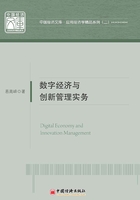
二、我国数字工业的典型案例
(一)海尔集团实现大规模个性化定制
海尔集团深耕互联网定制,实现从大规模制造向大规模定制转型,快速满足用户个性化需求。截至2016年底,海尔已建成8个互联工厂样板,包括青岛空调、郑州空调、青岛热水器、沈阳冰箱、胶州空调、佛山滚筒洗衣机6个整机工厂以及青岛FPA电机和青岛模具2个模块化工厂。主要呈现五大特点:一是注重用户参与,用户通过线上定制方案,将个性化需求第一时间传递到生产线,随后可参与制造、交付的全流程;二是互联互通,基于互联网将机器设备、产品及用户联系起来,实现用户与设计、生产部门的沟通和协同;三是智能化,通过智能制造执行系统进行监控,实时采集、分析生产数据、开展智能化管理;四是模块化,在接到订单后定制所需模块,按照客户的需求进行组合;五是定制全流程可视化,用户通过手机等终端设备不仅可以随时随地地获取订单状态,还可以观看从采购、装配到安装的整个过程。2016年,海尔发布了COSMO互联工厂云平台,进一步连接用户与内外部资源,让用户真正参与到设计、制造、物流、服务等各个环节中,并为互联工厂提供用户的体验反馈,实现利益相关方的共创共赢。数据显示,2016年前三季度,海尔定制产品订单量为73.2万台,其中第三季度单季度销售37万台。
(二)商飞公司金球网络设计系统
中国商飞公司搭建全球协同网络环境平台,实现了产品的设计、研发、制造全流程的全球协同管理。商飞公司负责飞机的总体设计和装配,零部件设计、制造等工作则外包给全球各地的零部件供应商来完成。飞机的总体装配过程中,商飞公司利用计算机模型进行总体结构的虚拟装配,利用部件生产数据进行部件组装和校验,部件组装完成后,各机体在商飞总装工厂完成最后的大部件对接和总装。利用全球协同研制平台,商飞公司实现了跨企业的统一构型和统一数据的管理以及统一协同工作流程,有效消除了因信息不一致导致的问题,使研制周期缩短20%,制造周期缩短30%,制造成本降低20%,能源消耗减少10%,制造质量问题发生率降低25%。2016年底研制成功的商飞C919飞机,涉及的研发成员企业包括设计与主制造商、10家机体结构、24家机载设备、16家材料供应商和54家标准件等供应商,另有200多家企业参与了项目的研制过程。2016年,商飞公司对C919大型客机进行了多项地面试验,首架C919飞机于2016年12月交付试飞中心。
(三)中科院与SAP合作开发“工业4.0”联合解决方案
2016年,中科院沈阳自动化研究所与SAP共同研制出“工业4.0”联合解决方案,并基于该解决方案共同搭建了“工业4.0”智能制造示范产线,助力未来智能工厂定制化生产。该解决方案将沈阳自动化研究所WIA-FA工业无线网络通信技术、SAP的HANA云服务平台和设备预防维护软件,以及新松机器人公司研发的工业机器人相互整合,通过工业无线网感知机器人状态,并通过云服务平台对机器人状态数据进行分析,最终实现了设备的预防性维护和生产系统结构的模块化,大幅提高了生产效率,降低了运行故障率。其中,SAP提供的HANA内存计算平台、云计算以及大数据等技术,可以帮助工厂实现从ERP管理层到车间执行层的无缝集成。新松机器人公司研发的工业机器人利用RFID技术,可以与SAP的MES系统中的订单对应的产品与工艺要求进行实时信息交互,实现同一生产线上多种个性化产品的混线生产。沈阳自动化研究所自主研发的WIA-FA工业无线网络通信技术,可以实现对设备状态、生产等信息的无线采集,并可以将数据快速传递到SAP的HANA平台,进行设备的诊断和生命周期预测,有效减少了设备停机时间。此外,该解决方案通过引入沈阳自动化研究所自主研发的软件定义生产系统以及面向动态生产过程的可重构工业控制网络等前沿技术,实现了生产系统结构模块化,整个生产系统可以根据当前设备状态和订单需求进行实时调整和动态优化,大幅提升了生产系统的智能化和灵活性。
(四)青岛红领大规模个性化定制
青岛红领集团全面顺应“互联网+”的趋势,充分围绕客户需求,利用大数据、物联网等信息技术建立大规模个性定制新模式,快速响应全球消费者的多元化需求。红领集团的制造模式主要有以下四个特点:一是运用大数据技术满足客户差异化需求。红领在多年的生产过程中,积累了海量的版型、款式、工艺等方面的数据,客户可以利用红领的版型数据库进行自由搭配组合。二是运用物联网技术实时传递生产信息,实现生产与管理的集成。红领实现了服装设计、下单、定制的全部数字化。红领生产的每件定制产品都有专属芯片,各工序员根据芯片指令完成制作,芯片精准地将个性化定制工艺参数和要求传递给工位上的电脑,确保定制产品高质高效完成。同时,生产管理部门可实现对每道工序、每个环节在线实时监控。三是以生产流程的模块化、标准化布局,实现个性产品规模化生产。红领的RCMTM平台通过将客户在定制平台上填写的数据与数据库中存储的模型进行对比,可以实现个性化数据的标准化。然后按照标准化数据将订单分拆成若干模块,并自动分配给生产线上的工人进行后期制作。通过上述模式能够在所有细节上既实现个性化定制,又做到规模化生产。四是客户需求数据驱动柔性定制模式。通过红领的C2M平台,可实现制造体系与用户需求数据无缝对接,于是制造环节能够根据用户的个性化需求快速调整生产要素和柔性布局。红领集团的大规模个性化定制模式颠覆了服装行业经营传统,大幅提升了企业经济效益,设计成本下降40%,生产成本下降30%,原材料库存量降低60%,生产周期缩短40%,产品储备周期缩短30%。2016年,红领开始输出以客户需求源点驱动公司价值链协同的解决方案。截至2016年6月,青岛红领共与38家企业签订了解决方案引进协议,帮助传统企业实现互联网时代的升级改造。