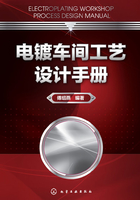
第2篇 电镀工艺
第5章 电镀前处理
5.1 电镀前处理方法
电镀、化学和电化学转化处理前,对零件表面进行清除油污、铁锈、氧化皮以及为适应镀覆层的特殊要求而对基体金属表面进行的特殊处理等任何准备工作,统称为电镀前处理。电镀前处理方法如图5-1所示。

图5-1 电镀前处理方法
5.2 机械前处理
机械前处理是以机械清理的方法,清理镀件表面的铁锈、氧化皮和缺陷,并赋予被镀零件表面平整、光亮及一定的粗糙度等性质的加工过程。机械前处理方法有喷砂、滚光、刷光、磨光、抛光、成批光饰等。
5.2.1 喷砂
电镀、化学和电化学转化处理工件的机械前处理,常采用喷砂。喷砂的种类和应用见表5-1。
表5-1 喷砂的种类和应用

喷砂用的磨料有钢砂、氧化铝、石英砂、河砂、碳化硅等,其中使用氧化铝砂较好,因其不易粉化,可改善操作人员的劳动条件。但现在生产中使用较多的仍然是石英砂,也用河砂。喷砂清理灰尘大,污染严重,应尽量采用其他工艺替代。喷砂清理尽可能采用湿喷砂。喷砂的工艺条件(即不同材料的零件与使用砂粒、压缩空气压力的关系)参见表5-2。
表5-2 零件材料与使用的砂粒大小、空气压力的关系

5.2.2 滚光和刷光
滚光和刷光的加工方法及应用见表5-3。
表5-3 滚光和刷光的加工方法及应用

表5-4 滚筒及滚光工艺条件

表5-5 湿法滚光溶液成分及工艺规范

表5-6 刷光轮金属丝的材料和直径

表5-7 刷光操作规范

5.2.3 磨光
磨光是借磨轮对金属制件进行抛磨,以提高制件表面平整度和光洁度的机械加工过程。钢铁件前处理一般只进行磨光(因钢铁件硬度高);而铜及铜合金、铝及铝合金等,磨光后常需要再进行抛光(因其表面硬度低,可以抛得很亮)。
(1)磨光轮及磨光的应用
磨光轮及磨光的应用见表5-8。
表5-8 磨光轮及磨光的应用

(2)磨光用的磨料
磨光用的磨料及其用途见表5-9。
表5-9 磨光用磨料及其用途

(3)磨光规范
①磨料粒度选择。磨料粒度直接影响生产效率、加工精度及表面粗糙度。除表面状态较好或质量要求不高的零件可一次磨光外,一般采用磨料颗粒逐渐减小的几次磨光。磨光一般分为粗磨、中磨和精磨,磨光的磨料粒度选用参见表5-10。
表5-10 磨光的磨料粒度选择

②磨光速度。磨光时采用的磨光轮圆周(线)速度,取决于金属材料、零件形状及表面状态等因素。一般情况下,零件形状简单或钢铁件粗磨时,采用较大的圆周速度;零件形状复杂或磨光有色金属及其合金时,采用较小的圆周速度。磨光不同材料适宜的磨轮圆周速度及允许的磨轮转速,如表5-11所示。
表5-11 磨光不同材料适宜的磨轮圆周速度及允许的磨轮转速

(4)磨光带磨光
①磨光带加工的优点
磨光带磨光也称带式磨光或砂带磨光。这种磨光是用磨光带作为磨光工具,把它安装在磨光带磨光机上,靠磨光带高速运行并与工件接触而进行磨削的加工方法。磨光带磨光可以部分替代磨光轮的磨光工序,与磨光轮相比,具有以下优点:生产效率高;磨光带磨削面积大,工作时冷却较快,工件变形可能性小;可对不同零件及复杂零件进行磨光;选用合成树脂胶黏剂粘接磨料的磨光带,可以带水湿磨等。磨光带磨光时也要添加润滑剂。润滑剂由动物油、脂肪酸和蜡制成,也可使用抛光膏。
②磨光带磨光参数的选择
使用磨光带磨光时,应根据材料种类、磨光类型选择磨光带的参数。磨光带磨光参数的选择见表5-12。
表5-12 磨光带磨光参数的选择

①为测量橡胶的钢轨硬度计的测量值。
5.2.4 抛光
机械抛光是借助高速旋转的抹有抛光膏的抛光轮抛磨,以提高金属制件表面平整度、光亮度的机械加工过理。抛光一般用于镀层的抛光,也可用于镀前的有色金属如铜及铜合金、铝及铝合金等的抛光(经过磨光后进行抛光)。抛光的分类、特点及其应用见表5-13。
表5-13 抛光的分类、特点及其应用

①抛光速度。即抛光轮圆周(线)速度,取决于被加工金属材料、零件形状及抛光要求等因素。抛光时抛光轮圆周速度及抛光轮转速参见表5-14。一般在粗抛时可选用较大的抛光轮圆周速度;精抛时可选用较小的抛光轮圆周速度。
表5-14 抛光不同金属材料适宜的圆周速度及抛光轮转速

②抛光膏。抛光轮上涂抛光膏的主要作用是增加其切削力。常用抛光膏颜色有棕黄色(俗称黄油)、白色(俗称白油)、绿色(俗称绿油)和红色(俗称红油)。常用抛光膏的成分和用途见表5-15。
表5-15 常用抛光膏的成分和用途

③抛光液。抛光液在室温条件下呈液态油状或水乳剂。构成组分中所有的磨料和润滑剂与固态的抛光膏相同,但胶黏剂不得用易燃的溶剂。其供料是连续不间断地少量添加,可减慢抛光轮的磨损速度;还由于其均匀喷注,不会在零件表面上留下过多的抛光液。但这种抛光液一般只适用于自动抛光机。
5.2.5 成批光饰
成批光饰是将被处理的零件与磨料、水或油和化学促进剂一起放入专用的容器内,通过容器的振动和旋转使零件与磨料进行摩擦,以达到去除毛刺、倒锐角、棱边倒圆、表面整平、降低粗糙度、提高零件表面光亮度、除锈和除油等表面精饰的加工过程。
成批光饰的特点是一次能处理很多小型零件,省工省时,质量稳定,成本较低。适合于多种形状的小型金属或非金属零件的光饰加工。成批光饰可以采用湿态加工和干态加工。根据光饰加工形式的不同,成批光饰可分为普通滚光(在本章滚光和刷光章节中介绍过)、振动光饰、离心光饰、离心盘光饰和旋转光饰等。
(1)光饰加工方法
光饰加工方法见表5-16,其中普通滚光已在本章滚光和刷光章节中介绍过。
表5-16 光饰加工方法

(2) 磨削介质[4]及其选择
成批光饰大都采用湿态加工,采用的磨削介质包括磨料、化学促进剂和水。有时也用干态加工,这时只用磨料。磨削介质及其选择见表5-17。
表5-17 磨削介质及其选择

5.3 除油
5.3.1 概述
除油是镀前处理的一项重要工序。在进行电镀、化学和电化学转化处理前,必须彻底清除零件表面的油污、固态及液态污垢,以保证镀覆层与零件基体金属的牢固结合,从而获得良好的镀覆层质量。
常用的油脂可分为皂化性油和非皂化性油两类。
常用除油方法的特点及适用范围,如表5-18所示。
表5-18 常用除油方法的特点及适用范围

5.3.2 有机溶剂除油
有机溶剂对各种油脂(皂化及非皂化性油)都有很强的溶解能力,如能溶解重质油、老化变质的油和抛光膏中的硬脂酸油脂,除油效率高、速度快。
常用的有机溶剂有:汽油、煤油、丙酮、甲苯、氯甲烷、氯乙烷、三氯乙烯、三氯乙烷和四氯化碳等。用的较多的是汽油。
近年来国内外对非溶剂型高效除油剂的开发取得了很大进展,为逐步取代有机溶剂除油创造了条件。有机溶剂除油方法的特点及适用范围见表5-19。
表5-19 有机溶剂除油方法的特点及适用范围

5.3.3 化学除油
化学除油包括有:碱溶液除油、乳化液除油、酸性溶液除油和表面活性剂除油、碱液除蜡等。
(1)碱溶液除油
常用的碱溶液除油的溶液组成及工艺规范见表5-20。
表5-20 常用的碱溶液除油的溶液组成及工艺规范

注:1.YC除油剂为非离子型和阴离子型的混合型除油添加剂。
2.除油依据零件表面油脂、污物情况,除净为止。
(2)乳化液除油及酸性溶液除油
乳化液除油是用含有有机溶剂、水和乳化剂(搅拌均匀后)的液体,去除制件表面油污的过程。该方法有较强的除油能力,除油速度快、效果好,能除去重油脂、黄油、抛光膏等。但乳化液除油只能除脱重油,除油不够彻底,电镀前还需再进行电化学除油。
酸性溶液除油是在硫酸或盐酸溶液中加入适量合适的表面活性剂组成的酸性除油溶液,习惯称为“二合一”除油除锈处理。
乳化液除油及酸性溶液除油的溶液组成及工艺规范见表5-21。
表5-21 乳化液除油及酸性溶液除油的溶液组成及工艺规范

注:PC-2铁件除油除锈剂、NA-1常温酸洗除油添加剂、PC-3铜件除油除锈剂是上海永生助剂厂的产品。
市售的酸性清洗剂(适用于钢铁件的除油除锈“二合一”)见表5-22。
表5-22 市售的酸性清洗剂(适用于钢铁件的除油除锈“二合一”)

(3)表面活性剂除油
表面活性剂除油是用含有表面活性剂、碱性盐、助剂和水等组成的液体除去零件表面油污的过程。是用多种表面活性剂复配在一起,而配制成的新型除油溶液,其特点是除油速度快,效果好。水基金属清洗剂除油,就是表面活性剂除油的一种。表面活性剂具有良好的润湿、渗透、乳化、加溶、分散等性能,利用这些特性能有效地除去油污。因而,这类清洗剂清洗是目前广泛应用的一种除油方法。
市售金属清洗剂牌号很多,部分市售的金属清洗剂、脱脂剂列入表5-23内。
表5-23 市售的金属清洗剂、脱脂剂

注:PK、SP为沈阳帕卡濑精有限公司产品。
(4)碱液除蜡
当零件进行磨光、抛光时,因摩擦而产生大量的热,导致抛光膏十分牢固地黏附在零件表面上,而蜡(如石蜡、地蜡、白蜡、羊毛脂蜡等)是抛光膏的主要成分之一。黏附抛光膏的残余物,仅使用有机溶剂、碱液化学的方法很难将其彻底清除。因此,在磨光、抛光后,除油工序前先进行除蜡。除蜡溶液大多可从市场上购买除蜡剂(除蜡水),加水配制而成。除蜡溶液组成及工艺规范见表5-24。
表5-24 除蜡溶液的组成及工艺规范

5.3.4 电化学除油
(1)电化学除油方法和特点
电化学除油特点是除油彻底、效率高,一般作为零件的最终除油。
电化学除油方法的特点和适用范围见表5-25。
表5-25 电化学除油方法的特点和适用范围

(2)电化学除油溶液组成及工艺规范
常用电化学除油溶液组成及工艺规范见表5-26。
表5-26 常用的电化学除油溶液组成及工艺规范

注:YC除油剂为非离子型和阴离子型的混合型除油添加剂。
5.3.5 超声波清洗除油
超声波清洗除油,是用超声波作用于除油清洗溶液,以更有效地除去制件表面油污及其他杂质的方法。它是将振荡的超声波场引入化学除油溶液中,由于超声波振荡所产生的机械能,可使溶液内产生大量真空的空穴,而这些真空的空穴在形成和闭合时,能使溶液产生强烈的振荡,从而对零件表面的油污产生强有力的冲击作用,强化了除油过程,可缩短除油时间,降低除油溶液的浓度和温度。
超声波清洗除油特点及适用范围如表5-27所示。
表5-27 超声波清洗除油特点及适用范围

5.3.6 擦拭除油和滚筒除油
擦拭除油和滚筒除油的工作方法、特点及适用范围见表5-28。
表5-28 擦拭除油和滚筒除油的工作方法、特点及适用范围

5.4 浸蚀
5.4.1 概述
浸蚀也称为酸洗,是将金属零件浸在一定浓度和一定温度的浸蚀液中,以除去其上的氧化物和锈蚀物等的过程。
不锈钢、铝及铝合金、锌及锌合金等零件的浸蚀工艺,将在本篇第11章特种材料上电镀的各有关章节中加以介绍。浸蚀可按其性质和用途、浸蚀处理方法等分类。浸蚀的分类和对浸蚀的要求见表5-29。
表5-29 浸蚀的分类和对浸蚀的要求

5.4.2 钢铁零件的化学浸蚀
钢铁零件容易被氧化和腐蚀,其表面一般都存在氧化皮和铁锈。常见的氧化物有灰色的氧化亚铁(FeO)、赤色的三氧化二铁(Fe2O3)、橙黄色含水的三氧化二铁(Fe2O3·nH2O)和蓝黑色的四氧化三铁(Fe3O4)等。
钢铁零件因大气腐蚀产生的锈蚀,一般是氧化亚铁和氢氧化铁。铁的氧化物、氢氧化物与酸作用都容易被溶解而去除。
钢铁零件常用的化学浸蚀溶液的组成和工艺规范见表5-30。
表5-30 钢铁零件常用的化学浸蚀溶液的组成和工艺规范

注:1.溶液成分中的d为密度,单位为g/cm3,例如硫酸(H2SO4)d=1.84,即d=1.84 g/cm3,下同。
2. YS-1添加剂是上海永生助剂厂的产品。
3.表中浓度含量的百分数(%)为质量分数。
5.4.3 铜及铜合金零件的化学浸蚀
铜及铜合金零件的化学浸蚀,一般情况下要进行两道连续的浸蚀工序,即先进行一般浸蚀(预浸蚀),后进行光亮浸蚀。当铜及铜合金件表面有厚的黑色氧化皮时,在预浸蚀前,可在10%~20%(质量分数)硫酸溶液中(50~60℃)进行疏松氧化处理。经过机械抛光的铜及铜合金件,一般只需弱浸蚀即可。
铜及铜合金零件化学浸蚀溶液的组成和工艺规范见表5-31。
表5-31 铜及铜合金零件化学浸蚀溶液的组成和工艺规范

注:1.在一般浸蚀(预浸蚀)中,也可采用盐酸(HCl)100~360g/L,室温。
2.表中浓度的百分数(%)均为体积分数。
3.浸蚀时间依据零件表面氧化皮状态而定,除净为止。
5.4.4 其他金属零件的化学浸蚀
镉、锡、镍及其合金件化学浸蚀溶液的组成及工艺规范见表5-32。
表5-32 镉、锡、镍及其合金件化学浸蚀溶液的组成及工艺规范

注:镍(配方1)经过浸蚀后,接着在硫酸200g/L、铬酐20~30g/L,60~80℃的溶液中进行光亮浸蚀。
铅、钛、钼、钨及其合金件化学浸蚀溶液的组成及工艺规范见表5-33。
表5-33 铅、钛、钼、钨及其合金件化学浸蚀溶液的组成及工艺规范

5.4.5 电化学浸蚀
电化学浸蚀也称为电解浸蚀(或电解酸洗)。即将金属制件作为阳极或阴极在电解质溶液中进行电解以清除制件表面氧化物和锈蚀的过程。
电化学浸蚀通常用于有较厚氧化皮或较致密氧化皮的钢铁零件。电化学浸蚀的特点如下。
①优点:浸蚀能力强,速度快,生产效率高,浸蚀溶液消耗量少,而且使用寿命较长;电解液浸蚀能力受溶液中铁含量影响小。
②缺点:电解液分散能力较低;形状复杂的零件不宜使用;零件装挂比较麻烦,且装载量少于化学浸蚀。
电解浸蚀方法的特点及适用范围见表5-34。
表5-34 电解浸蚀方法的特点及适用范围

钢铁件及不锈钢件电解浸蚀溶液的组成及工艺规范见表5-35。
表5-35 钢铁件及不锈钢件电解浸蚀溶液的组成及工艺规范

注:1.表中溶液浓度百分含量(%)为质量分数。
2.阴极电解浸蚀配方1适用于非弹性、非高强度零件,浸蚀后的零件,需在氢氧化钠(85g/L)、磷酸钠(30g/L)的溶液中进行阳极去铅膜,阳极电流密度为5~8A/dm2,温度50~60℃,时间8~12min,阴极材料为铁板。
3.阴极电解浸蚀配方3为镀前弱浸蚀溶液。
4.为了防止零件的过浸蚀,可向阳极电解浸蚀和阴极电解浸蚀溶液中添加缓蚀剂。
5.对于形状复杂而几何尺寸要求较严格的零件,为防止过浸蚀又减小氢脆,可采联合电解浸蚀,先进行阴极电解浸蚀,后进行短时间的阳极电解浸蚀。
6.不锈钢电解浸蚀配方2,用于电镀前的预处理阴极活化。石墨阳极必须套上阳极套。
钛、钨、镍等金属及其合金电解浸蚀溶液的组成及工艺规范见表5-36。
表5-36 钛、钨、镍等金属及其合金电解浸蚀溶液的组成及工艺规范

注:1.钛及其合金的配方1的操作方法:先用化学浸蚀10~15min,再进行交流电浸蚀。用于纯钛,后续镀铬。
2.钛及其合金的配方2的操作方法:先用化学浸蚀10~15min,再进行交流电浸蚀。用于6Al-4V钛合金,后续镀镍、铬。
3.钨及其合金的配方1,处理后需在100g/L的硫酸溶液中浸10min。
4.镍及其合金的配方2的操作方法:先在2 A/dm2下阳极浸蚀10min,再在20A/dm2下钝化2min,最后在20A/dm2下阴极活化2~3s,这种处理方法结合力好。
5.5 去接触铜、除浸蚀残渣
钢铁件去接触铜及除浸蚀残渣溶液的组成及工艺规范见表5-37。
表5-37 钢铁件去接触铜及除浸蚀残渣溶液的组成及工艺规范

5.6 工序间防锈
工序间防锈处理,是对经过除油除锈后,不能立即进行电镀或化学和电化学转化处理的零件,提供短时间工序间的防锈。工序间防锈溶液的组成及工艺规范见表5-38。
表5-38 工序间防锈溶液的组成及工艺规范

5.7 化学抛光
化学抛光,是金属零件在一定的溶液中和特定的条件下进行化学浸蚀处理,以获得平整、光亮表面的处理过程。
金属的化学抛光适用范围很广,如钢铁(包括不锈钢)、铜和铜合金、铝和铝合金、镍、锌、镉以及其他金属等的化学抛光。
5.7.1 钢铁件的化学抛光
钢铁件化学抛光溶液的组成及工艺规范见表5-39。
表5-39 钢铁件化学抛光溶液的组成及工艺规范

注:1.表中溶液浓度百分含量(%)为体积分数。
2.表中低、中碳钢和低合金钢的化学抛光,抛光前的零件,必须在干燥并加热至同溶液温度接近后再进槽。
3.润湿剂:低、中碳钢可用6501、6504洗净剂或聚乙二醇等;高碳钢配方采用海鸥洗涤剂。
4.高碳钢化学抛光配方,工作时温度会升高,应进行冷却。
5.7.2 不锈钢件的化学抛光
不锈钢如要达到镜面光亮,就需要机械抛光。但大多数不锈钢不需要镜面光亮,只要一般光亮就行,这样采用化学抛光或电化学抛光方法就能达到。常用的化学抛光溶液的组成及工艺规范见表5-40。
表5-40 不锈钢件化学抛光溶液的组成及工艺规范

注:1.配方1中的添加剂:复合缓蚀剂采用若丁和有机胺等;光亮剂采用氯烷基吡啶、卤素化合物和磺基水杨酸;水溶性聚合物为黏度调节剂,采用纤维素醚和聚乙二醇的混合物等。
2.配方1抛光时要抖动零件,避免气泡在表面停滞。加入适量甘油,可改善抛光质量。
3.硝酸型溶液的抛光作用较强,其缺点是有大量氮氧化物(黄烟)产生。
由于不锈钢牌号很多,其含镍、铬、钛等成分不一样,因此究竟选用何种溶液配方,需先作小样试验来确定。
5.7.3 铜及铜合金件的化学抛光
铜及铜合金件化学抛光溶液的组成及工艺规范见表5-41。
表5-41 铜及铜合金件化学抛光溶液的组成及工艺规范

注:1.配方1、2适用于铜和黄铜的抛光。配方1的温度降至20℃时,可以抛光白铜。
2.配方3的酸含量低,适用于铜及黄铜的抛光,当温度降至20℃时,可用于抛光白铜。
3.配方4适用于抛光精密、表面粗糙度低的零件。
4.配方5适用于铜铁组合体的抛光。
5.7.4 铝及铝合金件的化学抛光
铝及铝合金件的化学抛光溶液有两种类型,即酸性抛光溶液和碱性抛光溶液,其性能如表5-42所示。
表5-42 铝及铝合金件的化学抛光溶液类型及其性能

铝及铝合金件的化学抛光溶液的组成及工艺规范见表5-43。
表5-43 铝及铝合金件的化学抛光溶液的组成及工艺规范

注:1.配方1适用于纯铝和含铜量较低的铝合金。
2.配方2不含硝酸的抛光溶液,适用于6063及6061等型号的铝型材抛光。磷酸、硫酸的含量应为:磷酸(85%)∶硫酸(95%~98%)=70∶25(质量比)。WP-98添加剂由武汉材料保护研究所研制。
3.配方3适用于纯铝和铝镁合金。
4.配方4适用于含铜、锌较高的高强度铝合金。
5.配方5适用于铝锌镁合金、铝镁铜合金、含锌不超过7%含铜不超过5%的其他铝合金。
6.配方6适用于含硅大于2%的铝合金、高纯铝。
7.配方7对于1060纯铝和5356铝镁合金有很好的抛光效果,对铝的腐蚀量比含硝酸的配方碱少2/3。AP-1无黄烟添加剂(抛光剂)是上海永生助剂厂的产品。
8.碱性抛光溶液,应注意防止过腐蚀。碱性化学抛光后应迅速在50℃左右的温水清洗,清洗后再用250~300mL/L的硝酸溶液进行中和出光,在室温下,处理10~30s,经水洗后,进入下一道工序。
9.经含有铜离子抛光溶液抛光过的零件,应在400~500g/L的硝酸溶液中,在室温下浸渍数秒至十多秒,以除去表面的接触铜。
5.7.5 其他金属件的化学抛光
其他金属件的化学抛光溶液的组成及工艺规范见表5-44。
表5-44 其他金属件的化学抛光溶液的组成及工艺规范

注:镍的配方2适用于镍镀层的抛光。含量百分数(%)为体积分数。
5.8 电化学抛光
电化学抛光在一些场合下,虽然可以用来代替机械抛光,尤其是对形状比较复杂的零件,但是,电化学抛光方法不能去除或掩饰粗糙度较大、深划痕、深麻点等表面缺陷。同机械抛光相比,电化学抛光具有的特点如表5-45所示。
表5-45 电化学抛光与机械抛光的特点比较

5.8.1 钢铁件的电化学抛光
钢铁件的电化学抛光溶液的组成及工艺规范见表5-46。
表5-46 钢铁件的电化学抛光溶液的组成及工艺规范

注:阴极材料为铅。
5.8.2 不锈钢件的电化学抛光
不锈钢件的电化学抛光,一般在化学抛光后直接进行。大多不锈钢件只要一般光亮就行,这时选用化学抛光或电化学抛光就能达到。如要求镜面光亮的零件,应先进行机械抛光然后再进行电化学抛光。
不锈钢件电化学抛光溶液的组成及工艺规范见表5-47。
表5-47 不锈钢件电化学抛光溶液的组成及工艺规范

5.8.3 铜及铜合金件的电化学抛光
目前常用的铜及铜合金件的电化学抛光溶液,基本上是以磷酸为基型的溶液,其溶液的组成及工艺规范[4]见表5-48。
表5-48 铜及铜合金件的电化学抛光溶液的组成及工艺规范

注:1.配方1适用于纯铜或黄铜、铝青铜、锡青铜、磷青铜,以及铍、铁、硅或钴的含量低于3%(质量分数)的青铜。
2.配方2适用于纯铜或黄铜。
3.配方3适用于纯铜和含锡量低于6%(质量分数)的铜合金。
4.配方4适用于含锡量大于6%(质量分数)的铜合金。
5.配方5适用于含铅量高达30%(质量分数)的铜合金。
6.配方6适用于纯铜、黄铜件、板材、线材。添加剂中含有两种以上的有机酸,可加速铜的溶解,加快抛光速度,改善抛光质量,可达全光亮效果。
5.8.4 铝及铝合金件的电化学抛光
铝及铝合金件电化学抛光溶液有两种类型,即酸性电化学抛光溶液及碱性电化学抛光溶液。其性能如表5-49所示。抛光溶液的组成及工艺规范见表5-50。
表5-49 铝及铝合金件的电化学抛光溶液类型及其性能

表5-50 铝及铝合金件电化学抛光溶液的组成及工艺规范

注:1.配方1适用于纯铝、铝镁合金、铝镁硅合金。搅拌溶液或阴极移动。
2.配方2适用于纯铝、铝镁合金、铝锰合金。
3.配方3适用于纯铝、铝铜合金。
4.配方4适用于含铜3%铝铜合金、含镁1.5%铝镁合金、含镍1%铝镍合金、含铁1%铝铁合金。
5.配方5适用于含硅的压铸件。抛光后先在5%(质量分数)NaOH溶液中浸5min后再清洗,以防光亮度降低。
6.铝及铝合金件电化学抛光时,一般情况下需要搅拌溶液或阳极移动。
7.碱性电化学抛光后要进行去膜处理,否则将影响氧化膜的透明度。去膜溶液组成及操作条件如下:磷酸(H3PO4)30mg/L,铬酐(CrO3)10g/L;温度80~90℃;时间0.5~1.5min。
8.表中的百分数均为质量分数。