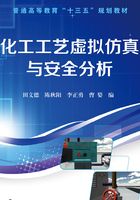
3.3 操作安全
单元操作在化工中占主要地位,决定整个生产的经济效益,在化工生产中单元操作的设备费用和操作费用一般可占到80%~90%,可以说没有单元操作就没有化工生产过程。同样没有单元操作的安全,也就没有化工生产的安全。
本节主要从安全角度介绍化工单元操作过程中应注意的安全问题,内容包括设备运行前的安全处理技术、设备启停过程中的安全、阀门使用安全、管线安全以及其他的安全生产措施等。
3.3.1 设备运行前的钝化防爆技术
设备是化工生产正常运行不可缺少的部分,设备的正常运转直接影响整个化工生产过程。化工装置在运行前通常对设备先进行“钝化”,钝化的对象一般是指生产过程中涉及有易燃易爆的物料,物料包括原料、产品、副产品以及中间产品。钝化目的主要是降低设备中空气的含量(主要是氧含量),通常使其在0.5%以下,使空气和物料形成的气体爆炸混合物浓度低于爆炸混合物的下限,降低设备发生爆炸的概率。
设备钝化防爆技术根据设备的运行情况(通常考察的因素是压力)分为真空钝化、压力钝化以及吹扫钝化。
(1)真空钝化
真空钝化技术主要针对的是化工生产过程中设计压力为负压的设备。通过真空机组作用于设备上,设备内气体被抽出,设备压力小于大气压,形成负压的操作技术。
真空钝化技术根据真空压力的不同可以分为粗真空(101.3kPa~1333Pa)、低真空(1333~0.1333Pa)、高真空(0.1333~1.333×10-6Pa)、超真空(<1.333×10-6Pa)。化工行业中常用到的是粗真空技术,主要用来抽出空气和其他具有腐蚀性、不溶于水、允许含有少量固体颗粒的气体。
(2)压力钝化
压力钝化防爆技术是指利用惰性组分(如氮气)经加压处理进入设备排除空气,使设备无法形成爆炸性混合物的操作技术。压力钝化防爆技术在设备运行前、设备生产运行过程中以及检修过程中都有应用,是设备钝化防爆技术应用最多的一种。压力钝化防爆技术应用的场合可以是带压设备或者是真空设备,压力钝化防爆技术使用时是带压操作,所以在使用时需要注意安全,一般会在设备或者管线上加装安全防护措施(如安全阀等)。
(3)吹扫钝化
吹扫钝化防爆技术主要用在不易发生爆炸或者压力不是很高的场所。应该算压力钝化防爆技术中的一种。
3.3.2 设备的启停
化工装置中设备的启停有两种:一种是正常情况下的启停,比如原始开车和生产检修时的设备启停;另一种是紧急状态下或者事故状态下设备的启停。两种情况下设备的启停方式是相同的,步骤上略有差异,像原始开车时设备开启步骤比较复杂,开车前需要编制开车程序说明,包含的内容有检查、水压试验和气密性试验要求、吹扫及干燥、注意事项等等。检修及事故时的设备启停不需要编制开车说明,程序相对简单一些。
化工设备根据其功能划分为输送设备、储存容器、换热器、塔器、反应器等,不同设备的启停方式各有不同。具体开停方式如下。
3.3.2.1 输送设备
输送设备:输送液体的设备称为泵,输送气体的设备称为风机,风机根据设备输出压力的大小分为:通风机(全压小于11.375kPa)、鼓风机(11.375~241.6kPa)、压缩机(全压大于241.6kPa)。离心泵是化工生产中应用最广泛的输送设备,以离心泵为例讲解输送设备的启停过程。
(1)泵的开启
①泵的检查 检查离心泵安装是否稳固,轴承能否正常转动,确认正常后进行灌泵,查看轴封装置密封腔内是否充满液体。
②泵出口管线检查 检查泵进出口管线上的阀门、压力表、流量计等管件的法兰连接是否正常,检查无误后关闭进出口管线上的压力表。
③启动泵 泵及进出口管线检查完之后,启动电动机。刚开始时采用手动,点动开启,查看泵的运转,防止电机倒转。泵启动后打开进出管线的压力表,并缓慢调节出口阀门开度,调节离心泵流量,流量稳定后检查泵进出口压力表、出口管线流量指示是否正常。
(2)停泵
离心泵的关闭比较简单,关闭出口阀门以后关闭泵的开关即可。但是在停泵时应注意:若长时间停泵,在关闭出口阀门之后需要打开泵进口管线设置的排凝阀放净泵壳体及管线中的料液。
3.3.2.2 换热设备
换热设备按照结构划分主要有管壳式换热器和板式换热器,化工生产中最常见的换热器结构是管壳式换热器。换热器的启停可概括如下。
(1)换热器的开启
①首先将换热器设置的放空阀、排净阀打开,将换热器内的气体或者液体排净,以免因气体或者液体的存在引起水击或者气堵现象,然后关闭排净阀门,打开排空阀。
②先通入冷流体,如果冷流体是液体,缓慢注入,待液体充满整个换热器时,关闭放气阀,然后再缓慢地通入热流体,以免因为热效应造成管束的断裂或破损。
③在换热器温度上升过程中,对外部连接的螺栓应重新进行紧固,防止密封不严产生泄漏。
(2)换热器的停用
一般先切断热物料进料,经过一段时间换热使温度降低到一定范围内,然后再切断冷物流的进料,这样可以保证换热器的停用安全。如果是长时间的停用应打开换热器上的排净阀门、排空阀门将物料全部排净,为检查做准备。
3.3.2.3 分离设备
现代化工分离设备主要还是塔类,用于分离气、液或者液、液混合物。根据塔内气、液接触构件的形式,塔类设备可以分为板式塔和填料塔。对于两种不同形式的塔,其启停过程也不一样。
(1)板式塔的开启
①先进料,并控制塔釜液位在1/3~2/3左右,达到液位后切断进料,停止进料;
②开启塔顶冷凝器,通入冷流体循环,然后对塔釜物料进行加热,往塔釜再沸器通入热物料(通常为饱和蒸汽),使塔内有上升的气体,蒸汽阀门的开度不要太大,因为刚开始阶段要求全回流,不出料。
③待塔的各项参数指标稳定后,产品合格后打开进料,慢慢调节出料,使塔设备正常运转,当达到稳定的连续进料和连续采出合格产品时塔设备才算正常开启。
(2)板式塔的停车
首先切断进料,在塔内循环的物料合格后,塔顶、塔釜排出塔内物料,塔釜再沸器在排料的过程中慢慢减少蒸汽用量,在塔釜物料排净后切断蒸汽进料,随着塔釜蒸汽的减少,上升气相越来越少,当塔顶无气相物流时,切断塔顶冷凝物流的进料,将冷凝的物料全部排入事故槽,待塔顶塔釜物料全部排完,一般还要将塔内压力释放到常压,压力释放完成后板式塔停车完毕。总体的停车顺序是停进料、停出料、停加热、停冷凝、泄压。
(3)吸收塔的启动
吸收塔的启动首先需要将吸收塔内压力提升起来,随后将吸收剂循环起来,一般吸收剂的循环都是利用吸收剂循环泵完成的。然后调节塔顶吸收剂的量至规定的要求,严格按照液气比要求进料。同时注意塔釜液位,调节塔釜液位至规定的要求。待吸收塔各监测参数正常后通入混合气相,开始时气相量不要开太大,防止排放太多不合格尾气,气相量调节至规定要求,当吸收塔顶尾气符合规定要求后,按此流量进行生产。吸收塔的启动完成。
(4)吸收塔的停车
吸收塔停车前需要将塔上设置的连锁控制改为手动控制,首先是切断进料,待到无上升气相时切断吸收剂进料及其他的辅助进料,最后泄压至常压状态。
3.3.2.4 反应器的启停
反应器是化工生产的关键设备,由于化学反应多样化,工业生产上反应器的类型及分类方式也有很多,比如按照操作方式的不同分为连续式反应器和间歇反应器,按结构的不同分为釜式反应器、管式反应器、塔式反应器、固定床、流化床反应器等,按物料相态又分为均相和非均相反应器等。不同反应器的启停方式各有不同,本文以最常见的釜式反应器为例叙述反应器的启停方法。
(1)釜式反应器的启动
反应器启动前检查设备仪表及管线是否正常,设备是否完好,检查完成后开始进料,按照开车程序里的进料速度进料,当釜内液位达到搅拌要求后开启搅拌装置,若是吸热反应,需要打开蒸汽或者导热油介质进行升温,切记不可急速升温,以免造成反应失控的局面;若反应是放热反应将冷凝介质打开,移走反应放出的热量。两种方式都需要控制反应温度并维持,反应釜各项参数正常后反应一段时间,物料合格后反应器成功启动。
(2)釜式反应器的停车
停车时首先切断进料管线的阀门停止进料,维持反应釜规定的反应时间要求使反应结束,判断标准一般是看温度的变化。对于放热反应冷却介质需要继续冷却至常温,然后关闭冷却介质的进料阀门,停止搅拌器打开放料阀,待放料结束后再关闭放料阀。对于吸热反应,反应结束后停止加热,釜温慢慢降低,降低至规定温度后停搅拌开始放料,放料结束关闭放料阀。
化工生产中涉及的典型设备主要是离心泵、反应釜、换热器、精馏塔等,设备的正常启停如上所述。生产过程中会遇到一些紧急情况,如某个设备损坏、电气设备电源发生故障,或者仪表失灵不能正常显示要测定的各项指标,这时的设备停车称为紧急停车,它与正常停车不同,会影响到整个装置的生产任务,甚至发生危险。遇到紧急停车的情况应按照事先编制的事故紧急处理措施进行处置,装置在设计时设置的安全措施可以有效降低紧急停车造成的损失。处理措施如下:
①重要的压力设备设置有安全阀门,压力超压后自动开启泄压;
②设置有紧急停车按钮,重要仪表仍能正常显示,冷却介质正常进料,加热介质切断进料,装置停车后关闭电源排除遇到的问题。
3.3.3 设备运行中阀门的使用和维护
阀门是在流体系统中用来控制流体的方向、压力、流量的装置,是使配管和设备内介质流动或者停止并能控制其流量的装置。在化工装置中,阀门起着控制全部生产设备和工艺流程正常运转的作用。因此对阀门的选用、安装、使用、保养等都必须进行认真负责地工作。阀门的选用可以参考实用阀门设计手册。
阀门的功能有很多,阀门可以接通或者截断介质,防止介质倒流,调节介质压力、流量,分离、混合或分配介质,防止介质压力超过规定数值,保证管道或者设备安全运行等功能。实现不同功能需正确选择阀门类型。
阀门分类繁多,根据用途和作用可以分为截断类阀门(如闸阀、截止阀、球阀、蝶阀、旋塞阀、隔膜阀等):主要用于截断或者接通介质流;止回类(各种结构的止回阀):用于阻止介质倒流;调节类(减压阀、调压阀、节流阀):调节介质的压力和流量;安全类(安全阀):主要用于保证管道系统和设备的安全运行;特殊用途阀门如疏水阀、放空阀、排污阀等。按压力分真空阀、低压阀、中压阀、高压阀、超高压阀。按温度分高温阀、中温阀、常温阀、低温阀、超低温阀。按材料分非金属阀、金属材料阀。通用分类法分为闸阀、截止阀、隔膜阀、仪表阀、柱塞阀、节流阀、球阀、止回阀、底阀、蝶阀、减压阀、安全阀、疏水阀、调节阀、过滤阀等。其中通用分类法是目前国际、国内最常用的分类方法。
表征阀门的主要参数有公称压力和公称直径、工作温度和工作压力,其他参数还有适用介质、试验压力、阀门密封副、阀门填料函等,其中公称压力用字母加数字表示如PN25,表示公称压力2.5MPa,公称直径用“DN”表示。阀门的标识以说明阀门类别、驱动形式、连接方式、结构形式、密封面和衬里材料、公称压力及阀体材料7个单元组成,阀门具体编号参见阀门型号编制方法、阀门标号说明。
(1)阀门的使用
①识别阀门的操作方向。一般规定:手轮的逆时针方向为开,顺时针方向为闭。
②开关旋塞阀、球阀和蝶阀时,必须看清楚阀芯所处状态,避免操作失误。
③开关暗杆闸阀时,应按标记进行操作。
④开启蒸汽阀门时,应先微开,以汽缓热设备与管路,并排放冷凝水,以免产生水锤现象和发生爆破事故。
⑤开启设有旁通阀的大口径阀门时,应先开旁通阀,而后再开主阀。
⑥开启长期未用阀门时,应先擦拭阀杆和松动填料压盖,然后加润滑油。再以缓慢速度旋转手轮,切忌用锤敲击。以防零件损坏或介质喷出伤人。
⑦开关大直径阀门时,应由两人操作,操作时应用扳手,不能用大锤敲击,以免零件损坏或卡死。
⑧关闭高温阀门时,操作人员不要立即离去,待一段时间后,再去紧闭一下,这样可使密封面严紧不留缝隙,否则高速气流会冲刷坏密封面而造成泄漏。
⑨当阀门全开时,应将手轮倒转少许,使螺纹之间严紧,以免松动损坏。
(2)阀门的维护
阀门与其他机械产品一样,也需要维护保养,这项工作做得好可以延长阀门的使用寿命。具体维护内容如下。
①经常擦拭阀门的螺纹部位,保持清洁和润滑良好,使传动零件动作灵活,无卡涩现象。阀杆螺纹经常与阀杆螺母摩擦,要涂一点黄甘油、二硫化钼或石墨粉,起润滑作用。
②阀杆,特别是螺纹部分,要经常擦拭,对已经被尘土弄脏的润滑剂要换成新的,因为尘土中含有硬杂物容易磨损螺纹和阀杆表面,影响阀门使用寿命。
③经常检查填料处有无泄漏,如有泄漏,应适当拧紧压盖螺母,或增添填料,如填料硬化变质,应更换新填料。
④齿轮传动阀门,要按时对变速箱添加润滑油,要经常保持阀门的清洁,要经常检查并保持阀门零部件完整性。
⑤对于减压阀应经常观察减压性能,减压值变动大时,应解体检修。
⑥对于安全阀要经常检查是否泄漏和挂污,发现后及时解决,每年校验其灵敏度。
⑦不经常启闭的阀门,也要定期转动手轮,对阀杆螺纹添加润滑剂,以防咬住。
⑧安装在露天或无防寒措施场所的阀门,应注意防寒保暖。冬季要检查保温阀门保温层是否完好。停用阀门要将内部积存介质排净,以防冻坏。
⑨室外阀门,要对阀杆加保护套,以防雨、雪、尘土锈污。
⑩不需保温阀门要定期进行防腐。
不要依靠阀门支持其他重物,不要在阀门上站立。
3.3.4 设备中的排液(水)
化工生产中涉及排液的设备主要有容器、泵及换热器。设备排液目的主要是为了安全和设备功能以及检修的需要考虑,另外是装置运行前的水压试验中水的排出,不同类型设备排液口一般都设计在设备底部排液。
(1)容器
化工容器是指化工生产中所用的各种设备外部壳体的总称。如反应釜、塔器、热交换器、各类贮罐、贮槽等均具有外壳,这个外壳就是容器。化工行业中许多容器设置有排液口(或者为排污口),这个主要与容器储存的物料物理化学性质有关以及容器出料口位置有关。
反应容器:反应容器是物料进行化学物理反应的场所。若反应容器为底部出料,一般不设计排污口,反应后的产物及杂质从出料口排出,反应容器不作处理。若反应容器出料口位置设计在容器顶部,此时在容器底部设计排污口,主要排出物料反应后生成水及其他物质。当产品比重比水轻且不溶于水,产品由反应釜上部出料(通常是负压操作),底部设置排污口用于排出反应生成的水,目的是减少后续分离过程的负荷。反应结束后开启排污口阀门排出水及其他物质。
贮罐:贮罐按照物料性质分原料罐、中间产品罐、产品罐,分别用于储存原料、中间产品和产品。贮罐类容器底部一般设计有排液口,其位置低于出料口。用于排出贮罐内沉淀下来的杂质,另外在设备或管线及附件出料需要检修时需要排净贮罐中物料。
(2)泵
泵是指输送液体的设备的总称。在泵的进出口管线均设计有排液口,这主要是出于安全和检修考虑。泵属于动设备,在生产过程中容器发生泄漏或者损坏,在发生事故后需要进行维修,维修前需要将泵体内的物料排净,排净的方法是在泵进口管线下部设计排液口,可以排净泵内物料。泵出口管线设置有止回阀防止物料倒流,设置有压力表监视泵的运行状态,若压力表失灵需要检修需排净出料口物料,这是在止回阀后安装排液口的目的。检修时一定是在泵停止运转后进行。
(3)换热器
换热器是用来进行物料热量交换的设备。涉及的物料是气相或者液相,在设计换热器时都设计有排凝口。目的主要是为了保证换热器的换热效率。换热器排凝阀一般设计时管径不是很大,DN20~40之间占大多数。换热器进出口管线一般设计温度监测,温度异常时说明换热效果降低,此时可以打开排凝阀和换热器上部的排空阀释放物料,可以提高换热效果。
3.3.5 设备运行中管线跑料的处理
管线跑冒滴漏是指工艺介质在空间泄漏或者一种介质通过连通的管道或者设备进入另一种介质内的异常状况。化工生产中管线的跑冒滴漏问题经常发生,这主要与化工生产特点和物料性质有关。化工生产涉及高温高压的管线非常多,造成跑冒滴漏在所难免,还有就是管线输送物料有的具有腐蚀性,也会造成管线泄漏。
化工生产涉及的物料大多是易燃易爆、有毒有腐蚀性,易燃易爆物料发生跑冒滴漏可能导致火灾、爆炸等恶性事件;有毒有害物质“跑冒滴漏”可引起职业病、中毒、窒息、死亡等事故,因此被化工企业非常重视。针对不同情形的“跑冒滴漏”处理措施应因地制宜。
(1)跑
指的是化工物料从容器或者管道中溢出。表现形式主要是管道或者设备破裂、进出口阀门开关失灵。针对这种情形的处理措施:
①涉及的物料危险性小且泄漏不严重,可在装置检修时进行维修或者更换;
②涉及的物料是危险物料时,通常需要停车更换管线、设备或者是阀门。
(2)冒
主要是指容器里的物料冒出来。主要表现形式是容器进出口流量调节阀门没有控制好,盛装物料时阀门该关闭的没有关闭,应该开启的阀门没有开启,致使物料溢出设备。针对这种情形的处理措施:
人工开或者关阀门,然后检查确认阀门状态是否损坏,损坏的阀门进行更换,未损坏应加强维护。若是人为事故需要加强安全教育。
(3)滴
在化工生产过程中,管道与管道、管道与容器、管道与阀门等接口处,以及管道、容器、阀件等自身密闭性能差造成物料渗漏。针对这种情形的处理措施:
①如果是法兰紧固件松动或者密封垫片损坏,需要拧紧紧固件或者更换垫片;
②如果是设备或者管线及附件自身密闭性造成,需更换。
(4)漏
一般是指容器的密闭性不好或者是阀门开关未到位、阀体存在缺陷,导致液体或气体从缝隙或裂口处流出。针对此情形的处理措施:
①如果是容器密封性不好引起的,需更换设备;
②如果是阀门开关不到位,人工关或者开启阀门,并加强安全管理;
③如果阀门存在缺陷,需更换阀门。
3.3.6 劳保用品的正确使用
劳动防护用品是指由生产单位为从业人员配给,使其在劳动过程中免遭或者减轻事故伤害及职业危害的个人防护装备,它是保护劳动者在生产过程中的人身安全与健康所必备的一种防御性装备,对于减少职业危害起着相当重要的作用。
化工装置配备防化服、空气呼吸器、防毒面具、滤毒罐和安全防护眼镜等劳动防护用品见表3-4;在处理或检修有可能有酸、碱物质喷溅的场所,必须穿戴全身防护衣,戴耐酸碱手套,同时佩戴防护面罩或防护眼镜。凡有可能泄漏可燃物料的部位设置固定式危险气体检测报警器。
表3-4 个人防护用品配置情况一览表

3.3.7 安全生产措施的应用
安全生产措施从系统安全角度分析,安全措施主要有三项内容:预防事故措施、控制事故措施、减少与消除事故影响设施。
安全生产措施设计的原则如下。
①清除:采用无危害工艺技术和遥控自动化技术。
②预防:当清除危害有困难时,采用预防措施。
③减弱:无法消除和难以预防危害时,采用减少危害的措施。
④隔离:无法消除、预防、减弱危害的情况下,应将人与危害因素隔开,把不允许共存的物料分开。
⑤联锁:操作失误、仪表失控、突发设备事故,应通过联锁装置终止危险、危害因素的发生。
⑥警告:易发生危险、危害的场所,应设置安全标志及声光报警装置。
3.3.7.1 预防事故措施
工艺过程采取防泄漏、防火、防爆、防尘、防毒、防腐蚀等主要措施。
(1)防泄漏措施
易燃易爆物质,防泄漏措施按以下原则实施:管道、设备选材合理。根据物料性质、操作温度及压力等因素选择合适的材料;危险物料及其余物料管道除阀门、设备管口等处用法兰连接外,其余均采用焊接,根据《工业金属管道设计规范》(GB 50316—2008)要求对焊接部位进行无损检测。各单元安装完毕后,均严格按照规范进行水压或者气压以及防泄漏试验,一旦发现泄漏问题,立即检修,杜绝输送介质的设备、管路发生跑、冒、滴、漏现象。
(2)防火、防爆设施
①易燃易爆放空管道设置阻火呼吸阀。
②压力设备一般设计液位计、温度计、压力表、低液位报警器、高液位报警器和高高液位自动联锁切断进料装置,设备出入口管道设置了紧急切断阀。
③根据装置设置蒸汽灭火和氮气吹扫措施。
④涉及易燃易爆危险物料的装卸采用万向节充装系统。
⑤对于各设备、管路上的法兰、密封垫等均严格按照规范要求选用。管道除阀门、设备管口等处用法兰连接外,其余均采用焊接。杜绝输送爆炸危险介质的设备、管路发生跑、冒、滴、漏现象。设备及其基础,管道及其支、吊架和基础,采用非燃烧材料;设备和管道的保温层,采用岩棉等非燃烧材料。管道法兰设置跨接导线。放空、安全阀管口高出10m范围内的平台或建筑物3.5m以上,同时位于排放口水平10m以外斜上45°的范围内不布置平台或建筑物。
⑥生产装置区为框架结构露天布置,以自然通风为主。若生产装置为厂房且属于甲、乙类厂房,除基本通风外,应按照国家标准规范设置机械通风或者事故通风。
装置机柜室、空气制氮机、变配电所应按GB 50019—2003第5.3.10设置机械通风设施,排风量不应小于每小时1次换气。空压制氮站通风换气次数按照GB 16912—2008第4.11.3条执行,并设置氧含量检测报警装置。
⑦对可燃液体输送管道进行防静电接地和跨接。
⑧距生产装置、罐区30m以内的管沟、电缆沟、电缆隧道,采取防止可燃气体窜入和积聚的措施,并用砂填埋充实等;电缆沟通入变配电室、控制室的墙洞处,进行填实、密封。厂区排水沟进出各装置区设置水封,水沟进出厂界设置水封等设施,防止因厂外火源、火花等沿地沟造成起火,引发重大恶性事故。
(3)防毒、防尘
①生产过程中原料涉及氮气等窒息性气体、有毒介质时,事故状态可造成有毒、窒息环境,应重点防范。
②在生产过程中,工艺参数最好选择常压或低压操作条件,减少有毒物料的泄漏。为防止腐蚀,使泄漏的可能性降至最低,对于设备材质的选择非常严格。对输送有毒物料的设备、管路上的排液、排气管设置盲板、丝堵,杜绝跑、冒、滴、漏现象。
③重点工艺参数采用报警及安全联锁,使反应温度、压力、液位等始终处于自动监控状态,生产过程采用自动控制,使作业人员不接触或少接触有毒物料,防止误操作造成中毒事故。
④在易产生及使用粉尘的工段均佩戴防尘口罩和防护眼镜。在这些场所设置机械排风装置,并设置淋洗洗眼器。
除了以上这些针对性的措施,在生产过程中还应该注意安全管理措施,必须对员工进行全面的、系统的安全维护培训,并执行良好的管理、监督。再完美的设计也不可能避免人为的疏忽、错误引起的损害,不断提高操作人员的素质是降低危险性、避免事故发生和扩大的有效措施之一。安全管理对策措施,简而言之就是建立安全管理制度、提高操作人员和管理人员的素质。具体的内容包括安全培训、检查和维修制度、定期安全检查、建立救护组织机构、制定事故应急计划等。
(4)防腐蚀措施
涉及液碱、硫酸等腐蚀性介质,所有涉及腐蚀性介质的建、构筑物均应按照《工业建筑防腐蚀设计规范》GB 50046—2008进行防腐设计。
根据其生产环境、作用部位、对建筑材料长期作用下的腐蚀程度等条件,并根据《工业建筑防腐蚀设计规范》、《化工建筑涂装设计规定》的要求进行防腐设计。
(5)正常工况下危险物料的安全控制措施
①依据《重点监管的危险化学品名录》(2013年完整版)判定,化工装置中哪些物料属于重点监管危险化学品,按照重点监管的危险化学品进行管理。
②蒸馏工艺按照《关于印发蒸馏系统安全控制指导意见的通知》(鲁安监发[2011]140号)、《关于推进化工企业自动化控制及安全联锁技术改造工作的意见》(鲁安监发[2008]149号)相关规定设置自动控制及安全联锁系统,按规定设置相应的仪表、报警讯号、自动联锁保护系统或紧急停车措施。
③危险工艺应按照《重点监管危险化工工艺目录》(2013年完整版)、鲁安监发[2009]108号、鲁安监发[2010]35号等相关规定设置自动控制及安全联锁系统,按规定设置相应的仪表、报警讯号、自动联锁保护系统或紧急停车措施;设计重点控制的工艺参数和安全控制方案。
3.3.7.2 控制事故设施
主要是泄压和止逆设施。
①在塔器、反应器、回流罐、球罐、分液罐等压力容器上应设置安全阀,防止设备超压。
②对连续使用的氮气管线应设置止回阀,防止物料反窜。在可燃液体、压缩机的出口管道上均设置止回阀,防止物料倒流造成事故。
③离心打料泵出口均设止回阀,防止物料倒流冲击叶轮。所有放空管道的设置均严格执行《石油化工企业设计防火规范》GB 50160—2008第5.5.11条:放空管的高度(见图3-2)符合下列规定。

图3-2 可燃气体排气口、放空管高度示意图
注:阴影部分为平台或建筑物的设置范围
a.连续排放的排气筒顶或放空管应高出20m范围内的平面或建筑物顶3.5m以上,位于排放口水平20m以外斜上45°的范围内不宜布置平台或建筑物;
b.间歇排放的排气筒顶或放空管口应高出10m范围内的平台或建筑物顶3.5m以上,位于排放口水平10m以外斜上45°的范围内不宜布置平台或建筑物;
c.安全阀排放管口不得朝向临近设备或有人通过的地方,排放管口应高出8m范围内的平台或建筑物顶3m以上。
3.3.7.3 减少与消除事故影响设施
(1)防止火灾蔓延设施
①根据装置火灾危险性,确定装置内是否应设置框架及各层设有软管站?软管站的保护半径不大于15m,各软管站应配置氮气、蒸汽、工业水及装置空气管线,以便于设备吹扫、置换和灭火。
②为了防止火灾蔓延,在建筑物等排水出口设置水封井,出装置设水封、出罐区设置水封井及阀门井,水封高度不小于250mm。
③通过对生产工艺过程中所涉及主要物料(原料、中间产品及产品)的危险有害因素的分析。按标准设计厂区各装置建、构筑物耐火等级、防火间距及防火、防爆措施。
(2)灭火设施
根据《石油化工企业设计防火规范》(GB 50160—2008),确定装置的火灾危险性分类,根据危险程度相应设计消防,确定是否设计水消防、蒸汽消防、移动灭火器材和火灾报警系统等必要设施。