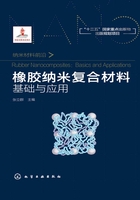
1.2 橡胶纳米复合材料的发展历史与现状
1.2.1 炭黑/橡胶纳米复合材料
1904年,英格兰一家橡胶公司的首席化学家莫特(S.C Mote)最早发现一旦把炭黑加入橡胶中便可提高橡胶的强度,这或许是橡胶材料史上第一次采用纳米颗粒来补强橡胶。但直到1912年,炭黑这一“秘密”组分才被美国的Diamond Rubber公司大量应用于轮胎,提高轮胎的寿命。这对于橡胶工业和炭黑工业,都是非常重要的,使这两个行业和这两种材料紧密联系在一起,相互促进、共同发展。通常认为,第一种炭黑生产工艺是由美国费城油墨制造商怀特(J. K. Wright)发明的,当时旨在用于生产一种新型的亮光漆。1872年,第一个商业化规模的炭黑生产厂在美国西弗吉尼亚州建成。槽法是早期炭黑的主要生产工艺,后来又发展出了炉法、热裂解法和油炉法等不同工艺。人们发现不同工艺生产出的炭黑对橡胶的补强性能和工艺性能不同。两次世界大战对于合成橡胶制备的驱动,也促进了更多新品种炭黑的发展。透射电子显微镜的使用,使人们对炭黑形态学有了深刻的认识。1940年报道了对炭黑的第一次电子显微镜测量结果。研究人员发现,易混槽法炭黑(EPC)的粒径为26~29nm。20世纪40年代初期,拉德(W. A. Ladd)利用透射电子显微镜对商品炭黑进行了大量研究,发现粒径越小的炭黑,比表面积越大,对橡胶的补强作用越强。随后,在1945年,拉德和韦厄甘德(Wiegand)用电子显微镜图像解释了炭黑“结构”,提到原生粒子会熔结成簇,现在将其称为炭黑的聚结体(aggregate)。第二次世界大战后,汽车工业的发展对轮胎的需求导致了炭黑品种的不断增加,这使得制定科学合理的分类体系和对炭黑工业进行标准化迫在眉睫。1952年,8家美国炭黑生产商组成了炭黑行业委员会,旨在使该行业合理发展,并为炭黑制定统一的试验方法。1955年9月,在美国材料与试验协会(ASTM)的支持下,该组织作为D24委员会开始运行,并于1967年,制定并发布了基于炭黑初级粒子粒径和硫化胶性能的炭黑品种分类体系。ASTM D24制定的ASTM D1765《橡胶用炭黑分类命名系统》是国际上广泛采用的橡胶用炭黑标准(ISO和GB标准各内容与其基本相同)。20世纪70年代初,在炉黑生产工艺基础上进行改进,出现了新工艺炭黑。新工艺炭黑的聚结体尺寸分布较窄,在比表面积与传统炭黑相同时,耐磨性提高5%~20%,进一步提升了子午线轮胎的性能。至今,全球炭黑总产能已超过1200万吨/年,其中90%以上用于橡胶增强。当前世界最大的四家炭黑生产企业是美国卡博特公司(Cabot Corporation)、德国赢创工业(Evonik Industries)、美国哥伦比亚化学公司(Columbian Chemicals)和中国黑猫炭黑股份有限公司。
炭黑纳米粒子增强橡胶的特点是:耐磨性好,抗撕裂,抗切割,具有抗静电性能和抗紫外老化性能;但动态生热高,且不适于浅色橡胶制品。为了提高炭黑在橡胶中的分散,美国卡博特公司采用独特的连续液相混合凝固工艺制备的炭黑/天然橡胶母炼胶——卡博特弹性体复合材料(CEC),显著提升了橡胶的综合性能,但该产品没有在市场上广泛销售。卡博特公司还开发出了以炭黑为基础的表面含有白炭黑成分的新型炭黑——双相炭黑,在不损失耐磨性的同时,可降低动态滞后损耗和提高抗湿滑性,特别适用于高性能节油轮胎胎面橡胶复合材料,但由于成本较高等原因,该产品商品化进展并不顺利。
总体来看,由于白炭黑在绿色轮胎工业中的用量不断增加,炭黑应用量的增速放缓,甚至还会有所下降。尽管如此,由于炭黑增强橡胶具有突出的耐磨性和抗切割特性等,其仍然是橡胶材料最为重要的增强剂。笔者认为,未来炭黑的发展方向是制备出表面能与橡胶材料产生化学键合的炭黑新品种或能实现炭黑与橡胶间化学键合的界面改性剂;发展高分散的炭黑橡胶纳米复合母胶技术,来提高炭黑在橡胶中的分散性并降低动态生热;发展出高导热、高导电性能的炭黑品种,来增强橡胶纳米复合材料的导热性、抗静电性和延长动态热负荷寿命。另外,制备中空结构的轻量化炭黑、生物质炭黑,以及从废轮胎中热解提取炭黑和利用废轮胎热解油气生产炭黑的绿色循环策略都是很有意义的方向。