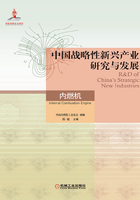
2.2 我国内燃机产业发展概况
内燃机行业在机械行业之中是跨行业、跨部门最多的行业之一,内燃机是交通运输、工程机械、农业机械、渔业船舶、国防装备、地质和石油钻机、旅游运动器械、园林机械和各种通用机械的主导动力设备,是各种配套产品的“心脏”,内燃机工业是重要的基础产业,对国防、工业、农业以及人民生活都有着重大的影响。
2.2.1 我国内燃机产业的特点
新中国成立以来,我国内燃机工业取得了长足进步,逐步建立了一个较为独立完整的制造体系,内燃机产品的技术水平有了很大提高,已成为全球内燃机生产和使用大国,成为支撑我国经济社会发展的重要基石和促进世界经济发展的重要力量。特别是改革开放后,内燃机行业根据国民经济发展的要求,不断对产品结构和企业结构进行调整,通过自行研制开发和引进国外先进技术,开发了一大批新产品;在国家出台有关排放法规和节能要求后,通过各种途径先后开发出一批满足国Ⅲ、国Ⅳ、国Ⅴ、国Ⅵ的发动机,生产出了一批可供汽车、摩托车、工程机械、船舶、农业机械、铁道内燃机车、内燃发电设备、石油钻机等产品选择配套的发动机机型,产品的结构趋向合理,产品质量和技术经济水平明显提高。
目前,我国内燃机产业主要具有以下特点:
1.使用领域量大面广
截至2015年,内燃机产品销量累计5707.33万台,总功率突破21.4亿kW,总功率比2015年同比增长1.14%,保有量达到4.5亿多台;我国农业人口众多,农业的经济形式以个体为主,因此对小型农业机械的需求量较大。单缸柴油机结构简单、易于使用和维修保养,被广泛配套于小型农业机械,我国产量居世界第一,2015年总产量276.34万台。我国地形复杂,山区多,农村道路建设相对落后,摩托车作为代步工具和小型运输工具得到了广泛应用,因此,我国摩托车产量较大,2015年产量超过2339.1万台,其中出口到发展中国家1000多万台。近年来,我国汽车工业得到高速发展。2015年乘用车用内燃机全年累计销量1866.33万台,商用车用内燃机全年累计销量301.16万台。此外,船用内燃机全年累计销量4.34万台;配套于我国农用机械用内燃机全年累计销量527.79万台;配套园林机械用内燃机全年累计销量399.16万台;配套于工程机械用内燃机全年累计销量42.22万台。由于很多地方的输配电配套措施不能满足经济发展需求,内燃发电机组在这些地区得到了广泛应用,发电机组用内燃机全年累计销量180.80万台。上述不同用途的内燃机构成了我国内燃机生产量大面广的特点。
2.产业链长
内燃机产品构成复杂,零部件数量多,涉及到冷却润滑、后处理、电子燃油喷射系统、缸体缸盖、曲柄连杆机构等精密的运动副和摩擦副,例如连杆活塞销,承受数千巴压力的喷嘴和出油阀偶件,原材料还涉及到抗高温高压、耐腐蚀、抗干扰、耐磨,还要满足轻量化等方面的要求。由于内燃机是配套主机的核心动力,要求具有完备的售后服务体系。这些构成了从原材料、零部件、设计、加工、制造、测试、生产以及配套和售后服务等各个环节,拉长了内燃机产品涉及的产业链。
内燃机产业链涉及的行业众多,具有较好的完整性和层次性。利用内燃机产业链长的优势,有利于降低内燃机制造企业的生产成本,有利于促进新兴企业的出现,有利于企业创新氛围的形成,有利于打造“区位品牌”,有利于区域经济的发展。
3.就业面广与消费拉动大
内燃机产业涉及到众多相关领域,广泛采用了信息技术、材料技术,并在研究、设计、试验、制造、销售及售后服务的全过程应用,已成为高新技术产业。现代内燃机已经融合了电子、化工和新型材料、新工艺等诸多高新技术,发展成为一个高科技产品,给直接和间接相关从业人员提供众多工作岗位。内燃机既是消费性产品也是投资性产品,拉动了国民经济增长,截至2015年年底,我国内燃机产品社会总保有量已达到4亿台,提供了直接就业机会逾40万人,如果加上相关服务业那就更多。2015年我国内燃机行业规模以上企业的主营业务收入快速增长,收入总额为2291.74亿元。
2.2.2 产业结构概况
内燃机整机主要分为汽油机和柴油机两部分。汽油机主要由乘用车和微型车用汽油机、小型通用汽油机、摩托车用汽油机三部分构成。柴油机的产业结构比较复杂,单缸机主要配套于小型农用机械,中小缸径的多缸柴油机主要配套于轻型运输车和大型农业机械,大缸径多缸高速柴油机主要配套于商用车和工程机械,大缸径多缸中低速柴油机主要配套于内河运输和发电机组。
零部件的生产企业按产品在内燃机上的功能实现专业化生产,包括热交换器行业、燃油系统、滤清器、水泵机油泵、缸套活塞环、排放后处理、增压器行业、曲柄连杆机构等。
1.汽油机
(1)车用汽油机 全国车用汽油机生产企业共有45家,除沈阳航天三菱汽车发动机制造有限公司外,其余44家企业都由汽车整车生产企业主导,其产销量超过97%。多缸汽油机企业全年累计销量1946.82万台。上汽通用五菱、东风日产、长城、长安福特、奇瑞等的同比增长更是达到了9.73%、48.14%、31.08%、60.45%、29.44%。上汽通用五菱、一汽-大众、上海大众动力总成、东风日产、重庆长安汽车等10家排在前列,其总体销量占行业销量比例为53.03%。
(2)摩托车发动机及通用小型汽油机 摩托车发动机行业集中度有所提高、全新车型增加、产品升级,对行业也带来了一定积极的影响。其中重庆隆鑫、力帆实业、大运、嘉陵、宗申、大长江及重庆银翔为行业龙头,实现批量外销,内销和外销比例6∶4。行业内规模以上企业50余家,前10家生产企业销量占50%以上。重庆地区生产企业众多且实力较强,形成了产业集聚优势。
通用小型汽油机行业,2015年小汽油机企业全年累计销量907.79万台,前五名企业为华盛、隆鑫、润通、中坚科技、林海,集中分布于重庆、山东、浙江、上海、福建和广东等地区,其中重庆地区产量约占总产量的40%。
2.柴油机
(1)车用柴油机 全国车用柴油机生产企业共有23家,独立发动机厂包括潍柴、玉柴及全柴等,其产销量占比达58%,其余为整车企业主导占比42%。合资品牌有3家,市场占有率为9.7%,自主品牌占有率为90.3%。销量前10位的市场集中度为85%,其中自主品牌有8家。多缸柴油机企业2015年全年累计销量357.12万台。玉柴、全柴、潍柴、锡柴等销量前10位的企业占总销量的65.79%。在多缸企业纷纷争夺的客车市场中,玉柴始终保持领先地位。广西玉柴机器集团有限公司、潍柴控股集团有限公司及中国一汽汽车集团股份有限公司年产销量达50万台以上,市场占有率为41.5%。车用柴油机产品在重型车用柴油机领域有很强的竞争力,而在轻型车中使用较少。
表 2-1 2015年国内前10位柴油机制造商销量情况

(2)非道路移动机械用发动机 作为内燃机生产大国,单缸柴油机是我国内燃机产业的一大特色,常柴股份有限公司、常发集团、江苏江动集团、全柴动力股份有限公司、山东华源莱动内燃机有限公司销量排名靠前,销量前5名企业市场占有率达到44.76%,以常州地区为主导的农用单缸柴油机在亚洲享有一定的声誉。
工程机械用和农业机械用多缸柴油机,其车辆生产厂大多也生产销售车用发动机,区域规模不突出,无特点,特别面对新的排放法规实施,面临技术升级的挑战,与国际知名发动机生产厂相比,产品竞争力弱。其中农业机械方面,中国一拖集团有限公司是特大型企业,其生产的发动机主要为轮式拖拉机、履带拖拉机配套。主流的工程机械配套发动机厂家主要包括道依茨、珀金斯、康明斯等品牌的发动机企业。
船用发动机中,1000kW以上大功率柴油机主要集中在淄柴、济柴、重庆康明斯等企业。大功率船用柴油机领域基本上是国外机型许可证生产,存在引进技术后,消化吸收再创新的问题。造船工业迅速发展而自主品牌主机供应迟缓的问题亟待解决。
机车用发动机主要由中国中车股份有限公司下属单位生产。中国中车是全球规模最大、品种最全、技术领先的轨道交通装备供应商,其大功率机车、铁路货车已经达到世界先进水平。
3.零部件
内燃机工业已经形成完整的零部件供应体系,包括基础原材料、燃油系统、增压系统、滤清器、排放后处理、冷却水泵和机油泵、电机电器、热交换器、气缸套和活塞环、曲轴和连杆、活塞和活塞销、轴瓦、进排气机构等系统部件和零件。生产企业有近700家,但是除水泵、机油泵外,市场集中度不高,与国外先进零部件技术水平相比仍有较大的差距。特别是先进燃油喷射系统等核心零部件,在技术创新和市场推广方面仍需加强。目前在增压器、燃油系统、后处理等关键零部件领域,行业正组织力量进行重点突破。
(1)燃油喷射系统 随着排放法规不断的升级,电控燃油系统已经成为新一代柴油机的必配装置。在排放法规的强力驱动下,此类产品装机量大幅增长。目前我国电控产品还无法完全满足车用发动机配套的需求,有超过10家企业在开发电控燃油系统(高压共轨系统等)以满足国Ⅳ及以后排放要求,如辽宁新风、湖南南岳电控及山东龙泵等。国家排放法规的实施以及产品升级换代的加快推进,为燃油系统行业发展带来了巨大的发展机会。但行业传统的产品与国外产品相比,丝毫不占优势,相反差距还相当大,行业面临更大的挑战。
由于燃油系统行业的集中程度越来越高,少数企业的经营状况影响着行业数据走向,以国内企业为主生产的传统机械产品几乎没有新的生存空间,而国外品牌的电控产品却供不应求。从统计资料上看,尽管行业还在发展,但国外品牌占据了半壁江山。2015年1月1日起,柴油车实施国Ⅳ排放标准。电控燃油系统产品(电控高压共轨系统、电控单体泵或组合式电控单体泵、电控高压分配泵)国内装机量比2014年有大幅增长。
我国目前电控产品还无法满足车用发动机的配套需求,虽然目前国内已有超过10家企业在开发电控燃油系统(高压共轨系统等)以满足国Ⅳ及以后排放要求。如一汽无锡泵所、辽宁新风、南岳电控、成都威特、龙口龙泵等单位都已投入相当力量开发自己的电控高压共轨系统,也取得了阶段性的成功。但是实际上还没有国内企业开发的电控高压共轨系统真正达到大批量生产和装机的阶段。在共轨系统生产中的关键技术以及稳定性、一致性、可靠性和成本等方面与德国博世(BOSCH)、日本电装(DENSO)等跨国公司相比有一定的差距。
(2)增压器及其系统 全球增压器市场排名前五位的生产厂商都在我国建立独资或者合资的研发和生产基地,如霍尼韦尔汽车零部件服务(上海)有限公司、博格华纳汽车零部件(宁波)有限公司、上海菱重增压器有限公司、长春富奥石川岛增压器有限公司、无锡康明斯涡轮增压技术有限公司,这些企业基本垄断了国内汽油发动机涡轮增压器市场。
国内自主品牌增压器企业与国际巨头的差距明显,主要集中在产能规模、研发实力、管理等方面。为主机厂配套的自主品牌企业形成“一超三强”的竞争态势。一超指湖南天雁,其产品以中、重型车配套为主;三强指康跃科技股份有限公司、潍坊富源增压器有限公司、宁波威孚天力增压器技术有限公司。目前,自主品牌增压器在华东、湖南及辽宁等地形成多个产业基地,初步形成产业集群。在华东地区,以康跃公司、富源公司、天力增压器技术有限公司为龙头,形成了集涡轮增压器及其零部件产品研发、应用、销售及配套为一体的研发生产基地,产品配套潍柴动力、上柴动力、玉柴动力、云内动力、长城汽车、北汽福田、天津雷沃、一拖集团、三一重工、江淮汽车等三十多家主机厂商;在湖南,以湖南天雁机械有限责任公司为代表,与玉柴、锡柴、潍柴、大柴等国内30余家主要发动机厂建立了稳定的配套和战略合作伙伴关系,增压器国内主机市场份额达到22%以上;在辽宁凤城地区,拥有增压器及配件企业120多家,生产各类增压器品种3000多种,年产量200余万台(套),占国内企业总产量的25%。凤城市生产的增压器及部件共为国内外20多家企业配套,出口30多个国家和地区。
凤城市在国内建立了唯一的省级汽车增压器产业技术创新战略联盟,全市有25家企业共同与10所著名高校和科研机构建立联合攻关产业技术联盟,进一步增强了产业技术创新能力。到目前,自主研发新产品达到1200多种,申请和授权的专利达到30多项,已形成比较完整的生产涡轮增压器产业链,具有较强的创新能力和产业竞争优势。建立了辽宁汽车增压器试验与检测中心,成为支撑凤城增压器集群快速发展的内动力,并建立了一套与产业集群相关联的产业研发中心、产品检测和企业孵化器为一体的产业创新服务体系,规范企业标准和生产管理。有效地引导和规范企业生产与管理,用现代检测手段修正企业技术创新路线和提高产品质量,加速产品研发和工艺创新,以达到与国内外主机厂融合和产品配套。
从2015年主机配套市场上看,仍然是外资和合资企业为主,博格华纳等四家外资企业年产量在100万台左右,但外资或合资企业有较大比例的产品出口到中国以外的市场,如康明斯约有30%的产品销售到中国以外的市场。国内企业中湖南天雁产量约60万台,康跃产量约36万台,天力、富源的产量均在30万台左右,英特迈、丰沃的产量在3万台左右,集中度呈现两极分化特点。国内市场上高端产品几乎100%由几家外资企业生产;中端产品市场外资和国内骨干企业各约占50%;低端产品主要由小规模企业生产。
(3)排放后处理系统 随着汽油车国Ⅲ法规和柴油车国Ⅲ、国Ⅳ法规的深入推行,尾气后处理市场面临较大机遇。乘用车三元催化剂领域,外资品牌占81.5%的市场份额,自主品牌只占18.5%。自主品牌中,无锡威孚力达、昆贵研、四川中自和安徽艾可蓝等几家形成了规模。
重型商用车方面主要使用SCR后处理技术,自主品牌占有68%的市场份额,包括无锡威孚、无锡凯龙、浙江银轮和天津亿利等厂家。高效SCR后处理和DPF等技术,国内企业与国外先进技术还有较大差距,有待突破。
自2013年7月1日,我国部分地区重型车开始执行国Ⅳ排放标准,重型商用车采用SCR系统在技术上是成熟的,2014年起大部分地区逐步执行国Ⅳ排放标准。2014年重型商用车销售量约83万辆(含大客车),而同期SCR系统的销量约35万套,占重型车销量的42%。生产SCR系统的企业主要有无锡凯龙、无锡威孚力达、浙江银轮和北京康明斯、天纳克等企业。
在国Ⅲ、国Ⅳ法规并行的背景下,取得如此成绩来之不易。但也应该看到,SCR系统所使用的尿素水溶液(添蓝)的加注问题仍然没有得到有效解决,实现尿素水溶液加油站配套加注及加强市场监管是SCR系统有效应用的必要条件,这也是后处理行业能否更好更快发展的关键。
经过近几年来多方面的不断努力,轻型车的国Ⅳ排放技术路线已经趋向明朗,即在柴油机使用共轨系统的前提下,一是EGR+DOC+POC(用于满足国Ⅳ排放标准);二是EGR+DPF(用于满足国Ⅳ和国Ⅴ排放标准)。
2015年1月1日起全国实行国Ⅳ排放标准,福田、江铃、庆铃、云内、锡柴等企业采用高压共轨燃油系统的后处理措施满足了排放标准。通常轻型车采用EGR+DOC+POC的技术路线,但环保部门和部分业内专家对此技术路线持有异议,认为DOC+POC技术路线只是一个过渡方案,对转化效率和可靠性有一定担忧。环保部门和部分业内专家认为,EGR+DOC+POC的技术路线中,应使用DPF替代POC,因为DPF的捕集效率更高,且欧美发达国家已成熟应用DPF捕集颗粒物,但考虑到我国的油品及国内DPF技术水平等因素,目前尚未见批量投入市场使用的DPF。在2014年生产的68万辆国Ⅳ排放标准轻型商用车中,国内后处理系统企业中无锡威孚力达配套32万辆,天纳克配套8万辆,依柯卡特配套6万辆,艾可蓝配套6万辆,康明斯配套4万辆,无锡凯龙配套3万辆车,佛吉亚等其他厂家配套9万辆。
EGR技术在轻中型商用车国Ⅲ以上排放技术路线中占据重要地位,2015年EGR生产约110万套,其中约68万套与DOC+POC配套使用,满足国Ⅳ排放要求。EGR的主要生产企业及产量是:无锡隆盛30万台、宜宾天瑞达20万台,浙江九隆10万台,此外还有常州星之路和天津益洁佳等企业5万台,外资企业主要有昆山皮尔博格8万台和宁波博格华纳30万台。EGR总供货量中内资企业占63.1%,外资企业占36.9%。
DPF技术是商用车解决PM问题的优选方案,且在美国已推广使用多年,但在我国却举步维艰,问题在于它的再生技术较复杂和碳化硅载体材料昂贵,在我国不易推广,因此前些年该项技术的研发和投入均严重不足,但近几年来电子控制技术进入商用车排放后处理领域使得DPF的再生技术有了较快发展,陶瓷载体DPF成为可能,另外钛酸铝DPF也已出现,此二种载体相较碳化硅而言成本可以较大幅度降低。因此可以预期在不久的将来,随着国Ⅳ、国Ⅴ排放标准的贯彻实施,以及DPF技术研发走向成熟,DPF技术将有更广泛的应用。当前,DPF技术已被应用于在用车改造市场中,其对PM控制有明显效果,是近期内解决城市PM问题的可行办法之一。
总体而言,国内从20世纪90年代初开始研发汽车尾气催化剂、载体、封装等尾气后处理技术,直至现在的SCR和DPF零部件及系统集成技术,国内企业得到了有效的发展、取得了一定的成绩,目前自主品牌催化剂企业实力较强、产量最大的无锡威孚力达和昆贵研,产业集中度较高(约占国产催化剂90%以上),但与外资企业相比,无论是市场占有率还是技术水平,在部分产品上还有一定差距,国家如何从产业政策上支持我国自主品牌汽车和零部件企业的发展,是一个急待解决的问题。
4.内燃机整机电控系统
电控系统由复杂精密的电器元件组成,在运行环境恶劣的内燃机上工作,影响其可靠性的关键因素主要有气候负荷、电器负荷、EMC负荷、机械负荷等。目前内燃机用电控系统技术被欧美发达国家所垄断,国外已经将可靠性的理念由后期的产品验证提前到产品开发过程,同时将试验作为开发重要环节正向推动开发过程。在开发过程中通过热仿真、机械仿真、EMC仿真建立基础开发平台,保证了其可靠性,同时降低了成本。目前国外电控系统可靠度达到了97%,电控系统产品使用寿命至少在15000h。
国内内燃机电控系统可靠性基础研究极其匮乏,在单一环境因素及组合环境因素作用下电控系统寿命曲线变化趋势的研究几近空白。目前国内通过常规模拟试验验证保证电控系统可靠性,这种方式试验效率低且成本高,无法得到环境对电控系统寿命的影响规律,不能形成对产品设计开发有指导性的技术支撑。目前国内电控系统可靠度约为90%,使用寿命约是国外同类产品的1/4。
国外电控技术成熟,博世、西门子、德尔福、电装等企业在电控系统领域具有很强技术实力。国内电控技术处于起步阶段,受技术等多方因素限制,高速高压电磁阀、喷油器、电子控制软件等核心技术受制于人。
5.再制造产业发展迅速
作为一种独具特色的新兴产业,已经成为制造业和服务业的重要组成部分。内燃机工业再制造生产能力、企业规模、技术装备水平等显著提升,初步建立内燃机再制造标准化体系和满足旧件回收要求的逆向物流体系。内燃机相关可再制造产品多达30余种。失效内燃机的缸体、缸盖等关键零部件以及增压器、发电机等主要配套件,多数为局部失效,通过成形、修复等再制造关键工艺技术,可在不改变形状和本体材质的情况下恢复其尺寸、精度和性能。与传统废金属回收利用处置方式相比,再制造能够回收失效产品所蕴含附加值的70%左右;与原始制造相比,再制造可节约能源消耗80%、节约材料70%以上,降低制造成本30%至50%。
目前市场上客户的认可度不够,用户对再制造产业还缺乏了解,消费习惯没有形成,市场认可与市场需求仍需大力培育。逆流回收是内燃机再制造的难点,回收旧件难。旧件是再制造企业的原料,没有原料就没法发展。修复技术是再制造产业区别于其他维修产业的关键。目前,国内的再制造联盟有80家成员单位。
2.2.3 产业地域分布情况
从表2-2中可以看出,内燃机产量占比超过10%的省(市)有4个,分别为吉林省、山东省、上海市和重庆市,占46.5%,前十位省(市)占全国总量的85.88%,按照地域划分,主要集中在华东、东北、华南和西北地区,地域规模优势不明显。
表2-2 2014年全国各省(市)内燃机产量及占比统计

(续)

2.2.4 资本或所有制结构情况
全国内燃机行业644家规模以上企业主要经济指标快报显示,2015年1—12月全国内燃机行业规模以上企业累计实现主营业务收入2291.74亿元。从全国内燃机行业规模以上企业不同控股企业实现主营业务收入看,2015年,集体控股企业、私人控股主营业务收入高于上年同期,同比分别增长1.16%、7.04%;国有控股企业、港澳台商控股、外商控股、其他控股企业主营业务收入低于上年同期,同比分别下降17.98%、22.41%、8.54%、4.04%。(表2-3)。
表2-3 2015年内燃机行业不同控股企业实现主营业务收入情况

2015年全国内燃机行业规模以上企业累计实现利润总额174.85亿元,同比下降9.54%,减少额为18.44亿元。从全国内燃机行业规模以上企业不同控股企业实现利润看,私人控股企业、其他控股企业利润总额高于上年同期,同比分别增长5.46%、35.91%;国有控股企业、集体控股企业、港澳台商控股企业、外商控股企业利润总额低于上年同期,同比分别下降33.49%、7.79%、13.88%、3.21%(具体见表2-4)。
表2-4 2015年内燃机行业不同控股企业实现利润总额情况

2.2.5 对外交流合作概况
改革开放30年来,我国内燃机行业通过对国外先进技术的引进和消化吸收,大幅度地提高了产品水平,增加了技术积累,各主要内燃机企业的自主开发能力得到了一定的提高。国外许多跨国公司将发动机生产基地转移到中国,并把在中国生产的国外品牌发动机出口到海外;同时国内企业的自主品牌发动机产品也增加了出口。
我国内燃机行业突出节能减排主题,坚持对外合作与交流,坚持引进技术和消化吸收兼容并蓄,以不断推进行业技术进步,尤其是提升内燃机节能减排技术的水平。内燃机行业的对外合作和技术引进呈现出如下特点:一是对外合作和技术引进瞄准了与国际先进水平保持同步水准的发动机技术,尤其是节能减排技术;二是引进产品更着重在市场需要填平补缺的先进产品;三是国内企业和跨国公司通过合资合作形式引进技术和产品的项目发展较快、增加较多。如:重型车用柴油机方面,上汽菲亚特红岩动力总成有限公司引进意大利菲亚特动力科技公司(FPT)依维柯重型汽车用柴油机;北汽福田与德国戴姆勒公司合作引进戴姆勒中、重型柴油机;广州日野汽车有限公司引进日野E13C重型车用柴油机等。轻型车用柴油机方面,东风朝阳柴油机有限公司引进美国万国公司GD3.0柴油机技术;北汽福田康明斯发动机有限公司引进美国康明斯2.8L、3.8L轻型柴油机;荣成华泰汽车有限公司引进意大利VM2.5L、3.5L柴油机等。天然气发动机,潍柴动力西港新能源发动机公司引进加拿大西港创新公司重型车用高压直喷LNG发动机和新能源动力系统等。
通过国际间的交流和合作研发,我国内燃机制造企业不仅获得到了先进技术和产品,更重要的是培养了科研骨干、学习了产品开发的全过程、掌握了先进的开发手段,大大增加了技术储备,为今后企业乃至内燃机全行业进一步发展自主开发和创新积累了宝贵的经验。
中国内燃机工业协会在2012年加入了国际内燃机工业协会,并在北京承办了2013年年会,促进了国内企业与国外同行的交流,方便行业企业及时了解国外主要国家和地区的技术、标准、法规动态。
2.2.6 行业发展环境概况
1.国内发展环境
目前我国仍将处于重要的战略转型发展机遇期,受国际金融危机引发全球经济不稳定和低速发展的影响,调整和优化经济结构,转变经济发展模式,将成为主体的经济形势,由此会推动我国的发展模式由粗放型经济增长向集约型经济增长方式转型,由规模扩张的工业化模式转变为质量提升的增长模式成为必然和主流。
我国汽车工业经过多年高速发展,其产量已居世界第一。我国将会继续通过消费政策的拉动,有效的扩大国内需求、特别是消费需求,汽车工业自身将会通过实现产品的技术进步和水平的提高,推动汽车产品有序的进入国际市场。中国汽车工业将会继续保持较快的发展速度,汽车产量的持续增长和消费必将对内燃机的产量增长提出新的需求,同时对内燃机动力的低耗能和低排放提出更高的要求。
我国会继续加快“西部大开发”的进程,会有一批以推进西部交通、能源等基本建设为主体的项目开工建设。国家规划实施的重大“战略性新兴产业”将带动一批基础设施的重大建设项目:包括大型能源基地的开发建设及其配套能源输送大通道的建设;高速铁路、新建铁路和高速公路、大型港口等交通运输基础设施的建设。伴随着国家城市化和新农村建设的推进步伐,会出现大量的居民住宅建设、社会主义新农村城镇化建设和农村道路建设等等。上述各类建设项目为工程机械、矿山机械、载重车辆及其配套的内燃机动力提供了一个非常广阔的市场。
未来五年是我国农业机械大发展的关键时期,提高农业装备水平和农机社会化服务体系建设、改善农业生产条件、增强农业综合生产能力、推进城镇化和加快新农村建设、调整优化城乡结构、拉动农村消费需求等,这些必将进一步带动面广量大的农机动力以及各种适合乡镇生活需求的内燃机动力的发展。
我国的国防现代化建设将持续稳定地发展。所需配套动力产品在品种和技术水平上必须及时跟上,以满足各种先进国防装备的需求。
内河航运、海洋渔业捕捞及远洋运输等船舶产业的发展为船用内燃机提供了更大的发展空间。休闲旅游产业以及低空飞行器的发展是国家战略性新兴产业之一,各类旅游、休闲、运动器械和低空飞行器将会有一个高速和高要求的发展态势,特别是游艇和低空小型飞机用高等级的先进发动机在目前以进口品牌为主的市场中,中国制造的产品将会面临由于质量的提升所带动而来的广阔市场需求。
21世纪以来,国际跨国公司采用了独资、收购中方合资股份等不同的方式在我国新建和扩建生产厂。特别是以汽车用内燃机为主导的主机和零部件企业,他们以持有的先进核心技术和能实现我国节能减排技术法规要求的优势,迅速构成了新时期下对我国内燃机行业的市场挤压。
我国将积极发展低碳经济,增强可持续发展能力。我国在国际上已经作了“将进一步加强节能、提高能效工作,争取到2020年单位国内生产总值二氧化碳排放比2005年有显著下降”的承诺。加快编制出台发展低碳经济、循环经济、节能减排、环境保护及资源型城市经济转型等规划,增加资源环境方面约束性指标。在实施上述计划的过程中,内燃机产品由于既是燃烧源,又是排放污染源的特性,全行业在节能减排国策中将肩负重大的历史责任和社会责任。
当前在我国一次能源的消耗结构中,内燃机产品年消耗我国60%以上的石油能源,降低产品的燃油消耗是内燃机动力的核心技术指标和首选商业指标。今后开发具有竞争力的节能产品,必须从一般性被动研究转向应用型主动研究,内燃机的节能工作,将作为主导命题,贯彻至科研开发和产业应用全过程。开展高效燃用替代燃料的研究,也将成为我国今后相当长时期内的工作主题和核心。
技术创新是提高产业核心竞争力、提升产品技术平台的动力。内燃机行业应抓住有利机遇,以增强科技创新能力为目标,努力争取在内燃机产品高新技术领域取得新的突破,并以此提升产业优势,优化整体产业结构。
近年来,民营资本在我国内燃机工业中发挥着不可或缺的重要作用,一些民营企业做出了很大成绩,具备了一定的规模和特色,行业将继续支持和鼓励民营资本注入内燃机整机和零部件企业,使之成为提高产品技术水平和质量,推动内燃机行业发展的一支重要力量。
我国内燃机经过多年的积累和发展,形成了一定的能力和基础,虽然和欧美日发达国家水平还有差距,但差距在缩小,为此结合国家“一带一路”战略,可以实施走出去战略(投资、海外建厂、技术输出等)。
2.国际发展环境
随着经济全球化的发展,我国内燃机产品逐步融入世界内燃机市场体系。首先,我国内燃机及其各类配套主机在保持稳定快速发展的前提下,产品进入世界市场的比重会逐步增加。同时,中国也成为世界跨国集团最为关注的市场。中国内燃机制造企业和世界各国强手在我国本土上的竞争,已等同于在国际市场上的竞争。
内燃机是当今热效率最高、应用最广的移动机械用动力。其快速的发展和巨大的社会保有量同时也产生了一系列严重的资源和环保问题,在全球50%以上的石油资源被内燃机消耗掉的同时,其燃烧后排放的大量CO2温室效应气体和以颗粒为主的各种有害气体,对环境和生态平衡产生了严重影响,尤其CO2减排已经成为国际社会首要面临的问题。
随着电子技术、材料工业、精细化工、精密制造和测试技术等新技术的发展,为现代内燃机发展成为一种低耗能、低排放的高新技术产品打下了很好的基础。尽管国内外很多研究工作者一直在研究、寻找替代内燃机的新型动力,但至今尚未找到能完全替代现有往复活塞式内燃机的动力装置。预计在今后较长的一段时期,人类目前探索和研究的各种新能源动力还无法大规模替代内燃机的位置。因此,内燃机作为实施节能减排最有潜力的产品,进一步研发先进的汽油机和柴油机,努力减少燃油消耗和CO2排放,是最有效和现实的途径。一方面大力研究发展新能源动力,另一方面在传统动力领域坚持进行大量行之有效的改进和提高,同时积极发展替代燃料在内燃机上的研究和推广应用,实行内燃机工业“三管齐下”的节能减排发展方针,最终实现节约能源和CO2减排的总目标,这在国内外内燃机和汽车等相关工业界已达成共识。
为满足市场需求和社会需求,保证内燃机动力的优势竞争地位,全球内燃机动力下一个发展周期的重点是产品动力性能最优化、经济性能最节约、环保性能最绿色。从可持续发展的战略高度上看,内燃机产品节能是产业持续发展的永恒主题,即使全部实现混合动力的节能目标,50%以上的努力工作还要集中在内燃机上。
进入21世纪以来,在新能源动力的开发热潮中,基于对未来各种新能源动力和内燃机动力的技术发展和市场应用前景的比较分析,国际内燃机工业发达国家仍大力致力于内燃机高新技术的创新开发,既追求内燃机动力性、经济性和可靠性的最优化,又要使环境负荷最小化,从而达到兼顾经济增长和节能环保双重远景的实现。当今各大跨国集团和公司利用各种高科技手段在研究开发内燃机新技术和新产品方面都取得了很多重大突破性的成果。