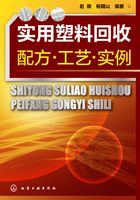
(六)PVC电缆生产中的废料的再生利用
在PVC电线电缆生产过程中,不可避免地会产生工艺废料、机头废料、产品异常剥离的绝缘与护套等废旧PVC电缆料。废旧PVC电缆料一般会有不同程度的老化,所含的助剂都存在不同程度的损失。虽然废旧PVC电缆料再生加工后,其性能与新材料相比有所差异,但是为了减少对环境的影响和变废为宝,应尽可能对其再生利用。可通过重新调整配方,添加必要的功能助剂来改进废旧PVC电缆料的加工性能、力学性能和电气性能等。
针对不同的产品要求,可以采用不同的工艺配方与工艺:
①直接利用废旧PVC块状、粒状料生产线缆用内衬料、电缆薄膜、普通填充条等,一般不必调整配方。
②对废旧PVC电缆料进行收集、破碎、除磁分选后再次挤出造粒成3mm×3mm的内衬专用料,并用于挤制内衬层。
在废旧PVC电缆料的收集、破碎、除磁分选过程中,应认真挑选异物,不能混入PE、LDPE等材料及PVC电缆胶带,必须分离出铜、铝等金属及木屑。确保废旧PVC电缆料干净、无杂物。
1.配方
以废旧PVC电缆料为100份(质量份)计,石蜡、硬脂酸、FWR复合稳定剂等功能助剂合计1.5份。
2.工艺流程
采用废旧PVC电缆料生产内衬专用料及深加工的工艺流程如下:
废旧PVC电缆料收集→分选过筛→破碎切块→混合取样测试→除磁装袋→配比混合→高速混合→挤出塑炼→造粒冷却→风送装袋→取样测试→挤制内衬→取样测试。
实例

挤出内衬层时,挤出机机身预热温度为180℃,机头预热温度为180~185℃,预热时间2h以上。挤出前应对PVC内衬专用料进行烘料,烘料温度为(90±5)℃,时间为0.5~1.0h。烘料温度可根据产品外观、剖面质量进行调整。破碎后的废旧PVC电缆料在70~85℃的混合温度下搅拌混合4~5min后,将混合均匀的PVC物料加入双阶双螺杆挤出造粒机组中挤出造粒,挤出温度为(150±5)℃。不同挤出机的挤出温度参数见表4-3、表4-4。
表4-3 200型挤出机的温度参数 单位:℃

表4-4 150型挤出机的温度参数 单位:℃

造粒后的颗粒料需进行分散冷却,防止粒料黏结。在废旧PVC电缆料二次造粒时,要严格按工艺要求定时更换滤网,并定期检查排气装置。一般每2~3h更换3~4层150~250μm筛孔(60~100目)的不锈钢滤网(或铜滤网),以免滤网被废旧PVC电缆料中的杂质、焦料冲破,在挤出内衬层时因混入杂质而造成电缆护套火花率偏高,发生电压击穿。要加强排气装置的检查,避免排气装置漏气,导致真空压力降低,不易排出HCl、CO2、CO等分解产物及水蒸气,从而造成内衬层出现气孔、针眼,工艺放线性能差,线缆产品外观毛糙、不光滑。
挤制过程中火花电压(10kV、5km)火花击穿不超过3个火花点,内衬层成品的电阻应为1~3MΩ。与H-90PVC护套的挤出温度相比,PVC内衬料的挤出温度相对偏低。每个班次连续挤制内衬8h后须停机进行清理。
二次造粒生产的PVC内衬专用料应及时使用,不宜摆放时间过长,避免材料吸湿受潮,建议摆放时间不超过1个月。
挤出的内衬层外观应光滑,无拉丝、通洞等不良现象;挤出过程中出胶量应稳定;内衬层剖面应无目视可见的气孔、针眼等缺陷;PVC内衬专用料仅用于挤制内衬层,不能用于挤制护套。
3.参考性能
按照GB/T 8815—2008中H-90的指标检测废旧PVC电缆料和PVC内衬专用料的性能,结果见表4-5。
表4-5 废旧PVC电缆料和PVC内衬专用料的性能检测结果

由表4-5可知,两种材料的性能都达到GB/T 8815—2008中H-90的标准要求。PVC内衬专用料因混合充分,经过再次挤出塑化,其力学性能、老化性能要比废旧PVC电缆料性能优异,质量损失稳定。在PVC内衬专用料的加工过程中,其含有的液体助剂在高温条件下分解、挥发,因而其密度略有增大(密度指标为企业要求),但不影响挤出性能。
废旧PVC电缆料因来源差异(来自于H-90、HZ-90、J-70、H-70、HZ-70等)与人为的随意性,仅仅是人工简单地混合压片,其性能存在较大波动,尤其是质量损失、老化前拉伸性能、20℃体积电阻率、冲击脆化性能等。因此,对废旧PVC电缆料进行再生利用前,建议先进行性能检测和二次造粒,最后再挤制内垫层。