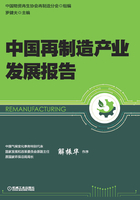
基础篇
Chapter 01
第一章 概述
第一节 什么是再制造
一、再制造的定义
再制造是把传统模式下到达使用寿命的产品,通过再制造技术及工艺(如修复技术、技术改造或再生等),使其质量或性能达到甚至超过原产品的技术措施或工程活动。宏观上讲,再制造是以废旧产品全生命周期设计和管理为指导,以实现其性能跨越式提升为目标,以优质、高效、节能、节材、环保为准则,以先进技术和产业化生产为手段,对废旧产品实施回收、拆解、清洗、检测、修复、改造或再生、装配、测试检验等一系列技术措施或工程活动的总称;微观而言,再制造是指在全生命周期内对失效零部件进行专业化修复、改造或再生的工序过程环节。
国家标准GB/T 28619—2012《再制造 术语》规定,再制造是对再制造毛坯进行专业化修复或升级改造,使其质量特性不低于原型新品水平的过程。其中质量特性包括产品功能、技术性能、绿色性、经济性等。再制造过程一般包括再制造毛坯的回收、检测、拆解、清洗、分类、评估、修复加工、再装配、检测、标识及包装等。
GB/T 28618—2012《机械产品再制造 通用技术要求》规范了机械产品再制造流程,如图1-1所示。
但是随着再制造生产实践活动的推进,发现很大一部分再制造产品只需性能达到或超过新品,就足以满足使用需要和寿命要求,无须强制所有再制造产品的质量达到或超过新品的质量,这样体现不出再制造的成本优势,反而会阻碍再制造产业的发展。

图1-1 机械产品再制造流程
再制造的出现完善了全生命周期的内涵,使得产品在使用周期的末端(报废阶段)不再成为固体垃圾,从而使传统、开放式生命周期(研制—使用—报废)转变为闭环式(研制—使用—退役—再生)的理想绿色产品生命周期,如图1-2所示。再制造不仅可以使废旧产品起死回生,而且还能更好地解决资源节约和环境污染问题。因此,再制造是对产品全生命周期的延伸和拓展,赋予了废旧产品新的寿命,形成了产品的多生命周期循环。

图1-2 闭环式生命周期
再制造的理念应该贯穿产品的全生命周期,如图1-3所示。在产品设计阶段,要考虑产品的再制造性设计;在产品的服役至报废阶段,要考虑产品的全生命周期信息跟踪;在产品的报废阶段,要考虑产品的非破坏性拆解、低排放式物理清洗,要进行零部件的失效分析及剩余寿命演变规律的探索,要完成零部件失效部位的具有高结合强度和良好摩擦学性能的表面涂层的设计、制备与加工,以及对表面涂层和零部件尺寸超差部位的机械平整加工及质量控制等。

图1-3 再制造在产品全生命周期中的地位
再制造的对象是“废旧产品”,既可以是设备、系统、设施,也可以是其零部件;既包括硬件,也包括软件。产品报废是指其寿命的终结,可分为物质寿命、技术寿命和经济寿命,通过对产品的维护和修理能延长其物质寿命和经济寿命,对其进行改造、升级可延长其技术寿命和经济寿命。在科技高速发展的今天,为适应产品更新换代、工艺改进、材料更新等需要,原生产线上的设备往往提前报废,一些耗能高、排污大的旧式产品(如一些老型号的电动机、锅炉)有时被企业或政府部门强制淘汰,诸多性能和科技含量低的过时产品会被市场抛弃,在这种情况下报废的产品一般都没有达到它的物质寿命,有些是半新甚至是全新产品,大部分零部件可直接使用或可通过再制造加工、改造成为新的产品。此外,来自不同渠道的旧品,主要包括更换下来的高品质的零部件,同样可通过再制造被重新使用。可见,再制造的对象是多种多样的,构成极其广泛。
再制造根据其加工范围可分为恢复性再制造、升级性再制造和综合性再制造。恢复性再制造,主要针对达到物理寿命和经济寿命的产品,在失效分析和寿命评估的基础上,把蕴含使用价值、由于功能性损坏或技术性淘汰等原因不再使用的产品作为再制造毛坯,采用表面工程等先进技术进行加工,使其尺寸和性能得以恢复。升级性再制造,主要针对已达到技术寿命的装备、不符合当前使用要求的装备或不符合节能减排要求的产品,通过技术改造、局部更新,特别是通过新材料、新技术、新工艺等的使用,改善和提升装备技术性能,延长装备的使用寿命,减少环境污染。综合性再制造主要是针对失效零部件在性能恢复的同时实现升级再制造,即所谓对失效零部件“控形控性”的修复,比如在役再制造,就是以装备健康能效检测诊断理论为基础指导,以在役老旧和性能低下的机电装备实现提升健康能效和智能化水平为目标,以再制造后装备更适应生产为需求准则,以先进技术和再设计为手段,进行改造机电装备的一系列技术措施或工程活动。
二、再制造与维修、传统制造和再循环的区别
传统的产品生命周期是从开发到报废的开环系统,这时的产品在报废阶段只是固体垃圾,其主要表现为以下三个特性。
1)单向性。产品生命周期的物流、信息流方向是从产品规划至报废单向流动的,前后段相互影响不大。
2)阶段性。产品生产企业的全部工作只涉及产品生命周期的部分阶段,用户则是全链条中的终端主体。
3)孤立性。产品周期中各阶段的行为主体相互关联性不强,生产企业不对产品循环再利用负责,也不与开展产品再利用业务的第三方发生直接关系。
再制造开启了一个从本轮生命周期进入下一轮生命周期的多生命周期循环过程,形成了一个闭环系统,延长了产品的使用寿命。产品全/多生命周期理论认为,从原材料、产品设计、制造、使用与维修到回收处理再利用、再循环,构成了一个产品的生命周期全过程。基于这种全生命周期理论,产品产业链沿着其零部件的生命过程得到了延伸,形成了闭环式结构。以汽车全生命周期为例(图1-4),在这个闭环系统里,包含了再制造、传统制造、维修和再循环,但再制造有别于传统制造、维修和再循环。

图1-4 汽车全生命周期
1. 再制造与传统制造的区别
再制造属于制造的范畴,但不等同于制造。两者之间的区别体现在以下四方面。
(1)对象不同
制造的对象是原材料。再制造的对象则是不合格品、损坏的零部件及报废品等,属于半成品,零部件具有各自不同的技术状态和剩余寿命,每个零部件毛坯可能来源于不同的废旧产品,需要经历不同的再制造修复技术,毛坯状态、失效形式和再制造修复方法都有高度的随机性和不确定性。
(2)生产过程不同
制造过程是原材料到产品,而再制造生产过程是从再制造毛坯到再制造产品的过程。再制造过程主要包括五个重要阶段:一是废旧产品回收、拆解、清洗等;二是零件质量检测及其寿命评估;三是失效零件表面尺寸恢复至可供加工的毛坯尺寸;四是再制造坯料的加工,实现几何尺寸、精度和机械性能的新品化;五是再制造部件的装配、试验和验收。
(3)质量控制体系不同
由于再制造产品的生产过程体现了回收、拆解、清洗、再制造加工、再装配和再检测等生产节点,其过程较传统制造更为复杂,因此其质量控制体系也愈加复杂。
(4)生产成本不同
再制造的原材料可以通过废旧零部件回收获得,与传统制造的原材料相比,具有较高的资源利用率,生产成本也比传统制造低。一般来讲,再制造零部件产品在价格上有较强的优势。
因此,制造过程中输入的毛坯原材料多属于初级制成品,质量单一,易于保证产品的生产一致性和可靠性,而原材料的采购成本随着生产过程的不同而变化。而再制造的输入对象为已处于失效状态的退役产品零部件,通过采用一定的技术措施使这些失效的退役零部件质量或性能恢复至新品水平,即要求所有零部件经过再制造加工后,必须恢复其原始新品的设计集合要素,不能丧失其装配互换性。
2. 再制造与维修的区别
再制造过程起源于维修,但与维修存在明显的本质上的区别,见表1-1。
(1)对象不同
维修主要针对出现故障的在役产品,而再制造主要针对达到寿命或技术落后的产品。
(2)生产内容不同
维修主要以更换零部件为主,以单件或小批量零部件的性能修复为辅,对在使用过程中因磨损或折旧不能正常使用的个别零件所进行的修复,为产品在使用阶段继续保持其良好技术状况及正常运行而采取的技术措施,其生产过程具有明显的随机性、原位性和应急性。
再制造主要是通过新技术对废旧机电产品进行专业化和批量化修复使其达到新品性能的生产过程,包含产品批量拆解、回收、清洗、修复、再装配等工艺过程。
(3)技术标准不同
维修的技术标准主要是执行目标对象的维修标准,其修复后的产品质量和性能无法达到新产品的水平,维修后的产品仍然是旧产品。
再制造生产过程各个环节具有规范的技术标准,再制造产品的技术性能和质量可靠性不低于原型号的新品。再制造产品的可靠性建模和分析方法也将不同于新产品制造和维修。经过再制造形成的不是二手产品,而完全是新产品。
因此,由再制造质量或性能达到甚至超过原型新品质量或性能、再制造过程充分吸纳高新技术,以及规模化的生产方式这三个特点可以看出,再制造是机电产品修复发展的高级阶段。
3. 再制造与再循环的区别
再循环是一种低级、低效的再利用工艺,主要针对的是经过前期使用后,其原材料已经丧失了新品的物理、化学性质,不能满足制造新品所需的基本条件的废旧产品,通过再循环工艺过程,失效零件通过回炉、重熔等方式回归至初级材料原始状态,零件的附加加工值随之消失,一般只能实现降级再利用,但随着材料改性、改形新技术在再利用工程中的应用,再循环原材料恢复其物理和化学性能、实现同级再利用成为可能。
再制造与维修、传统制造、再循环的区别主要体现在制造对象、生产过程和输出产品性能及质量三个方面(表1-1)。
表1-1 再制造与维修、传统制造、再循环的区别

三、再制造的特点
机电产品与人类社会生活息息相关,如生活中的电器、电子设备和生产中的机械、各类农具、电器、电子设备等生产设备与生活用机具等。
废旧机电产品与环境的关系有以下三个特点。
(1)废旧机电产品处理不当将会对环境造成严重污染
废旧机电产品大部分材料由金属、塑料、玻璃等固体无机物成分构成,产品退役报废后不易降解。甚至有部分电子元器件还具有重金属毒性,对环境危害大。因此,机电产品报废后的主要表现形式与生活垃圾有明显区别。机电产品报废后采用传统的掩埋、焚烧、堆肥等普通垃圾处理方法,不但占用大量土地,破坏自然环境,还会对空气、土壤和水质造成严重污染,影响人类生活质量,威胁人们的身体健康,不利于综合利用资源。
(2)废旧机电产品蕴含大量的可再利用资源
废旧机电产品大多含有金属材料,因此蕴含丰富的可再利用资源。据统计,1t电脑及其部件含有约0.9kg黄金、270kg塑料、128.7kg铜、58.5kg铅、39.6kg锡、36kg镍、19.8kg锑等资源。每回收200万辆汽车,仅对其中的废旧发动机进行资源化利用,可节约钢材80万t,节电30亿kW·h。而每回收利用1t废钢铁,可炼钢850kg,相当于节约成品铁矿石2t,节能0.4t标准煤。
(3)废旧机电产品蕴含丰富的剩余附加值
机电产品大多由多个部件或零件组成。每个零部件在其制造过程中均注入了劳动力、资金、技术等附加值,其价值往往要大于产品材料本身的价值。以废旧汽车为例,汽车发动机作为核心零部件,本身的材料价值仅占全部价值的5%,却是汽车再制造的主要对象、附加值最高的汽车零部件再制造产品。
据估计,原厂商如果能够回收再利用已退役产品,只要再多付出20%的努力,就可以节省40%~60%的生产成本。
因此,废旧机电产品再制造的特点总结如下。
(1)环保和经济效益突出
废旧产品再制造与废旧产品回炉相比,其节能减排效果十分突出。据美国Argonne国家实验室统计结果表明,再制造1辆汽车的能耗只是制造1辆新车的1/6,再制造1台汽车发动机的能耗是1台新发动机的1/11。
装备再制造的基础是对装备中失效的零件进行再制造,再制造的对象是经过使用的成形零件,这些零件中蕴含着从采矿、冶炼到加工一系列的附加值(包括了全部制造活动中的劳动成本、能源消耗成本、设备工具损耗成本等),再制造能极大地保留和利用这些附加值,降低加工成本、减少能耗。
(2)质量稳定可靠
再制造的对象是由于功能性损坏或技术性淘汰等原因不再使用的机电产品及其零部件,该机电产品在使用过程中,科学技术迅速发展,新材料、新工艺、新检测手段、新控制装置不断涌现。在对旧机电产品实施再制造时,可以吸纳最新的成果,既可以提高易损零件的使用寿命,又能对老旧设备进行技术改造,还可以弥补原设计和制造中的不足,使产品质量得到提升。
再制造过程中采用批量化的生产方式,再制造企业从事再制造生产需要获得认证,出售的再制造产品应有明确的标识,确保废旧装备及其零部件在全面性能质量恢复过程中有健全的质量保障体系保证,质量稳定可靠。