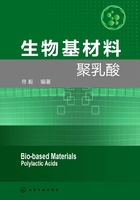
1.3 聚乳酸的合成
PLA的合成主要有两种途径:一种是由乳酸直接缩聚合成聚乳酸,常通过熔融缩聚、熔融缩聚-固相聚合或溶液缩聚完成,该法统称为PC法[80];另一种则是通过丙交酯开环聚合得到聚乳酸,即利用乳酸单体经脱水环化先制备丙交酯单体,然后由丙交酯开环聚合获得具有高聚合度的聚乳酸,该法统称为ROP法[81]。
PLA的合成路线如图1-7所示。

图1-7 PLA的合成路线
1.3.1 乳酸直接缩聚法
直接缩聚法就是由乳酸直接脱水得到聚乳酸,该方法合成的聚乳酸的分子量一般为几万,分子量相对来说较低,且分子量的范围也宽。但是通过除去聚合过程的水以及控制反应温度等条件,可以得到改良,获得分子量较高的聚乳酸。方法主要包括溶液缩聚法和熔融缩聚法[82]。原理见图1-8。

图1-8 乳酸直接缩聚制备聚乳酸
在适当的条件下,乳酸分子之间的羟基和羧基直接脱水缩合,去除小分子水产物,使反应向聚合的方向进行,从而制备PLA。直接缩聚法制备PLA可以分为三个主要阶段:①降低自由水含量;②低聚物缩聚;③熔融缩聚得到较高分子量PLA。
乳酸直接缩聚法制备PLA的过程是一个可逆反应,该反应在反应体系中存在着游离乳酸、自由水、PLA和丙交酯的平衡。随着反应的进行,体系的黏度不断增加,后期聚合过程中从黏稠熔体中除去水变得越来越困难,即使在真空条件下也很难进一步去除水。更高的温度(>200℃)虽然有助于去除小分子水,但是也有利于丙交酯的形成。同时,体系中伴随着一系列副反应,如酯交换反应可能形成不同尺寸的环状产物[83]。分子量较低的PLA容易水解、力学性能极差、没有使用价值。
通过缩聚反应制备高分子量聚合物,必须采用高光学纯度的聚合级乳酸,并且抑制副反应,尽量除去水和其他副产物。研究者尝试多种方法提高直接缩聚法获得的PLA的分子量,包括:①采用与溶剂形成共沸混合物的方法带走小分子水,从而制备高分子量PLA,摩尔质量可达300000g/mol[84];②在反应后期采用熔融聚合的方法,降低体系的黏度、去除小分子水,提高分子量[85,86];③采用扩链剂将乳酸缩聚法制备的PLA分子偶联起来,从而提高PLA的分子量[87~89]。
1.3.1.1 溶液缩聚法
溶液缩聚法一般是利用溶剂共沸法除水回流进行高分子量的聚乳酸的制备。体系中水分除得越彻底,得到的聚乳酸的分子量就越高。因此该法对溶剂的要求较高,一方面不能参与反应,另一方面要能够溶解聚合物并与水共沸。溶液缩聚法体系的反应温度一直处于共沸点,因此能够避免因升温和局部温度的变化引起的聚合物的分解。但是该方法的不足之处就是有机溶剂的使用和回收会使得操作和设备更加复杂,而且使用高沸点或有异味的有机溶剂时,会增加聚合物纯化的难度。
溶液缩聚法是指在一定温度和真空度下,在体系中加入一种有机溶剂与乳酸单体和反应得到的水进行共沸回流,在回流过程中,水分会随着回流时间的增加而逐渐被带出,从而推动反应向正方向进行,以获得高聚合度的聚乳酸[90]。在反应过程中,溶剂的作用分为三点:第一,有效降低反应体系的黏度,吸收反应放出的热量,降低反应剧烈程度;第二,可以溶解乳酸单体,使正在增长的聚乳酸溶解或溶胀,促进聚乳酸链的增长;第三,可以与体系中产生的水分子形成共沸物,在回流的同时将水分子逐渐除去[91]。日本研究者Ajioka[92]采用二苯醚作溶剂,锡粉催化,经分子筛共沸回流反应40h,可使聚乳酸的分子量达到300000。秦志忠等[93]通过分阶段地升温减压除水,制得了分子量为20万的聚乳酸,与Ajioka等的方法相比较有一定的差距,但是也具有非常大的实用价值。同济大学任杰[94]等发明了一种用于溶液缩聚的反应装置,该装置可以实现溶剂的反复回流使用,既可用于溶剂密度小于水的反应,也可用于溶剂密度大于水的反应,大大降低了反应成本。复旦大学钟伟[95]等使用苯甲醚作为溶剂,通过真空缩聚和溶液回流带水的方法制取PLA,在常压下反应温度为180℃时共沸回流36h,得到数均分子量可达19000的合成聚乳酸;陈春明[96]以离子液体氯化1-丁基-3-甲基咪唑盐和氯化亚锡的复盐为催化剂,采用直接溶液缩聚法制备的聚乳酸,其黏均分子量为3.5×104。三井化工开发了共沸缩聚制备高分子聚乳酸的工艺[97~100],该工艺采用锡化合物和质子酸作为催化剂,并采用高沸点溶剂,在较低温度(130℃)和高真空度下共沸除去水分子,然后通过溶解沉淀的方法将PLA从溶剂中分离出来,得到了重均分子量为30万的聚乳酸。
1.3.1.2 熔融缩聚法
熔融缩聚法是一种发生在聚合物熔点温度以上,且没有任何介质参与的本体聚合方法[101]。熔融缩聚就是将体系直接加热进行缩聚反应,反应过程中体系要一直处于熔融的状态,生成的水等副产物要通过真空抽出或者通过惰性气体携带排除。该方法得到的聚合物分子量一般小于溶液法。但是通过对预聚物进行处理,增加反应时间、降低反应温度,或者使用更优的催化剂等进行进一步的缩聚可以提高聚乳酸聚合物的分子量,因此再缩聚的催化剂的选择和反应条件的控制是熔融缩聚法的研究重点,主要有反应挤出聚合、熔融-固相聚合、扩链反应等方法。
东华大学余木火等发明了一种熔融缩聚制备高分子量聚乳酸的方法[102],通过以乳酸、脂肪族二元酸为起始原料,制得两端为羧基的乳酸预聚物,然后再加入一定比例的环氧树脂,于一定温度、压力条件下制得高分子量的聚乳酸,通过优化条件可以得到黏均分子量为13万~22万的高聚物。杨青芳[103]采用阶段控温的熔融聚合法,大幅度提高了聚乳酸的产率和分子量,合成出数均分子量为1.9万的PLA,产率高达77%。
在催化剂的选用方面,常用的酯化反应催化剂有中强酸(H2SO4、H3PO4)、过渡金属及其氧化物或盐(Sn、Zn、SnO2、ZnO、SnCl2、SnCl4)、金属有机物(辛酸亚锡、三乙基铝)。
(1)反应挤出聚合 利用反应器与双螺杆挤出机组合进行熔融缩聚得到高分子量的聚乳酸,该方法的反应时间短、成本低,具有一定的研究前景。如日本Steel Works公司通过将4.4万分子量的聚乳酸缩聚物置于具有回流装置的双螺杆挤出机中,并补充因真空抽滤损失的乳酸,进行低分子量缩聚物的进一步缩聚,使得最终的聚乳酸分子量达到了15万。
(2)熔融-固相聚合 该方法是将缩聚的预聚物处于高于其玻璃化转变温度、低于熔融温度的条件下进行进一步的聚合。进一步聚合的机理是无定形区的低分子与大分子的端基进行反应生成高分子聚合物,最终的聚乳酸的分子量和结晶度都得到了进一步的提高,但是该方法的反应时间较长。
该法首先将反应物乳酸在减压条件下脱水缩聚得到聚乳酸低聚物,然后将该低聚物在低于Tm且高于Tg的温度下进行缩聚得到高分子量的聚乳酸[104]。在低聚物中,由于大分子链部分被“冻结”形成结晶区,同时官能团末端基、小分子单体及催化剂会被排斥在无定形区,因此促使低聚物获得足够的能量,有利于分子之间发生有效碰撞,使反应得以继续,并且通过高真空或惰性气体将反应体系中的水分子带走,也能使反应平衡向正方向移动[105],而加长的分子链在晶区边缘集结结晶,又使聚合物结晶度增加,限制副反应的发生,促进残留单体的转化,从而提高聚乳酸的纯度和质量。
赵文军[106]以乳酸丁酯单体为原料,以复配的SnCl2和TSA为催化剂,首先在160℃下熔融聚合10h合成低聚物,继续在140℃下固相缩聚40h以进一步提高分子量。合成的聚乳酸经红外光谱和XRD测定,为聚外消旋乳酸(PDLLA),黏均分子量可达22000。Moon等[107]利用改良后的熔融-固相缩聚方法,以二水氯化锡和邻甲苯磺酸二元体系为催化剂,合成了聚合物分子量高达50万的PLLA,克服了缩聚温度高于PLLA的Tm时产率下降的问题。
(3)扩链反应 在获得高聚合度聚乳酸的方法中,扩链剂扮演着重要角色。扩链剂是指在短时间内能够提高低聚物聚合的某些化合物,通常是一种双官能团化合物,且极易与两种低聚物链末端官能团发生反应[108]。其原理是:聚乳酸低聚物中含端—OH和端—COOH,采用对这两种基团反应活性均较高的扩链剂与其作用,使聚乳酸低聚物分子量成倍增长,得到具有较高分子量的聚乳酸[109]。扩链聚合法具有反应速率快、时间短的优点,但反应活性较高的偶合剂或扩链剂一般都具有较差的热稳定性。具有端—OH和端—COOH的二异氰酸酯、二环氧化物、双唑啉、二酸酐和双乙烯酮缩醛是应用较多的几种扩链剂。Hiltunen等[110]采用L-乳酸为原料、1,5-二羟基萘作为扩链剂,于220℃条件下进行聚合,最终获得了最高重均分子量高达7.2万的高分子量聚乳酸。
1.3.2 丙交酯开环聚合法
L-丙交酯开环聚合可以制备高分子量PLA,并可以调控PLA的分子量、分子链结构形态和物理化学性质。目前工业化PLA树脂合成均采用该方法。该方法可以通过熔融聚合、本体聚合、溶液聚合和悬浮聚合等技术实现。其中,熔融聚合技术被认为是最简单且具有可重复性的方法[111]。丙交酯开环聚合制备PLA先由乳酸制备丙交酯,再通过熔融聚合技术由丙交酯开环聚合得到PLA。
采用不同结构的丙交酯开环聚合,可以得到不同分子结构的PLA。丙交酯开环聚合制备PLA通常采用辛酸亚锡为催化剂,脂肪醇为引发剂[112~117]。采用这种方法也可以制备不同比例的L-丙交酯、D-丙交酯共聚物。该方法的反应过程见图1-9。辛酸亚锡是最常用的催化剂,能够很好地控制反应速率和分子量。丙交酯开环聚合制备PLA的反应机理依赖于聚合条件、催化剂类型、引发剂浓度和溶剂等因素。

图1-9 丙交酯开环聚合制备PLA(R:H、烷基等)
开环聚合方法能够通过控制反应时间、温度和选择不同的催化剂对聚乳酸的合成分子量进行控制,但是该方法聚乳酸提纯的过程比较复杂,成本较高。根据使用的催化剂的不同以及反应机理的不同,可分为离子开环聚合、配位开环聚合和有机开环聚合等。
1.3.2.1 离子开环聚合法
离子开环聚合又可分为阳离子聚合和阴离子聚合。阳离子聚合中阳离子催化剂主要指的是质子酸型。质子酸型的聚合机理是H+与乳酸单体中的氧原子作用形成氧离子,促使烷氧键断裂,单体开环,产生酰基正离子,进而进行链的增长。阴离子聚合中阴离子催化剂主要指的是碱金属烷氧化合物,其催化聚合的反应机理是烷氧基阴离子与乳酸单体中的羰基发生亲核反应,促使烷氧键断裂,产生增长活性中心,进行链增长的聚合反应。阳离子聚合中链的增长是在手性碳上,常常会伴随着外消旋的反应,温度高于50℃发生消旋化,而导致无定形聚乳酸的生成,因此该方法很少用于聚乳酸的制备。同样地,在阴离子聚合中由于阴离子碱性比较强,会促使乳酸手性碳发生去质子化,而导致产物的消旋化甚至是反应终止,限制了聚乳酸分子量的增加,同样限制了该方法的应用。
(1)阳离子聚合 阳离子开环聚合的引发机理如图1-10所示。用于聚合的阳离子引发剂有:质子酸(HCl、RSO3H等)、路易斯酸[AlCl3、MnCl2、SnCl4、Sn(oct)2等]、烷基化试剂(CF3SO3CH3等)等多种酸性化合物。

图1-10 阳离子聚合机理
研究表明,改变[LA]/[R]的比例,并不能使PLA的聚合度有较大改善,因此可以确定阳离子聚合在这种条件下并不属于活性聚合的范畴。因此,为了提高阳离子聚合的催化活性,Bourissou[118]等用酸和质子试剂作为催化剂,使LA发生阳离子聚合。实验表明,利用三氟甲基磺酸作催化剂,异丙醇作引发剂,可以在室温条件下合成分子量大于20000的PLA。
(2)阴离子聚合 图1-11为ROK催化聚合机理。其引发途径可能有两种:第一种是LA的去质子化;第二种则是亲核进攻而开环。因此,通过链端基分析可以很容易地从是否含有引发剂成分来区分两种途径[119]。

图1-11 阴离子聚合机理
通常烷氧碱金属盐常被作为阴离子聚合的催化剂。Kricheldorf等[120]用叔丁氧钾和叔丁氧锂作为催化剂,催化LA聚合,在相同条件下,这两种催化剂和增长链均会发生外消旋反应,同时LA的转化率不会超过80%。然而,利用原位生成的一级钾、二级钾和烷氧锂作为催化剂,却能使LA的转化率高于80%,甚至更高。根据H NMR的链端基分析可以发现,烷氧引发剂已经并入了PLA链中,其引发途径是亲核进攻途径[121]。
Sipos和Zsuga[122]对叔丁氧锂和叔丁氧钾在LA开环聚合中的催化活性进行了研究,同时还研究了冠醚对聚合反应的影响。由于紧密连接的离子对转化成了分散的离子对,因此冠醚试剂可以提高聚合反应的反应速率。然而实验表明,将18-冠醚-6加入叔丁氧钾中之后,聚合反应速率却减小了;同时,将12-冠醚-6加入叔丁氧锂中后,也出现了和18-冠醚-6相同的结果,只是程度较小。
1.3.2.2 配位开环聚合法
LA的配位开环聚合常用的引发剂为羧酸锡盐类、异丙醇铝、烷氧铝或双金属烷氧化合物等。烷氧铝是一类环酯开环聚合的有效催化剂,如Al(Oi-Pr)3被广泛用来研究LA聚合机理。然而其催化活性却不高,在125~180℃条件下,LA的本体聚合需反应几天才能获得较低分子量的PLA。由于Al(Oi-Pr)3催化反应过程中需要一段时间引发[123],同时Al3+在人体内不能新陈代谢,在人体内积聚极易引起早老性痴呆症,因此作为生物可降解聚酯合成的催化剂,Al(Oi-Pr)3应用得并不是很多。
PLA的工业生产中应用最为广泛的催化剂则是羧酸锡盐类化合物,尤其是辛酸亚锡,其自身活性远大于Al(Oi-Pr)3,在醇类试剂的存在下,不但能够较快地催化LA进行聚合,还能更好地控制反应程度。因此,在工业生产中,备受人们青睐,而辛酸亚锡的催化聚合机理研究却颇有争议,一般认为有两种可能性,一种是阳离子或活化单体机理;另一种是配位插入机理。
1.3.2.3 有机开环聚合法
为了更好地满足生物医药聚乳酸材料的应用,研究不含金属的绿色安全的有机催化剂是非常必要的。查阅文献可以发现这类催化剂主要包括胺类、硫脲类等有机催化剂。这类催化剂合成的聚乳酸中不会有金属的残留,能够更好地用于医药材料,但是对于这方面的研究还处于探索期,对机理的研究还不够深入,需要研究者做进一步的研究。