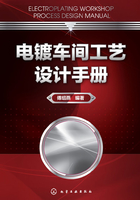
第7章 镀铜、镀镍、镀铬
7.1 镀铜
铜镀层呈粉红色,结晶细致、结合力好,质地柔软,具有良好的导电性、导热性和延展性,容易抛光,也能从镀液中直接镀出光亮铜层。铜镀层上一般容易镀上其他镀层,常用作其他镀层的底层,也因此被广泛用作装饰镀层的底层。
铜镀层在电镀中占有重要的地位和较大的比例,主要应用如表7-1所示。
表7-1 铜镀层的应用

7.1.1 预镀及预浸渍处理
在钢铁件上镀铜的关键之一,是解决好铜镀层与钢铁基体的结合力问题。铜镀层的结合力包括两个方面:一是基体材料与铜镀层的结合力;二是铜镀层与其上的其他镀层的结合力。在钢铁件上无氰镀铜,要获得良好结合力的铜镀层,必须同时解决好铜在钢铁件上的置换和钢铁件的钝化问题。
(1)提高基体金属上铜镀层结合力的措施
提高基体金属上铜镀层结合力的措施见表7-2。
表7-2 提高基体金属上铜镀层结合力的措施

镀铜前预镀的溶液组成及工艺规范见表7-3。
表7-3 镀铜前预镀的溶液组成及工艺规范

注:1.镀镍也可以采用低浓度的普通镀镍(暗镍)溶液。
2.氰化预镀铜配方1,用于普通氰化预镀铜;配方2用于锌合金压铸件预镀铜;配方3用于铝件预镀铜,阴极电流密度即开始镀时为2.6A/dm2,时间2min;然后用1.3A/dm2,时间3min。
镀铜前预浸渍处理的溶液组成及工艺规范见表7-4。
表7-4 镀铜前预浸渍处理的溶液组成及工艺规范

注:1.采用丙烯基硫脲浸铜时,经预浸后不经水洗直接浸铜。
2.采用柠檬酸盐浸铜或焦磷酸盐浸铜时,浸渍后不经水洗直接进行镀铜(柠檬酸盐镀铜或焦磷酸盐镀铜)。
(2)镀铜前处理工艺流程
镀铜前处理工艺流程参见图7-1。前处理工艺流程与被镀件基体材料、镀铜种类、工艺规范等有密切关系,而且镀铜工艺及前处理工艺也在不断改进和完善,所以图中的处理工艺流程仅供参考。

图7-1 镀铜前处理工艺流程
7.1.2 氰化镀铜
在所有镀铜工艺中,仅氰化镀液中铜的存在形式为一价铜,它以一价铜与氰根形成铜氰配离子,低价金属离子具有强的还原性,而氰化镀铜有较强的析氢现象,新生态氢原子具有强的还原能力。因此,氰化镀铜可以在钢铁件、黄铜件、锌合金压铸件、铝及铝合金件等上直电镀,也可作为预镀铜。
近年来光亮氰化镀铜有了发展,虽不如光亮酸性镀铜,但也能得到有较好的外观和整平性的镀层,可以省去镀后的抛光,所以亦能用作装饰性镀层的底层。
氰化镀铜溶液按其浓度的不同,可分为:低浓度镀液,主要用于闪镀;中浓度镀液,主要用于光亮镀,以及用于底镀层;高浓度镀液,主要用于快速镀和镀取厚镀层。氰化镀铜的溶液组成及工艺规范见表7-5。
表7-5 氰化镀铜的溶液组成及工艺规范

①为锌、铝基体上闪镀时用酒石酸甲钠30~70g/L。闪镀铜配方用于锌合金压铸件、铝及铝合金件、高浓度镀液电镀前基体的闪镀。
注:1.光亮镀铜配方1适用于钢铁、铜及其合金,尤其适合锌合金铸件的光亮镀铜,滚镀或挂镀均宜。Cu505诺切液、Cu503主光亮剂、Cu504辅光亮剂为德胜国际(香港)有限公司、深圳鸿运化工原料行的产品。
2.光亮镀铜配方2适用于挂镀,诺切液、LM3#高位光亮剂、LM4#低位光亮剂为广州美迪斯新材料有限公司的产品。
3.光亮镀铜配方3适用于滚镀,诺切液、RM33#高位光亮剂、RM34#低位光亮剂为广州美迪斯新材料有限公司的产品。
4.光亮镀铜配方4,采用周期换向电镀,正向时间∶反向时间=25∶5,阴极移动。
7.1.3 硫酸盐酸性镀铜
20世纪60年代后,人们不断研制开发出硫酸盐酸性镀铜添加剂,而光亮剂使获得镀层具有优异的光亮性,整平剂可消除微小的抛光痕迹,使硫酸盐酸性镀铜得以快速发展。
光亮酸性镀铜(也称为全光亮酸性镀铜)的镀液,是在硫酸盐酸性镀铜溶液的基础组分中加入有机组合的光亮剂和添加剂配制而成的。所获得镀层光亮、柔软、孔隙率低,镀液整平性好。全光亮镀铜后,无需再抛光就能够得到镜面光泽铜镀层。光亮酸性镀铜常作为高装饰性组合镀层中重要的中间镀层。由于它具有高光亮、高整平、高分散性能,加之光亮镀镍的发展,使装饰性电镀实现了镀层不用抛光的“一步法”电镀工艺。光亮酸性镀铜现已成为无氰镀铜的主流工艺。其特点如表7-6所示。
表7-6 光亮酸性镀铜的特点

(1)镀液类型
从铜镀层的光亮性来分,可分为光亮性镀液和非光亮性镀液两类,非光亮性镀液现应用很少。
从镀液中的硫酸铜和硫酸相对含量来分,可分为高铜低酸、中铜中酸和低铜高酸等三类。其组分含量、镀液工艺规范、性能及应用见表7-7,可供参考。
表7-7 硫酸盐镀铜的镀液类型、工艺规范、性能及应用

(2)镀液组成及工艺规范
光亮硫酸盐镀铜的溶液组成及工艺规范见表7-8。
表7-8 光亮硫酸盐镀铜的溶液组成及工艺规范

(3)光亮酸性镀铜后的除膜
全光亮酸性镀铜,镀层表面都会产生一层膜层。若亮铜镀层不除膜直接镀亮镍,则亮镍层与亮铜层结合力很差。所以光亮酸性镀铜后,必须考虑除膜。除膜方法有电解除膜和化学除膜。除膜溶液组成及工艺规范见表7-9。
表7-9 除膜溶液组成及工艺规范

7.1.4 焦磷酸盐镀铜
焦磷酸盐镀铜的研究和应用已有较久的历史,我国于20世纪70年代,为取代氰化镀铜,不少单位对此进行了深入研究。焦磷酸盐由于对许多金属离子都具有配位能力,因而在无氰镀铜及合金电镀中被广泛采用。
(1)焦磷酸盐镀铜的特点及应用
焦磷酸盐镀铜的特点及应用见表7-10。
表7-10 焦磷酸盐镀铜的特点及应用

(2)镀液组成及工艺规范
焦磷酸盐镀铜常用的有闪镀铜、普通镀铜、光亮镀铜和滚镀铜等。
焦磷酸盐镀铜的溶液组成及工艺规范见表7-11。
表7-11 焦磷酸盐镀铜的溶液组成及工艺规范

注:1.闪镀铜工艺时间为0.5~2.0min。
2.钢铁件上直接镀铜工艺:阴极起始电流密度用2.0A/dm2冲击镀,时间0.5~1min。在钢铁件上直接镀铜,其结合强度与氰化镀铜的在同一水平上,结合力为7180~9550N/cm2。
焦磷酸盐光亮镀铜的溶液组成及工艺规范见表7-12。
表7-12 焦磷酸盐光亮镀铜的溶液组成及工艺规范

7.1.5 有机膦酸镀铜
有机膦酸种类很多,目前应用于镀铜工艺的是羟基亚乙基二膦酸(HEDP)。
HEDP纯品为白色结晶,它本身及碱金属和铁的盐类均很容易溶于水。HEDP可在广泛的pH值范围内同多种金属离子形成稳定的配位化合物,其稳定常数比焦磷酸配位化合物高。
镀液成分简单,稳定性好,HEDP不会水解产生正磷酸盐。镀液自身有较好的pH缓冲性能,不需另加缓冲剂。若工艺控制得当,钢铁件直接镀铜能获得结合力良好的、结晶细致的、半光亮的铜镀层。镀液和铜镀层主要性能指标接近氰化镀铜,部分指标(如镀液覆盖能力)优于氰化镀铜。但允许阴极电流密度较小,仅为1.0~1.5A/dm2,经改进加入CuR-1添加剂后,阴极电流密度可达3A/dm2。由于工艺开发使用还不久,现在应用范围不广。存在有机膦废水处理问题。
HEDP镀铜的溶液组成及工艺规范见表7-13。
表7-13 HEDP镀铜的溶液组成及工艺规范[25]

注:配方1为南京大学配合物研究所的工艺。
7.1.6 柠檬酸盐镀铜
柠檬酸盐镀铜镀液成分简单,允许阴极电流密度比HEDP基本型镀铜液稍宽。若工艺控制操作得当,对钢铁等多种基材直接镀铜,可以获得较好的结合力。但镀液容易长霉菌(特别是在夏季)。
加入辅助配位剂酒石酸钾钠后为双配位型镀液,柠檬酸和酒石酸都是Cu2+良好的配位体,镀液和镀层性能有很大的提高。据有关文献报导,该镀液的电导率与氰化镀铜相仿;阴极极化值大于焦磷酸盐镀铜而小于氰化镀铜;镀液分散能力均优于焦磷酸盐镀铜和氰化镀铜;覆盖能力比氰化镀铜好;镀25μm时测的孔隙率,比同样厚度的氰化镀铜的孔隙少。其溶液组成及工艺规范见表7-14。
表7-14 柠檬酸盐镀铜的溶液组成及工艺规范

注:1.配方2为基本型。
2.配方4用于锌合金压铸件镀铜。
7.1.7 其他镀铜
其他镀铜包括市售商品镀铜液镀铜及多种无氰镀铜。有的无氰镀铜已在生产中使用数年,但由于种种原因未能坚持下来或未能推广。随着对氰化电镀的严格控制,今后还会对无氰镀铜进一步研究与开发,所以有必要对曾经应用过的一些无氰镀铜做简要介绍。
其他几种无氰镀铜特点见表7-15。
表7-15 几种无氰镀铜特点

无氰镀铜的溶液组成及工艺规范见表7-16。
表7-16 无氰镀铜的溶液组成及工艺规范

注:1.草酸酸盐镀铜的阳极面积∶阴极面积为(1~2)∶1。
2.酒石酸盐镀铜配方中,硝酸铜[Cu(NO3)2·5H2O]含量为40~45g/L,含铜约11~12g/L。阳极面积∶阴极面积为(1.5~2.0)∶1。阳极材料为电解铜或酸性镀铜用的磷铜。静镀或阴极移动,连续循环过滤。
商品镀铜溶液的组成及工艺规范参见表7-17。
表7-17 商品镀铜溶液的组成及工艺规范(示例)

注:1.配方1的238开缸浓缩剂及238配位剂是上海永生助剂厂的产品。
2.配方2的SF-638Cu开缸剂及SF-638E促进剂,以及配方3的SF-8639Cu开缸剂及SF-8639E促进剂,是广州三孚化工技术公司的产品。开缸剂为蓝色液体,主要由铜盐和配位剂组成,用于配缸及铜离子浓度的补充。镀液中的铜含量可以通过化学分析进行控制,一般铜含量在4.5~7.2g/L。促进剂为无色或淡黄色液体,由配位剂、阳极活化剂、润湿剂、金属杂质的掩蔽剂和导电盐所组成,要常添加补充,其消耗量为800~1200mL/(kA·h)。
3.配方4为挂镀,配方5为滚镀,适合于钢铁件、黄铜、铜、锌合金压铸件、铝及铝合金浸锌层的预镀。BH-580无氰碱铜开缸剂及BH-580无氰碱铜光亮剂是广州二轻工业科学技术研究所的产品。
4.配方6的CU-100浸铜粉是广州美迪斯新材料有限公司的产品。采用化学浸渍处理, 浸铜粉可使钢铁件得到结合力好的化学镀层,用于酸性镀铜前的底层。耗量为:每添加1000g硫酸添加浸铜粉400g。
7.1.8 不合格铜镀层的退除
不合格铜镀层的退除方法见表7-18。
表7-18 不合格铜镀层的退除方法


7.2 镀镍
7.2.1 概述
钢铁基体上的镍镀层是阴极镀层。镍镀层的孔隙率高,只有当镀层超过25μm时才基本上无孔隙率,所以薄的镍镀层不能单独用来作为防护性镀层。为了提高镍镀层的防腐性能,采用双层镍、三层镍镀层结构是比较合理的。而通常是通过组合镀层,如铜/镍/铬、镍/铜/镍/铬或双层镍、三层镍/铬来达到装饰防护的目的。
在镀镍的溶液中,加入各种添加剂后,能大大改善镀层表面质量,可以镀出半光亮镍、光亮镍(镜面光亮)、双层镍、三层镍、黑镍、缎面镍等等,因此镍镀层是一种防护-装饰性的最主要镀层。镍镀层应用很广,主要用于防护装饰性和功能性两个方面。
镀镍溶液的类型,主要有硫酸盐型、氯化物型、氨基磺酸盐型、柠檬酸盐型、氟硼酸盐型等。其中以硫酸盐型(低氯化物)[也称为Watts(瓦特)]镀镍液在工业上应用最为普遍。
7.2.2 镀镍添加剂
酸性光亮镀镍可以从镀液中直接镀取镜面光亮的镍镀层,而且可以直接套铬,不必再经过机械抛光,这完全依靠于光亮镀镍添加剂。镀镍添加剂(也有称为镀镍光亮剂)主要分为初级光亮剂(又称为第一类光亮剂)、次级光亮剂(又称为第二类光亮剂)和辅助添加剂(也有称为辅助光亮剂)三大类。
(1)初级光亮剂的作用
能细化镍镀层的晶粒,并产生一定的光泽(半光亮镀层);能把硫引入镍镀层中,可以控制镍镀层中的含硫量;与次级光亮剂配合使用,能获得镜面光亮(全光亮)的、整平性好的镍镀层;有抗杂质的能力,能使镀液对杂质具有较高的容忍度等。
(2)次级光亮剂的作用
单独使用虽然可获取光亮镀层,但电流密度范围十分狭窄;与初级光亮剂联合使用时,则可在较宽电流密度范围内得到镜面光泽(全光亮)镀层;在阴极上有强烈的吸附性能,使阴极电位明显负移,增大阴极极化作用;次级光亮剂对镍镀层会产生张应力,增加脆性,从而会降低其延展性等。
(3)辅助添加剂的作用
其作用是多方面的,如细化晶粒,扩大电流密度范围,改善镀液分散能力和覆盖能力,抑制或降低光亮剂的分解速率,能抗异种金属杂质,能根据需要增加或减少镀层的含硫量等。辅助添加剂的品种:润湿剂、走位剂、柔软剂、整平剂、除杂剂、抗杂剂、防针孔剂等。辅助添加剂在各自岗位上发挥一些不可或缺的作用。
7.2.3 普通镀镍
普通镀镍又称镀暗镍,是指镀液不添加光亮剂而获得镍本色的镀层。这是最基本的镀镍工艺,如用于装饰,则镀镍镀层需要进行机械抛光。普通镀镍的镀液可分为预镀液、普通镀液、瓦特镀液和滚镀液等。
普通镀镍的溶液组成及工艺规范见表7-19。
表7-19 普通镀镍的溶液组成及工艺规范

①也可以采用LB低泡润湿剂1~2mL/L,来代替十二烷基硫酸钠。LB低泡润湿剂为上海永主助剂厂的产品。
注:普通镀液配方3的ST-1、ST-2添加剂是上海日用五金工业研究所的产品。
7.2.4 镀多层镍
镀多层镍是指在同一基体上,选用不同的镀液成分及工艺规范,镀得二层、三层和四层不同类型的镍镀层。这种镀层主要利用各不同镍层电位差来达到电化学保护的目的,以改善防护装饰性镀层体系,并在不增加或减低镍层厚度的基础上,增加镍层的耐蚀能力。
(1)多层镍的组合形式
目前生产上应用较多的多层镍/铬组合体系有:
双层镍 半光亮镍/光亮镍/铬
三层镍 半光亮镍/高硫镍/光亮镍/铬
半光亮镍/光亮镍/镍封/铬(微孔铬)
半光亮镍/光亮镍/高应力镍/铬(微裂纹铬)
四层镍 半光亮镍/高硫镍/光亮镍/镍封/铬(微孔铬)
(2)多层镍的耐蚀性
多层镍/铬镀层体系之所以能提高镀层抗腐蚀性能,是由于电化学的保护作用。电化学保护分为牺牲阳极型(如双层镍和高硫镍组合的镀层)和腐蚀分散型(如镍封及高应力镍组合的镀层)两种。
①牺牲阳极型的保护。它是通过牺牲多层镍组合镀层中电位较负的镀层(成为阳极,被腐蚀),来延缓电位较正镀层的腐蚀,从而使整个镀层体系的耐腐蚀性能得到提高。镍镀层中含硫量越高,电位越负。
②腐蚀分散型的保护。在有大量的微孔或微裂纹的铬镀层表面上,使腐蚀电流大大分散,从而达到延缓腐蚀,使整个镀层体系的耐腐蚀性能明显提高。
(3)单层镍、双层镍和三层镍体系
金属在大气中腐蚀是一种电化学过程。单层镍镀层与双层镍镀层的腐蚀和钢铁基体保护的作用机理是不同的。单层镍-铬镀层、双层镍-铬镀层及三层镍-铬镀层的腐蚀机理如表7-20所示。
表7-20 单层镍、双层镍-铬镀层及三层镍-铬镀层的腐蚀机理

(4)半光亮镍/光亮镍/镍封/微孔铬的组合体系
在这种组合体系中,将半光亮镍镀层和光亮镍镀层作为基础镀层,然后镀一层镍封(即封闭镀镍)和微孔铬。这种组合体系的腐蚀机理如表7-21所示。
表7-21 半光亮镍/光亮镍/镍封/微孔铬的组合体系的腐蚀机理

(5)半光亮镍/光亮镍/高应力镍/微裂纹铬的组合体系
这种组合体系,是在光亮镍镀层上再镀一薄层高应力镍,由于高应力镍的内应力大,与其镀上的薄层铬的相互作用下,产生大量微裂纹。在腐蚀介质作用下,这些微裂纹部位形成无数个微电池,使腐蚀电流分散到微裂纹处,将局部的严重腐蚀转变为缓慢的均匀腐蚀。其耐蚀机理与镍封/微孔铬组合体系一样。
7.2.5 半光亮镀镍
半光亮镍镀层一般用于镀多层镍的底层,要求其镀层不含硫或仅含少量的硫,硫的质量分数少于0.003%,并有较好的整平性,与上层的镍镀层之间有好的结合力。半光亮镀镍的溶液组成及工艺规范见表7-22。
表7-22 半光亮镀镍的溶液组成及工艺规范

注:1.配方2的BN-99添加剂是武汉材料保护研究所的产品。
2.配方3的SN-92无硫半光亮镍添加剂是上海永生助剂厂的产品。
3.配方4的SPECTRAT-501、502、503等是上海永星化工有限公司的产品。
4.配方5的BH-963是广州二轻工业研究所的产品。
5.配方6的SNB-1等是武汉吉和昌精细化工有限公司的产品。
6.配方7的NS-23A、NS-23B、NS-118是广州电器科研所的产品。
7.2.6 光亮镀镍
光亮镀镍是在瓦特型或普通型镀镍溶液中,加入某些添加剂而直接镀取得的白色或乌亮的光亮镍镀层的一种镀镍方法。目前所指的光亮镀镍,是指既能达到镜面光泽的外观,又具有优良整平性的镀镍工艺。质量优良的镀镍光亮剂,可获得良好整平性和镜面光亮度的镀层,而且韧性好,孔隙率低。镜面光亮镍镀层可以直接套铬,不必再经过机械抛光,可大大减少抛光工作量和镍镀层损耗。
挂镀光亮镀镍的溶液组成及工艺规范见表7-23。
表7-23 挂镀光亮镀镍的溶液组成及工艺规范

注:1.配方1的BN-92A、BN-92B光亮剂是武汉材料保护研究所的产品。
2.配方2的3#或5#镀镍光亮剂A、B及LB低泡润湿剂是上海永生助剂厂的产品。
3.配方3的3#或5#镀镍光亮剂A、B及LB低泡润湿剂是上海永生助剂厂的产品。
4.配方4的N-100主光亮剂、N-101走位剂是武汉风帆表面工程有限公司的产品。
5.配方5的HKB-3光亮剂、Ni Conc柔软剂等是安美特(广州)化学有限公司的产品。该配方提出需要加入FE-1添加剂。
6.配方6的NP631主光亮剂、NP630辅助剂等是安美特(广州)化学有限公司的产品。
滚镀光亮镀镍的溶液组成及工艺规范见表7-24。
表7-24 滚镀光亮镀镍的溶液组成及工艺规范

注:1.配方1的N-200B开缸剂、N-201B补加剂是武汉风帆表面工程有限公司的产品。
2.配方2的200#或300#A、B及LB低泡润湿剂是上海永生助剂厂的产品。
3.配方3的BH-932A开缸剂、BH-932B润湿剂是广州二轻工业科学技术研究所的产品。
4.配方4的TS-1000主光亮剂等是德胜国际(香港)有限公司,深圳鸿运化工原料行的产品。
5.配方5的RNI-3A走位剂、RNI-3B光亮剂是广州美迪斯新材料有限公司的产品。
6.配方6的FK-833A开缸剂、FK-833B补加剂是福州八达表面工程技术研究所的产品。
7.2.7 镀高硫镍
高硫镍镀层主要用于钢、锌合金基体的防护-装饰性组合镀层体系(三层镍镀层)的中间层,其底层是半光亮镍镀层,上层是光亮镍镀层。
镀高硫镍工艺要点见表7-25。
表7-25 镀高硫镍工艺要点

实验测得镍镀层含硫量与电极电位的对应关系见表7-26。
表7-26 镍镀层含硫量与电极电位的对应关系[20]

镀高硫镍的溶液组成及工艺规范见表7-27。
表7-27 镀高硫镍的溶液组成及工艺规范

注:1.配方2的HS高硫镍添加剂及LB低泡润湿剂是上海永生助剂厂的产品。
2.配方3的TN-98高硫镍添加剂是武汉材料保护研究所的产品、HSA-60高硫镍添加剂是温州美联物资有限公司的产品。
3.配方4的TS-3、TS-812添加剂是德胜国际(香港)有限公司,深圳鸿运化工原料行的产品。
4.配方5的NS-32高硫镍添加剂是广州电器科学研究所的产品。
5.配方6的BNT-2高硫镍添加剂是杭州东方表面技术有限公司的产品。
7.2.8 封闭镀镍
封闭镀镍简称为镍封,或称为复合镀镍。镍封闭镀层是为了提高防护-装饰性镀层体系的耐腐蚀性能而开发的镀层。
在光亮镍溶液中加入一些固体非导体微粒(一般有二氧化硅、硫酸钡和氧化硅等,微粒直径<0.05μm),借助搅拌,使固体微粒与镍离子共同沉积,并均匀分布在金属组织中,在制件表面形成由金属镍和非导体固体微粒组成的致密复合镀层。镍封闭镀层厚度不宜过厚,以2~3μm为宜。镀液需剧烈搅拌,不能有搅拌不到的死角。
封闭镀镍的溶液组成及工艺规范见表7-28。
表7-28 封闭镀镍的溶液组成及工艺规范

注:1.配方1的NS-51A、NS-51B、NS-52、NS-52镍封粉是广州电器科学研究所的产品。
2.配方2的BN-99-MIC光亮剂、柔软剂、微孔乳液、分散剂、润湿剂是武汉材保电镀技术生产力促进中心的产品。
3.配方3的NB1080-A、B、C、D是上海诺博化工有限公司的产品。
4.配方4的SF-352A、B、C、D、E是广州市三孚化工有限公司的产品。
5.配方5的NC-1、NC-2是上海长征电镀的产品。
7.2.9 镀高应力镍
在特定的镀镍溶液中,加入适量的特殊添加剂,能镀得应力很大的容易龟裂成微裂纹的镍镀层,叫作高应力镍。这种镍镀层的应力很大,如光亮镍镀层在厚度为5μm时,镀层应力为0.012MPa,而同样厚度的高应力镍镀层应力则为3.41MPa。在光亮镍镀层上镀一层1~3μm左右的高应力镍镀层(高应力镍镀层能达500~1500条/cm),在高应力镍镀层上再镀一层0.2~0.3μm的普通铬镀层。铬镀层在与高应力镍的相互作用下,导致铬镀层表面也形成均匀的微裂纹。
镀高应力镍的溶液组成及工艺规范见表7-29。
表7-29 镀高应力镍的溶液组成及工艺规范

注:1.配方2的MCN-1、MCN-2添加剂是上海长征电镀厂的产品。
2.配方3的GYN-1、GYN-2添加剂是上海轻工业研究所的产品。
3.配方4的HNS-1、HNS-2添加剂是上海永生助剂厂的产品。
4.配方5的PN-1、PN-2添加剂是武汉材料保护研究所的产品。
7.2.10 镀缎面镍
缎面镍又称沙丁镍、珍珠镍或麻面镍。它具有绸缎般的光泽,略呈乳白色。还具有结晶细致,孔隙少、耐蚀性好的特性,不会因手触摸而留下痕迹。在缎面镍层上镀装饰铬、光亮银或光亮金,可分别形成沙铬、沙银或沙金。广泛应用于防护-装饰性镀层。
目前制作缎面镍镀层的最普遍使用的方法是乳化剂法。这种方法需要向镀镍溶液中加入非离子表面活性剂。目前,市场商品中有很多缎面镀镍添加剂可供选用。
镀缎面镍的溶液组成及工艺规范见表7-30。
表7-30 镀缎面镍的溶液组成及工艺规范

7.2.11 镀黑镍
黑色镍镀层具有很好的消光能力,常用于光学仪器、摄影照相及电信器材等。黑色镍镀层对太阳能的辐射有着较高的吸收率,可用于太阳能集热板。
黑镍镀层中含有镍、锌、硫化物及有机物等。它的组成随镀液成分及工艺规范而变化,大约含镍40%~60%、锌20%~30%、硫10%~15%、有机物10%(均为质量分数)。黑镍镀层比较硬,镀层较薄,一般只有2μm左右,耐蚀性较差,经过涂漆或浸油处理,可提高耐蚀性。在钢铁件上直接镀黑镍,镀层与基体结合力差,因此,一般是先镀暗镍或亮镍再镀黑镍。镀黑镍的溶液组成及工艺规范见表7-31。
表7-31 镀黑镍的溶液组成及工艺规范

注:1.挂镀配方3也适用于滚镀,BS-101黑镍开缸盐和BS-102黑镍添加剂是广州美迪斯新材料有限公司的产品。
2.挂镀配方4的黑镍盐是德胜国际(香港)有限公司、深圳鸿运化工原料行的产品。
3.挂镀配方5的BS-1黑镍调和盐、BS-2黑镍添加剂是广州美迪斯新材料有限公司产品。
7.2.12 镀枪色镍和合金
枪色镍镀层的色泽不同于黑镍,而是一种铁灰色闪烁着寒光略带褐色的黑,接近枪械的颜色,称为枪色。枪色镍镀层是靠加入一种或几种有机添加剂来实现的。镀层薄,约2μm左右,一般在光亮镍或光亮铜镀层、青铜等镀层上镀覆枪色镍镀层,为提高耐蚀性,其镀层表面再涂覆透明涂料保护。镀枪色镍-锡合金拥有比枪色镍镀层更好的性能,其结晶细密,硬度高,耐磨性和耐蚀性好,镀层不易变色,应用非常广泛。镀枪色镍和镍合金的溶液组成及工艺规范见表7-32。
表7-32 镀枪色镍和镍合金的溶液组成及工艺规范

注:1.配方1的PBN枪色镍盐、PBN添加剂(增黑剂)由上海永生助剂厂研制。
2.配方2的锡盐开缸剂、镍盐补缸剂由上海永生助剂厂研制。
3.配方3适用于挂镀及滚镀,挂镀宜采用阴极移动、连续过滤。其使用的发黑剂、调整剂是广州美迪斯新材料有限公司的产品。
4.配方4的XSN-1枪色镀镍添加剂、XSN-2含硫聚胺化合物溶液由厦门大学研制。
5.配方5的90组合添加剂由上海大庆电镀厂研制。锡钴合金(不含镍),镀层为偏蓝紫色的枪黑,色泽均匀,极具特色,适用于眼镜、首饰等工件的装饰性电镀。
7.2.13 其他镀镍
其他镀镍有柠檬酸盐镀镍、氯化物镀镍、氨基磺酸盐镀镍等。
其他镀镍的技术特点见表7-33。
表7-33 其他镀镍的技术特点

其他镀镍的溶液组成及工艺规范见表7-34。
表7-34 柠檬酸盐镀镍的溶液组成及工艺规范

注:柠檬酸盐镀镍配方2为中性预镀镍工艺,电镀时间3~5min。PNI-A络合剂、PNI-B添加剂是广州美迪斯新材料有限公司的产品。镀件下槽后,先用5~7A/dm2的阴极电流密度冲击电镀,时间为0.35~1min,然后进行正常电镀,时间为3~5min。
7.2.14 不合格镍镀层的退除
在镍镀层上如有铬镀层,一般应先用盐酸退除铬层。不良镍镀层的退除方法见表7-35。
表7-35 不良镍镀层的退除方法


7.3 镀铬
铬镀层具有很好的化学、物理性能。铬电极电位虽然很负,但它有强的钝化性能,在大气中很快钝化,从而使铬镀层的电位向正方向移动,使电位变正,显示出贵金属的特性。对于钢铁零件,铬镀层是阴极镀层。所以,一般铬不直接镀覆在钢铁件上(除加厚铬镀层或功能性镀层外)。
铬镀层具有很高的耐热性,较小的摩擦系数,很好的耐磨性,良好的反射能力等优良的性能。广泛用于防护-装饰性镀层体系的表层和功能性镀层。装饰性镀铬是镀铬的主体,在电镀工业中占有重要的地位。
7.3.1 普通镀铬
普通镀铬应用广泛,在普通镀铬溶液的基础上加入不同的催化添加剂,能开发出各种不同类型的镀铬溶液。普通镀铬溶液基本组分为铬酐和硫酸,按铬酐浓度可分为低、中、高浓度三种镀液。普通镀液,成分简单,使用方便,是目前应用量最多和应用面最为广泛的镀铬溶液。普通镀铬溶液的特点及应用见表7-36。
表7-36 普通镀铬溶液的特点及应用

(1)镀液组成及工艺规范
普通镀铬的溶液组成及工艺规范见表7-37、表7-38。
表7-37 普通镀铬的溶液组成及工艺规范

注:中浓度镀液配方2为标准镀铬溶液。
表7-38 加有添加剂的普通镀铬的溶液组成及工艺规范

注:1.低浓度镀液配方1的LC-2添加剂是上海永生助剂厂的产品。镀液电流效率为22%~26%。深镀能力好。兼有除铜、铁、镍等金属杂质的作用。本添加剂适用于装饰性镀铬。
2.低浓度镀液配方2的WR-1添加剂是武汉风帆电镀技术有限公司的产品。本品工艺稳定,维护方便,装饰、硬铬均可。分散能力提高30%~60%。
3.中浓度镀液配方1的4HC-A剂、4HC-B剂是上海永生助剂厂的产品。镀液电流效率为22%~25%。镀层光亮度高,适宜镀厚铬层,工艺稳定,硫酸含量范围宽;分散能力和覆盖能力好,特别适用于复杂零件镀装饰铬。
4.中浓度镀液配方2的CR-842添加剂是广州市达志化工科技有限公司的产品。沉积速度快,阴极电流效率高,分散能力和覆盖能力好。
5.中浓度镀液配方3的CS1添加剂是美坚化工原料有限公司的产品。沉积快,电流效率高,不易烧焦,有极佳的覆盖能力,可自动调节催化剂浓度。
6.阳极材料用的合金含量百分数均为质量分数。
(2)提高铬镀层结力的措施
提高铬镀层与基体金属的结合力,可采用几种方法[21],见表7-39。
表7-39 提高铬镀层与基体金属结合力的方法

(3)铬镀层的渗氢和除氢
在镀铬过程中,由于镀液电流效率很低,会在阴极上析出大量的氢,而吸附在阴极上的氢大部分结合成氢分子,氢分子聚合成小气泡并逐渐长大,最后离开阴极表面而逸出。剩余的氢一部分被镀层吸收,另一部分被基体所吸收,渗入基体晶体内,而造成不同的内应力,便会形成脆性断裂,这种氢脆现象严重威胁产品质量。
为减少镀铬对机械加工、研磨、成形、冷矫形零件基体材料使用性能的影响,抗拉强度大于1034MPa钢铁关键件、重要件镀前必须进行消除应力处理,镀后应进行除氢处理。消除应力及除氢处理条件[5]见表7-40。
表7-40 镀前消除应力和镀后除氢处理条件

注:除氢必须在镀铬后4h内进行。
7.3.2 防护-装饰性镀铬
装饰性铬镀层必须有中间镀层以保证有足够的防腐蚀能力,常用的中间层有亮铜、镍、铜-锡合金、铜-锌合金、镍-铁合金等镀层,在光亮或经过抛光的中间镀层上镀铬后,可以得到带银蓝色光泽的镜面镀层。
防护-装饰性镀铬,可分为一般防护-装饰性镀铬(也称常规防护-装饰性镀铬)和高耐蚀性-装饰镀铬。一般防护-装饰性镀铬应用最广泛,多用于室内温和环境使用的产品。高耐蚀性-装饰镀铬多用于耐蚀性要求高的室外严酷环境用的产品。
(1)一般防护-装饰性镀铬
一般防护-装饰性镀铬应用最为广泛,要求镀层光亮、镀液覆盖能力好,采用多镀层体系,铬镀层一般在0.25~0.5μm,多用0.3μm。
装饰镀铬的镀液一般常用普通镀铬溶液的中、高浓度的镀液,还可用复合镀铬、自动调节镀铬、快速镀铬、四铬酸盐镀铬、稀土镀铬等镀液。其镀液组成及工艺规范分别见各种镀种的镀液组成、工艺规范。采用稀土镀铬,铬酐浓度可降至150~200g/L,而覆盖能力、电流效率要明显提高。
装饰镀铬宜采用中等偏低的温度,常采用55℃±5℃。温度过低镀层灰暗;适中镀层光亮;过高外观呈乳色。加入稀土添加剂后,在低温下也能得光亮的镀层。
装饰镀铬的电流密度范围很宽,随着镀液温度而定,它们的对应关系[3]见表7-41。
表7-41 镀液温度与电流密度的关系

(2)高耐蚀性-装饰镀铬
高耐蚀性-装饰镀铬,常采用双层镍或三层镍与不连续铬(微孔铬和微裂纹铬)组成的镀层体系,具有很高的防腐蚀性能。
镍封闭镀镍及高应力镀镍的镀液及工艺规范,参照本章镀镍中的镍封闭镀镍及高应力镀镍工艺。镀铬的镀液及工艺规范基本上与一般防护-装饰性镀铬相同。一般常用普通镀铬溶液的中、高浓度的镀液,还可用复合镀铬、自动调节镀铬、快速镀铬、四铬酸盐镀铬等镀液。采用稀土镀铬,铬酐浓度可降至150~200g/L,而覆盖能力、电流效率要明显提高。
7.3.3 镀硬铬
镀硬铬(也称耐磨铬)是功能性镀铬中使用面广、用量大的重要镀种。镀层硬度高,随工艺条件的不同,其硬度可达维氏硬度6865~9807MPa。该铬镀层还具有耐磨、耐热、耐腐蚀等优良性能。而且铬镀层摩擦系数低,当与其他金属表面对磨时不易磨损、卡住和咬死。
(1)硬铬镀层的厚度
硬铬可以直接镀在钢铁基体上,并要求被沉积在足够硬的基体上。硬铬镀层厚度一般为2~50μm,特殊耐磨镀铬为50~300μm,修复磨损零件可达800~1000μm,通常还要进行机加工。镀后进行除氢。硬铬镀层的适宜厚度参见表7-42。
表7-42 硬铬镀层的适宜厚度

(2)镀液组成及工艺规范
镀硬铬溶液有普通镀铬溶液(即常规镀硬铬溶液)和高效镀铬溶液。目前,在国内从催化剂及添加剂上来研究如何提高电流效率、覆盖能力等,取得不少成果,镀层质量已有很大提高。
①普通镀铬溶液。普通镀铬溶液的组成及工艺规范见表7-43。
表7-43 普通镀铬溶液的组成及工艺规范

②高效镀铬溶液。高效镀铬溶液是在普通镀铬溶液中,加入一种或几种有机添加剂,并辅助加入少量无机化合物,使其镀液及镀层获得优良的性能。目前,国内已有这类添加剂商品供应。高效镀硬铬的溶液组成及工艺规范见表7-44。
表7-44 高效镀硬铬的溶液组成及工艺规范

注:1.配方1的3HC-25添加剂、8F铬雾抑制剂是上海永生助剂厂的产品。电流效率可达到20%~27%,沉积速度快,达1~1.5μm/min。硬度达HV1000以上。3HC-25消耗量约2~4mL/(kA·h)。阳极为含锡8%的铅锡合金板(经过锻压)或含锑6%的铅锑合金板(经过锻压)。
2.配方2的CR-102A开缸剂是广东达志化工有限公司的产品。
3.配方3的STHC-2添加剂是郑州鑫顺电镀技术有限公司的产品。镀层硬度可达1000HV以上,阴极电流效率可达22%~27%,能产生微裂纹(400~1000条/cm2以上)。
4.配方4的HP-6201添加剂是东莞市华普表面处理有限公司的产品。
5.配方5的HVEE添加剂是江苏梦得电镀化学品有限公司的产品。
6.配方6的CR-203A开缸剂是广州美迪斯新材料有限公司的产品。镀层具有微裂纹(400~1500条/cm2),耐蚀性高。镀层硬度为1050~1200HV。阴极电流效率达26%。可用铬雾抑制剂,改善操作环境。
7.3.4 滚镀铬
滚镀铬多用于体积小、数量多又难于悬挂的零件的装饰性镀层。但只适用于形状简单、具有一定自重的零件;不适用于扁平片状、自重轻以及外观要求较高的零件的电镀。
滚镀铬比滚镀其他金属要困难些,因为镀铬液覆盖能力差,滚镀铬无牢固的接触点,电流不连续使镀层结合力和光亮度降低,镀液升温快。
滚镀铬溶液不能只采用硫酸催化剂,应采用与氟硅酸(或氟硅酸盐等)配合使用的催化剂。这是因为滚镀铬时镀件不断传(翻)动和相互碰撞,会使电接触的情况不断变化,电流密度时大时小,甚至还有断电的过程,而滚镀液加进了氟硅酸离子后,会使其具有活化铬镀层表面的作用,使电流中断后再镀时,仍然能获得结合力良好的光亮铬镀层。
滚镀铬对镀件的镀前处理比较简单。由于是在中间层(如镍、锌-铜、铜-锡、镍-铁、锌-铁合金等)上套铬,可在5%(体积分数)硫酸的溶液中活化,仔细清洗后就可以进行滚镀铬。
滚镀铬的溶液组成及工艺规范见表7-45。
表7-45 滚镀铬的溶液组成及工艺规范

7.3.5 复合镀铬
由铬酐和两种催化剂硫酸和氟硅酸组成的镀液,称为复合镀铬溶液。具有电流效率高(18%~25%)、分散能力和覆盖能力好、光亮电流密度范围宽、阴极电流密度可提高到80A/dm2以上等特点。复合镀铬适用于装饰性镀铬、镀硬铬及小件滚镀铬。氟硅酸可降低沉积铬的临界电流密度,并具有活化作用,短时断电,重新电镀不会引起铬层脱皮。但镀液腐蚀性强,必须采取相应的防护措施。
复合镀铬与普通镀铬的比较见表7-46。
表7-46 复合镀铬与普通镀铬的比较

装饰性复合镀铬的溶液组成及工艺规范见表7-47。
表7-47 装饰性复合镀铬的溶液组成及工艺规范

注:1.配方5的氟硅酸含量3~5g/L,以100%计。
2.阳极采用铅-锡合金。
硬铬、厚铬等复合镀铬的溶液组成及工艺规范[1]见表7-48。
表7-48 硬铬、厚铬等复合镀铬的溶液组成及工艺规范

注:1.因镀层裂纹不明显,不宜用于松孔镀铬。
2.氟硅酸也可用氟硅酸钠,含量4~8g/L。
3.阳极采用铅-锡合金。
7.3.6 自动调节镀铬
自动调节镀铬与标准镀铬的不同之处,是在其溶液中以硫酸锶代替了标准镀铬溶液中的硫酸,与新添加的氟硅酸钾,组成复合催化剂。由于在电镀过程中,过量添加的低溶解度的催化剂的盐类,能够通过自动电离来补充镀液中的硫酸催化剂,从而可以自动调节镀液。自动调节镀铬的溶液组成及工艺规范见表7-49。
表7-49 自动调节镀铬的溶液组成及工艺规范

7.3.7 快速镀铬
快速镀铬溶液,是在普通镀铬溶液(标准镀铬溶液)的基础上,加入硼酸及氧化镁,可允许使用较高的电流密度,从而提高了沉积速度,所得镀层内应力小,与基体的结合力好,分散能力好,镀层结晶细致,硬度高(HRC61~62)。
快速镀铬的溶液组成及工艺规范见表7-50。
表7-50 快速镀铬的溶液组成及工艺规范

7.3.8 冷镀铬
在室温下进行镀铬,称为冷镀铬,对铜及铜合金件无显著腐蚀。电流效率高,分散能力和覆盖能力很好,由于阴极电流密度较低,沉积速度慢,可适用于镀薄的光亮铬镀层。冷镀铬可以挂镀和滚镀,多用于滚镀。
镀液由铬酐和氟化物(NH4F或NaF)组成,也可加入少量硫酸。镀液温度和阴极电流密度较低。冷镀铬的溶液组成及工艺规范见表7-51。
表7-51 冷镀铬的溶液组成及工艺规范

7.3.9 四铬酸盐镀铬
这类镀液中的铬酸被碱中和到以四铬酸钠(Na2O·4CrO3)形式存在,因此称为四铬酸盐镀铬。镀液的铬酐浓度较高,除含有铬酐、硫酸外,还加有氢氧化钠、氟化钠、柠檬酸钠和糖等。这种镀液的允许阴极电流密度高(20~80A/dm2)、沉积速度快、电流效率高(可高达30%~37%)。镀液具有良好的分散能力和覆盖能力,可使复杂零件无需采取特殊处理措施。镀层结晶细致、孔隙少、易抛光,具有良好的耐蚀性。但镀层硬度较低。镀层色泽灰暗,如需光亮度,必须抛光。使用高电流密度时,需要冷却镀液。四铬酸盐镀铬是很有发展前途的一种新镀液,但由于镀层色泽与铬酸镀液获得的镀层色泽还有差距,尚未取得大量应用。
四铬酸盐镀铬的溶液组成及工艺规范见表7-52。
表7-52 四铬酸盐镀铬的溶液组成及工艺规范

7.3.10 双层镀铬
双层镀铬也称双重铬。其作用提高镀层的耐蚀性、耐磨性。有两种双层铬形式,即耐蚀双层铬和耐磨双层铬。
(1)耐蚀双层铬
先在标准镀铬溶液中镀第一层铬,然后在无气孔和低裂纹的镀铬溶液中镀第二层铬,可以获得高耐蚀性的铬镀层。其溶液及工艺规范[1]见表7-53。
表7-53 耐蚀双层铬的溶液组成及工艺规范

(2)耐磨双层铬
先镀上一层10~20μm乳白铬,然后在其上再镀一层20~30μm耐磨性硬铬,这种组合的耐磨双层铬,既耐蚀又耐磨。
这种铬镀层的电镀方法,可以在同一镀铬槽内进行。先将镀液温度加热到65~70℃,镀第一层乳白铬;不取出镀件,也不断电,将阴极电流密度降至5~15A/dm2,将镀液温度降到58~60℃范围,再提高阴极电流密度至55~60A/dm2,镀硬铬镀到所需时间。耐磨双层铬的溶液组成及工艺规范[1]见表7-54。
表7-54 耐磨双层铬的溶液组成及工艺规范

7.3.11 镀乳白铬
通过改变镀铬溶液的工艺规范,在较高镀液温度(65~75℃)和较低的阴极电流密度(20A/dm2±5A/dm2)下获得的乳白色的无光泽的铬镀层称为乳白铬。镀层具有柔和舒适、带有弱反光的乳白色调,韧性好,能承受较大的变形而镀层不致剥落。铬镀层孔隙少、裂纹少、内应力小、耐蚀性好,但镀层硬度比硬铬稍低些,维氏硬度为5884~6865MPa(HV600~700)。
乳白铬可直接镀覆在钢、锌、铝制品上,以代替多层电镀。在乳白色铬镀层上再镀一层光亮硬铬,能提高耐蚀耐磨性能,这种镀层称为双层铬。
乳白铬直接镀在经喷砂后的表面,能达到缎面铬外观,并具有良好的耐蚀性,常用于量具、分度盘、仪器面板等镀铬。
镀乳白铬的溶液组成及工艺规范见表7-55。
表7-55 镀乳白铬的溶液组成及工艺规范

7.3.12 镀黑铬
黑铬是在一定组成的镀液中,获得没有反光作用的镀层。它不是纯金属铬,而是由金属铬和三氧化二铬的水合物组成,呈树枝状结构,金属铬以微粒形式弥散在铬的氧化物中,形成吸光中心,使镀层呈现黑色,即黑色铬镀层。
黑铬镀层属于功能性镀层中的一种特殊镀层,具有耐磨、耐蚀、耐热等优点。耐蚀性优于普通镀铬,热稳定性高,与底层结合力好。但硬度较低,只有HV130~350。镀黑铬应用广泛,尤其是用于太阳能吸收器的吸收镀层。
黑铬镀层可以直接在钢铁、铜、镍和不锈钢上进行电镀,也可先镀中间层,如钢铁件镀黑铬,先镀铜、镍或铜-锡合金作底层;黄铜镀黑铬则用镀镍作底层。黑铬电镀工艺与装饰性镀铬相似,可采用双层镍或三层镍等高耐蚀性电镀工艺。
镀黑铬的溶液组成及工艺规范见表7-56、表7-57。
表7-56 镀黑铬的溶液组成及工艺规范

表7-57 市售商品添加剂的镀黑铬工艺规范

7.3.13 松孔镀铬
松孔铬亦称为网纹铬,是对已有的硬铬镀层进行阳极处理(松孔处理),使铬镀层原有的网状裂纹加深加宽,使其具有一定疏密程度和深度而彼此沟通的网状沟纹的硬铬镀层。松孔铬镀层是耐磨铬镀层中的特殊镀层。该镀层具有很好的吸油(储油)能力,工作时,沟纹内储存的润滑油被挤出,溢流在工作表面上,由于毛细管作用,润滑油还可以沿着沟纹渗到整个工作表面,从而改善整个工作表面的润滑性能,降低摩擦系数,提高铬镀层的耐磨能力,同时,因镀层内有油,也大大提高了耐蚀性。
松孔铬镀层主要应用于摩擦状态下工作的零件,如内燃机汽缸腔、活塞环、滑动轴承、油门操纵轴以及起重机的活塞杆等。对松孔铬镀层的技术要求,如表7-58所示。
表7-58 松孔铬镀层的技术要求

(1)松孔镀铬的加工方法
松孔镀铬的加工方法有机械法、化学法和电化学浸蚀法,而目前最常用的是电化学浸蚀加工方法。其加工方法见表7-59。
表7-59 松孔镀铬的加工方法

(2)镀液组成及工艺规范
松孔镀铬的溶液组成及工艺规范见表7-60。
表7-60 松孔镀铬的溶液组成及工艺规范

阳极松孔处理的溶液组成及工艺规范见表7-61。
表7-61 阳极松孔处理的溶液组成及工艺规范

7.3.14 三价铬镀铬
为了取代危害性大、严重污染的六价铬电镀,人们经过长期不懈的努力,进行大量的研究,目前对三价铬镀铬方面已取得明显的进展,已在装饰性电镀方面获得工业应用。
三价铬镀铬与六价铬镀液比较,其工艺特点如表7-62所示。
表7-62 三价铬镀铬工艺特点

三价铬镀铬的难点见表7-63。
表7-63 三价铬镀铬的难点

目前,三价铬镀铬研究、开发和应用的镀液类型有硫酸盐三价铬镀液体系和氯化物三价铬镀液体系两种。
(1)硫酸盐三价铬镀铬
硫酸盐三价铬电镀发展相对较晚。20世纪90年代以后,在研究中发现硫酸盐体系三价铬电镀具有很多特点,于是该体系的研究和发展迅速。近几年来,三价铬电镀在我国发展迅速,相继推出了一些产业化的三价铬镀铬商品。
硫酸盐三价铬镀铬工艺的特点[25]见表7-64。
表7-64 硫酸盐三价铬镀铬工艺的特点

目前硫酸盐三价铬镀液体系大致可分为两种类型:一类是含铬浓度较高(约0.4mol/L),使用温度较高(40~50℃);另一类是含铬浓度较低(约0.2mol/L以下),使用温度较低,常温即可。
新近发展的几种硫酸盐三价铬镀铬的溶液组成及工艺规范见表7-65。
表7-65 硫酸盐三价铬镀铬的溶液组成及工艺规范[25]

注:镀液配方中硫酸铬-柠檬酸盐体系,是否应为硫酸铬-甲酸盐体系。
(2)氯化物三价铬镀铬
氯化物三价铬镀铬工艺的研究和开发比较早,几十年来这种工艺已有了很大进步和发展,成为最早产业化的三价铬电镀工艺,有些已投入工业应用。
氯化物三价铬镀铬工艺的特性见表7-66。
表7-66 氯化物三价铬镀铬工艺的特性

氯化物三价铬镀铬的溶液组成及工艺规范见表7-67。
表7-67 氯化物三价铬镀铬的溶液组成及工艺规范[25]

(3)商品添加剂的三价铬镀铬
近年来,国内一些单位经开发研制,已相继推出了一些三价铬镀铬的添加剂,并已投入生产应用,取得良好的效果。其工艺规范见表7-68。
表7-68 商品添加剂的三价铬镀铬工艺规范

(4)三价铬镀铬用的阳极
阳极对三价铬镀液的稳定性有很大影响。在三价铬镀铬的过程中,阳极附近的Cr3+常会被阳极析出的氧氧化成Cr6+,因此,如何在阳极氧化过程抑制六价铬(Cr6+)生成和积累,是非常重要的。这必须从阳极选用方面来考虑,以达到控制六价铬的目的。目前在三价铬镀铬中所采用的阳极大致有表7-69中的几种。
表7-69 三价铬镀铬中所采用的阳极

7.3.15 三价铬镀黑铬
近年来,三价铬镀黑铬发展很快,达到工艺生产程度,已有商业产品出售,但仍存在着铬镀层外层黑度不够、镀液稳定性差等的问题,需进一步改进和提高。
三价黑铬镀液与三价白铬镀液的组成相似,主要区别是补充了发黑剂。
三价铬镀黑铬溶液组成及工艺规范见表7-70。
表7-70 三价铬镀黑铬溶液组成及工艺规范

商品添加剂的三价铬镀黑铬工艺规范见表7-71。
表7-71 商品添加剂的三价铬镀黑铬工艺规范

7.3.16 低铬酸镀铬
低铬酸镀铬溶液中的铬酐浓度低(50g/L左右),只有常规标准镀铬溶液的20%~25%,大大降低对环境的污染,也减少铬酐的消耗。
低铬酸镀铬的电流效率和镀层硬度,介于标准镀液与复合镀液之间;耐蚀性与高浓度镀铬相当。但由于铬酸浓度大幅度降低后,引起镀液电导率降低,槽电压升高,镀液的pH值提高,镀液覆盖能力较差,镀层外观较差(有彩色膜和黄膜等)。如果加入第二催化剂,可改善覆盖能力,电流效率可提高到21%~26%,并使硬度较高,镀层光泽。所以,低铬酸镀铬主要是选择合适的催化剂种类(如硫酸、氟硅酸及卤素化合物)及含量,如匹配合适就能获得较好的镀铬溶液和镀层质量。
低铬酸镀铬的溶液组成及工艺规范见表7-72。
表7-72 低铬酸镀铬的溶液组成及工艺规范

注:1.阳极面积∶阴极面积=(2~3)∶1。
2.阳极一般采铅-锡合金(质量分数为铅70%、锡30%)。
7.3.17 稀土镀铬
稀土镀铬溶液,是在传统镀铬溶液的基础上,加入一定量稀土添加剂及氟离子。可以降低铬酐的浓度、拓宽镀液温度范围,并降低和拓宽阴极电流密度范围,使阴极电流效率高,提高镀液的导电性,降低槽压,有些添加剂还能直接镀取微孔铬或微裂纹铬。使镀铬生产初步实现低温度、低能耗、低污染和高效率,即所谓的“三低一高”的镀铬工艺。稀土镀铬现已在工业生产中获得较广泛的应用。但稀土添加剂多为物理混合体系,成分复杂,常规方法又不能化验其成分和杂质,给镀液带来不可靠性和不稳定性。镀液维护较困难。市售商品的很多添加剂即为混合稀土,给镀液的控制带来许多不便。
稀土镀铬的溶液组成及工艺规范见表7-73。
表7-73 稀土镀铬的溶液组成及工艺规范

注:1.阳极合金材料中Sn的含量均为质量分数。
2. CS添加剂是江苏省常熟环保局、常熟市兴隆电镀材料厂的产品。
3. CE-198型稀土镀铬,在新配镀液中应加0.3mL/L的酒精。CE-198添加剂是江苏梦得电镀化学品有限公司的产品。
4. CF-201添加剂是江苏省宜兴市新新稀土应用研究所的产品。
5. RL-3C添加剂是湖南省稀土金属材料研究所的产品。
6. HIL、HIS1添加剂是湖南省稀土金属材料研究所的产品。
7. LS-Ⅲ添加剂是安徽省合肥市科化精细化工研究所的产品。
7.3.18 不合格铬镀层的退除
不合格铬镀层的退除方法见表7-74。
表7-74 不合格铬镀层的退除方法

铜/镍/铬多层镀层一次退除的方法见表7-75。
表7-75 铜/镍/铬多层镀层一次退除的方法

①825添加剂是北京欣普雷技术开发有限公司的产品。
②W-710退除剂是武汉风帆电镀技术有限公司的产品。
③STR-710镀层电解退镀剂是广州美迪斯新材料有限公司的产品。