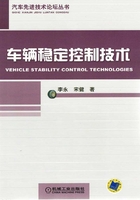
第三节 液压控制模型
以ANSYS和AMESIM软件为平台,建立HCU的动力学模型,运用有限元方法等求解HCU的电磁场模型、流场模型;稳控系统应用涉及车型、制动器形式、材料工艺、加工设备等因素;采用计算机辅助工程对HCU进行相关性能检验;建立HCU测试实验系统,对HCU进行相关实验。稳控系统电磁阀是一个体积小,油路布置复杂的机、电、液压集成系统,采用常规的计算难以分析清楚其电磁力、液压力等相关动态响应,在对典型系统剖析后,采用有限元方法和AMESIM分析相结合的方式对稳控系统的工作过程进行分析。液压控制模型逻辑关系如图2-15所示。
图2-15 液压控制模型逻辑关系
一、液压控制单元
越来越多的车辆已安装稳控系统,而且各国已有相应的法规要求采用稳控系统来提高车辆的安全性能。压力调节单元是稳控系统起作用的执行机构,是稳控系统的关键部件之一。压力调节单元通常都是调节阀。根据驱动阀芯的机构不同又可分为电动机驱动阀和电磁阀两种。HCU组成如图2-16所示,包括阀本体、回流泵、蓄能器、阻尼器及电磁阀等。
图2-16 HCU组成
HCU泵体采用铝材挤压成形制造工艺,与铸造或锻造相比,具有更好的塑性变形特性。电磁阀等部件是通过泵体的挤压变形装入本体的,这对整个HCU的工艺性能至关重要。采用整体式模块结构设计,将HCU与电子控制单元集成于一体,体积小,质量小,成本低。电磁阀采用材料加工技术进行挤压装配,从而使系统的密封性能完全得到保证。电磁阀线圈集成于电子控制器内,省去了电磁阀线圈与控制器之间的连接电线,提高了系统的抗电子干扰能力。采用大功率集成电路直接驱动电磁阀及回流泵电动机,省去了较占空间的电磁继电器。
二、液电混合模型
电磁系统必须具有良好的电磁、流场和机械响应特性。同时,电磁阀要有可靠的防泄漏性能。图2-17所示是电磁阀的结构模型图,图2-18所示为电磁阀工作范围内不同线圈电流和不同阀芯开度状态下,阀芯所受的电磁力。可以看出,电磁力随着阀芯开度的增大(动铁和定铁间距的减小)和电流的增大而增大,并且随着阀芯开度的增大,电磁力相对电流的增长越来越快。
图2-17 电磁阀的结构模型
1—隔磁管 2—定铁 3—回位弹簧 4—线圈扼铁 5—线圈 6—动铁 7—推杆 8—阀体 9—隔磁片 10—工作气隙
图2-18 电磁力-线圈电流-阀芯开度图
采用轴对称模型,主自由度为矢量磁势。认为隔磁材料的顶杆与隔磁管具有与空气一致的磁特性,为施加麦克斯韦电磁力标志,假定与动铁直接接触的不是隔磁的顶杆,而是空气。用B-H非线性曲线表征磁性材料的磁特性。磁场建立的时间常数远远小于机械运动的时间常数,因此不考虑阀芯运动与磁场的耦合问题。采用图2-19所示的四边形和三角形平面单元。非工作气隙和工作气隙处磁势降很大,加密其网格。
图2-19 单元的形状、结点位置与自由度
电磁场的边界条件可分为三类:狄里克利边界条件(式2-16)、诺依曼边界条件(式2-17)和两者的组合。
和
是两类边界;g(
),σ(
),h(
)是位置的一般函数。狄里克利边界条件表示势函数在边界上是定值,而诺依曼边界条件常表达几何和激励源的对称性。磁感应强度在边界上强制地与边界平行。为了处理远场模型时减少单元数目,设立一种特殊的单元类型——远场单元。其实质是一种狄里克利边界条件。图2-20所示包含了轭铁上端部分空气的模型,而图2-21所示为无周边空气模型。尽管轭铁上端的部分空气中确实存在磁场分布,但计算表明这种差别对结果不敏感。为减少计算量,采用的是图2-21所示的模型及边界条件。
图2-20 含部分周边空气模型
图2-21 无周边空气模型
对于一定的动铁位置x,给电磁线圈加斜坡电压载荷。在前一个载荷步结果的基础上,加以电压载荷增量,重新进行分析。这种方式保存了前一步的涡流密度结果,从而实现涡流损失的时间积分。在求解前耦合线圈电流自由度,后处理程序根据线圈节点上的电流密度求得总电流。每个电压载荷步对应不同的线圈电流,分析整个加载过程,可以建立电磁力Fm和电感L等与线圈电流i的关系。改变动铁的位置x,重复用上述方法进行分析,得到动铁在整个行程中的特性。
磁力线图形象地描述了磁场的分布,阶跃地撤去电压后磁力线分布如图2-22所示。在撤去电压载荷后,导磁体内部的磁场比表面衰减得慢。磁场在导磁体的表面与内部不同快慢的变化率与导体内感生电流有关。图2-22显示,动铁中心磁力线很少。如果钻去动铁中部的部分材料,在不影响磁场下减少动铁质量,从而缩短电磁阀响应时间,减小阀芯落座冲击。
图2-22 磁力线分布图
三、液压理论模型
在稳控系统仿真平台的研究中,稳控系统液压制动系统模型是重点和难点之一,这里所指的稳控系统制动系统是包括HCU、主缸、轮缸、制动管路等在内的整套制动系统。由于受制动系统的零部件之间的间隙、制动元件的弹性以及摩擦等许多不确定性因素的影响,制动压力-力矩响应表现出死区、饱和、满环等非线性动态特性。整个制动系统的响应由准静态部分和瞬态部分构成。瞬态特性是指HCU的间歇式压力调节使制动管路压力产生急剧变化的特性,制动管路内制动液的流动状态、制动器的刚度特性等对制动器的瞬态特性具有重要的影响,动态特性的存在使制动力矩的建立滞后于制动压力。制动器的准静态特性是指在制动过程中,制动器摩擦系数随车轮转速、温度等变化而缓慢变化的特性。摩擦系数的变化造成制动压力与制动力矩间的非线性关系。动力学模型可以分为理论模型、半经验模型和经验模型等,液压制动系统包括制动主缸、HCU、制动管路和制动轮缸。驾驶人所施加的踏板力传递到制动主缸的活塞上,推动前、后缸两个活塞向前运动,将制动液压入制动管路。制动液通过HCU后,流经同制动硬管和制动软管组成的制动管路,进入制动轮缸。
HCU由增压阀、减压阀、蓄能器、回流泵和阻尼器组成,增压阀为常开阀,减压阀为常闭阀,每个制动轮缸都由一套独立的增、减压阀对自身的制动压力进行调节。稳控系统通过对电磁线圈施加控制信号来控制增压阀和减压阀的通断,以实现增压、保压和减压的防抱死控制过程:在增压阶段,增、减压阀上均无控制信号,增压阀打开,减压阀关闭,由制动主轴过来的制动液不能进入减压回路,而是通过增压阀阀口进入相应的制动管路,并经过制动软管进入制动轮缸,使制动压力不断升高。在保压阶段,只对增压阀施加电信号使其关闭,这样便切断了制动轮缸与制动主缸之间的联系,使其内部压力保持不变。在减压阶段,对增、减压阀同时施加电信号,增压阀关闭,减压阀打开,各制动轮缸与减压回路相连通,轮缸中的制动液便通过减压阀阀口进入弹簧活塞式蓄能器,实现制动压力的降低。蓄能器中的制动液会在回油泵的作用下随制动踏板的抬起排回制动主缸;如果稳控系统制动还未结束,制动液会在回油泵和增压阀之间聚积成一高压区域,等增压阀打开时再次进入轮缸。在回油泵和制动主缸之间,阻尼器起降低液压脉动和噪声的作用。
HCU模型包括增压阀、减压阀、阻尼器、蓄能器、回油泵几个部分。节流器模型在稳控系统液压制动系统中应用非常广泛,各组增压阀均有各自的节流器,各组减压阀在各自的隔磁管上均开有节流孔;阻尼器其本质也是一个节流器。因此HCU中的增压阀、减压阀和阻尼器均用节流器的动力学模型表示。在节流器的动力学模型中,输入量为制动液压力,输出为通过节流器的制动液流量。计算表达式如式(2-18)表示。
式中 Q——制动液流量;
Cq——流量系数;
ρ——制动液密度;
Δp——模型两端压力差;
A——节流孔截面积。
考虑到模型计算的精度,流量系数Cq不应当为一个恒定的值,引入式(2-19)和式(2-20)。
式中 Dh——阀直径;
λ——制动液流动雷诺数;
χ——节流孔湿周长度;
η——制动液动力黏度。
流量系数Cq的表达式如式(2-21)。
式中 Cqmax——最大流量系数;
λc——层流变紊流的临界雷诺数。
节流器动力学模型,如式(2-22)。
模型中考虑了流量系数的非恒定性,当Δp较小时,流量Q基本与Δp成正比,随着Δp的增大,流量系数很快接近于Cqmax,流量Q与√|Δp|成正比。这样,改变节流器的孔径即可得到不同的流量特性。HCU中的低压蓄能器为弹簧活塞式液压蓄能器。由于活塞的质量很轻,故建模时不考虑活塞惯性。HCU蓄能器模型输入量为制动液流量,输出量为制动液压力。模型的示意图如图2-23所示,S为活塞的最大行程,x为活塞瞬时的位置。
图2-23 蓄能器模型
由弹簧和活塞位置关系,可得:
式中 pl——活塞在最大行程时的弹簧力;
p0——蓄能器内制动液压力;
Aa——活塞面积;
k——弹簧刚度。
式(2-33)两边对时间t求微分,结果如式(2-24)。
由于蓄能器为液容性元件,其考虑到活塞位移的基本方程如式(2-25)。
式中 Ky——制动液体积弹性模量;
Va——蓄能器内制动液体积;
q0——端口流量。
蓄能器动力学模型为
回油泵的动力学模型主要为包括柱塞式回油泵和驱动回油泵的稳控系统电动机,采用理想的液压泵模型,忽略机械损失和制动液泄漏,则回油泵排量如式(2-27)所示。
式中 Vb——回油泵排量;
Db——柱塞直径;
e——电动机偏心轮偏心距。
泵的输出流量如式(2-28)。
式中 qb——回油泵输出流量;
Sm——电动机的平均转速。
以上为HCU的动力学模型。以下对制动系统的其他部分进行建模,主要包括制动管路、主缸、轮缸等部分。
制动管路模型包括制动硬管和制动软管,二者都会有由于管壁摩擦所产生的制动液沿程压力损失;对于制动软管,其管壁的弹性变形对压力的影响也要考虑。
制动管路的沿程压力损失动力学模型如式(2-29)。
式中 Δpg——管路沿程压力损失;
ξ——沿程阻力系数;
Lg——管路长度;
Dg——管路内径;
v——制动液在管路中的平均流速。
由于制动液在制动管路中的流动已经得到了充分的发展,其流动模式为层流,雷诺数λ约为100。则沿程阻力系数ξ在制动硬管中为75/λ,在制动软管中为80/λ。
制动软管属于液容性元件,其管路的体积弹性模量如式(2-30)。
式中 Kg——管路体积模量;
Eg——管路材料弹性模量;
δ——管壁厚度。
综合考虑制动液和软管的体积弹性模量,其等效体积弹性模量Kz如式(2-31)。
由液容性元件的基本方程可得到考虑制动软管弹性变形时的动力学模型,如式(2-32)。
式中 pg——管路内制动液压力;
Vg——管路内制动液体积;
qg——制动液流量。
模型依据当前车辆常采用的双腔式主缸建模,考虑了其内部两个活塞的惯性、两活塞间的间隙及弹簧阻尼连接。模型示意图如图2-24所示。
图2-24 主缸模型
后缸活塞和前缸活塞的运动方程分别如式(2-33)和式(2-34)。
式中 m1——后缸活塞质量;
m2——前缸活塞质量;
x1——后缸活塞位移;
x2——前缸活塞位移;
Fy1——后缸制动液压力;
Fy2——前缸制动液压力;
Fs1——无间隙连接弹簧力;
Fd1——无间隙连接阻尼力;
Fs3——前缸内弹簧力。
无间隙连接的弹簧力和阻尼力分别如式(2-35)和式(2-36)。
Fs1=(x1-x2+G1)k1 (2-35)
式中 k1——无间隙连接的弹簧刚度;
f1——无间隙连接的阻尼系数;
G1——无间隙连接的弹簧预紧量。后缸和前缸的制动液流量分别如式(2-37)和式(2-38)。
式中 A1——后缸活塞有效面积;
A2——前缸活塞有效面积。
在间隙消除之后,主缸的动力学模型与间隙消除之前类似,只是要将有间隙连接的弹簧力和阻尼力再列入模型即可,如式(2-39)和式(2-40)。
式中 Fs2——有间隙连接的弹簧力;
Fd2——有间隙连接的阻尼力。
Fs2=(x1-x2-d)k2 (2-41)
式中 k2——有间隙连接的弹簧刚度;
f2——有间隙连接的阻尼系数;
d——活塞间隙。
制动轮缸模型取盘式制动器,考虑了钳体的惯性、钳体和制动盘之间间隙和接触后的弹簧阻尼等效模型。输入量为制动压力,输出量为制动力,模型如图2-25所示。
制动钳体先要克服回位弹簧的阻力来消除钳体与制动盘之间的间隙,间隙消除后,还要额外克服钳体和制动盘直接接触所产生的等效弹簧阻尼影响,制动钳体运动方程为
图2-25 轮缸模型
式中 mq——钳体质量;
xq——钳体位移;
Fz——制动压力;
Fsq1——弹簧刚度。
回位弹簧力为
式中 kq1——回位弹簧刚度;
Gq1——回位弹簧预紧量。
间隙消除之后,轮缸的制动力矩为
式中 μ——制动片摩擦系数;
rd——制动盘有效摩擦半径。
磁感应强度矢量在阀体和工作气隙处最强。同样可得到磁场强度的分布,磁场强度
在气隙处远远大于其他部分。还得到了线圈外的电流分布情况,该电流是感生电流,其方向与线圈电流相反。麦克斯韦张量法将力计算转化为一个面积分:
式中 S——气隙中包围器件的任意闭合曲面;
——曲面的单位法向矢量。
此法计算的电磁力在很大程度上取决于有限元网孔的划分密度和闭合曲面的选择,从而限制了计算精度。磁场中贮能增量等于机械能与电能增量的总和,磁场的贮能及伴随贮能计算式分别为
低速运动时用伴随贮能计算磁场力:
计算表明,用以上两种方法计算动铁受力有一定差别。表2-3是阀全开时,用麦克斯韦张量法和能量法(虚功法)计算结果对照。虚功法是更精确的方法,下文电磁力用虚功法计算。
表2-3 麦克斯韦张量法与虚功法计算动铁磁力(单位:N)
阀芯电磁力随气隙减小而增大,对阀芯位置非常敏感(图2-26)。通过插值法,确定电磁力的表达式为
上述电磁阀有限元模型可以研究除材料磁滞效应以外的各种因素对电磁阀性能的影响,包括结构、材料和电流加载方式等。这里仅讨论非工作气隙、材料磁特性等对电磁力的影响。图2-27所示是电磁阀全开状态(左图)和全闭状态(右图),不同非工作气隙的Fm—I曲线族。电磁力随气隙厚度增大而减小,但不如对主工作气隙敏感。这是由于主工作气隙的截面相对较小,更容易形成磁感应强度的“瓶颈”。
图2-26 动铁电磁力
材料的磁特性,如初始磁导率、最大磁导率、饱和磁感应强度等,对电磁阀性能影响显著。图2-28和图2-29分别显示了两种不同的电磁材料下的电磁力和电感。图中的上下两组曲线分别是阀关闭和开启时的情形。图中实线对应退火处理后的碳素钢16,虚线对应的是碳素钢55。
图2-27 非工作气隙对电磁力的影响
图2-28 磁特性对电磁力的影响
图2-29 磁特性对电感的影响
增压阀和减压阀的节流孔径和阀芯几何形状及位置对稳控系统的压力调节性能有显著影响。本节以增压阀为例,用有限元法建立了流场的牛顿流体层流模型,得到阀口的压力-流量特性,并建立阀芯作用力与阀芯位置和流量的关系。
四、流场控制模型
通过上述研究,建立了稳控系统住址平台的动力学模型,包括驾驶人操作模型、轮胎模型、车辆动力学模型(单轮、双轮、四轮模型)、稳控系统制动系统模型(理论模型、经验模型)等。为了使用计算机进行仿真计算,需要将平台的动力学模型转化为计算机可以接受的形式,这种转化有许多方式和软件仿真环境可以选择,例如Matlab/Simulink、AMESim软件等。增压阀轴对称,因而可以建立平面二维模型。使用四节点四边形或三节点三角形单元,对增压阀口附近的流体建模。为避免求解时由于出口端面上加常压边界条件造成质量不守恒,在出口处增加一段虚拟长度,ANSYS称之为“烟囱”,以使流动充分发展。计算表明,“烟囱”为顶杆和阀套之间的缝隙的15倍左右时,在压力、速度变化梯度大的边界以及狭窄处加大单元密度。而在远离节流孔的出口处,采用大网格单元,如图2-30所示。
图2-30 节流孔附近的单元划分
入口处速度和出口处的压力都规定为均一值,这与实际流场有差别。为减少它们对流场分布的影响,需要加大入口和出口的长度(虚拟长度),使入口处的压力和出口处的速度具有较一致的分布。图2-31显示了阀口附近的节点流速。对比左右两图,最大流速对阀口开度很敏感。壁面上的速度分布说明方程的解确实满足狄里克利边界条件。对不同阀开度时的等势分布分析可知:当阀的开度为0.01mm时,只有在钢珠与阀座靠近处有明显的速度梯度;而当阀的开度为0.05mm时,节流孔处也出现相当的速度梯度,说明此时节流孔已成为流速的制约因素。
图2-31 阀口附近的节点流速
阀小开度时,压力梯度集中于钢珠与阀座靠近处,而阀充分打开时,压力只是在节流孔处有明显的梯度。这意味着,所设计的阀开度已不至于成为流速的制约因素。图2-32所示是不同流量和阀开度下的流线分布,阀全开,入口流速5m/s,出现了两处明显的涡流。增压阀打开时,影响阀口特性的主要因素是节流孔本身;增压阀动作过程中,影响过渡过程的主要因素是钢珠与阀座的相对位置等。增压阀是常开阀,只考虑节流孔本身对流量-压力特性的影响。相反,研究制动液对阀芯的作用力时,必须考虑阀芯的位置,以确定液力对电磁阀的动态过程的影响。由于规定出口压力等于0,且“虚拟长度”与阀芯的设计长度相当,阀芯边界的压力积分即近似于阀芯所受到的液压反作用力Fp。图2-33所示是不同流量Q下Fp与阀开度的关系。当阀口开度大于20%后,液压差没有对阀芯造成显著的反力。当然,增压阀闭合/开启的动态过程中,流量Q是不恒定的。图2-34所示是不同节流孔直径下增压阀打开时的Q-Δp特性曲线。
图2-32 阀口附近流线图
图2-33 阀芯液压作用力-阀开度
图2-34 流量-压力特性
五、液压匹配模型
AMESIM软件是一种包括液压系统在内的机电系统专用建模与分析软件,集成了常用机电系统的模型,使用者可以采用物理建模方式建立所要分析系统的模型,如图2-35所示。结合所建立的整车模型,得到图2-36所示的稳控系统整车分析系统,进行HCU参数与整车分析,完成硬件在环仿真分析及实车实验前的参数匹配。
图2-35 HCU与制动系统的模型
1—主缸 2—HCU 3—软管 4—硬管 5—制动器
图2-36 稳控系统整车AMESIM模型
1—HCU 2—ECU 3—整车模型
六、整车匹配模型
对稳控系统的HCU,电磁阀的阀口参数是十分重要的参数,因此,电磁阀不同参数下的整车制动效果是稳控系统匹配过程中研究人员十分关心的一个方面。以HCU中某一节流阀的参数匹配为例,在系统匹配过程中,希望了解其参数与制动效果的关系。在AMESIM中所建立的稳控系统整车匹配模型中,分别选取该阀口的直径参数为0.3mm、0.5mm和0.7mm。得到整车以初速80km/h开始制动时控制距离和制动过程中轮速的变化情况如图2-37和图2-38所示。
图2-37 节流阀不同阀口直径参数下控制距离
图2-38 节流阀不同阀口直径参数下轮速变化
由结果可以看到,当节流阀阀口直径为0.7mm时,控制距离最短,但制动效果稍显粗暴;当节流阀阀口直径为0.3mm时,车轮速度控制较为理想,但距离稍长;当节流阀阀口直径为0.5mm时,控制距离和制动效果均理想。
七、整体布置模型
在剖析HCU结构以及分析电磁阀电磁场、流场之后,根据控制要求确定HCU的设计,图2-39所示是液压单元的整体布置图。两前轮分别用一组增压阀和减压阀独立控制,两后轮为非独立控制。前后回路各有一个低压蓄能器、回流泵和缓冲器,两个柱塞式回流泵由同一电动机驱动,部件安装在锻铝液压单元本体上,增压阀常开,减压阀常闭,回流泵、缓冲器和低压蓄能器等呈对称分布,三组电磁阀在本体上均布。
图2-39 液压单元整体布置模型
压力调节单元的本体采用复合孔设计方法,在保证加工精度的同时,将大大降低加工难度。由于压力调节单元的高度集成化,使得在压力调节单元的本体的每个面都有加工孔,并存在较多的孔套孔、孔中再加工孔的情况。设计中采用复合孔方法,将大大降低了加工难度。压力调节单元采用精密挤压成形密封,密封性能高。在设计制作挤压冲头后,采用行程精密控制的方法将增压阀和减压阀挤压铆接在本体上,既完成增压阀和减压阀与本体联接,又完成增压阀和减压阀的密封。压力调节单元的本体采用方形型材,以便于加工。HCU使用的介质是车辆制动液,且安装在车辆车身上。根据零部件的使用条件,确定HCU的非金属材料。在对HCU进行性能分析的同时,对材料进行光谱分析,确定被分析样品的组成成分;根据光谱分析的结果,对被分析样品进行分类归组,对每组样品进行扫描电镜分析,对样品中所含元素周期表中钠以上元素进行定量和/或半定量分析,分析并找出对材料性能起关键作用的样品中的元素进行化学分析,精确确定其含量。根据对HCU金属材料及电磁场分析的结果,确定HCU金属材料的具体型号。
八、质量控制模型
稳控系统质量标准是进行稳控系统标定和稳控系统性能评定的依据,为了提高标准的科学性,需要分析选取的质量因素对稳控系统评价的影响。首先分析制动效能中的质量因素。根据单一路面紧急制动过程的车辆运动学分析,控制距离为
式中 S——控制距离;
v0——制动初速度;
amax——制动时最大速度;
t0——制动器开始升压的滞后时间。
t1—t0之后,压力升至使减速度达到amax所用时间,控制距离的第一项与v0,amax有关,amax由控制性能和路面附着条件决定,控制越好,则amax越接近路面峰值附着系数对应的减速度。
车辆横摆动运动方程如式(2-52):
式中 Iz——车辆绕横摆轴的转动惯量;
Yaw——车辆横摆角加速度;
B1、B2——车辆前后轴的轮距;
Fx11,Fx12,Fx21,Fx22——四个车轮的纵向力;
Fy11,Fy12,Fy21,Fy22——四个车轮的侧向力;
a、b——车辆悬上结构质心至前、后轴的距离;
δ——车轮转角。
在进行车辆仿真时,认同转向盘转角与车轮转角的关系如式(2-53):
式中 θ——转向盘转角;
iw——转向系统的角传动比。
cosδ≈1,sinδ≈δ,在直线行驶工况下,可得:
由于前轮转角较小,在直线制动工况下,可以假定前轮测偏角与转角一致,纵向力与侧向力存在近似关系式Fy=Fxδ。由于两前轮侧向力相差不大,则可以得到车辆直线行驶时稳定的转角与两侧车轮纵向力关系如式(2-55):
车轮纵向力即车轮制动力。从式(2-55)可以看出,在总制动力相等的情况下,当在单一路面制动时,两侧制动力可以认为相等,因此车轮转角为0,当两侧附着系数不同时,附着差异越大则车轮制动力差异越大,需要的车轮转角越大,转向盘修正转角也就越大。转向盘转角的大小还与车辆结构参数iw、B1、a密切相关。由于轮胎的侧偏特性,侧偏角控制在线性区间比较安全,在极限情况下侧偏角不应超过10°,则前轮转角δ最好控制在10°以下,此时iw=18对应的最大转向盘转角在180°以内,即θ<180°。由于制动过程中发生载荷前后转移,采用后轮低选控制策略,可以认为后轮高附侧制动力与低附制动力相同,且两后轮与前低附侧车轮的制动力系数一样,则四个车轮制动力如式(2-56):
式中 G——车辆重力;
kh——高附制动力系数,kL≤kh≤kH,kH是高附路面附着系数;
kl——低附制动力系数,kl<kL,kL是低附路面附着系数;
hg——车辆质心高度;
L——车辆轴距,L=a+b。
在对开路面上,提高稳定性,则减小转向盘修正转角,损失附着系数利用率,降低制动效能;提高制动效能,则增大转向盘修正转角,损失稳定性。转角控制由调节高附增压速率实现。