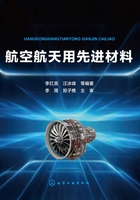
1.3 材料的性能
材料的性能是一种参量,用于表征材料在给定外界条件(温度、载荷、电场、磁场、化学介质等)下的行为,通过测试和表征材料在不同条件下的行为便可得到不同的性能指标。材料的性能可分为简单性能和复杂性能,简单性能包括力学性能、化学性能,复杂性能包括复合性能、工艺性能和服役性能。对于航空航天结构材料,其热学性能、力学性能和耐久性能比较重要。
1.3.1 热学性能
航空航天材料通常在极端温度环境下服役,航天器中储存液氮、液氧的容器必须承受很低的温度,航天飞行器重返大气层时要承受很高的温度,而发动机涡轮叶片的温度也非常高。材料在不同温度会表现出不同的热物理性能,称为热学性能,包括熔点、软化点、热容、导热性、热膨胀系数、抗热震性等。
1.3.1.1 熔点和软化点
晶体材料的各种热学性能的物理本质均与其质点热振动相关,而质点热振动的剧烈程度与温度有关。在低温时,参与低频振动的质点较多,随着温度升高,参与高频振动的质点逐渐增多,当温度高于一个特征温度(德拜温度ΘD)时,几乎所有质点都以最大频率ωm振动。当加热至一定温度时,原子的振幅达到使晶格破坏的数值,固态转变为液态,相应温度称为熔点Tm(反之为凝固点)。纯金属有固定的熔点,而合金的晶体组织有较多的缺陷,常常在一个温度范围内熔化。
非晶材料加热时表现出不同的状态和性能,温度低于玻璃化温度Tg时,材料具有刚性、脆性、透明性;温度高于Tg时,材料具有可塑性、黏性、弹性。玻璃、橡胶、塑料、耐火材料等非晶材料在加热时会逐渐软化,使性能发生急剧变化的温度称为软化点Tf,非晶材料的服役温度应低于软化点。
1.3.1.2 热容
在没有相变和化学反应的条件下,物质温度升高(或降低)1K所吸收(或放出)的热量称为该物质的热容,通常以大写的英文字母C表示。热容与物质系统的质量成正比,单位质量物质的热容称为比热容(质量热容),通常以小写的英文字母c表示。不同材料的比热容不同,不同物态的同种材料的比热容也不同,水的比热容最大,材料的含水率越大,比热容越大。热容与温度有关,工程上通常用单位质量的材料从温度T1升高到T2所吸收的热量的平均值表示其比热容,称为平均比热容。若温度变化时物质的压力不变,相应热容和比热容为定压热容Cp、定压比热容cp,若温度变化时物质的体积不变,相应热容和比热容为定容热容CV、定容比热容cV,通常Cp>CV,cp>cV。由于温度变化总会导致体积变化,Cp、cp可通过实测获得,CV、cV则通过计算获得。
1.3.1.3 导热性
导热性可用热导率λ表示,在单位温度梯度下,单位时间内通过单位面积和单位厚度均质材料传导的热量为λ。导热性好的材料有利于散热,可用于制造航空发动机燃气轮机叶片等高温环境下服役的部件;导热性差的材料有利于保温或绝热,可用于制造航天飞行器挡热板、低温燃料储箱等。
金属拥有大量质量很小的自由电子,可以迅速实现热量的传递,导热性能较好。晶体缺陷和振动质点是影响热传导的主要因素,产生缺陷热阻和声子热阻。纯金属的热阻主要为声子热阻,按照T2的规律上升,其热导率随温度升高而下降;合金的热阻主要为缺陷热阻,按照T-1规律下降,其热导率随温度升高而增大。由于异类原子的作用,合金的热导率明显低于纯金属,对于固溶体来说,溶质的结构及质量与溶剂相差越大,固溶后结合力改变越大,晶格畸变产生的散射作用越大,对热导率的影响越大。金属热导率λ与电导率σ间遵从Wiedeman-Franz定律,许多金属在室温的λ/σ比值几乎相同,与温度T成正比,引入Lorenz常数L,如式(1-1)所示。
(1-1)
式中,kB为玻尔兹曼常数;e为电子电量。当T为0℃以上较高温度时,L近似为常数,因此可以通过测量电导率来评估金属的热导率。
主要依靠质点振动的格波实现传热的非金属材料,其热导率受结合键及邻近原子的振动、结合的基团及分子间结合力的影响。无机非金属材料主要依靠声子和光子导热,石英、金刚石等由强力共价键键合的非金属晶体材料也是良好的导热体,在较低温度下的导热性可以与金属相提并论。但是,无机非金属材料的热导率还受表观密度、含水率及孔隙率、孔隙尺寸、孔隙特征等的影响。有机材料的热导率通常低于无机材料,结晶聚合物的热导率稍高一些,呈现远程无序结构的非晶聚合物的热导率较低,沿大分子链进行热传递比在分子间进行热传递更为容易,因此,非晶聚合物的热导率随分子增大而升高,加入低分子的增塑剂会使热导率下降。
1.3.1.4 热膨胀系数
材料的体积或长度随温度升高而增大的现象称为热膨胀,温度T升高1K导致体积和线尺寸的相对变化量,分别称为体膨胀系数(β)和线膨胀系数(α)。通常采用线膨胀系数α来表征热膨胀,对于各向同性材料,β≈3α;对于各向异性材料,用α1、α2、α3分别表示3个方向的线膨胀系数。固体材料的线膨胀系数随温度而变化,其变化规律与热容随温度的变化规律相似。在产品选材、加工、装配方面,热膨胀系数是很重要的材料性能指标。在温度变化较大环境中工作的构件,要采用线膨胀系数较小的材料;焊接两种材料,其热膨胀系数不能相差过大。一般用平均线膨胀系数表示材料的热膨胀特性,常用材料的平均线膨胀系数可以从相关手册查得。
1.3.1.5 抗热震性
抗热震性是材料承受急剧温度变化(热冲击)而不致破坏的能力,又称为耐急冷急热性。一般无机材料和其他脆性材料,在环境温度急剧起伏的热冲击下产生热应力,当内应力超过材料的强度极限时,容易发生突然的开裂或断裂,称为热冲击断裂。材料抗热冲击断裂性能指标以其能够抵抗热冲击断裂的最大温差ΔTmax表征,ΔTmax值越大,说明材料能承受的温度变化越大。对于一些多孔材料和非均质的金属陶瓷,会在热冲击循环作用下发生热疲劳,导致材料表面开裂,裂纹扩展可能受到微孔、晶界或金属相抑制,使材料不会发生瞬时的完全断裂,只是开裂、剥落并不断发展至碎裂或变质,称为热冲击损伤。
在不同工况和服役环境下,对材料的抗热震性要求也不同,火箭喷嘴要求材料能承受温差为3000~4000K的热冲击。
1.3.2 力学性能
力学性能表征材料在载荷作用下抵抗变形和破坏的能力,既是材料自身固有的性质,也受载荷性质、应力状态、温度、环境介质等外在因素的影响。国际标准化组织规定,主要采用拉伸试验、硬度试验、韧性试验、疲劳试验测定材料的力学性能指标。当应变速率小于10-2s-1时,可视为静载作用,在室温静载条件下的力学性质称为常规力学性能,包括弹性、塑性、刚度、强度、硬度等。冲击载荷、交变载荷、摩擦载荷等为动载,冲击韧性、断裂韧性、疲劳强度、耐磨性等为动载荷作用下的力学性能,会随加载速率变化而变化。
1.3.2.1 硬度
硬度表征材料的软硬程度,是综合体现材料弹性、塑性、强度、韧性等的力学性能指标。采用不同测试方法得到不同的硬度指标,压入法得到的是布氏硬度、洛氏硬度、维氏硬度,弹性回跳法得到的是肖氏硬度,划痕法得到的是莫氏硬度,其中压入法应用最多,试验力的单位是kgf(1kgf=9.80665N)。
以一定直径的硬质合金球为压头,施加一定的试验力将其压入试样表面,保持一定时间后卸载,测量试样表面残留压痕的平均直径,试验力除以压痕面积便得到布氏硬度值。布氏硬度可用硬度值、HBW、球直径、试验力、试验力保持时间(10~15s不标注)表示,后3项间依次用斜线隔开,如300HBW10/1000/30表示用10mm直径的硬质合金球,在1000kgf 载荷作用下保持30s测得的布氏硬度值为300。布氏硬度测试一般采用直径较大的压头球,所得的压痕面积较大,试验数据稳定、重复性高,特别适合测量具有晶粒或组成相的金属材料的硬度,但是,测量操作麻烦,针对不同材料的布氏硬度试验需要更换不同直径的压头球并改变试验力,压痕直径测量也比较麻烦。此外,由于压痕直径较大,不宜对成品进行试验。
洛氏硬度测试方法与布氏硬度测试方法相似,压头可以是锥角为120°的金刚石圆锥体或一定直径(1.588mm,3.175mm)的小淬火钢球、硬质合金球,加载、保压、卸载后,测量试样的压痕深度,以一常数值减去压痕深度来表征硬度值。洛氏硬度的表示方法为:硬度值、HR、标尺字母,字母A、B、C、D、E、F、G、H、K分别对应9种洛氏硬度标尺,其中 HRA、HRB、HRC较为常用,70HRC表示用C标尺测得的洛氏硬度为70。表面洛氏硬度的表示方法为:硬度值、HR、总试验力、标尺字母,有N、T、W、X、Y等15个标尺字母,如70HR30N表示用30kgf总试验力的N标尺测得的表面洛氏硬度值为70。洛氏硬度测试操作简便、迅速,硬度值可直接读出,采用不同标尺可测定各种硬度和各种厚度的试样,广泛用于热处理质量检验,由于压痕较小,可检测成品、小件、薄件。但是,由于压痕较小,代表性较差,如果材料中有偏析及组织不均匀等缺陷,所测硬度重复性差、分散度大。此外,用不同标尺测得的硬度值彼此没有联系,不能直接进行比较。
维氏硬度测试压头是两相对面间夹角为136°的金刚石四棱锥体,通过测量出压痕对角线平均长度来计算压痕表面积,试验力除以压痕面积便得到维氏硬度值。维氏硬度可用硬度值、HV、试验力、试验力保持时间(10~15s不标注)表示,650HV30表示在30kgf载荷作用下保持10~15s测得的维氏硬度值为650。维氏硬度的试验力可任意选择,而且压痕测量精度较高,硬度值较为准确,选择较小的测试力,可用于表面硬化层和薄片材料的硬度测试。
对于测量材料极小范围内(晶粒、组成相、夹杂物)的硬度、测量陶瓷材料等脆性材料的硬度,或研究扩散层组织、偏析相、硬化层深度等,上述3种硬度测试方法就不适用了,必须采用显微硬度测试方法。通常,显微硬度测试的测试载荷小于2N,常用的有显微维氏硬度和努氏硬度。显微维氏硬度测试可测量金属箔、极薄表面层的硬度和合金中各组成相的硬度,测试原理与维氏硬度试验相同,仍可用HV表示,但是测试结果必须注明载荷大小,如350HV0.1表示用0.1kgf的载荷测得的显微维氏硬度为350。努氏硬度试验方法是维氏硬度试验方法的发展,采用金刚石长棱形压头,如图1-3所示,两长棱夹角为172.5°,两短棱夹角为130°,在试样上得到的是长、短对角线长度比为7.11的棱形压痕。努氏硬度用HK表示,以单位压痕投影面积上所承受的力来定义,由于压痕浅而细长,更适于测量极薄层(表面淬火层或化学热处理渗层)、极薄零件,丝、带等细长件,以及玻璃、玛瑙等硬而脆的材料,其测量精度高,对表面状况的敏感程度也高。

图1-3 努氏硬度压头与压痕示意图
1.3.2.2 常规力学性能
材料在外力作用下发生形变,外力去除后能恢复原来大小和形状的性质称为弹性。弹性模量E、剪切模量G、泊松比μ是表征材料弹性的3个常数,E=2(1+μ)G,对于各向同性材料,根据其中两个常数可算出另一个常数。材料产生单位弹性变形所需载荷的大小称为刚度,为承载截面积与材料弹性模量之积,对于截面积一定的构件,其刚度取决于材料的弹性模量。材料在载荷作用下产生塑性变形而不破坏的能力称为塑性,以断后伸长率(延伸率)A和断面收缩率Z表示。对于单一拉伸条件下工作的长形构件,一般用A表征其塑性,通常认为A>5%的材料为塑性材料;对于非长形构件,如果拉伸时形成缩颈,则采用Z表征其塑性,Z值对冶金因素和组织变化更为敏感。材料在载荷作用下抵抗变形和断裂的能力称为强度,通常指在拉伸、压缩、剪切、弯曲等静载荷作用下的强度,相应有抗拉强度、抗压强度、抗剪强度、抗弯强度。此外,表征材料强度的指标还有断裂强度、剥离强度、冲击强度、疲劳强度等。
通过静载拉伸试验可以获得弹性极限、弹性模量、屈服强度、抗拉强度、塑性等常规力学性能指标。一般按标准将材料加工成圆棒状或片状拉伸试样进行常规拉伸试验,试验机缓慢对试样施加均匀的轴向拉力,并自动记录载荷-伸长(拉伸)曲线,拉伸曲线的纵坐标和横坐标分别除以试样的原始截面积S0、原始标距长度L0,得到工程应力-应变曲线。由于小试样包含的冶金缺陷较少,用小试样测得的强度和塑性往往高于大尺寸构件的性能指标,为了使不同尺寸试样得到相同的断后伸长率(A),要求应用比例试样,圆柱形试样的尺寸为L0=5d0或L0=10d0,分别称为短比例试样和长比例试样,相应断后伸长率分别为A5和A10。大多数韧性金属材料的集中塑性变形量大于均匀塑性变形量,比例试样的尺寸越短,其断后伸长率越大,即A5>A10。
图1-4为典型的工程应力-应变曲线,其形状与拉伸曲线相似,纵坐标为工程应力R,由拉伸载荷F除以原始截面积S0得到,横坐标为工程应变ε,表示相对伸长量,由试样的绝对伸长ΔL除以试样标距长度L0得到。工程应力-应变曲线一般包括弹性变形、屈服变形、均匀塑性变形、不均匀塑性变形、断裂5个阶段,op段对应弹性变形阶段,应力应变关系为线性关系,比例常数为弹性模量E,试样单位面积所能承受的最大应力为弹性极限;pe对应滞弹性变形阶段,应力应变关系非线性,具有滞后性;eh对应微塑性变形阶段;hls对应屈服阶段,塑性变形急剧增加;sb对应应变硬化阶段,发生均匀连续的塑性变形;bk对应缩颈阶段,发生集中变形,k点断裂。

图1-4 静载拉伸的工程应力-应变曲线
我国制定的金属室温拉伸试验标准(GB/T 228.1—2010)的主要技术内容与国际标准(ISO 6892-1:2009)完全相同,定义了12种可测拉伸性能,如表1-1所示。
表1-1 可测拉伸性能指标

实际上,在拉伸过程中,试样截面积是逐渐变小的,真实应力和真实应变的计算应该采用瞬时截面积和瞬时长度,图1-5为真应力-真应变曲线,OA段为弹性变形部分,AB段是均匀变形部分,其斜率D为材料的形变强化模数,随变形增加而减小,自B点开始产生缩颈,BC段为局部变形阶段,其斜率D为常数,表示形变强化趋势稳定,曲线最后一段上翘是因为缩颈发展到一定程度后,三向应力不利于变形而导致的。均匀变形阶段,在双对数坐标下的真应力-真应变曲线是一条直线,在直角坐标中可以用S=ken表示,其中n称为应变硬化指数,k为强度系数,表征在均匀变形阶段材料的形变强化能力。

图1-5 材料的真应力-真应变曲线
对于淬火钢、硬质合金、陶瓷等硬脆材料,可采用弯曲试验测定其断裂强度,用最大弯曲挠度表征其塑性。弯曲试样有圆柱和方形两种形状,包括三点弯曲和四点弯曲两种加载方式,载荷(或弯矩)与试样最大挠度的关系曲线称为弯曲图,由弯曲图可以确定材料在弯曲载荷下的力学性能,得到抗弯强度、弯曲弹性模量、最大弯曲挠度。弯曲试验还可用来比较和检验表面处理的质量及材料表面的性能。
1.3.2.3 韧性
韧性是材料断裂前吸收塑性变形功和断裂功的能力,通常以裂纹萌生及扩展的能量消耗或裂纹扩展抗力来表征材料的韧性。静力韧度UT是反映材料强度和塑性的综合指标,其大小取决于静载拉伸的真应力-真应变曲线所包围的面积,对于韧性材料,可以根据UT=RmA或UT=(Rp0.2+Rm)A/2计算获得近似的静力韧度。
(1)冲击韧性
冲击韧性是材料抵抗冲击破坏的能力,反映材料在冲击载荷作用下吸收塑性变形功和断裂功的能力。火箭发射、飞机起飞和降落时会受到冲击载荷作用,为了评定材料承受冲击载荷的能力,主要进行缺口试样一次冲击弯曲试验和小能量多次冲击试验。一次冲击弯曲试验通常采用摆锤式冲击试验机,摆锤刀刃半径有2mm和8mm两种,将待测材料加工成标准试样,如图1-6所示,放在试验机的机架上,试样缺口背向摆锤冲击方向,将具有一定重量W的摆锤举至一定高度H1,使其具有势能WH1,然后摆锤落下冲击试样,试样断裂后摆锤上摆到H2高度,在忽略摩擦和阻尼等条件下,摆锤冲断试样所做的功即为冲击吸收功,用AK表示,AK=W(H1-H2)。

图1-6 一次冲击弯曲试验示意图
《金属材料夏比摆锤冲击试验方法》(GB/T 229—2007)规定,采用夏比U形或V形两种缺口试样,如图1-7所示,测得的冲击功分别为AKU、AKV。冲击试样主要有全尺寸(10mm×10mm×55mm)和半尺寸(5mm×10mm×55mm)两种规格,测量脆性材料的冲击功可以采用无缺口的全尺寸试样。

图1-7 标准夏比冲击试样尺寸示意图
冲击功取决于材料本身及其状态,同时与试样的形状、尺寸有关。同种材料的试样,缺口越深、越尖锐,缺口处的应力集中程度越大,越容易产生变形和断裂,冲击功越小,材料表现出的脆性越大。因此,对不同类型材料和尺寸的试样,其冲击韧性或冲击功不能直接比较,同一种材料在相同试验条件下,AKU明显大于AKV。
冲击功AK与冲断截面积之比为冲击韧度αK,冲击韧度值越大,材料的冲击韧性越好。但是,上述冲击韧度αK是大能量一次冲击条件下测得的冲击抗力指标,而绝大多数构件承受的是小能量多次冲击,通常要采用多次冲击试验评价材料的冲击抗力。图1-8为多次冲击试验示意图,将具有双冲点的冲头以一定的冲击能量、冲击频率和冲击速度打击旋转的试样,在每一个冲击能量A下可得到一个冲断周次N,从而得到试样断裂后冲击功和冲断周次的关系曲线,一般用冲击能量A下的冲断周次N,或用要求的冲击工作寿命N对应的冲断能量A来表示材料的多冲抗力。多冲抗力是取决于材料强度和塑性的综合力学性能指标,随着条件的变化,其强度和塑性的作用及要求不同,冲击能量高时,材料的多冲抗力主要取决于塑性;冲击能量低时,材料的多冲抗力主要取决于强度。航空航天零部件要求的冲击周次N在数万甚至数百万以上,属于小能量多次冲击,其多冲抗力主要取决于强度,在选材时应尽量发挥材料的强度,而不应过高追求塑性和冲击值αK。在中、低强度范围,αK对多冲抗力影响不大,在高强度范围内,提高αK值可明显提高多冲抗力,这对选用高强度材料具有重要的指导意义。

图1-8 多次冲击试验及多次冲击曲线
材料的冲击韧度还与试验温度有关,如果材料的AK值或αK值在某个温度点附近急剧下降,如图1-9所示,则这个温度为材料的韧脆转变温度。可用系列温度冲击试验法测量材料的韧脆转变温度, 图1-10为一种高强钢的系列温度冲击曲线,其中横坐标为试验温度,纵坐标表示冲击吸收功和脆性断面率。GB/T 229—2007规定了4种测定韧脆转变温度的方法,常用的有两种,其中一种方法规定脆性断口面积率为50%所对应的温度FATT50为韧脆转变温度,另一种方法以冲击吸收功达到上下平台区间的50%来判定韧脆转变温度ETT50。结合上述两种判定方法确定韧脆转变温度,FATT50为-38℃,ETT50为-36.5℃,两种判定方法确定的韧脆转变温度相近。

图1-9 温度对冲击韧性的影响

图1-10 一种高强度钢的系列温度冲击曲线
应变速率对材料的塑性变形、断裂及有关的力学性能有显著的影响,当应变速率大于10-2s-1时,应变速率增大导致的力学性能变化不可忽视,提高应变速率将导致材料的脆化倾向增大。
(2)断裂韧性
根据外加应力与裂纹扩展面的位向关系,裂纹扩展分为张开型(Ⅰ)、滑开型(Ⅱ)、撕开型(Ⅲ)3种基本型式,如图1-11所示,实际裂纹扩展可能是3种型式的组合。当拉应力垂直作用于裂纹扩展面时,如图1-11(a)所示,发生张开型扩展;当切应力平行作用于裂纹扩展面且与裂纹线垂直时,如图1-11(b)所示;发生滑开型扩展;当切应力平行作用于裂纹面且与裂纹线平行时,如图1-11(c)所示,发生撕开型扩展。

图1-11 裂纹扩展的基本型式
如果存在半长度为a的裂纹,裂纹尖端的应力场是裂纹扩展的动力,Ⅰ、Ⅱ、Ⅲ型裂纹尖端应力场可分别用力学参量KⅠ、KⅡ、KⅢ表征,相应称为Ⅰ、Ⅱ、Ⅲ型裂纹的应力场强度因子,可用式(1-2)~式(1-4)计算。
(1-2)
(1-3)
(1-4)
式中,σ为拉应力;τ为切应力;a为裂纹半长度,mm; Y为裂纹形状系数(无量纲系数),与裂纹几何形状及加载方式有关,一般Y=1~2。
Ⅰ型裂纹扩展容易导致脆性断裂,因此多以Ⅰ型裂纹扩展为研究对象。在动态加载中,当应力场σ逐渐加大时,应力场强度因子KⅠ和裂纹尖端各应力分量随之增大,裂纹a逐渐扩展,当KⅠ增大到临界值Kc或KⅠc 时,裂纹失稳扩展而导致材料断裂。Kc为平面应力断裂韧度,表征平面应力条件下材料抵抗裂纹失稳扩展的能力,当试样厚度增加,裂纹尖端达到平面应变状态时,断裂韧度趋于稳定的最低值KⅠc。KⅠc为平面应变断裂韧度,是与试样尺寸无关的材料常数,表征平面应变条件下材料抵抗裂纹失稳扩展的能力,可用式(1-5)计算,式中ac为临界裂纹尺寸,σc为临界状态对应的平均应力,称为断裂应力或裂纹体断裂强度。
(1-5)
KⅠ和σ对应,都是力学参量,与载荷及试样尺寸有关,而与材料无关;KⅠc和σc对应,都是力学性能指标,只与材料成分及组织结构有关,而与载荷和试样尺寸无关。
断裂韧性是材料抵抗裂纹扩展和断裂的能力,反映材料对微裂纹等缺陷的敏感性,通常用材料在平面应变和小范围屈服条件下的应力强度因子KⅠ的临界值KⅠc来表征,称为断裂韧度。《金属材料 准静态断裂韧度的统一试验方法》(GB/T 21143—2014)规定了测量KⅠc的4种试样,分别为标准三点弯曲试样、紧凑拉伸试样、C形拉伸试样、圆形紧凑拉伸试样。图1-12为两种最常用的断裂韧度试样示意图。

图1-12 两种最常用的断裂韧度试样
三点弯曲试样较为简单,使用较多,在确定试样尺寸时,应预估材料的屈服强度和KⅠc值,国标规定了试样厚度B、裂纹长度a及韧带宽度(W-a)尺寸。预制裂纹可在高频疲劳试验机上进行,疲劳裂纹长度应不小于0.025W,a/W控制在0.45~0.55范围内,Kmax≤0.7KⅠc。对于中低强度高韧性材料,可用弹塑性断裂力学的临界J积分(Jc)、裂纹顶端张开位移COD的临界值δc等指标来表征断裂韧性,δc是裂纹顶端塑性应变程度的度量,δc越高,断裂韧性越好。
航空航天构件中不可避免地存在裂纹或类似的缺陷,根据含有预制裂纹的试样测出的断裂韧性比较符合实际情况。断裂韧性的表达式和断裂强度相关,既是强度指标也是韧性指标,如果知道了所用材料的断裂韧度KⅠc值,就可以根据公式算出含有某种尺寸裂纹a的构件断裂时的临界应力,从而可确定构件所能承受的最大载荷。当载荷大于构件的实际承载能力时,构件中的裂纹就有扩展和断裂的可能,当知道构件实际承受的载荷时,就可计算构件允许存在的最大裂纹尺寸。
1.3.2.4 超塑性
超塑性是指材料在一定内部条件和外部条件下表现出异常高的流变性能,流变抗力和加工硬化异常小,均匀变形而不出现宏观缩颈,延伸率δ可达百分之几百,甚至百分之几千。根据实施超塑性的条件,超塑性可以分为三类:第一类超塑性为组织超塑性,又称恒温超塑性;第二类超塑性为相变超塑性,又称变态超塑性;第三类超塑性为短暂超塑性。一般超塑性多属于组织超塑性,具有超细等轴晶粒(晶粒尺寸在0.5~5μm)的材料,在一定温度和一定应变速率条件下呈现超塑性。相变超塑性不要求有超细晶粒,在一定温度和外加载荷条件下,经过多次循环相变或同素异构转变获得大的延伸率。非超塑性材料在一定条件下快速成形时,会呈现短暂的超塑性现象。
非晶态固体或玻璃一般都具备超塑性,玻璃在高温条件下通过黏滞性流变可以被拉长很多而不发生缩颈。金属及合金在正常状态没有超塑性,具有超细晶组织的金属材料在较高变形温度[T=(0.5~0.65)Tm,Tm为熔点的热力学温度]和较低变形速率(=10-4~10-2s-1)条件下会出现超塑性,表现出特别大的均匀塑性变形而不产生缩颈,延伸率可达到500%~2000%。式(1-6)为超塑性的状态方程。
(1-6)
式中,σ为应力;K为由材料决定的常数;为应变速率;m为应变速率敏感性指数,
。
晶粒尺寸对流动应力σ、m值、伸长率均有很大影响微细晶组织的m值较高。材料拉伸时均匀流动应力σ对应变速率
很敏感,其关系曲线呈现S形,S形曲线的斜率为m值,如图1-13所示,可将S形曲线分为三个区域。Ⅰ区和Ⅲ区的m值均很低,Ⅰ区相当于蠕变的低应变速率区,σ值随着
值增加而缓慢上升,近似于蠕变曲线;Ⅲ区相当于一般塑性加工的高应变速率区,σ值的变化近似于一般拉伸曲线。Ⅱ区为呈现超塑性的区域,m值较大且变化较大,m的取值范围通常为0.3~0.7。m值是评定材料潜在超塑性的重要参数,反映材料拉伸时的抗缩颈能力,间接反映超塑性的组织要求。

图1-13 金属及合金的σ和m与应变速率的关系
具有超塑性的合金,其晶粒在热变形过程中不能长大或长大很慢,采用较高的温度以发生扩散和蠕变,采用较低的应变速率以保证晶界滑动和扩散蠕变的充分进行,航空航天用的铝合金、钛合金、高温合金等在一定变形条件下均会出现超塑性,合金的流动性和填充性好,容易成形,能极大地发挥变形材料的塑性潜力,有利于复杂零件的精确成形。
1.3.3 耐久性能
1.3.3.1 耐疲劳性能
在循环加载下,材料、零件和构件的某点或某些点产生局部的永久性损伤,并在一定循环次数后形成裂纹或使裂纹进一步扩展直到完全断裂的现象,称为疲劳。根据应力状态,可将疲劳分为弯曲疲劳、扭转疲劳、拉压疲劳、复合疲劳等;根据环境和接触情况,可将疲劳分为大气疲劳、腐蚀疲劳、高温疲劳、接触疲劳等;根据应力高低和破坏前所经受的循环次数,可将疲劳分为高周疲劳(HCF)和低周疲劳(LCF)。常见疲劳多属高周疲劳,断裂前的循环次数Nf大于105,疲劳寿命主要由裂纹扩展寿命组成,所承受的交变应力远低于材料的屈服强度,甚至只有屈服极限的1/3,也称低应力疲劳。低周疲劳断裂前的循环周次为102~105,所承受的应力高于屈服极限,每次循环都发生了塑性变形,疲劳断裂是塑性变形累积的结果,也称高应力疲劳或应变(塑性)疲劳。
经过无穷多次应力循环而不发生破坏的最大应力值称为疲劳极限,又称为持久极限,是材料承受疲劳的能力,一般采用标准试样(光滑小尺寸试样)进行疲劳试验获得。利用超声波振动疲劳试验机可以测试循环次数大于107的超高周疲劳,一般钛合金为107,铝合金和高强度钢均为108。图1-14为通过疲劳试验获得的疲劳应力与疲劳寿命(S-N)曲线,主要用于确定疲劳极限和估计疲劳寿命,其中纵坐标S为循环应力的最大应力或应力幅,横坐标N为疲劳破坏前的循环周次。对于具有应变时效硬化的金属材料,当循环应力水平降低到一临界值时,低应力段趋于水平,表明试样可以经历无限次应力循环而不发生疲劳破坏,对应的应力σ-1称为疲劳极限;对于不存在应变时效硬化的材料,S-N曲线没有水平部分,疲劳破坏前循环次数随着应力降低持续增加,即使循环应力值降到很低,经一定次数循环后材料也会断裂,不存在真正意义上的疲劳极限。因此,规定循环107周次不发生断裂的最大应力为条件疲劳极限或疲劳强度σ-1,通常,σ-1低于Rp0.2,大多数金属的σ-1=(0.4~0.5)Rm。

图1-14 疲劳应力与疲劳寿命(S-N)曲线
低周疲劳一般通过拉-压疲劳试验获得的ε-N曲线来描述,对于存在较大塑性变形的低周疲劳,采用以塑性应变幅为参量的疲劳寿命描述方法,这种基于循环应变的表征方法被广泛用于估计疲劳寿命。
材料的疲劳极限既是材料固有的性质,也受循环特征、变形形式、环境等的影响。同一材料在不同应力状态测得的疲劳极限不同,常用的疲劳载荷有对称弯曲、对称扭转、对称拉压等,相应的疲劳极限分别标记为σ-1、τ-1、σ-1P,手册上给出的通常是对称弯曲疲劳σ-1。
采用带预置裂纹的标准试样,如紧凑拉伸(CT)试样、中间裂纹拉伸(CCT)试样、三点弯曲(SEB)试样,在给定载荷条件下进行恒幅疲劳试验可以获得a-N曲线,如图1-15(a)所示,其中横坐标为疲劳载荷循环次数N,纵坐标为对应循环次数的裂纹长度a,a-N曲线前端接近水平的部分为裂纹萌生阶段,循环次数的多少可以大致反映材料抗疲劳载荷的能力。通常用裂纹长度a随着循环周次N的变化率da/dN表征疲劳裂纹扩展的快慢,称为疲劳裂纹扩展速率,将(da/dN)i、(ΔK)i画在双对数坐标系中,得到1-15(b)所示的da/dN-ΔK曲线,表征疲劳裂纹扩展速率与应力强度因子幅值ΔK的关系。

图1-15 实测的a-N曲线(a)和da/dN-ΔK曲线(b)
金属材料的da/dN-ΔK曲线可分为3个区域(Ⅰ区、Ⅱ区、Ⅲ区),如图1-16所示。

图1-16 典型da/dN-ΔK曲线
Ⅰ区是低速率区,随着应力强度因子幅值ΔK的降低,裂纹扩展速率迅速下降,当ΔK趋近ΔKth时,裂纹扩展速率趋近于零。ΔKth为疲劳裂纹扩展的门槛应力强度因子幅值,称为疲劳门槛值,是表征材料疲劳裂纹扩展性能的重要参数,当ΔK<ΔKth时,疲劳裂纹不发生扩展。与疲劳极限σ-1相似,ΔKth受材料成分和组织、载荷条件、环境因素的影响,但是,σ-1为光滑试样的无限寿命疲劳性能,用于传统的疲劳强度设计和校核,ΔKth为裂纹试样的无限寿命疲劳性能,适用于裂纹件的强度设计和校核。测定材料的ΔKth时,很难做到da/dN=0,一般规定平面应变条件下da/dN≤10-7mm/周次所对应的ΔK为ΔKth,称为条件(工程)疲劳门槛值,工程金属材料的ΔKth为(5%~10%)KⅠc 。
Ⅱ区为中速率区,da/dN与ΔK呈线性关系,可用Paris公式表达,如式(1-7)所示。
(1-7)
式中,C是与加载条件及试验相关的常数;m为材料常数;ΔK为应力强度因子幅度。根据lg(da/dN)-lg(ΔK)曲线的截距和斜率可求得C、m,绝大多数金属材料的m参数在2~4,铝合金的da/dN分散度较大,m=2~7。
对疲劳寿命估算最有用的是区域Ⅱ的da/dN-ΔK关系和区域Ⅰ的门槛值ΔKth、疲劳断裂韧度KⅠc。根据疲劳断裂韧度KⅠc、疲劳门槛值ΔKth、疲劳裂纹扩展速率da/dN可定量估算构件材料的剩余寿命,预防疲劳断裂。
1.3.3.2 抗蠕变性能
在一定温度和载荷长期作用下,随着时间推移,工件变形不断增加的现象称为蠕变。对于航空发动机涡轮盘、叶片等在高温和载荷长时间作用下的构件,要求材料具有一定的蠕变极限和高温持久强度。图1-17为通过静态蠕变试验(温度和载荷恒定)获得的典型蠕变曲线,ε0为加载瞬间产生的普通变形(并非蠕变),如果应力超过该温度下的屈服强度,ε0包括弹性变形和塑性变形两部分,否则,仅为弹性变形。蠕变曲线可以分为3个阶段,Ⅰ为减速蠕变(过渡蠕变)阶段,变形随着加载时间延长而持续发生,但蠕变速率随时间延长而降低,到B点,蠕变速率达到最小值;Ⅱ为恒定蠕变(稳态蠕变)阶段,对应的BC段为线性段,蠕变速率保持恒定,且为最小蠕变速率,称为稳态蠕变速率;Ⅲ为加速蠕变阶段,蠕变速率随着时间延长逐渐增加,最后产生蠕变断裂,D点对应的tr、εr分别为蠕变断裂时间和总蠕变量。陶瓷的典型蠕变曲线与金属类似,也可分为3个阶段,曲线的形状除受应力、温度、环境条件影响外,还受晶粒尺寸、气孔率等自身条件的影响。

图1-17 典型蠕变曲线
温度和应力对蠕变过程影响较大,图1-18为不同温度和应力条件下的蠕变曲线。在低温(<0.3Tm)或低应力条件下,蠕变第Ⅱ阶段持续时间较长,蠕变速率接近于零,甚至可能不出现第Ⅲ阶段;相反,在高温(>0.8Tm)或高应力条件下,蠕变第Ⅱ阶段很短,甚至完全消失,很快出现断裂。

图1-18 不同温度和应力条件下的蠕变曲线
材料在规定蠕变条件(一定温度和时间内,蠕变变形量或蠕变速度达到规定值)下不失效的最大承载应力称为蠕变极限,也称蠕变强度。实际应用中采用失效应力表征蠕变极限,通常以或
表示,其中,T表示测试温度,℃;ε表示变形量,%;t表示持续时间,h;
为稳态蠕变速率,%/h。如
表示在600℃和10000h内产生1%的应变量的蠕变极限为100MPa,
表示在500℃、稳态蠕变速率达到10-5%/h的蠕变极限为200MPa。这种表示方法通常用于受蠕变变形控制的运行时间较长的构件,蠕变第二阶段很明显,最小蠕变速率容易测量。
持久强度是高温和载荷长时间作用下的蠕变断裂判据,有时也用蠕变断裂寿命(在一定应力下产生断裂所需的时间)衡量材料抗蠕变能力的高低。材料在规定温度(T)达到规定持续时间(t)而不发生断裂的最大应力称为高温持久强度,以(MPa)表示,
表示材料在500℃工作10000h的持久强度为200MPa,当σ<200MPa或t<10000h时,材料不发生蠕变断裂。持久强度试验通常在恒定的温度和载荷下进行,比蠕变试验简单,只需测定试样在规定温度和应力作用下的断裂时间。规定持续时间通常根据设计寿命确定,一般战斗机喷气发动机为上千小时,而气轮机机组的设计寿命为数十万小时,要进行这么长时间的试验比较困难,通常根据一些应力较大、断裂时间较短(数百或数千小时)的试验数据,将其在lgσ-lgt双对数坐标系中回归成直线,用外推法求出数万甚至数十万小时的持久强度。为了保证外推结果的可靠性,外推时间一般不得超过试验时间的10倍。
持久强度对于高温工作部件,如发动机的叶片、涡轮盘等的意义特别重大,近年来发展出变温变载的持久强度试验方法,为接近使用条件下构件持久强度性能测试开拓出新途径。
1.3.3.3 松弛稳定性
对于容易产生应力松弛的结构件,选材时要考虑材料抵抗应力松弛的能力,即松弛稳定性,可通过应力松弛试验测得应力松弛曲线来评价材料的松弛稳定性。图1-19为典型松弛曲线,在给定温度和总变形量下的应力随时间而降低的曲线,分为加速松弛阶段(Ⅰ)和缓慢松弛阶段(Ⅱ)。第Ⅰ阶段持续时间较短,σ0为初始应力,随着时间延长,应力急剧下降,松弛速率较大,对应过渡蠕变。第Ⅱ阶段持续时间较长,松弛速率较小,对应稳态蠕变,σsh、σs0分别为任一时间试样的剩余应力和松弛应力。通常以规定时间后的剩余应力σsh作为表征材料应力松弛稳定性的指标,对于不同材料或经不同热处理的同一材料,在相同试验温度和初始应力下,经过规定时间后,剩余应力σsh越高者,其松弛稳定性越好。

图1-19 典型松弛曲线
在高温工作的燃气轮机的紧固件特别容易发生应力松弛,其初始紧固应力随着时间延长而不断下降,通常要进行不同温度和不同初始应力下的应力松弛试验,以确定紧固件在高温长期使用时保持足够紧固力所需要的初始应力。应力松弛试验还可用来预测密封垫密封度的减小、弹簧弹力的降低,以及判明锻件、铸件和焊接件消除残余应力所需要的热处理条件。
1.3.3.4 耐腐蚀性能
耐腐蚀性能是材料抵抗酸、碱、盐、水、空气、溶液、润滑油等介质腐蚀的能力,金属材料的耐腐蚀性能往往不如非金属材料。
(1)腐蚀试验
现场暴露腐蚀试验是测试材料腐蚀性能最简单、可靠的试验方法,其特点是腐蚀环境与实际服役情况相同,但是,由于试验周期长,不利于材料耐蚀性能的快速评定,而且试验结果与所处地域有关,使其难以得到推广和应用。在与现场暴露试验有较好相关性的基础上,加速模拟腐蚀试验可用于预测材料长时间的腐蚀行为,进而估算材料在服役环境中的腐蚀寿命,可以辅助或部分替代现场暴露试验。常见的加速模拟腐蚀试验主要有加速老化试验、盐雾试验、循环喷雾腐蚀试验、全浸试验、交替浸泡试验、多因子循环试验等。
加速老化试验包括人工气候试验、热老化试验、UV荧光紫外光老化试验、氙灯老化试验、高压加速老化试验等,通过提高温度、湿度、压强等环境因素来加速试验过程,能有效测试材料在高温、高压、高湿度等严酷环境中的耐腐蚀性能。
盐雾试验主要用于评估产品或考核材料在盐雾环境中的耐腐蚀性能,通常采用NaCl溶液作为中性盐雾腐蚀溶液,NaCl+适量冰醋酸溶液作为酸性盐雾腐蚀溶液。设置腐蚀试验温度为(35±2)℃,盐雾的沉降率设置在1~2mL/h,将试样(根据实际要求确定类型、数量、形状和尺寸)放置在腐蚀试样箱的支架上,可将试样水平放置,也可将试样与垂直方向成45°倾斜放置,试验时间根据实际需要确定。
静态全浸泡腐蚀试验主要用于研究试样的电化学腐蚀行为和机理。将试样浸泡在特定的试验溶液(定时更换)中,隔一定时间将试样取出,记载试验后的外观、去除腐蚀产物后的外观、腐蚀缺陷(如点蚀、裂纹、气泡等的分布和数量)、开始出现腐蚀的时间。
(2)耐蚀性能评价
评价工程材料的耐腐蚀性能主要采用重量法、形貌观察法、电化学测试法、恒应力法。
①重量法 重量法是用试样腐蚀前后的重量差表征材料的腐蚀速率,分为增重法和失重法,增重法是腐蚀后连同全部腐蚀产物一起称重,失重法是清除全部腐蚀产物后称重。对于腐蚀产物疏松、容易脱落且易于清除的情况,通常采用失重法;对于腐蚀产物致密、附着力好且难于清除的情况,通常采用增重法。
②形貌观察法 形貌观察法分为宏观观察和显微观测,宏观观察是用肉眼对腐蚀前后的试样、腐蚀产物、腐蚀液进行观察分析,显微观测是对腐蚀试样进行金相检查或断口分析,或者用扫描电镜、透射电镜、电子探针等做微观组织结构和相成分的分析。形貌观察法,特别是局部腐蚀形貌观察,通常既要观察表面腐蚀形貌,也要观察截面腐蚀形貌。图1-20为2297铝锂合金剥落腐蚀样品的表面和截面的金相照片。

图1-20 剥落腐蚀样品的表面和截面的金相照片
③电化学测试法 根据体系状态,电化学测试可以分为稳态测试和暂态测试。在规定时间范围内,电极电位及电流、电极表面状态及浓度分布等电化学系统参量变化甚微(或基本不随时间变化)的状态称为稳态,在体系达到稳态进行的电化学测试称为稳态法(静态法)。从开始极化至达到稳态的电极过程中,体系的参量随时间而发生变化,相应的状态称为暂态,在暂态进行的电化学测试称为暂态法(动态法),动态法可以自动测绘,扫描速率可控,因而测量结果重现性好,适用于对比实验。根据外加信号,电化学测试可以分为直流测试和交流测试,直流测试包括动电位极化曲线、线性极化法、循环极化法、循环伏安法、恒电流/恒电位法等,交流测试包括阻抗测试和电容测试。
利用电化学工作站测试动电位极化曲线和交流阻抗谱(EIS)是应用最广泛的腐蚀性能测试方法,图1-21为典型的三电极电化学测试系统,参比电极(RE)为饱和甘汞电极(SCE),辅助电极(CE)为高纯Pt片,工作电极(WE)为待测试样。

图1-21 三电极电化学测试系统
图1-22为电化学测试样品示意图,在一侧钻孔并用带有绝缘层的铜质导线进行连接,保证两者之间导电正常,在试样中部预留出10mm×10mm区域作为待测区域(工作面),四周边沿及背面的非测试面、试样小孔与导线连接处均用松香进行涂覆,严格保证1cm2的工作面,而非工作面绝缘、密封。

图1-22 电化学测试样品示意图
根据GB/T 24196—2009《金属和合金的腐蚀 电化学试验方法 恒电位和动电位极化测量导则》,将试样、Pt电极、饱和甘汞电极连接成三电极体系,浸泡入腐蚀溶液(腐蚀溶液和浸泡时间根据实际需要确定)中,待测试体系电位稳定后开始测试,测试温度为25℃,每次测试重复2~3次,以保证实验结果的可重复性。极化动电位扫描范围根据需要测试的扫描区间进行调整,一般选取-1000~+1000mV,扫描速率根据需要测试的精度进行调整,通常在0.5~2mV/s,扫描速率越慢,测试点越多,时间越长。
图1-23为一种Al-Cu-Mg合金在不同溶液中浸泡及浸泡不同时间的动电位极化曲线,浸泡溶液分别为5%NaCl、0.2%NaHSO3+5%NaCl。表1-2为实验合金在5%NaCl溶液、0.2%NaHSO3+5%NaCl溶液中的动电位极化曲线的拟合结果,结果显示实验合金在0.2%NaHSO3+5%NaCl溶液中的自腐蚀电位更负、自腐蚀电流较大。自腐蚀电位决定合金的腐蚀倾向,自腐蚀电位越负,腐蚀倾向越大,自腐蚀电流决定合金的腐蚀程度,自腐蚀电流越大,腐蚀程度越严重,说明含硫的腐蚀介质显著促进合金的腐蚀过程。由图1-23(a)可以看出,在5%NaCl溶液中,实验合金表现出明显的钝化现象,而在0.2%NaHSO3+5%NaCl溶液中,实验合金表面维持钝化的区间明显变窄,且阴极电流密度要高于5%NaCl溶液中的阴极电流密度,说明加入NaHSO3会显著降低合金表面钝化膜的稳定性,而水解导致腐蚀介质中有较高的H+浓度,促进了阴极反应过程,使阴极电流密度增大。
图1-23(b)为实验合金在0.2%NaHSO3+5%NaCl溶液中浸泡腐蚀0h、48h、96h、192h后的动电位极化曲线,表1-3为通过Tafel外延法得到曲线对应的自腐蚀电位(Ecorr)和自腐蚀电流密度(Icorr)。由图1-23(b)和表1-3可以看出,随着浸泡时间延长,腐蚀电位负移,说明合金的腐蚀倾向增加;浸泡48h的腐蚀电流密度最高,为5.62×10-3A/cm2,浸泡96h的腐蚀电流密度下降为2.49×10-3 A/cm2,浸泡192h的腐蚀电流密度上升为3.58×10-3 A/cm2。随着浸泡时间延长,一方面,形成的腐蚀产物阻碍腐蚀过程,造成腐蚀速率下降;另一方面,因腐蚀产物剥落造成新鲜基体暴露,会加快腐蚀过程,在腐蚀后期出现腐蚀产物的剥落、开裂,使腐蚀速率呈现先降后升的趋势。

图1-23 Al-Cu-Mg合金在不同溶液中浸泡及浸泡不同时间的动电位极化曲线
表1-2 实验合金在不同溶液中的极化曲线拟合结果

表1-3 实验合金浸泡不同时间的极化曲线拟合结果

对于稳定的线性系统M,将1个角频率为ω的正弦波扰动电信号X(电压或电流)输入其中,该系统相应输出1个角频率为ω的正弦波电信号Y(电流或电压),其中Y=G(ω)X。如果X为正弦波电流信号,Y为正弦波电压信号,则G(ω)为系统M的阻抗,以GZ表示;如果X为正弦波电压信号,Y为正弦波电流信号,则G(ω)为系统M的导纳,以GY表示。阻抗和导纳合称阻纳,是一个当扰动与响应都是电信号且分别为电流信号和电压信号时的频响函数,对于稳定的线性系统,当响应与扰动之间存在唯一的因果性时,GZ和GY都取决于系统的内部结构,存在唯一的对应关系(GZ=1/GY)。
在系列不同角频率下测得的一组频响函数值就是电极系统的电化学阻抗谱。电化学阻抗谱技术就是测定不同频率ω(f)的扰动信号X和响应信号Y的比值,得到不同频率下阻抗的实部Z'、虚部Z″、模值Zmode、相位角,并绘制成曲线(电化学阻抗,EIS)。测量电化学阻抗谱应具有稳定性、因果性、线性三个前提条件,即扰动不会引起系统内部结构发生变化,扰动信号与响应信号之间具有因果关系且呈线性关系。给电化学系统施加不同频率的小振幅正弦波电位(或电流),对系统微扰且作用时间短,可以近似认为满足稳定性条件。若系统的内部结构是线性的稳定结构,则响应信号就是扰动信号的线性函数,因此,可以认为EIS系统的扰动信号与响应信号是近似线性关系,测量结果的数学处理较简化。EIS是一种频率域测量方法,可测定的频率范围很宽,可比常规电化学方法得到更多的动力学信息及电极界面结构信息。通常,电化学交流阻抗谱测试在开路电位下测定,施加振幅为10mV的正弦交流电流作为激励信号。
图1-24为一种Al-Cu-Mg合金在0.2%NaHSO3+5%NaCl溶液中浸泡不同时间的电化学阻抗谱,浸泡时间分别为0h、48h、96h、192h,扫描频率的范围为0.01Hz~100kHz,采用Origin8.5软件处理实验数据绘制交流阻抗谱,通过Nova2.1软件进行拟合分析。Nyqusit图第一象限的半圆形弧为容抗弧,在低频处存在收缩现象,若容抗弧在低频处偏离了第一象限,出现在了第四象限,则为感抗弧。容抗弧的大小代表耐腐蚀性能优劣,容抗弧越大,耐腐蚀性能越好;容抗弧的个数代表时间常数的多少,一个容抗弧代表腐蚀过程存在一个时间常数,两个容抗弧则代表两个时间常数。由图1-24(a)所示的Nyquist图可以看出,未经浸泡腐蚀的样品容抗弧半径最大;浸泡48h的容抗弧半径明显下降;浸泡96h的容抗弧半径比浸泡48h大,在低频段出现了Warburg阻抗;浸泡腐蚀192h的容抗弧半径复减小,合金表面阻抗值降低;其变化规律与腐蚀电流密度的变化规律一致。在腐蚀过程中,表面氧化膜发生破损会导致阻抗值明显降低,而表面堆积的腐蚀产物会阻碍试样与腐蚀介质之间的电荷交换,导致阻抗值有所回升,随着浸泡时间进一步延长,表面的腐蚀产物破损严重并有部分剥落,实验合金与腐蚀介质之间的电荷交换通道增加,导致表面阻抗下降,耐蚀性变差。图1-24(b)、图1-24(c)为浸泡不同时间样品的交流阻抗Bode图,其中图1-24(b)为扫描频率与阻抗模值的关系图,高频时为近似水平直线,由低频到高频的直线的斜率为-1,由斜线与高频水平线延长线的交点可确定特征频率;图1-24(c)为扫描频率与相位角图,根据存在的峰值个数可确定时间常数。

图1-24 电化学阻抗谱
④恒应力法 应力腐蚀对航空航天结构件具有普遍性,以铝材为例,除纯铝、Al-Mn和Al-Mg-Si合金未发现应力腐蚀开裂现象外,其他铝合金都有不同程度的应力腐蚀开裂敏感性,而且强度越高,应力腐蚀开裂倾向越大。评价材料的抗应力腐蚀性能对保证航空航天器的安全可靠至关重要。通常采用慢应变速率应力腐蚀试验(又称慢应变拉伸试验)、恒应力腐蚀试验、应力腐蚀疲劳试验等获得断裂寿命或断裂时间来评价材料在应力作用下的腐蚀行为,用临界应力强度因子KISCC、Kth、裂纹扩展速率da/dt等指标表征材料抵抗应力腐蚀开裂(SCC)及氢脆(HE)断裂的能力。
恒应力腐蚀试验是最常用的应力腐蚀性能测试方法,主要有单轴拉伸和C型环加载两种试验方法,对应标准为GB/T 15970.4—2000 《金属和合金的腐蚀 应力腐蚀试验 第4部分:单轴加载拉伸试样的制备和应用》和GB/T 15970.5—1998 《金属和合金的腐蚀 应力腐蚀试验 第5部分:C型环试样的制备和应用》。在试样的工作区段安装腐蚀溶液槽,在槽内注入腐蚀溶液(推荐为3.5%NaCl溶液,也可根据具体要求进行配比),按照设定的加载力(一般设定为材料屈服强度的百分比,如屈服强度的60%~75%)对试样加载,加载时间可根据具体情况设定(推荐为720h)。在加载过程中应定期观察试样及腐蚀溶液状况,若试样断裂,则记录断裂时间,取下并用流动水冲洗、干燥;若超过设定的加载时间试样仍未断裂,则用丙酮清洗试样表面,并用放大镜观察是否存在裂纹。腐蚀实验结束后,在拉伸机上测试用于对比的空白试样剩余强度,未断裂的加载试样也进行腐蚀后的拉伸实验,计算其强度损失,并对断口进行观察分析。