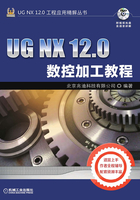
1.6 数控工序的安排
1.工序划分的原则
在数控机床上加工零件,工序可以比较集中,尽量一次装夹完成全部工序。与普通机床加工相比,加工工序划分有其自身的特点,常用的工序划分有以下两项原则。
• 保证精度的原则:数控加工要求工序尽可能集中,通常粗、精加工在一次装夹下完成,为减少热变形和切削力变形对工件的形状精度、位置精度、尺寸精度和表面粗糙度的影响,应将粗、精加工分开。对轴类或盘类零件,应该先粗加工,留少量余量精加工,以保证表面质量要求。同时,对一些箱体工件,为保证孔的加工精度,应先加工表面后加工孔。
• 提高生产效率的原则:数控加工中,为减少换刀次数、节省换刀时间,应将需用同一把刀加工的加工部位全部完成后,再换另一把刀来加工其他部位。同时应尽量减少空行程。用同一把刀加工工件的多个部位时,应以最短的路线到达各加工部位。
实际工作中,数控加工工序要根据具体零件的结构特点和技术要求等情况综合考虑。
2.工序划分的方法
在数控机床上加工零件,工序应比较集中,在一次装夹中应尽可能完成尽量多的工序。首先应根据零件图样,考虑被加工零件是否可以在一台数控机床上完成整个零件的加工工作。若不能,则应该确定哪一部分零件表面需要用数控机床加工。根据数控机床加工的特点,一般工序划分可按如下方法进行。
(1)按零件装卡定位方式划分
对于加工内容很多的零件,可按其结构特点将加工部位分成几个部分,如内形、外形、曲面或平面等。一般加工外形时,以内形定位;加工内形时,以外形定位。因而可以根据定位方式的不同来划分工序。
(2)按同一把刀具加工的内容划分
为了减少换刀次数,压缩空程时间,减少不必要的定位误差,可按刀具集中工序的方法加工零件。虽然有些零件能在一次安装刀具情况下加工出很多待加工面,但考虑到程序太长,会受到某些限制,如控制系统的限制(主要是内存容量)、机床连续工作时间的限制(如一道工序在一个班内不能结束)等。此外,程序太长会增加出错率,查错与检索也相应比较困难,因此程序不能太长,一道工序的内容也不能太多。
(3)按粗、精加工划分
根据零件的加工精度、刚度和变形等因素来划分工序时,可按粗、精加工分开的原则进行工序划分,即先进行粗加工再进行精加工。特别对于易发生加工变形的零件,由于粗加工后可能发生较大的变形而需要进行校形,一般来说,凡要进行粗、精加工的工件都要将工序分开。此时可用不同的机床或不同的刀具进行加工。通常在一次装夹中,不允许将零件某一部分表面加工完成后,再加工零件的其他表面。
综上所述,在划分工序时,一定要根据零件的结构与工艺性、机床的功能、零件数控加工的内容、装夹次数及本单位生产组织状况等灵活协调。
对于加工顺序的安排,还应根据零件的结构和毛坯状况,以及定位安装与夹紧的需要来考虑,重点是工件的刚性不被破坏。加工顺序安排一般应按下列原则进行。
• 要综合考虑上道工序的加工是否影响下道工序的定位与夹紧,中间穿插有通用机床加工工序等因素。
• 先安排内形加工工序,后安排外形加工工序。
• 在同一次安装中进行多道工序时,应先安排对工件刚性破坏小的工序。
• 在安排以相同的定位和夹紧方式或用同一把刀具完成加工工序时,最好连续进行,以减少重复定位次数、换刀次数与挪动压板次数。