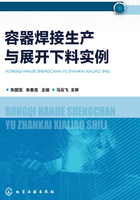
第二节 压力容器的制造工艺
一、封头的展开和下料
目前广泛采用冲压成形工艺加工封头。现以椭圆形封头为例来说明其制造工艺。
封头制造工艺大致如下:原材料检验→划线→下料→拼缝坡口加工→拼板的装焊→加热→压制成形→二次划线→封头余量切割→热处理→检验→装配。
椭圆形封头压制前的坯料是一个圆形,封头的坯料尽可能采用整块钢板,如直径过大,一般采用拼接。这里有两种方法:一种是用两块或由左右对称的三块钢板拼焊,其焊缝必须布置在直径或弦的方向上;另一种是由瓣片和顶圆板拼接制成,焊缝方向只允许是径向和环向的。径向焊缝之间最小距离应不小于名义厚度δn的3倍,且不小于100mm,如图1-5所示。封头拼接焊缝一般采用双面埋弧焊。

图1-5 封头拼缝位置
封头成形有热压和冷压之分。采用热压时,为保证热压质量,必须控制始压和终压温度。低碳钢始压温度一般为1000~1100℃,终压温度为850~750℃。加热的坯料在压制前应清除表面的杂质和氧化皮。封头的压制是在水压机(或油压机)上,用凸凹模一次压制成形,不需要采取特殊措施。
已成形的封头还要对其边缘进行加工,以便于筒体装配。一般应先在平台上划出保证直边高度的加工位置线,用氧气切割割去加工余量,可采用图1-6所示的封头余量切割机。此机械装备在切割余量的同时,可通过调整割矩角度直接割出封头边缘的坡口(V形),经修磨后直接使用;如对坡口精度要求高或有其他形式的坡口,一般是将切割后的封头放在立式车床上进行加工,以达到设计图样的要求。封头加工完后,应对主要尺寸进行检查,合格后才可与筒体装配焊接。典型冲压封头的下料尺寸如表1-1所示。

图1-6 封头余量切割机示意图
1—封头;2—割炬;3—悬臂;4—立柱;5—传动系统;6—支座
表1-1 典型冲压封头的下料尺寸 单位:mm

续表


注:铁的相对密度:7.85;不锈钢的相对密度:7.93;封头的重量=下料尺寸的平方×厚度×相对密度。
二、筒节的展开和放样
筒节制造的一般过程为:原材料检验→划线→下料→边缘加工→卷制→纵缝装配→纵缝焊接→焊缝检验→矫圆→复检尺寸→装配。
筒节一般在卷板机上卷制而成,由于一般筒节的内径比壁厚要大许多倍,所以,筒节下料的展开长度L,可用筒节的平均直径Dp来计算,即:
L=πDp (1-1)
Dp=Dg+δ (1-2)
式中 Dg——筒节的内径,mm;
δ——筒节的壁厚,mm。
筒节可采用剪切或半自动切割下料,下料前先划线,包括切割位置线、边缘加工线、孔洞中心线及位置线等,其中管孔中心线距纵缝及环缝边缘的距离不小于管孔直径的0.8倍,并打上样冲标记,图1-7为筒节划线示意图。这里需注意,筒节的展开方向应与钢板轧制的纤维方向一致,最大夹角应小于45°。

图1-7 筒节的划线
中低压压力容器的筒节可在三辊或四辊卷板机上冷卷而成,卷制过程中要经常用样板检查曲率,卷圆后其纵缝处的棱角、径纵向错边量应符合技术要求。
筒节卷制好后,在进行纵缝焊接前应先进行纵缝的装配,主要是采用杠杆——螺旋拉紧器、柱形拉紧器等各种工装夹具来消除卷制后出现的质量问题,满足纵缝对接时的装配技术要求,保证焊接质量。装配好后即进行定位焊。筒节的纵环缝坡口是在卷制前就加工好的,焊前应注意坡口两侧的清理。
对于单层高压容器,由于壁较厚,筒节一般采用热弯卷加热矫正成形。由于加热时产生的氧化皮危害较严重,会使钢板内外表面产生麻点和压坑,所以加热前需涂上一层耐高温、抗氧化的涂料,防止卷板时产生缺陷;同时热卷时,钢板在辊筒的压力下会使厚度减小,减薄量为原厚度的5%~6%,而长度略有增加,因此下料尺寸必须严格控制。始卷温度和终卷温度视材质而定。
三、容器的装配工艺
封头与筒体的装配可采用立装和卧装,当封头上无孔洞时,可先在封头外临时焊上起吊用吊耳(吊耳与封头材质相同),便于封头的吊装。卧装时如是小批量生产,一般采用手工装配的方法,如图1-8所示。装配时,在滚轮架上放置筒体,并使筒体端面伸出滚轮架外400~500mm,用起重机吊起封头,送至筒体端部,相互对准后横跨焊缝焊接一些刚性不太大的小板,以便固定封头与筒体间的相互位置。移去起重机后,用螺旋压板将环向焊缝逐段对准到适合的焊接位置,再用“П形马”横跨焊缝用点固焊固定。批量生产时,一般是采用专门的封头装配台来完成封头与筒体的装配。封头与筒体组装时,封头拼接焊缝与相邻筒节的纵焊缝也应错开一定的距离。

图1-8 封头简易装配法
1—封头;2—筒体;3—吊耳;4—吊钩;5—滚轮架;6—П形马
四、球罐的制作工艺的下料及成形方法
1.瓣片制造
球瓣的下料及成形方法较多。由于球面是不可展曲面,因此多采用近似展开下料。通过计算(常用球心角弧长计算法),放样展开为近似平面,然后压延成球面,再经简单修整即可成为一个瓣片,此法称为一次下料。还可以按计算周边适当放大,切成毛料,压延成形后进行二次划线,精确切割,此法称为二次下料,目前应用较广。如果采用数学放样,数控切割,可大大提高精度与加工效率。
对于球瓣的压形,一般直径小,曲率大的瓣片采用热压;直径大、曲率小的瓣片采用冷压。压制设备为水压机或油压机等。冷压球瓣采用局部成形法。具体操作方法是:钢板由平板状态进入初压时不要压到底,每次冲压坯料一部分,压一次移动一定距离,并留有一定的压延重叠面,这可避免工件局部产生过大的突变和折痕。当坯料返程移动时,可以压到底。
2.支柱制造
球罐支柱形式多样,以赤道正切式应用最为普遍。
赤道正切支柱多数是管状形式,小型球罐选用钢管制成;大型球罐由于支柱直径大而长,所以用钢板卷制拼焊而成。如考虑到制造、运输、安装的方便,大型球罐的支柱制造时分成上、下两部分,其上部支柱较短。上、下支柱的连接,是借助一短管,使安装时便于对拢。
支柱接口的划线、切割一般是在制成管状后进行。划线前应先进行接口放样制样板,其划线样板应以管子外壁为基准。支柱制好后要按要求进行检查,合格后还要在支柱下部的地方,约离其端部1500mm处取假定基准点,以供安装支柱时测量使用。
3.球罐的装配
球罐的装配方法很多,现场安装时,一般采用分瓣装配法。分瓣装配法是将瓣片或多瓣片直接吊装成整体的安装方法。分瓣装配法中以赤道带为基准来安装的方法运用得最为普遍。赤道带为基准的安装顺序是:先安装赤道带,以此向两端发展。它的特点是:由于赤道带先安装,其重力直接由支柱来支承,使球体利于定位,稳定性好,辅助工装少。图1-9所示是橘瓣式球罐分瓣装配法中以赤道带为基准的装配流程简图。

图1-9 橘瓣式球罐的装配流程图