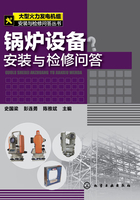
第一章 超(超)临界锅炉设备特点
第一节 大型电站锅炉机组技术特点
1-1 什么是超临界锅炉?
答:水的临界状态参数为22.115MPa,374.15℃,在水的参数达到该临界点时,水的完全汽化会在一瞬间完成,即在临界点时,在饱和水和饱和蒸汽之间不再有汽、水共存的二相区存在,二者参数不再有分别。当锅炉参数高于这一临界状态参数时,通常称其为超临界锅炉。
1-2 哈尔滨锅炉厂660WM超临界锅炉的概况是什么?
答:锅炉采用全钢结构构架,高强螺栓连接。锅炉呈“П”型布置方式,设计有固定的膨胀中心,受热面采用全悬吊结构。炉膛上部布置有屏式过热器。水平烟道中布置有末级过热器、末级再热器。尾部为双烟道,前烟道布置有低温再热器和省煤器,后烟道布置水平低温过热器和省煤器,水平低温过热器和再热器采用水冷吊挂结构。后烟道下部布置有两台三分仓回转式空气预热器。
炉膛中间集箱以下采用螺旋水冷壁、以上为垂直膜式水冷壁。顶部受热面各部分间采用大口径连接管连接。
锅炉燃烧器采用墙式切圆燃烧方式,形成大直径切圆,以获得沿炉膛水平断面较为均匀的空气动力场。主燃烧器采用低NOx的水平浓淡燃烧器,主燃烧器二次风偏离一次风5°进入炉膛,形成风包粉的布置方式,有效减少炉膛的结焦。主燃烧器的上方为(SOFA)喷嘴,它具有补充燃料后期燃烧所需要的空气,同时实现分级燃烧抑制NOx的生成的低NOx燃烧系统。
燃烧器采用大风箱结构。主燃烧器采用固定式,共设六层水平浓淡煤粉一次风喷口,四层油风室,四层分离型燃烬风室和八层辅助风室。其中分离型燃烬风室(SOFA)采用手动水平摆动形式,用于调节炉膛出口处烟温偏差。燃烧器采用单元制配风。整个燃烧器同水冷壁固定连接,随水冷壁一起向下膨胀。
锅炉采用两套供油系统,锅炉共16只油枪,分四层布置,第一层为轻油,每只油枪配有高能点火器,采用两级点火,即高能点火器点燃轻油,轻油点燃煤粉;另外三层为重油。
锅炉调温方式,过热蒸汽主要靠调节煤水比和一、二级喷水减温器调温。再热蒸汽主要靠烟气挡板调温,在再热器进口导管上装有两只喷水减温器,主要用作事故喷水。
1-3 二次再热机组相对一次再热机组的特点是什么?
答:采用二次再热可使机组的热效率提高1%~2%,但也造成了调温方式、受热面布置、结构等的复杂性,成本明显提高。
1-4 超超临界压力锅炉的发展情况是什么?
答:世界上第一台试验性的超临界锅炉是西门子公司制造的。1949年原苏联安装了第一台超超临界试验机组,直流锅炉出口参数为29.4MPa、600℃(12t/h),经节流至15MPa后通入汽轮机,以后又生产了29.4MPa、650℃型号为P-100-300的100MW机组,作为改造中压机组的前置级。1956年联邦德国投运1台参数为34MPa、610℃/570℃/570℃、容量为88MW的机组。
美国在20世纪50年代末投运了2台具有代表性的超超临界机组,菲罗电厂6号机组,容量为125MW、参数为31MPa、621℃/566℃/538℃;艾迪斯顿电厂1号机组,参数为34.3MPa、649℃/566℃/566℃、容量为325MW。费城电力公司的这台艾迪斯顿1号机从1960年开始按设计参数运行8年,后因出现一些故障,主要是材料问题,1968年起参数降为31MPa、610℃/557℃/557℃。美国一开始就试制这样高参数的超超临界机组,不可避免地频繁发生事故,故不得不降低参数运行。在开发初期,过高的蒸汽参数超越了当时的技术水平。以后将蒸汽降至24.1MPa、538~566℃,并逐步完善,这种蒸汽参数保持了20余年。
日本引进美国的技术并结合欧洲的适合变压运行的本生式直流炉,成功地开发了超超临界机组。在1989年和1991年成功地投运2台700MW、31MPa、566℃/566℃/566℃的机组,运行情况良好,可用率水平很高。1998年投运主蒸汽和再热蒸汽温度均为600℃的原町2号1000MW机组,该机组实测发电机端效率达44.7%。
欧洲在1995~1999年间至少投运9台蒸汽压力28.5~31.0MPa、温度545~587℃的超超临界机组,在建的还有10台,并将蒸汽温度提高至600℃以上。其中丹麦已投运的2台超超临界机组的热效率可达47%~49%。
我国2007年华能玉环电厂由哈尔滨锅炉厂引进日本三菱(MHI)技术生产的1000MW机组超超临界直流锅炉投入商业运行,过热蒸汽流量上2952.54t/h;过热蒸汽压力是27.46MPa;过热蒸汽温度为605℃。
1-5 超超临界压力锅炉的关键技术是什么?
答:由于采用超临界参数,对机组的设计、制造和运行等方面提出了更高的要求和标准,当然也就带来了一些新的问题,需要在技术上进一步开展试验和研究工作。在这些问题中,有些是属于超临界机组本身所特有的技术问题,如超临界参数下部件的材料特性问题,工质流体热物性的变化对锅炉传热、水动力、热偏差和动态特性的影响分析,汽机缸体结构设计与转子的冷却技术等;有些是属于火电技术在持续发展和技术进步过程中的一些共性问题,如机组轴系稳定性研究,叶片固体颗粒侵蚀的技术问题,汽轮机末级长叶片的开发设计技术等等,而还有些则是国产化条件下所需要解决的技术问题。此外,如果对于更大容量的超临界机组,还需要解决机组大型化而带来的技术问题,同时也要在发电机的设计、制造和大件运输等方面相应开展一系列的技术攻关工作。
1-6 超超临界压力锅炉的关键技术中,材料选择的内容是什么?
答:早期的超超临界锅炉使用了大量的奥氏体钢,而奥氏体钢比铁素体钢具有高的热强性,但热膨胀系数大、导热性小,抗应力腐蚀能力低、工艺性差,热疲劳和低周疲劳性能(特别是厚壁件)也比不上铁素体钢,且成本高得多,出现许多奥氏体钢制部件损伤事故。世界各国一直致力于开发新材料和新工艺,改进和开发新型铁素体钢和改进了奥氏体耐热钢。最近几十年的研究集中于开发能够替代奥氏体钢的低成本高强度铁素体钢,并已经开发了具有良好焊接性能和断裂韧性且能够用于620℃的铁素体钢。
①在铁素体钢基础上发展起来的新钢种能很好地应用在蒸汽温度在538℃/17MPa条件下。
②锅炉管道和联箱用钢需要高蠕变强度。基于这个原因,发展合金集中于含Cr 9%~12%的铁素体钢。在含Cr 9%~12%的铁素体钢中加入Nb、Mo、V、W等产生了3种新型合金P92、P122和E911,能够工作在620℃/34MPa条件下。含Co和W的12%Cr新型钢种NF12和SAVE12可能能应用650℃下。初步研究表明,温度超过650℃,可能需要奥氏体钢或者镍基合金。
③过热器和再热器管,蒸汽侧抗氧化能力和向火侧抗腐蚀能力是主要的。在温度超过565℃高温时就需要奥氏体钢。根据煤种不同,可能需要高Cr钢和镀层钢。对于620℃,在无腐蚀条件下可以采用Super 304H,AA1,17CW-MO;但在腐蚀条件下,就需要20%~25% Cr钢,如HR3C、NF709和镀IN72合金。另外几种合金Inconel671、NF709、Cr30A和镀Inconel671(50%)合金可以用于650℃。
④对于水冷壁部分,根据蠕变强度和焊接性可以采用两种含Cr2.5%和Cr12%的T23和HCM12合金。纯粹从蠕变强度考虑,它们可以用于595~650℃范围内;当某些锅炉含NOx较低,存在向火侧腐蚀时,这些合金就必须进行镀层,或用Cr18%~20%合金表面涂层。
1-7 超超临界压力锅炉的关键技术中,水冷壁设计的关注点是什么?
答:超超临界压力锅炉的水冷壁系统,主要集中在螺旋管圈水冷壁和由内螺纹管组成的垂直管圈两种形式。螺旋管圈水冷壁可以自由地选择管子的尺寸和数量,因而能选择较大的管径和保证水冷壁安全的质量流速,管圈中的每根管子均同样地绕过炉膛和各个壁面,因而每根管子的吸热相同,管间的热偏差最小,适用于变压运行,其缺点是螺旋管圈的制造安装支承等工艺较为复杂及流动阻力大。内螺纹管的垂直管圈水冷壁受炉膛沿周界热负荷偏差的影响较大,除了需要采取一定的结构措施(例如加装节流装置)使管内工质流量的分配与管外热负荷的分布相适应外,还要求较高的运行操作水平和自动控制水平。在开发超超临界压力机组时,有必要在现有的超临界压力水冷壁内沸腾传热研究的基础上,扩展实验研究的压力范围,进一步进行试验研究,防止似膜态沸腾现象,确保水冷壁系统工作的安全性。
1-8 直流锅炉的工作原理是什么?
答:直流锅炉是指靠给水泵压力,使给水顺序通过省煤器、蒸发受热面(水冷壁)、过热器并全部变为过热水蒸气的锅炉。由于给水在进入锅炉后,水的加热、蒸发和水蒸气的过热,都是在受热面中连续进行的,不需要在加热中途进行汽水分离。因此,它没有自然循环锅炉的汽包。在省煤器受热面、蒸发受热面和过热器受热面之间没有固定的分界点,随锅炉负荷变动而变动。
直流锅炉的主要优点是它可用于一切压力,特别是在临界压力及以上压力范围内广泛应用。由于它没有汽包,因此,加工制造方便,金属消耗量小;水冷壁布置比较自由,不受水循环限制;调节反应快,负荷变化灵活;启、停迅速;最低负荷通常低于汽包锅炉。但对给水品质和自动调节要求高,汽水系统阻力大,给水泵的耗电量较大。
1-9 直流锅炉的特点是什么?
答:直流锅炉没有汽包,启停速度较快。与自然循环锅炉相比,直流炉从冷态启动到满负荷运行,变负荷速度可提高一倍左右。直流锅炉适用于亚临界和超临界以及超超临界压力锅炉。直流锅炉的锅炉本体金属消耗量最少,锅炉质量轻。一台300MW自然循环锅炉的金属质量约为5500~7200t,相同等级的直流炉的金属质量仅有4500~5680t,一台直流锅炉大约可节省金属2000t。加上省去了汽包的制造工艺,使锅炉制造成本降低。
直流锅炉水冷壁的流动阻力全部要靠给水泵来克服,这部分阻力约占全部阻力的25%~30%。所需的给水泵压头高。直流锅炉启动时约有30%额定流量的工质经过水冷壁并被加热,为了回收启动过程的工质和热量,并保证低负荷运行时水冷壁管内有足够的重量流速,直流锅炉需要设置专门的启动系统,而且需要设置过热器的高压旁路系统和再热器的低压旁路系统。直流锅炉的参数比较高,需要的金属材料档次相应要提高,其总成本不低于自然循环锅炉。系统中的汽水分离器在低负荷时起汽水分离作用并维持一定的水位,在高负荷时切换为纯直流运行,汽水分离器作为通流承压部件。为了达到较高的重量流速,必须采用小管径水冷壁。这样提高了传热能力而且节省了金属,减轻了炉墙质量,同时减小了锅炉的热惯性。
直流锅炉水冷壁的金属储热量和工质储热量小,即热惯性小,使快速启停的能力进一步提高,适用机组调峰的要求。但热惯性小也会带来问题,它使水冷壁对热偏差的敏感性增强。当煤质变化或炉内火焰偏斜时,各管屏的热偏差增大,由此引起各管屏出口工质参数产生较大偏差,进而导致工质流动不稳定或管子超温。
为保证足够的冷却能力和防止低负荷下发生水动力多值性以及脉动,水冷壁管内工质的质量流速在MCR负荷时提高到2000kg/(m2·s)以上。加上管径减小的影响,使直流锅炉的流动阻力显著提高。600MW以上的直流锅炉的流动阻力一般为5.4~6.0MPa。汽温调节的主要方式是调节燃料量与给水量之比,辅助手段是喷水减温或烟气侧调节。由于没有固定的汽水分界面,随着给水流量和燃料量的变化,受热面的省煤段、蒸发段和过热段长度发生变化,汽温随着发生变化,汽温调节比较困难。
低负荷运行时,给水流量和压力降低,受热面入口的工质欠焓增大,容易发生水动力不稳定。由于给水流量降低,水冷壁流量分配不均匀性增大;压力降低,汽水比容变化增大;工质欠焓增大,会使蒸发段和省煤段的阻力比值发生变化。水冷壁可灵活布置,可采用螺旋管圈或垂直管屏水冷壁。采用螺旋管圈水冷壁有利于实现变压运行。超临界压力直流锅炉水冷壁管内工质温度随吸热量而变,即管壁温度随吸热量而变。因此,热偏差对水冷壁管壁温度的影响作用显著增大。
变压运行的超临界参数直流炉,在亚临界压力范围和超临界压力范围内工作时,都存在工质的热膨胀现象。并且在亚临界压力范围内可能出现膜态沸腾;在超临界压力范围内可能出现类膜态沸腾。启停速度和变负荷速度受过热器出口集箱的热应力限制,但主要限制因素是汽轮机的热应力和胀差。直流锅炉要求的给水品质高,要求凝结水进行100%的除盐处理。控制系统复杂,调节装置的费用较高。
1-10 直流锅炉启动系统的特点是什么?
答:锅炉启动系统是直流锅炉特有的辅助系统,其主要功能是:在锅炉启动、停炉和最低直流负荷以下运行期间避免过热器进水,为水冷壁的安全运行提供足够高的工质质量流速和尽可能回收工质及其所含的热量,使启动更容易。
直流锅炉启动系统由汽水分离系统和热量回收系统两部分组成。现代变压运行超临界直流锅炉毫无例外地都采用内置式分离器启动系统。所谓内置式,系指自锅炉点火至正常运行期间,分离器始终接入汽水系统。在最低直流负荷以下,分离器呈湿态运行,在最低直流负荷以上转为干态运行,此时汽水分离器仅作为蒸汽通道使用。
作为内置式分离器启动系统,依据疏水能量回收方式的不同,可以分成:大气扩容器、启动疏水热交换器和再循环泵方式三种。三种启动系统各有优点:大气扩容器式系统简单,投资小,但能量回收较差,如图1-1所示;启动疏水热交换器(如图1-2所示)和再循环泵方式(如图1-3所示),系统较复杂,投资大,但能量回收较好。

图1-1 大气扩容式启动系统

图1-2 带疏水热交换器的启动系统

图1-3 带循环泵的启动系统