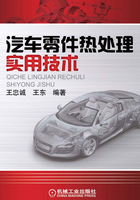
1.2汽车零件热处理特点
汽车零件用材料包括钢铁材料、非铁金属及其他高温合金材料等,其中大部分材料只有通过热处理,才能达到改变材料性能,即改善其硬度、强度和可加工性的目的。材料的性能取决于组织结构、碳含量和合金元素的成分等,因此根据汽车零件的服役条件与技术要求,选择合理的热处理设备与工艺,达到延长汽车零件使用寿命、提高力学性能的目的。
汽车零件的热处理技术要求决定了其采用的热处理工艺与特点。目前汽车制造对零件的热处理提出了具体的要求,除材料本身外,还提出了具体的热处理工艺手段,故汽车制造一直是热处理技术的主要应用领域,各种热处理技术得到了广泛应用。
1.2.1汽车零件的整体热处理特点
汽车零件材料要达到使用技术要求,则必须进行合理选材与必要的热处理,一般零件的热处理包括退火、正火、淬火与回火、固溶与时效等,其是依据零件的服役条件来选择的。
1)退火工序多用于铸铁(合金铸铁)件的热处理,如去应力退火、低温退火等,以消除铸造后的内应力与加工应力等,确保零件尺寸的稳定与后续加工。通常包括灰铸铁缸体、缸盖、飞轮、变速器壳、离合器壳、后桥壳等,它们的退火温度均低于650℃,无组织的转变,通常采用箱式炉、推杆炉、振底炉、台车炉等作为加热设备,生产率不高。
2)正火工序则用于钢制曲轴、前轴、转向节、半轴、二轴、变速器齿轮、后桥齿轮等零件的锻造后处理,目的是提高基体的表面硬度与心部强度,便于进行机械加工,获得要求的力学性能,满足使用要求。正火多采用大型箱式炉、台车炉、推杆炉等,少数采用盐浴炉、井式炉等,冷却方式多为空冷、喷雾冷却等,获得的组织通常为F+P。
3)淬火与回火用于渗碳齿轮与活塞销、钢制钢板弹簧与气门弹簧、马氏体钢制气门、前轴、转向节、半轴等零件的热处理,包括低温回火、中温回火与高温回火等,获得要求的力学性能与表面硬度等,是最为常见的热处理工艺方法。通常采用可控气氛加热设备,防止零件表面的氧化脱碳,如保护气氛网带炉、振底炉、多用炉(箱式炉),具有生产率高、质量稳定性好、机械化与自动化程度高、工作环境清洁等特点,因此应用十分广泛。
调质处理是比较常见的热处理工艺,由于汽车零件是大批量生产的,故多选用网带炉、铸链炉进行热处理,调质处理既可作为预备热处理,也可作为最终热处理,处理后的零件具有良好的综合力学性能。
4)固溶与时效用于非铁金属与合金、奥氏体耐热钢等零件的热处理,以获得要求的力学性能或满足特殊的服役要求,如用于铸造铝合金制缸体与缸盖、活塞、奥氏体钢制气门等,是一类比较特殊的热处理工艺。采用的加热设备通常为盐浴炉、高温燃气炉、高温保护气氛炉、井式炉、多用炉等,均为周期性作业炉,具有劳动强度大、效率低等特点,用于特殊零件的热处理。
1.2.2汽车零件的常见基本热处理特点
1.调质处理
汽车零件的调质热处理可分为保护气氛调质热处理和一般调质热处理。保护气氛热处理能够保证零件在热处理过程中不会产生表面氧化、脱碳等缺陷,确保零件的表面质量。当调质处理后零件工作面需要后续加工时,采用一般热处理。根据零件的质量、大小,调质热处理设备有网带炉、铸链炉、料盘(料筐)推杆式炉、托架炉、悬挂式连续炉等。调质处理后的组织为回火索氏体,不允许有块状的铁素体,否则会降低零件的强度和韧性等,通常零件调质处理的硬度为30~38HRC(283~350HBW),以汽车紧固件热处理为例,调质热处理技术的发展主要有以下几方面:
(1)炉型 由于辐射管和网带寿命的大幅度提高,在国内标准件行业网带炉得到普遍应用。网带炉具有炉内布料、加热均匀,零件质量稳定,工作环境好等优点。特别是对于高强度螺栓的热处理,采用网带炉使质量有了可靠保证。
(2)碳势控制技术的应用 碳势控制技术在保护气氛调质生产线上得到普遍应用。采用碳势控制技术炉内碳势的控制精度可达到±0.03%,保证了零件热处理的表面质量。
(3)计算机技术的应用 通过计算机能够按照工艺设定自动完成工件生产的全过程,记录、保存工件生产中的各种工艺参数,具有完善的故障诊断、显示,安全警示及联锁功能。
(4)快速淬火油和水基淬火冷却介质的应用 快速淬火油的应用保证了高强度螺栓件的热处理内在质量。水基淬火冷却介质的应用解决了零件淬油不硬、淬水开裂以及零件淬火变形的质量问题。
2.锻造余热热处理
大部分汽车结构零件采用热锻成形工艺。利用锻造余热实施毛坯的热处理是节能的重要措施。如采用锻造余热等温退火、锻造余热淬火,可以获得利于后续加工的组织和硬度,省去了再次加热能耗,节能效果显著。利用锻造余热热处理的零件有各类齿轮毛坯、前轴、转向节、摇臂、花键轴、曲轴、连杆等。对于齿坯的余热等温退火,为了保证锻造余热热处理的组织、硬度均匀性,需要严格控制终锻温度、中冷过程、等温温度等。对于余热淬火的零件,为保证零件的强韧化性能,除了直接淬火工艺外,也可以采用预冷至550~650℃,完成珠光体转变后,再次加热至奥氏体化温度的方法。主要目的是细化组织,获得良好的强韧化性能。
1.2.3汽车零件的表面热处理特点
1.感应热处理
在20世纪30年代,出现了感应热处理技术,感应热处理技术是一项高效、节能、环保的热处理技术,符合现代工业生产的3S和3C标准(Sure可靠、Safe安全、Saving节约及Cool低温、Clean清洁、Clam安静),几十年来有了迅速的发展,特别是在汽车生产方面得到了广泛应用。
从最初的曲轴轴颈感应淬火,逐渐扩展到汽车发动机、汽车底盘等汽车零件上。我国的感应热处理起步于20世纪50年代,首先应用于机床制造工业与纺织机机械制造工业,其后在汽车制造工业、拖拉机及工程机械、轴承工业、石油钻机与化工机械、铁路、重型机械、冶金机械、航空航天、农业机械制造、建筑材料等各个行业大量采用感应热处理技术。
感应热处理具有节能、高效、环保、劳动强度低、在线作业、自动化程度高等特点,故发展迅速,在国内外得到普遍的应用与推广。
目前典型的零件表面淬火,多应用于传递动力转矩的轴类零件:内燃机气门的杆端与盘锥面、曲轴轴颈、凸轮轴、花键轴、齿轮齿圈、半轴、等速万向节、变速叉、传动器轴、十字轴、齿轮轴、减振器、销轴、轴承座、制动凸轮、转向节等。感应热处理零件占汽车热处理零件的70%以上,是比较有前途的热处理工艺。
(1)感应热处理工艺与应用 感应热处理工艺中应用最多的为淬火,其次为回火与退火或正火。感应热处理工艺的调整是在电源设备(频率及功率已经确定)、淬火机床、感应器(工艺装备件已经具备)、辅助装置(淬火冷却介质浓度、温度等)以及需要淬火调整的零件达到该工序的要求后进行的。感应淬火的工艺方式与适用范围见表1-4。
表1-4感应淬火的工艺方式与适用范围
感应淬火件回火的目的是降低淬火应力,避免产生淬火裂纹或降低硬度,达到零件的热处理技术要求。感应淬火后的回火有三种方式:自回火、感应回火、炉中回火。
(2)感应淬火件的质量检验 感应淬火件的质量检验项目与要求见表1-5。
表1-5感应淬火件的质量检验项目与要求
2.火焰淬火
火焰淬火的淬火温度比普通的淬火温度要高50~70℃,加热速度快,因此工件经火焰淬火后硬化层不厚,不适合处理十分重要的零件。硬化层的深度主要取决于零件的淬透性、尺寸、加热层深度、冷却条件等因素。一般推荐水压为0.1~0.2MPa。整体浸入冷却油中,另外根据零件的硬度也可采用压缩空气、乳化油等淬火冷却介质。
根据加热方式和工件的形状、大小及淬火后要求不同等,火焰淬火有以下四种:静止火焰淬火法、旋转火焰淬火法、推进火焰淬火法与联合火焰淬火法。
火焰淬火工艺参数见表1-6。
表1-6火焰淬火工艺参数
3.电解液淬火
零件作为阴极浸入电解液中,当电路通以直流电时,电解液发生电解,此时氢离子趋向零件(阴极),在周围形成了氢气膜。由于氢气膜的电阻大,故电流通过时将产生很大的热量将零件加热(称为阴极效应)。被加热到淬火温度的零件,一旦切断电源立即由电解液迅速冷却而完成淬火,可采用端部自由加热、端面绝缘加热、回转加热和连续加热等方式。
1)电解液淬火所用的电解液为质量分数为5%~10%的碳酸钠水溶液,也可采用5%~10%的碳酸钾、氢氧化钠、氢氧化钾、硫酸钠、氯化钙、氯化钡以及硝酸钙等水溶液。
2)电解液加热所用电压与电流应控制在要求的范围内,电流可通过对总电流及浸入电解液中工件面积的调节来实现。
3)整个过程中,电解液的温度应控制在20~40℃,最高不超过60℃。
资料介绍,除高频感应淬火可用作内燃机进、排气门杆端的表面淬火外,接触电阻加热淬火也用于该类产品的顶端面淬火。气门的杆部材料为40Cr,技术要求为杆端淬硬层深度为2~4mm,硬度为45~62HRC,则具体的工艺参数为:电解液为质量分数为12%~15%的碳酸钠水溶液,温度为30~60℃,直流电压为180V,电流为10~15A,通电时间为4.5s。
需要注意的是,在生产过程中,零件表面不得有过热、烧熔、腐蚀以及任何形式的裂纹等缺陷产生;硬化层组织为细小马氏体,晶粒度应不大于5级,过渡层为托氏体和索氏体,心部为原始组织。
4.激光热处理
激光热处理(即激光表面淬火)又称为激光相变硬化,因其具有快速的加热速度与冷却速度,故可获得极细的马氏体组织,此方法适用于碳素钢、中碳低合金钢、铸铁等材料的表面淬火。因此大量用于汽车、拖拉机等的发动机缸体和缸套内壁的处理,以提高其耐磨性和使用寿命,此外,还可用于曲轴、齿轮、模具、刀具、活塞环等的表面硬化处理。
1.2.4汽车零件的化学热处理特点
钢铁件化学热处理的目的是改变表层化学成分与组织结构,以提高表面的力学性能、物理与化学性能。
采用化学热处理可有效提高模具表面的耐磨性、抗咬合性、抗氧化性、抗粘着性、抗冷热疲劳性等性能,同时可使零件内部保持原有的强韧性,化学热处理均是以提高零件的耐磨性与使用寿命为目的的。
汽车零件的化学热处理包括渗碳、碳氮共渗、渗氮、氮碳共渗、硫氮碳共渗等,应用比较广泛的为渗碳、碳氮共渗、渗氮与氮碳共渗,其中渗碳与氮碳共渗零件所占比例较大。
1.渗碳
渗碳热处理的主要目的是使零件获得良好的抗疲劳性能和耐磨性,保证零件的使用性能与可靠性。同时由于心部与表层的碳含量不同,硬化后的表面获得了有利的残留应力分布,从而提高了渗碳工件的弯曲疲劳强度和接触疲劳强度。采用渗碳淬火强化热处理的零件有:汽车驱动桥的差速器齿轮、变速器轴齿类零件、转向器轴齿件、发动机活塞销、柴油机针阀体和齿轮零件、部分模具等。十几年来,渗碳热处理技术发展的重要标志是传感技术和计算机技术在生产中的应用。可实现对渗碳热处理工艺参数如温度、时间、碳势,淬火过程以及动作程序的完全自动控制,甚至根据零件的技术要求、材料牌号及特性等,系统可以自动生成工艺,实现智能控制。
汽车零件的渗碳热处理装备有箱式炉,单排、双排、多排连续炉以及真空炉等多种热处理设备。
汽车零件渗碳热处理技术有如下特点:①工业计算机对炉温、碳势、自动线动作程序进行监控与数据自动采集;②对自动线渗碳热处理工艺过程进行自动跟踪与监控,实现渗碳工艺仿真与优化和零件渗碳质量的预测;③对炉内温度、碳势和动作进行实时显示及控制,系统故障自动诊断、显示及报警;④热处理生产工艺的全过程在线自动显示、记录以及保存和建档,可以建立可追踪的热处理质量管理系统。
气体渗碳多用于承受大冲击、高强度和使用硬度在58~62HRC范围内的小型模具、齿轮等。井式炉气体渗碳典型工艺曲线如图1-1所示。部分齿轮在井式炉中的典型气体渗碳工艺如图1-2和图1-3所示。
图1-1 井式炉气体渗碳典型工艺曲线
2.碳氮共渗
汽车零件碳氮共渗的目的是提高工件的表面硬度、耐磨性和耐疲劳性等,其中应用最广的为中温气体碳氮共渗,其共渗介质为渗碳和渗氮用混合气体,即在井式渗碳炉内滴入煤油(或甲苯、丙酮等),同时通入渗氮用氨气。共渗温度为820~860℃,气体碳氮共渗中的碳、氮含量主要取决于共渗温度,即共渗温度越高,共渗层中碳含量越高,氮含量越低;反之共渗温度越低,共渗层中的碳含量越低,氮含量越高。零件完成渗碳、碳氮共渗(排气、强烈渗碳或碳氮、扩散后),对于可直接淬火的零件,可随炉冷却到适宜的淬火温度,并保温一定时间,待零件的内外温度均匀后出炉,而对于需要重新加热的零件,可在出炉后在空气中冷却或放入缓冷罐,为了减少零件的表面氧化、脱碳和变形,也可保持扩散阶段的渗剂流量,并随炉降温至500~550℃再出炉。
进行碳氮共渗的汽车零件有汽车变速器齿轮、差速器齿轮、部分曲轴、活塞销等。
图1-2 变速器齿轮的气体渗碳工艺规范
注:材料20CrMnTi,渗层深度为0.8~1.2mm,RQ3-75-9T。
图1-3 转向器齿轮的气体渗碳工艺规范
注:材料20CrMnTi,渗层深度为0.4mm,可控气氛多用炉。
3.渗氮
渗氮是将钢件置于含有活性氮原子的气氛中,加热到一定温度保温一定时间,使氮原子渗入工件表面形成渗氮层的热处理工艺。渗氮的目的是提高工件的表面硬度、耐磨性、疲劳强度及耐蚀性。常用的渗氮用钢为38CrMoAlA、Cr12、Cr12MoV、3Cr2W8V、5CrNiMo、4Cr5MoSiV等。模具渗氮前应进行调质处理,为了保持模具的整体性能,渗氮温度一般不超过调质处理的温度,一般渗氮温度为480~550℃。汽车零件进行渗氮的有活塞环、活塞杆、螺杆、部分齿轮等。
4.氮碳共渗
氮碳共渗后的工件表面形成了化学特性较稳定的渗氮物,可显著提高工件的耐磨性,具有良好的抗咬合、抗擦伤能力,可减轻粘模现象,另外可明显提高工件的抗疲劳性能,使工件具有良好的耐蚀性,一般认为经过氮碳共渗后的工件,其抗大气腐蚀的能力与发蓝、镀锌件相当,内燃机气门、曲轴等进行氮碳共渗后,表面的耐磨性成倍提高,耐蚀性明显提高,是一种十分有效的表面强化工艺手段。广泛用于模具(压铸模具、热挤压模、锤锻模、冲模、塑料模)、曲轴、凸轮轴、气门、挺杆、燃气管等领域,并取得了令人满意的效果。
图1-4所示为选用TJ-2氮碳共渗基盐对3Cr2W8V钢制气门用热挤压模进行氮碳共渗的工艺曲线,渗层深度为0.10~0.25mm,表面硬度在850HV以上,使用寿命比气体氮碳共渗提高80%。
图1-4 3Cr2W8V钢制气门用热挤压模氮碳共渗工艺曲线
汽车零件进行氮碳共渗的目的是提高耐磨性、抗擦伤性、耐蚀性和疲劳强度等,也是一种成本较低且变形小的热处理工艺,适用于大批量零件的生产,汽车内燃机气门、气门挺杆、曲轴等均采用了氮碳共渗工艺,表1-7为几种主要氮碳共渗工艺方法的比较,可以看出液体氮碳共渗具有明显的优势。
表1-7几种主要氮碳共渗工艺方法的比较
(续)