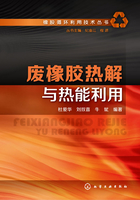
3.1 废轮胎的热解技术
废轮胎热解有很多方法,如真空热解、催化热解、煤共热解、等离子体热解等,各种热解方式一般都有其特定的目的,即主要回收热解产物中的某种主要物质,下面将介绍几种常见的废轮胎热解技术。
3.1.1 常压热解
常压热解是目前应用最多的废轮胎热解方式,其示意图如图3-2所示。常压热解压力容易控制、设备简单、操作简便、安全系数高,国内外规模较大的废轮胎热解装置都在常压环境下运行。废轮胎的常压热解一般分为有载气(N2等)和无载气两种情况,热解在缺氧或无氧环境中于高温条件下进行,热解产物因热解温度和气氛的不同而不同。

图3-2 常压惰性气体热解示意图
William、Berrueco等研究了在静态分批式反应器中N2氛围下废轮胎的常压热解,在热解温度为300~720℃、加热速率为5~80℃/min的条件下,热解产物的组成与特性取决于热解温度,在热解温度为600℃时,获得了质量分数为55%的衍生油、10%热解气和35%炭黑,同时发现随着热解温度的升高,热解油品中芳烃的含量有上升的趋势。
Wey等以空气为载气,在流化床内进行废轮胎热解,并控制空气分率使轮胎部分氧化,以达到维持自热的目的,研究表明,当空气分率为0.21、温度为570℃时,可以得到质量分数为39.3%的汽油、35%的柴油、7.5%的燃料油和8.9%的重油。
GOTSHALL公司发明了无氧高温热解制取炭黑的方法。900℃时,轮胎橡胶转化率为55%,低温时转化率大约有30%。高温热解得到的炭黑质量好,费尔斯通轮胎公司的研究显示,废轮胎在500~900℃热解,液体产物的最高收率在500℃、气体产物收率在900℃达到最大。
3.1.2 真空热解
热解在减压条件下进行,有机挥发物在反应器中停留的时间短,副反应少,故收率高于常压热解法,其示意图见图3-3。此外,芳烃化合物的收率高,经济收益好。此法是由加拿大的C.Roy等人提出并开发的。Chaala等研究了在真空条件下的废轮胎热解情况,在温度480~500℃、绝对压力20kPa的条件下,采用长3m、直径0.6m的水平管式反应器,经过热解反应得到了质量分数为54%的热解油、26%的炭黑、11%热解气和9%的钢丝。但相对于常压热解,真空热解回收的炭黑表面碳质沉积物较少,从而提高了炭黑的表面活性。

图3-3 真空热解示意图
采用该技术商业化的装置中以熔融盐为传热介质,采用卧式双层加热盘片结构,安装较方便,且对密封要求低,较易实现真空操作。该热解过程在480~520℃、低于10kPa下进行。破碎的废轮胎在真空状态下进入反应器。轮胎碎片在机械驱动下通过两层水平加热盘(经过不同温度的熔融盐预先加热),并在其上热分解产生烃类化合物。熔融盐的整体温度比热解物料高约30℃。反应产生的高温蒸汽通过真空泵从反应区迅速抽出,经过两级冷凝器后得到轻油、重油及不凝可燃气。
加拿大的C.Roy等在绝对压力2kPa、温度415℃条件下热解废轮胎得到了55%的油品、39%的固体和6%的气体。该热解油的相对密度为0.95,总热值43MJ/kg,总硫量为0.8%,热解油中富含苯及其他组分。美国的Garb-oil公司采用真空热解,温度为650~925℃,每天可处理9000条轮胎,得到55t原油,11.4t钢和28.6t炭黑。
据文献报道,真空热解的条件为温度在520℃左右,系统的压力维持在3500~4000Pa之间,可使废轮胎基本裂解完全。真空热解技术与常压热解技术相比具有许多优势:首先,真空热解的温度低,热解初级产品在反应器中的停留时间短,减少了副反应(热解炭黑表面碳质沉积物的生成、柠檬油精等的二次热解等)发生的可能性;其次是真空热解油品的收率高;三是真空热解油品中含有较多的芳烃化合物,有利于提高热解油品的辛烷值;四是真空热解得到的炭黑表面碳质沉积物比常压热解炭黑少,化学性质与轮胎用商业炭黑更接近。
3.1.3 超临界热解
近年来,利用超临界流体对废轮胎进行热解研究已经引起了研究者的重视。超临界流体因温度压力均在其临界点之上,具有很高的溶解能力和流动、传递性能等特点。Kershaw等尝试了超临界状态下废轮胎的萃取过程,将超临界反应在400mL的高压釜内进行,加热速率为70℃/min,试验了乙醇、丙酮、甲苯、正丁醇等不同超临界流体存在下废轮胎萃取反应的变化,结果表明不同溶剂及不同萃取温度是影响产品产率的主要因素,其中萃取液为甲苯、温度分别为350℃和380℃时,产率分别高达66%和67%。杜昭辉等以水为介质,在温度为450℃下进行废橡胶超临界裂解,得出废橡胶超临界水裂解的反应时间为5min,混合油收率高达59.20%。刘银秀等进行废轮胎在超临界甲苯中的解聚研究,在温度345℃时,液相产物以芳香族和烯烃化合物为主,且相对分子质量均小于300。
Toshitaka Funazukurl等人尝试了将超临界反应在0.7L分批式操作高压釜内进行,试验了不同超临界流体:水、正戊烷、甲苯、氮存在下废轮胎热解反应的变化。通过实验发现,溶剂的溶解能力由大到小依次为:甲苯、正戊烷、氮,而水的溶解能力与正戊烷相近;不同溶剂的使用并未影响产品的产率,如:在653K、5.2MPa的操作条件下,油品的产率均为57%,固体产率均为40%。
超临界热解示意图见图3-4。

图3-4 超临界热解示意图
3.1.4 熔融盐热解
熔融盐是优良的传热介质,可使液体和橡胶充分接触,反应速率快。这项工艺可应用于整个或半个轮胎及粉碎轮胎。该工艺使用类似氯化锂/氯化钾低共熔混合物作传热介质,这些混合物在反应前后没有改变,可循环使用。典型的做法是:将轮胎碎块浸入氯化锂/氯化钾的低共熔混合物中,加热至500℃,可得到质量分数为47%的油、45%的固体残余物和12%的气体。油中包括质量分数约为21%的芳烃油、34%的链烯烃和45%的石脑油。气体为C1~C4的石脑油和链烯烃混合物。Stemachowski以熔融盐为介质,在390~420℃的温度下分解废橡胶,得到了C2~C8为主的气体产物质量分数为14%,液体产物C4~C24为主的质量分数为41%,其中75%(摩尔分数)为C4~C10和固体残余物。
英国邓禄普公司在ASTON大学投资研究使用熔融金属碳酸盐作为热解传热源。由于硫及其他污染物同熔融盐进行了反应,因此气体中的硫化氢质量分数小于3×10-7。Chalnbers等选用废轮胎在多种熔融盐中热解,温度380~570℃,反应迅速。随着温度增高,甲烷量增加,同时C4气体减少;随着酸性金属盐增加,气体产量提高。
熔融盐热解示意图见图3-5。

图3-5 熔融盐热解示意图
3.1.5 微波热解
微波是一种非离子的电磁辐射,其频率在100~300GHz之间。生活及工业中常用的频率为915MHz和2450MHz。微波热解技术是在150~350℃的惰性氮气环境中利用微波能将化学键断开,经分离得到液油、燃气及炭黑的过程。日本大阪技术试验所研制的微波热解装置频率为2450MHz,输入功率为1100W,输出功率为580W。将块状废轮胎盛入一容器,再将容器放入微波炉,导入氮气、施加微波,废轮胎开始分解,接着生成气体由导出管冒出,经过三个冷凝器进行油气分离。由于施加微波时,废轮胎从内部发热,所以在数十秒至数分钟内,局部热解产生的有机气体像火山爆发似的喷射出来,炭黑残留原处,吸收微波形成更高的温度,继续施加微波,有机成分分解气化,炭黑局部堆积,接着炭变得炽热,有机成分急剧排出,数分钟就变成炭黑为主的黑色粉末。
BRC Environmental开发出5000吨/年的微波炉处理装置。废轮胎不需破碎,整只送入微波炉。实践证明该装置的传热效果很好,可以得到较为干燥的产物,而且可以得到较高质量的活性炭。
加拿大Ellsin Environmental公司与Environmental Waste International(EWI)公司合作,采用EWI公司的反相聚合专利技术兴建废轮胎微波热解示范装置。采用微波处理技术,只需较低的分解温度(250~300℃)即可在氮气室中将轮胎分解成炭黑和油气。此外,新技术还能够通过产生的气体带动微涡轮发电,剩余的电量可纳入国家电网。该示范场每天可回收900条轮胎。
与传统热解工艺相比较,它避免了有机物的氧化过程,阻止了如二氧(杂)芑和呋喃等有毒物质的产生,大大改善了热解产物的质量,特别是炭黑的稳定性。
3.1.6 共热解
由于废轮胎含碳高达82%(质量分数),含氧极低,而生物质本身含氧较高34%~38%(质量分数)、含碳较低39%~47%(质量分数),两种物质单独热解得到的热解油的品质都不高,所以就有学者考虑将这两种物质与催化剂按一定比例混合后共热解,以生物质热解产生的含氧自由基破坏废轮胎热解产生的碳氢自由基,使某些不希望生成的化合物受到抑制,进而提高热解油品的品质。
曹青等将稻壳与废轮胎按不同比例组混合,以MCM-41和SBA-15为催化剂在管式热固定床反应器内共热解,发现共热解过程中组分间可以产生一定的相互作用,具有协同效果,主要体现在柠檬油精组分的含量低于加权后的浓度,氧含量大于加权后的数值。与没有催化剂的情况相比,MCM-41和SBA-15的存在能显著降低热解液体的黏度和密度,其中SBA-15的降低效果更为明显。
靳利娥等对生物质与废轮胎共热解催化热解油的蒸发过程进行了研究,认为催化剂SBA-15和MCM-41的存在对降低高沸点馏分的物质具有一定作用,而SBA-15催化作用优于MCM-41。
曹青等还在500℃下将不同比例的稻壳与轮胎混合物在SBA-15、Mo/SBA-15和Co/SBA-15三种催化剂下共热解,研究表明,随着轮胎比例的增大,热解油相对密度和黏度有所降低;当稻壳与轮胎比例为75:25时,Co/SBA-15对油中氧含量的降低和氢含量的提高表现出较好的效果。
由于废橡胶、废塑料、生物质与煤存在共同的热分解区间,1990年以来,国内外研究者从塑料、合成树脂、橡胶轮胎、生物质等高分子废料再利用的角度出发,进行添加上述废料与煤共热解或共焦化研究,以期上述废料能与煤发生良好的协同效应,能作为配煤炼焦的黏结剂,减少炼焦煤的用量,同时能够获得焦化剂副产品煤焦油、煤气。
煤热解制取焦油和煤气是传统的工艺。这种过程的一个主要问题是需要高压氢气的供应。这就造成生产的焦油与原油相比经济性较差。而废轮胎是富氢的废弃物。所以把废轮胎与煤共热解,可以提供煤热解所需的氢,同时利用现有的煤热解设备节约了设备投资。与此同时,废橡塑的几何形状各异、熔点不同、化学组成不同等因素使得很难找到一个工艺过程同时适用于这些废橡塑。这样与固体燃料的共热解不失为一种有效的解决办法。由图3-6所示的废轮胎与煤共热解过程可以看出,废橡塑与固体燃料及循环热灰混合在约500℃的热解反应器中热解得到热解油和气,然后进行收集。或者热解得到的挥发分在温度约为600~900℃的二次反应器中继续气化来得到更高品质的燃气和芳香化合物含量更高的热解油。废轮胎与煤共热解技术经济性好,不需要为废橡塑专门设计反应设备,废橡塑作为供氢原料有利于改善固体燃料的热解,由于固体燃料中常含有碳酸盐,因而共热解可以减少硫的排放,混合物更容易输送和给料。

图3-6 废轮胎与煤共热解过程流程示意图
西班牙A.M.Mastral等多年来致力于废轮胎与煤的共热解研究。他们先后在批量式(管式炉、搅拌釜)、半连续式(吹扫式固定床)反应器中进行试验。在批量式反应器中有机组分达到100%的转化率,而半连续的反应器就达不到这种效果。反应器的类型对产物中油和气的比例是有影响的。对于批量式反应器增加氢气的压力会提高转化率,而对半连续的反应器则反之。而且搅拌釜热解油的饱和烃含量最高、极性物质的含量最低。在搅拌釜反应器中共热解所获得的油中芳香烃的含量要高于两者分别单独热解。这是由于两者的自由基团相互反应的缘故。在管式炉中共热解反应时间对废轮胎获得最大转化率没什么影响,而对煤却有一定的影响,而且反应时间长有利于生产轻质油。
3.1.7 加氢热解
加氢热解技术在炼油工业得到广泛的应用。其主要目的是提高石油加工的深度,增加发动机燃料、化工原料以及微生物工业原料的产量,扩大润滑油的生产规模并改善其品质。现在许多学者用这种方法进行生物质等废弃物热解油的改良。但是废轮胎加氢热解技术的应用研究还非常少。A.M.Mastral等人在固定床反应器中,对废轮胎进行了氮气热解和加氢热解的研究。认为两种情况下总转化率和油产率相差不大,但是氢气的压力是油组成的最主要的影响因素。氢气的压力越高,油中轻质油、芳香物的含量升高,极性物质的含量减少。而且Hao-kan Chen等人的研究也表明,加氢热解有利于燃料中硫的析出,从而减少热解产物中硫的含量,改善产物的品质。加氢热解不仅是调和废轮胎气化、燃烧、液化的重要阶段,而且是其洁净转化的简单有效的方法,因此,最近这些技术受到了格外的关注。
3.1.8 自热热解
废轮胎的热解反应的总体热效应是吸热反应。大多数的热解装置都需要外热源。但是废轮胎本身的热值很高,约为35MJ/kg,而热解吸热仅为700kJ/kg。所以很少一部分轮胎燃烧就可以提供大多数轮胎的热解。基于这种优势提出用自热热解的方式来处理废轮胎。日本瑞翁-日挥方式的流化床热解装置通入少量的空气使2%~3%的废轮胎燃烧来维持450~500℃的热解温度。Min-Yen Wei等人在鼓泡流化床反应器中进行了自热热解的研究。系统的运行温度在500℃左右。实践证明,自热方式的运行还是有一定困难的。油的产量受到过量空气系数的影响,一般在15%~45%。Jong Ming Lee等人也在流化床反应器中进行了废轮胎的自热热解研究。热解温度在700~880℃,燃料气的产率在30%~40%,半焦产率32%。
3.1.9 等离子高温热解
美国Westinghouse公司开发了等离子体热解装置用于处理废水。Retech公司开发等离子体离心反应器用于处理污泥。该装置有一个低速旋转的炉膛,温度在1127℃。二次反应器的温度在977℃。MasonHanger国际公司使用一个静态的主反应室来处理医用垃圾。到目前为止还没有发现处理废轮胎的等离子体反应装置。只是由于考虑到这种反应装置良好的环境效果,才在这里提出。希望能在以后的发展中看到它在废轮胎处理方面的应用。等离子高温热解的主要设备如图3-7和图3-8所示。

图3-7 等离子体高温热解主要设备Ⅰ

图3-8 等离子体高温热解主要设备Ⅱ
3.1.10 催化热解
轮胎橡胶是一种高分子材料,在一定的温度和压力下,可使这种高分子聚合物热解成低分子化合物,但若采取单一热解处理,则需温度高(400℃以上)、加热时间长、油品产率低、将增大设备投资和操作难度、缩短设备使用寿命、经济效益低。而采取催化热解的方式,不但可以降低反应的活化能,使热解反应迅速进行,还可以改善热解油品的品质,提高了废轮胎热解的经济效益。催化热解示意图见图3-9。

图3-9 催化热解示意图
(1)催化剂 目前研究中所用的催化剂按性质分为固体酸和固体碱两大类。固体酸催化剂主要是ZSM-5、USY、SBA-15等分子筛类催化剂;固体碱催化剂则有很多种类,包括碱金属或碱土金属氧化物(如MgO、ZnO)、金属盐类(Na2CO3等)和负载碱类(如碱金属或碱土金属分散在活性炭上)催化剂等。此外还有一些过渡金属氯化物(如ZnCl2、NiCl2等)和碱液(NaOH等)也被用作废轮胎热解的催化剂。
催化剂的加入方式分为直接加入和间接加入两种。直接加入是将催化剂与废轮胎按一定比例混合后放置在反应器中;间接加入是将催化剂单独放置在反应器的后段,催化废轮胎热解产生的油气混合物、大部分分子筛类催化剂都是以这种方式加入的。
目前研究中催化剂对热解反应的影响主要表现在以下几个方面。
①降低反应的活化能,加速热解反应 王文选等选用FeCl3、NiCl2、CoCl2、TiO2和Cr2O3五种催化剂,将催化剂粉末与絮状废旧轮胎粉按质量比1:10均匀混合进行热解。结果表明在最终热解率相同的情况下,选用的几种氯化物对热解反应是有影响的,与未加入催化剂时单一热解的终端温度600℃相比,NiCl2催化效果最好,可以把终端温度降低45℃左右,FeCl3、CoCl2可以降低25℃左右;选用的氧化物对热解反应影响较小,TiO2和Cr2O3只能降低15℃左右。加入的催化剂对最终热解率没有影响,但能降低反应的活化能,加速热解。
唐光阳将T-2型催化剂与废轮胎碎片按质量比1:100的比例混合在常压下催化热解,结果表明在400℃时,催化热解的油品收率即达到最高(约45%),而单一热解的油品收率在500℃时最高(约35%),催化热解的温度比单一热解温度降低约100℃。在400℃以前相同的温度下催化热解比单一热解的油品收率提高15%左右。
Zhang等研究了添加NaOH和Na2CO3在450~600℃时对废旧轮胎真空热解(3.5~4.0kPa)的影响,发现单一热解时油品收率在550℃时达到最大,为48%;加入3%(质量分数)的NaOH粉末后,480℃时油品收率就达到50%。
②对热解气组成的影响 催化剂的加入可以改变热解气体的组成,这种影响主要体现在小分子气体产物含量增加和大分子气体产物含量降低,但也有相反的情况出现。
张兴华等研究发现热解气态产物主要有H2、CO、CH4、CO2、C2H4、C2H6以及少量的H2S等。NaOH(固体粉末)的加入使气体产品中的H2相对体积分数明显增加,500℃时热解气中H2体积分数达到60%左右,而CH4、CO、C2(C2H4+C2H6)等的体积分数降低。刘阳生等将4% NaOH溶液加入到40目的破碎胶粉中进行热解,也发现在相同的热解温度下NaOH的加入使H2的收率提高,CO、CH4、CO2的收率减少。
张兴华等以CaO、ZnO、CaO/TiO2和ZnO/TiO2作催化剂520℃真空热解(3.5~4.0kPa)废轮胎,发现ZnO/TiO2作催化剂时,对气体组成的影响比较显著,热解气收率达到24.82%,气体热值达到28.76MJ/m3,H2含量明显降低而CH4的含量增加。CaO/TiO2则使气体中H2含量增加而C2(C2H4+C2H6)减少。使用催化剂后,气体中的H2S含量显著降低,从未加催化剂时热解气中的195mL/m3下降到60mL/m3以下。添加ZnO时催化剂的脱硫效果更显著,H2S含量降到25mL/m3。同时未添加催化剂时在加热过程中形成的结焦或积炭的量较大,积炭率达到8.25%,而添加催化剂能有效降低热解过程中结焦或积炭现象的发生,ZnO/TiO2催化时积炭率仅为2.73%。
③对热解油品收率和品质的影响 废轮胎热解得到的油品成分非常复杂,含有大量的有机物,其中最有再利用价值的是石脑油。石脑油是管式炉热解制取乙烯、丙烯、催化重整制取BTX(苯)、甲苯、二甲苯的重要原料。催化热解废轮胎得到石脑油的量高于未加入催化剂热解的,尤其是具有较高价值的单环芳烃(苯、甲苯等)的浓度显著增加,提高了热解油品的品质。
Ucar等研究了金属负载活性炭催化剂和商业催化剂对废旧轮胎热解油品质的影响。活性炭由废旧轮胎热解炭黑制备,其上负载有不同的金属对:Co-Ni、Co-Mo和Ni-Mo。在350℃,7kPa氢气气氛下,几种金属负载活性炭催化剂的催化活性相似,但Ni-Mo/Ac效果最好,在Ni-Mo/Ac和商业催化剂作用下,液态油中有45%~55%的石脑油馏分和20%~25%的煤油馏分。
Miguel等研究了五种固体酸催化剂(催化剂与轮胎质量比为1/10)(ZSM-5、纳米晶体n-ZSM-5和β-ZSM-5、Al-MCM-41和Al-SBA-15)对废轮胎热解生成烃类的影响,发现三种ZSM-5对芳香烃的生成特别是甲苯(19.82%)、二甲苯(16.91%)和苯(10.28%)具有明显的选择性,其中n-ZSM-5的选择性催化作用最为显著,因为其具有较强的酸性和较弱的空间位阻效应。Al-MCM-41和Al-SBA-15表现出强烈的芳构化和苯烷基化性能,因此有大量的烷基化芳香烃生成。
Williams和Brindle用ZSM-5和Y型分子筛作为废轮胎热解的催化剂也发现油品中单环芳烃的浓度明显增加。随着催化温度的升高,油品收率下降,随之气体和热解炭收率增加,油品中苯、甲苯、二甲苯、萘和烷基化萘的浓度明显升高,尤其是Y型分子筛的作用更加明显,这与其具有较高的表面活性和较大的孔径有关。沈伯雄等的研究也发现USY型分子筛催化剂与ZSM-5相比具有更高活性。
张兴华等发现未添加催化剂所得石脑油要少于添加Na2CO3、NaOH,使更多的大分子有机物降解为沸点较低的小分子有机化合物。这表明添加Na2CO3、NaOH使热解程度提高,有利于改善热解油的品质。热解石脑油中含量最大的组分为柠檬油精(C10H16)。这是一种应用价值较高的工业有机溶剂、添加剂和油脂树脂颜料分散剂,亦作为氟氯烃的替代品用于清洁电路板等。热解油中柠檬油精的质量分数较高,在11%以上。碱性催化剂加入后,热解油中柠檬油精的质量分数略微增加。
(2)催化机理的探讨 在大多数情况下,人们认为催化剂本身和反应物一起参与了化学反应,降低了反应所需活化能。有些催化反应是由于形成了很容易分解的“中间产物”,分解时催化剂恢复了原来的化学组成。有些催化反应是由于吸附作用,吸附作用只能在催化剂表面最活泼的区域(称为活性中心)进行。活性中心的区域越大或越多,催化剂的活性就越强。
对于分子筛类催化剂,其催化活性主要受其孔径和Si/Al摩尔比的影响。孔径较大的分子筛能让更多的分子物质进入其孔内发生催化反应,形成更多的芳香烃;有较低的Si/Al摩尔比的催化剂有相对较强的氢转移能力,即高的催化活性,也就产生较多的芳香烃。分子筛的酸性较强,适中的酸性有利于芳构化及芳烃和烯烃的烷基化。在分子筛结构中,靠近Al中心的O位容易吸附H+,通常称之为酸性位质子,各种吸附过程及催化反应均在酸性位附近进行。分子筛催化反应的选择性取决于分子与孔径的大小,这种选择性成为择形催化。在废轮胎的催化热解方面主要表现为对油品中的芳烃类物质如苯、甲苯、二甲苯等具有明显的选择性。
固体碱催化剂通过电子收受配位体(EAD)形成碳负离子从而使反应发生。例如:双键异构化反应是在固体碱催化作用下通过形成烯丙基阴离子然后脱氢而实现,对反应中间产物烯丙基的存在可通过烯与氘的交换示踪研究证实。金属氧化物如MgO、CaO等可以催化烯烃、炔烃、丙二烯类含杂原子的不饱和有机物发生双键异构化反应,混合氧化物如ZnO/Fe2O3可以催化酚类、苯胺类物质发生烷基化反应。
Ranby和Rabeck研究了过渡族金属化合物在烃类化合物中的催化作用,提出了可能的催化反应方程式:
①
②
③
其中反应后的R还可以以有机基团配体的形式与金属离子直接以配位键结合成有机过渡金属配合物作为反应的中间体,使分子轨道能级发生变化而活化,促使反应加速进行。
(3)存在的问题及研究方向 催化剂的加入使废轮胎热解反应加速,得到了品质较高的热解产物,提高了废轮胎热解的经济价值。但是在实际应用过程中还存在一些问题。
①催化剂与废轮胎的比例问题 催化剂与废轮胎的比例直接影响热解产物的组成及催化热解的经济性问题。以往的研究中虽然对催化剂与废轮胎的比例问题作了多方探讨,但实验室规模研究较多,加入量一般占废轮胎质量的百分之几,从工业化应用的角度看,经济性不高。
②催化剂与热解炭黑的分离问题 对于催化剂与废轮胎直接混合的体系来说,热解反应结束后催化剂与热解炭黑混杂在一起。催化剂一般作为灰分存在于热解炭黑中,降低了热解炭黑的品质,不利于热解炭黑的再利用。
③催化剂结焦失活问题 催化剂的结焦问题在废轮胎与催化剂分开放置的两段或多段式反应器中比较严重。尤其混合物在经过催化剂时逐渐沉积在催化剂的孔隙和表面上,使其催化活性慢慢丧失。废轮胎热解催化剂上的结焦物成分复杂,难以通过一般方法使催化剂再生。
因此,选择适宜的催化剂,掌握好催化剂与废轮胎的比例,热解反应条件的优化等都是未来废轮胎催化热解的研究方向。
3.1.11 热解气化联用技术
德国VEBA OEL工程技术公司设计了一套混合的系统以克服气化过程中经常出现的细小颗粒的磨损以及均匀物料的给料问题。由于热解中的给料通常达到200mm或以上,热解产物可以均匀地混合在一起,这样就解决了上述问题。废轮胎联合热解气体系统流程如图3-10所示。

图3-10 废轮胎联合热解气化系统流程