在开机前必须将模具预热到适宜温度。为此,有些注射模备有加热和冷却两套装置。
图3-39 模具温度对塑料的一些成型条件和制品性能的影响
1—塑料熔体的黏度 2—熔合缝的强度 3—注射生产效率 4—制品内残余应力 5—制品表面粗糙度 6—制品的冷却时间 7—制品的密度和结晶度 8—成型收缩率 9—制品的翘曲变形
2.冷却时间计算
注射模不仅是射料熔体的成型设备,而且还是热交换器。模具温度调节系统直接关系注塑件的质量和生产效率,是注射模设计的核心内容之一。大型注射模具的冷却系统设计尤其重要,计算也较为复杂。对于大多数模具温度较低的塑料注射,仅设置模具冷却系统。但对于模温超过80℃的塑料,以及大型模具还需要设置加热装置。
注射成型周期是指完成一次注射成型工艺过程所需的时间。它包含注射成型过程中所有的时间,直接关系到注射成型生产效率。注射成型周期的时间组成如图3-3所示。注射成型周期由四部分组成:注射时间,约占个成型周期的5%;脱模推出制件时间,约占10%;其他操作时间,约占5%;冷却时间,约占80%。合理确定冷却时间是保证制件质量和提高生产效率的关键所在。
注射过程中塑料熔体冷却时间,通常是指塑料熔体从充满模具型腔起,到可以开模取出注塑件为止的时间。可以开模取出注塑件的时间,常以注塑件已充分凝固,具有一定强度和刚度为准。用注塑件厚度计算冷却时间的计算式,按无定形和结晶型塑料分为两类。
(1)无定形塑料
1)薄壁塑件。无定形注塑件的薄壁制品,通常按注塑件断面的平均温度tx,由式(2-100)计算冷却到该温度的时间。
式中 k——塑料的热扩散系数(mm2/s),查表3-31;
H——注塑件的厚度(mm);
Tc——注射塑料熔体的初始温度(℃),查表3-31;
Tm——模具温度(℃),查表3-31;
Tx——注塑件的平均脱模温度,应低于塑料材料的热变形温度(℃),其冷却时间查表3-31。
表3-31 部分塑料成型冷却时间计算的参考数值
2)厚壁制品。只要其厚度方向的两表面皮层有足够刚性就可脱模。最厚部位的中心层温度大致在该物料的热变形温度附近,就可用塑料的热变形温度或略低于该温度作为脱模温度Ty,由式(2-99)来计算冷却到该温度的时间。
式中 Ty——制件最厚部位中心层达到的脱模温度(℃),查表3-31。
H、k、Tc和Tm含义同上。
使用式(3-20),还要进一步校验注塑件各表面层所达到的温度,以判断凝固程度。制品厚度方向的温度以中心层为对称轴,呈抛物线分布规律。定义x变量为距中心层的位置,则有
式中 T(x)——注塑件脱模时,距中心层x的断面层的温度(℃);
其中 x——距注塑件厚度中心层的任意断面距离(mm);
Tc、Tm、k、H和Ty含义同前。
使用此式的前提是制品厚度两侧模具型腔壁温度Tm相等。若有温差,则温度分布抛物线不对中心层对称。
以上两种公式在推导过程中,假定充模熔料温度是均一的;假设注塑件在模内冷却过程中,始终与型腔壁紧密接触;在冷却过程中,假设模具型腔表面的温度均匀,且始终保持均一;按两平行的大平面壁的注塑件来推导,忽略成型件侧面的冷却作用。故计算结果存在与实际的偏差。塑料的热扩散系数随着温度而变化,结晶型塑料的这种情况比较明显。所以以上计算式对结晶型塑料不适用。
(2)结晶型塑料 以下是三种结晶型塑料冷却时间的经验公式。
1)聚乙烯(ρ=0.945g/cm3),适用范围Tc=193.3~248.9℃,Tm=4.4~79.4℃。
棒:
板:
2)聚丙烯,适用范围Tc=232.2~282.2℃,Tm=4.4~79.4℃。
棒:
板:
3)聚甲醛,适用范围Tc>190℃,Tm<125℃。
棒:
板:
以上各式中,R为棒状注塑件半径(mm);H为板状注塑件厚度(mm)。
表3-32是七种塑料制件在不同壁厚下的冷却时间。必须明了,注塑件的冷却时间与壁厚的平方成正比关系。
表3-32 塑料制品厚度与所需冷却时间
3.3.4 常用塑料的注射成型工艺
注射成型工艺的选择和拟定,必须充分掌握塑料材料的性能。由于塑料材料品种繁多,新品种又不断涌现,必需取得合成树脂企业提供的材料说明书。它应该详细和准确地列出塑料的热性能和力学性能、塑料黏流态的流变曲线和熔体流动速率及注射成型收缩率。也有提供注射机料筒、喷嘴和模具温度等控制参量。工艺的选择是科学分析和技术应用的过程,也是不断修正优化的过程。现将五种常见的热塑性塑料的注射成型工艺作综合性分析和介绍。
1.聚苯乙烯塑料
聚苯乙烯塑料本身的吸水率很小,成型一般制件可以不予干燥,但对外观质量要求较高的注塑件,可在成型前进行干燥处理,在70~80℃温度下干燥2~4h。
聚苯乙烯为无定形塑料,黏度适宜,流动性较好。聚苯乙烯的成型温度范围较宽,热稳定性也好,注射成型比较容易。在黏流态时熔料的温度有少许波动,不会影响注射流动过程。
如图3-40流变曲线所示,聚苯乙烯熔料的黏度对剪切速率和温度都比较敏感,在注射成型中无论是增大注射速率,还是升高料筒温度都会使黏度下降明显。注射压力为60~120MPa,较高的注射压力让熔体高速注入型腔,但模具型腔内压力尽量低些,并分布均匀。料筒温度可控制在140~230℃之间,喷嘴温度为170~190℃。把物料温度加热到190~215℃,有利熔体流畅充模。但料温过高使聚合物过热分解,使制件上出现花斑、银纹、发白、泛黄和气泡。这对透明的聚苯乙烯制品是严重的缺陷。
图3-40 聚苯乙烯的表观黏度ηa与剪切速率的流变曲线(MFI=10g/10min,200℃)
聚苯乙烯的分子链刚硬,成型中容易产生分子取向和残余应力,甚至在制件中生成银纹和开裂。聚苯乙烯注塑件的冷却速度不宜过快(模具常用水冷却,模具温度为40~45℃)。为此:模具温度应维持稳定,模具壁的温度分布均衡,其温差低于±2.5℃;并对制件进行退火处理,将制件放入65~75℃热水中处理1~4h,然后缓慢冷却至室温;而且聚苯乙烯不宜带有金属嵌件,嵌件周边塑料容易开裂;聚苯乙烯制件浇口的附近区域,内应力集中,容易产生各种缺陷,在注射模设计时,要注意优化浇口位置和类型。
聚苯乙烯塑料的成型收缩率为0.3%~0.7%,制件的弹性小,硬度高,脱模困难。为使制件顺利脱模,模具的型芯取较大的斜度1°~2°。
2.聚丙烯塑料
聚丙烯为结晶型聚合物,吸水率很低,约为0.03%~0.04%,注射前一般不需要干燥,必要时可在80~100℃下干燥3~4h。
聚丙烯在160~175℃有比较明显的熔点,分解温度为350℃,所以注射成型的熔体温度较宽,约为200~260℃。注射级的聚丙烯的熔体流动速率为15g/10min左右,熔体的流动性较好。一般料筒温度控制在210~270℃,喷嘴温度可比料筒温度低10~30℃。生产薄壁制品时可取较高的料筒温度;反之,生产大型厚壁制品时为防止熔料在料筒内停留时间过长而分解,料筒温度应适当低些。聚丙烯在270~300℃以上的高温下,长时间停留会有热降解的可能。
如图3-41流变曲线所示,聚丙烯的黏度对剪切速率的依赖性比温度影响大。因此,在注射充模时,提高注射速率和注射压力来改善熔体的流动性,比通过提高温度有利。尽管高温对提高熔体流动性影响不大。但可改善压力传递和补缩,有利于克服制件的凹陷,减小收缩在各位置和各方向的差异。一般采用的注塑压力为70~120MPa。
图3-41 聚丙烯的表观黏度ηa与剪切速率γ·的流变曲线(MFI=31.6g/10min)
聚丙烯的结晶能力较强,120~130℃时具有最高的结晶速率,提高模具温度将有助于增加注塑件的结晶度。采用较高的模具温度60~90℃,不仅有利于结晶,也有利于分子链的松弛,减轻制品的取向,并降低残余应力,从而改善制品的力学性能;但是由于冷却时间延长,影响了注射生产率。因此,只有在成型长流程和复杂制件或充模流动不佳时,才采用高模温。一般情况下,多维持30~50℃的模具温度。倘若模具温度过低,注塑件冷却太快,浇口冻结过早,不仅制品的密度小,结晶度低,而且残余应力大,制品质量变差。制件冷却速度不仅影响结晶度,还影响晶体结构。骤冷时分子结构形态不稳定,力学和物理性能较差。聚丙烯注射模采用针点式小浇口时,成型制件的收缩率较大,因此,要以高温熔料注射弥补。采用矩形浇口,有中等截面,保证充分注射和补缩,降低制品的收缩。
由于聚丙烯的玻璃化转变温度低于室温,其制件在室温下存放中会有收缩现象。原因是聚丙烯注塑件在脱模后仍在结晶。制件的厚度越大,后期收缩量越大。后期收缩量的90%约在制品脱模后6h内完成,剩余10%发生在随后的10天内。对尺寸稳定性要求较高的制件,应将制件在沸水中浸泡10~15min,进行退火处理。
3.ABS塑料
ABS是丙烯腈-丁二烯-苯乙烯的三元共聚物。与聚苯乙烯相比,它具有较好的综合性能。丙烯腈赋予ABS较高的耐热性和表面硬度。但因极性的腈基易吸水,吸水率为0.2%~0.45%,表面吸水率可达0.3%~0.8%。所以ABS粒料成型前必须进行干燥处理。料斗干燥时,加热温度为70~85℃,需2~4h,使含水量降至0.1%以下。如果对于制品有优良光泽要求,或在湿热的季节,干燥加热时间需长达4~8h,还须防止已干燥的ABS再度受潮。
ABS是无定形塑料,黏流态的成型温度范围较宽,比聚苯乙烯熔体有较高些的黏度,对流动剪切速率敏感(见图2-10的ABS流变曲线)。对薄壁和复杂的制件,注射生产时,采用较高的注射速率和压力;在注射成型时,常用0.6~1.8mm直径的针点式浇口。因此,其浇口冻结时刻的型腔压力决定了制品的质量。注射成型时,料筒温度在190~250℃。提高ABS物料温度,熔体黏度降低很少。熔体注射温度高于250℃,首先导致ABS中丁二烯降解,将会分解和产生有毒挥发物,物料变色甚至炭化。ABS注射模的温度相对较高,在注射大型复杂制品时,需要有60~80℃高温。通过改变ABS中各单体的组分的比例,有许多品种类别的ABS,它们有不同的性能,加工的工艺条件也有差异,见表3-33。
表3-33 ABS塑料螺杆式注射机成型工艺
成型后的注塑件,一般不需要热处理。如果注塑件要表面电镀装饰时,应在70~75℃空气介质中,视壁厚厚度处理2~4h。以消除残余应力,得到装饰完好的制品。
ABS塑料的成型收缩率较小,一般为0.4%~0.7%。ABS塑料容易着色,可以注射成型各种色泽艳丽的制件。模具型腔经研磨抛光,达到镜面的表面粗糙度;采用适宜的注射工艺,较高的模具温度,可以得到高度光泽的制品。
4.聚酰胺塑料
聚酰胺是指主链上含有大量重复酰胺键的塑料。其化学结构有差异,品种众多。其中聚酰胺6、聚酰胺66、聚酰胺610和聚酰胺1010应用较多。
聚酰胺在分子结构中因含有亲水的酰胺基,容易吸水。聚酰胺6吸水性最高;聚酰胺66次之;聚酰胺610的吸水率为聚酰胺66的一半;聚酰胺1010的吸水性最低。聚酰胺6的吸水率在平衡状态为1.3%~3.0%。水分对这些塑料的物理性能有明显的影响。如果用已吸湿的聚酰胺物料注射成型,会引起熔体的黏度下降,使注塑件表面出现气泡、银丝和斑纹等缺陷,制品的内在质量和力学性能变差。在成型前必须将物料的含水量降至0.2%以下。干燥处理聚酰胺塑料时应防止氧化变色,最好用真空干燥,脱水率高而时间短。干燥条件为:真空度9.3×105 Pa,烘箱温度90~110℃;料层厚度25mm以下,干燥时间8~12h;常压下干燥空气温度要低些,干燥时间增加。干燥处理后的塑料即时加盖,雨天的存放时间不超过1h,晴天限制在3h内。如果采用沸腾干燥方法,见表3-20;料斗式干燥见表3-21。
聚酰胺为结晶型塑料,有明显的熔点,视不同品种而异,大致在200~270℃。聚酰胺的熔融温度较高,而其范围较窄,约10℃左右,如图3-42所示(PA6的流变曲线)。而且,提高熔体流动剪切速率时,对其黏度下降影响较小。采用螺杆式注射机,料筒温度比其熔点高10~30℃,因此,应采用压缩段较短的突变螺杆。聚酰胺熔体的黏度低,有很大的充模流程比。为防止螺杆注射推进时发生过多漏流,螺杆头部应有滑动式止逆环。熔料也容易在注射模中泄漏,溢料会在制件上生成飞边,所以要求注射模上运动零件的配合间隙要很小。为防止喷嘴口熔体流涎,可用阀式喷嘴,一般用外弹簧针式自闭喷嘴为好。而且熔体的热稳定性差,容易分解,生产中料筒的加热温度不宜超过300℃,熔料加热时间不要超过30min。几种聚酰胺塑料在螺杆式注射机的注射成型工艺参数见表3-34。
图3-42 聚酰胺6(PA6)的ηa与的流变曲线(MFI=50g/10min,235℃)
表3-34 几种聚酰胺塑料螺杆式注射机的注射成型工艺参数
模具温度(通常控制在40~100℃)对制品的物理和力学性能影响较大。模温高时结晶度高,制品的硬度、耐磨性、刚性和耐热等性能提高;模温低时,结晶度低,制品的拉断伸长率、韧性和透明性较好。一般应控制模具温度,使制品有适宜的结晶度,从而得到较好的综合性能。模具温度还取决于注塑件的壁厚。厚壁制品应有较高模具温度,而且还能减小残余应力。为此,注射模同时兼备有冷却和加热的温度调节装置。
聚酰胺注塑件在脱模后尺寸不稳定。搁置或退火处理能使它发生收缩,而吸湿则会引起膨胀。按照机械零件的精度要求,进行退火处理和/或调湿处理。对于使用温度高于80℃,或精度要求较高的聚酰胺制品需退火处理。聚酰胺制品退火处理在隔氧条件下进行,将制品放在热油、液体石蜡或充氮炉中,在100~120℃温度下处理一定时间,按厚度需10~60min,然后缓慢冷却至室温。聚酰胺的调湿处理见3.2.3的制件后处理一节所述。调湿要用热水处理,加快达到吸湿平衡,也隔绝空气防止氧化,同时也起到退火作用。
5.聚碳酸酯塑料
聚碳酸酯是刚硬又有韧性的工程塑料。但其制品易发生环境应力裂纹,难以带金属嵌件注射成型。用于注射成型的聚碳酸酯相对分子质量常为2万~4万。聚碳酸酯的热稳定性和力学强度随相对分子质量的增加而提高。其熔体黏度也随着相对分子质量的增加而加大。
聚碳酸酯主链上有亲水的酯基,容易吸水分解。在高温下对水分很敏感,微量水分也会造成聚碳酸酯水解,相对分子质量下降,性能劣化,所以在成型前必须严格干燥。可采用沸腾干燥(温度120~140℃,时间1~2h)、真空干燥(温度110℃,真空度9.5×105 Pa,时间10~25h)。干燥后的含水量应小于0.02%。注射时最好用注射机料斗式干燥器再干燥。物料的干燥程度不足,对空注射时从喷嘴流出的条料表面不光亮,内部夹有气泡。干燥程度很差时,深色的熔料黏度很低,并有分解气体喷出。干燥合格的喷出条料应均匀光亮,无细丝和气泡。
聚碳酸酯属于无定形塑料,其玻璃化转变温度较高,为149~150℃,其黏流态温度在220~240℃。由于主链上刚性的苯环存在,熔体的黏度比聚苯乙烯高很多,而且其流动特性接近牛顿流体(见图3-43)。聚碳酸酯有较高的热稳定性和很宽的成型温度范围。熔体黏度受剪切速率的影响较小,但对温度的变化十分敏感,因此,在注射成型时,通过提高温度来降低黏度,比增大压力更有效。
图3-43 聚碳酸酯的表观黏度ηa与剪切速率γ·的流变曲线(MFI=10g/10min,330℃)
成型温度的选择与聚碳酸酯的相对分子质量、制件的壁厚和注射机的类型等有关,一般控制在250~310℃范围内。注射成型应选用相对分子质量稍低物料,其熔体有较好的流动性,但制品的韧性会有所降低。为保证薄壁制件型腔内的充模流动性,应有较高的成型温度(285~310℃)。螺杆式注射机的成型温度为250~285℃,柱塞式的为270~310℃。两类注射机的喷嘴均应加热,温度为260~310℃。加料口一端的料筒温度要求高于230℃,应在聚碳酸酯的软化温度以上,以提高物料升温塑化的速率。
聚碳酸酯熔料的黏度很高,成型长流程和薄壁的复杂注塑件需要较高的注射压力。螺杆式注射机为80~130MPa,柱塞式为100~160MPa。选用高料温和低压力有利于减少成型制件内的残余应力。由于聚碳酸酯的成型收缩率较小,保压时间不应过长,以免制件脱模困难、出现应力开裂。
聚碳酸酯注射模的模具温度为80~120℃。对薄壁制件模温为80~100℃,对厚壁制件成型的模温为100~120℃。成型聚碳酸酯的注射模,应该备有加热装置(用热油循环或用电热棒或电热板)。较高的模温可减小注塑件中的温差残余应力,但延长了注射周期。金属嵌件在放入模具前,要预热到模具温度。
聚碳酸酯制品内的残余应力可通过退火处理基本消除。退火加热温度为100~130℃,处理时间视制件的厚度而定,以1~2h/mm计,保温2~8h。热处理时间对制件的性能影响显著,如图3-44所示。其硬度、弯曲强度、热变形温度和拉伸屈服极限都有提高;但是制件的冲击强度和断裂伸长率会有下降,不过在保温2h之内并不明显。
图3-44 热处理时间对聚碳酸酯制件性能的影响
1—洛氏硬度(120℃) 2—弯曲强度(130℃) 3—冲击强度(130℃) 4—热变形温度(130℃) 5—拉伸屈服极限(130℃)