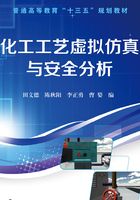
第2章 控制系统
2.1 化工工艺中的控制系统
2.1.1 概述
控制系统在化工生产中的作用可以概括为以下三个方面。
(1)抑制外部扰动的影响
抑制外扰对过程的影响是过程控制系统最基本的作用。扰动意味着周围环境(外界)对反应器、分离器、热交换器和压缩机等设备有影响,它是客观存在的,不可避免的。因而,需要引入控制机构,使过程产生适当的变化,以消除扰动对化工生产可能造成的不良影响。
有一贮槽加热系统如图2-1所示。液体流入槽内流量为Fi,温度为Ti,槽用蒸汽加热,蒸汽流量为Fst,F和T分别为流出贮槽液体的流量和温度。假设槽内搅拌均匀,故可认为流出贮槽的液体温度与槽内液体的温度相等。

图2-1 搅拌贮槽加热器
该加热器的操作目标为:
①使流出贮槽的液体温度保持在预期值Ts;
②使槽内液体的体积量保持在预定值Vs。
加热器受到进料流量Fi和温度Ti的变化等外界因素的影响。如果它们无任何变化,那么达到T=Ts和V=Vs,也就不需要对系统进行任何监视和控制。显然,这不符合实际情况,因为Ti和Fi总是要变化的,而且有时变化可能还很频繁。对于贮槽加热系统来说,Ti和Fi的变化都属于来自外界的扰动,它们分别对贮槽内液体的温度和体积量有影响,因而需要某种形式的控制作用,以缓和扰动的影响,并使槽内液体的温度和体积量保持在预期值。
图2-2给出了贮槽加热器的控制系统,其中包括两个控制回路。在温度控制回路中,热电偶测量槽内液体温度T,然后T与预期值Ts比较,得到偏差ε=Ts-T,偏差值ε被送到控制机构,产生相应的控制作用,使温度T恢复到要求值Ts。当ε>0,即T<Ts,控制器开大蒸汽阀以增加供热;相反,如果ε<0,即T>Ts,控制器关小蒸汽阀;显然当T=Ts,即ε=0,控制器不动作。与此相类似,在Fi发生变化时,如果欲使液体体积或与其相当的液位高度h保持在给定值hs,测量槽内液位h,开大或关小对液体流出量有作用的阀门。

图2-2 贮槽的控制系统
总之,在化工生产中,采用控制的主要原因之一是抑制扰动对工艺设备操作工况的影响。
(2)确保过程的稳定性
假定在时间t=t0时,系统由于受到某些外部因素的影响而使系统中的状态变量发生变化,如温度、压力、浓度等。如果随着时间的推移,在没有外界干预的情况下这些变量能够逐渐回复并最终稳定在t=t0时的数值,则我们就称这样的系统是稳定的或自平衡的,显然这样的系统是不需要控制机构来使系统保持稳定的。
与上述情况相比较,如果系统的状态变量不能自动回复到初始值,则这样的系统就称为不稳定系统,它需要外部的控制来保持系统的稳定。以下以一个实例来说明不稳定系统的控制问题。
有一连续搅拌反应釜。在釜内进行A→B不可逆放热反应,流过釜外夹套的冷却剂移去反应热。通过对连续搅拌釜的分析可知,描述放热反应所释放热量的曲线是釜温T的S形函数(图2-3中曲线A);另外,冷却剂移去的热量是釜温T的线性函数(图2-3中所示直线B)。稳态时(即无任何变化)反应产生的热量应等于冷却剂移去的热量,所以图2-3的曲线A和直线B的交点P1、P2和P3为稳态位置,稳态P1与P3是稳定的,而P2是不稳定的。为了理解稳定性的概念,可用稳态点P2来分析。

图2-3 连续搅拌反应釜的三个稳态值
假定反应从T2温度和相应的浓度CA2开始。当进料温度升高时,反应混合物温度升高至某一点T'2。T'2时的反应放热量Q'2大于被冷却时移去的热量Q″2(见图2-3),这将导致釜温升高,继而反应速度加快,反应速度的加快使放热反应释放的热量增加,其结果又导致温度进一步上升。可见,进料温度的升高将使釜温偏离稳态P2,最后达到稳态值P3;同样,当进料温度下降时,稳态点将从P2变化到P1。相比较,如果在稳态P3或P1下操作,对反应釜干扰后,它将自然回复到P3点或P1点。
有时要在不稳定的中间稳态点P2操作连续搅拌釜。原因是:①低温稳态P1时的产量低,因为温度T1很低;②高温稳态P3的温度可能很高,会造成不安全的工况,破坏结晶,或产品质量变劣等。在此情况下,需要用控制器来保证在中间稳态点P2操作时的稳定性。
本例生动地说明了在外扰使系统有可能偏离要求状态的情况下利用某种形式的控制来实现稳态操作的必要性。
(3)使化工生产过程最优化
安全性和满足生产指标是化工厂的两个基本生产目标,一旦达到,下一个目标即是如何使工厂获得更多的利润。假定影响工厂生产的操作条件是变化的,显然就需要按经济目标(利润)总是最大值的方式去改变工艺操作参数(流量、压力、浓度和温度)。这项任务由工艺操作人员和自动控制装置来完成。
假定在一个间歇反应器中有如下两个连续反应发生:
假定两个反应皆为具有一级动力学过程的吸热反应。蒸汽流经反应器外的夹套以提供反应所需要的热量。B是有用产品,C是副产物。该反应器运行的经济目标是在整个工作周期tR内获得最大利润Φ,即
式中tR是反应周期。
为了使利润最大,唯一可任意改变的变量是蒸汽流量Q。蒸汽流量随时间变化,并影响该反应器温度。继而影响到希望的和不希望的反应的反应速度。问题是如何使Q随时间变化,以获得利润最大值Φ。让我们观察有关Q(t)的特殊情况。
①如果Q(t)是整个反应周期内的最大可能值,反应混合物温度也将是可能最大值。起初因反应物浓度CA大,产生的B多,但同时消耗蒸汽也多。随着时间的推移和B浓度增加,C产量也增加。因而,随着接近反应周期结束,必须减少蒸汽流量以降低温度。
②如果在整个反应周期tR内蒸汽流量保持最低值[即Q(t)=0],那么将无蒸汽消耗,但也没有B产生。
从这两种极端情况可知,在反应周期tR内,Q(t)将在最大值和最小值之间变化。应如何变化才能使利润最大?这个重要问题就是以上提到的最优化求解问题。
为了使利润Φ最优,蒸汽流量可按图2-4所示的趋势变化,所以需要控制系统。其作用:①计算反应周期内每一时刻的最佳蒸汽流量;②调整阀门(置于蒸汽管线上)开度,使蒸汽流量取得最佳值。此类问题就是所谓最优控制问题。

图2-4 间歇式反应器的最优蒸汽流量
该例说明,此处蒸汽流量的控制不是为了确保反应器的稳定性或消除外扰对反应器的影响,而是使其经济指标最优化。
2.1.2 基本控制系统的组成
以下将以经典的反馈控制为例来说明控制系统的组成。
图2-5给出了控制系统的方块图。由图2-5可知,自动控制系统由被控对象、调节器、测量原件和变送器、执行机构和调节阀等基本环节组成。现将这些组成控制系统的基本硬件介绍如下。

图2-5 控制系统的方块图
①被控对象(过程):指需要自动控制其工艺参数的工业过程、设备或装置,如精馏塔,锅炉汽包等。它包括由输入信号到输出信号之间的整个工业过程区间。
②测量原件和变送器:测量原件是用以测量过程工艺参数的真实值的部件,如热电偶、波纹管、孔板、气相色谱分析仪等。变送器用来将测量信号从感测原件送到调节器以及将控制信号从调节器传送至执行器。
③调节器:这是一个具有逻辑功能的单元(比较元件的功能也包括在内),决定控制变量应改变多少。它需要有设定值指标,根据测量值与设定值的偏差进行运算,产生一个输出值。调节器的输出值通常是0~100%的一个数,该数的大小决定了执行机构动作幅度的大小。
④执行机构:通常是调节阀或变速计量泵。该原件接受来自调节器的控制信号(输出值OP),并通过具体地调节控制变量来执行控制作用。调节器的输出值OP大小决定了调节阀开度的大小,而后者决定了控制变量对过程的影响程度。
现将几个名词解释如下。
①被控变量y:指需要控制的工艺参数,如裂解炉的出口温度、锅炉汽包的液位等。它是被控对象的输出信号。在控制系统方块图中,它也是自动控制系统的输出信号,但它是理论上的真实值。测量变送器输出的信号是被控变量的测量值ym。
②设定值SP:指生产过程中被控变量需要保持的值,当它由工业调节器内部给定时称为内给定值,最常见的内给定值是一个常数,它是被控变量需要保持的工艺参数值,如锅炉发生的过热蒸汽温度需要保持在440℃。当设定值产生于外界某一装置并输入至调节器时,称为外给定值。
③控制变量m:受控于调节阀、用于调节被控变量大小的物理量称为控制变量。它是调节阀的输出信号,例如图2-1中贮槽加热蒸汽流量。
④外界扰动:自动控制系统中,各个环节实际上或多或少会受到外界的扰动,如电源电压的波动、气源压力的波动、环境温度的波动等。但在自动控制中,除控制变量外,作用于被控对象并对被控变量影响较大的输入作用都称为干扰。
⑤偏差信号ε:它是比较元件的输入信号,其值是设定值SP和测量值反馈信号ym之差。在反馈控制系统中,调节器根据偏差信号的大小操纵控制变量。
此处介绍的控制系统,当测量值与设定值的偏差为零时调节器不动作,只有当扰动对控制变量的影响发生以后才开始动作,故称为反馈控制系统。
2.1.3 常见的控制结构
调节器把过程的测量值与设定值进行比较,确定偏差,并按照一定的规律产生一个使偏差为零的或使偏差为很小值的调节信号,调节器产生这种信号的作用叫调节作用,调节作用所遵循的数学规律称为调节规律。
(1)PID控制
在实际的自动调节系统中,大量采用PID调节规律,即比例、积分、微分调节规律。常见的调节系统中大量采用P(比例)调节器,PI(比例、积分)调节器和PID(比例、积分、微分)调节器
①比例调节:比例调节是最基本的调节规律,应用范围广,其特点是调节器输出与偏差成正比,对偏差的反应快。由于比例调节的调节作用是与偏差成正比的,所以当负荷变化时,调节的结果存在静偏差。要用人工再调整设定值,才能使被控变量重新等于原先设定值,以消除余差。
比例调节器的输出P(t)与偏差信号e(t)之间的关系为:
P(t)=KCe(t)
②比例、积分调节:所谓积分作用,就是调节器输出的变化量与偏差随时间的积分成比例的调节规律。亦即输出的变化速度与输入偏差值成正比。在一般调节系统中,比例积分调节规律(PI调节规律)已能基本满足需要。PI调节器既有偏差立即放大(或缩小)的规律,又有将偏差累积的规律,其输出值P(t)和输入的偏差信号e(t)之间的关系为:
式中Ti为调节器的积分时间。比例积分调节器的特点是调节的结果无余差,但由于引入积分作用,使系统的稳定性变差,振荡周期变长。
③比例、积分、微分调节:微分调节的规律是输出变化量P(t)与输入偏差e(t)的变化速度成正比,是一个纯微分环节。在比例积分调节规律的基础上引入微分调节规律,就构成了为比例积分微分调节规律:
式中Td为微分放大倍数。引入微分作用以后的特点为:对偏差反应的速度较比例作用还要快,适用于滞后大的对象,使系统的稳定性增加;微分作用不能消除系统余差。
(2)串级控制
图2-6为原油常减压装置中原油加热炉出口温度一种可能的控制方案。当负荷发生变化时,由温度变送器、调节器和调节阀组成一个单回路控制系统,通过改变燃料油的流量去克服由于负荷变化而引起的原油出口温度的波动,以保持原油出口温度在给定值。但是燃料油的流量受到燃料油供应系统影响,波动大且频繁,由于加热炉滞后较大,原油出口温度也就会出现大幅度波动。因此这不是一个好的控制方案。

图2-6 原油出口温度单回路控制
为了更好地控制原油出口温度,可以先构成一个燃料油流量控制系统(回路Ⅱ),先稳定燃料油的流量,而把原油出口温度调节器的输出值作为燃料油流量控制回路的设定值,形成回路Ⅰ,使燃料油流量调节器随着原油出口温度调节器的需要而工作,这样就构成了图2-7所示的串级控制系统。在这一串级控制系统中,存在着两个控制回路。其方块图如图2-8所示。

图2-7 原油出口温度的串级控制

图2-8 串级控制系统的方块图
在这个串级控制系统中,原油出口温度称为主被控变量,简称主变量;燃料油流量称为副被控变量,简称副变量;原油出口温度调节器称为主调节器;燃料油流量调节器称为副调节器;从燃料油调节阀后至原油出口温度这个温度对象称为主对象。调节阀后流量对象称为副对象;由副调节器、调节阀、副对象、副测量变送器所组成的回路称为副回路,而由主调节器、副回路等效环节、主对象和主变量测量变送部分称为主回路。
串级控制系统有如下特点:
①由于副回路的存在,进入副回路的干扰影响大为减小。同时,由于串级控制系统增加了一个副回路,具有主、副两个调节器,大大提高了调节器的放大倍数,从而也就提高了对干扰的克服能力。尤其对于进入副回路的干扰,表现更为突出。
②串级控制对克服容量滞后大的对象特别有效。
③串级控制的适应能力强。串级控制系统就其主回路来看,它是一个定值控制系统,但其副回路对主调节器来说,却是一个随动控制系统。主调节器能够根据对象操作条件和负荷的变化情况,不断纠正副调节器的给定值,以适应操作条件和负荷的变化。从这一点意义上来讲,串级控制系统的适应性较强。
(3)比值控制
在生产过程中往往需要两个或两个以上的流量之间满足一定的比值关系,为此目的构成的控制系统称为比值控制系统。例如合成氨厂中进入气化炉的氧气和重油流量应该保持一定比例;精馏塔的回流比保持恒定;吸收塔的液气比保持一定等等。这种比值关系的控制精度对于提高产品的质量和数量、降低消耗以及防止事故发生具有重要的意义。
比值控制系统主要用于控制两种物料之间的流量比,两流量皆被测量,但只对其中一个加以控制,流量未被控制的物料称为自由流。图2-9为一种单闭环比值控制。
在图2-9中,测量两流量,并求出其比值,将该比值与预期的比值(设定值)比较,被测比值与预期比值间的偏差作为作用于比值控制器的信号。

图2-9 比值控制系统
(4)分程控制
在反馈控制系统中,一般的情况是一台调节器的输出去控制一只调节阀。但是在某些工艺过程中,需要由一只调节器的输出同时控制两只或两只以上调节阀的开度。它的方法是根据调节器输出信号的不同范围,去分别控制不同的调节阀,所以称为“分程”。例如某调节器的输出信号范围是0.02~0.1MPa气压,要控制A、B两阀,那么只要在A、B上分别装上阀门定位器,A阀上的阀门定位器调整为当输入为0.02~0.06MPa时输出为0.02~0.1MPa,而B阀上的阀门定位器可调整为当输入为0.06~0.1MPa时输出为0.02~0.1MPa。这样当调节器输出在0.02~0.06MPa时A阀动作,调节器输出在0.06~0.1MPa时B阀动作,达到了分程的目的。
在分程控制系统中,调节阀的开闭形式可以分两类。一类是几只调节阀同向动作;另一种是几只调节阀异向动作,见图2-10。

图2-10 调节阀分程动作
采用分程的目的一般是为了扩大调节阀的可调范围或满足某种工艺上的特殊需要。
2.1.4 典型化工设备的控制方案
(1)管路的控制方案
化工生产经常需要对管路中流体的流量进行调节,可用于流量、液位、压力等变量的控制。流量调节方式较为简单,若管路中安装有离心泵,则通常采用泵的出口阀门开度控制方案,如图2-11所示。若管路中安装有容积式泵,如往复泵、齿轮泵、螺杆泵和旋涡泵等,或安装有压缩机,则由于该类输送装置直接控制了管路中的流量,所以不能在出口管道上直接安装节流装置来调节流量,而是通常采用旁路调节,如图2-12所示。另外,压缩机的流量还可以通过调节转速来控制,这种方案效率高,在目前工业生产中的离心式压缩机中应用较多。

图2-11 带离心泵的管路流量调节

图2-12 带容积式泵的管路流量调节
(2)换热器的控制方案
用换热介质流体的流量来控制工艺流体的出口温度[图2-13(a)],调节速度快,是一种应用最为广泛的调节方案。当换热的两股流体的流量都不允许改变时,可用其中一股流体部分走旁路的办法来调节温度,如图2-13(b)所示。该方案实际上增加了一个系统的自由度,使得系统的可控性更好一些。

图2-13 换热器出口温度控制方案
如果换热介质有相变,则需要控制液相的液位和气相的压力。对于换热介质为液相的情况(如液氨),则通过液相进料来控制液位,如图2-13(c)所示。对于换热介质为气相的情况(如水蒸气),则通过液相出料来控制液位,如图2-13(d)所示。这两种换热控制适用于冷凝器、蒸发器等设备的温度控制,以被控工艺物流的出口温度为主变量,以换热器的液位为副变量,进行串级控制(用温度控制器来修正液位控制器的设定值),通过液位的高低来改变有效传热面积,进而调整传热量。这种方案滞后大,而且还要有较大的传热面积余量。但使用这种方法调节时,传热量的变化比较和缓,可以防止局部过热,对热敏性介质有好处。
(3)精馏塔的控制方案
精馏塔是一种传质设备,用于组分间的分离,所以产品质量是其主要的控制指标。如果对产品质量要求不严,则只需控制回流量和塔釜加热量即可,如图2-14所示。如果要严格控制塔顶和塔釜的产品质量,则可以间接以精馏段和提留段灵敏板的温度为被控变量来调整回流量和塔釜加热量,见图2-14中的两个虚线圆框。实际上,上述的精馏塔质量控制系统的主要被控变量有4个:回流量L、塔顶采出量D、塔釜加热量QR和塔釜采出量W。通常选L和D中较大者控制回流罐液位,较小者作为控制产品质量的手段来控制塔温度,而W则用来控制塔釜液位。

图2-14 精馏塔的质量控制方案
精馏塔的另一个重要被控变量为塔顶压力。塔顶压力的变化必将引起塔内气相流量和塔板上气液平衡条件的变化,使操作条件改变,最终将影响到产品的质量。图2-15中的塔顶压力通过调节冷凝器热负荷来控制,适用于馏出物中不含或仅含微量不凝性气体的情况。该方案的优点是所用的调节阀口径较小,节约投资,且可节约冷却水,缺点是冷凝速率与冷却水量之间为非线性关系。在冷却水流量波动较大时,可设置塔压与冷却水量的串级控制,以克服冷却水量波动对搭压的影响。如果塔顶气体不能被全部冷凝下来,则按如下方案来设计:①如果塔顶气体含有大量的不凝气,则塔顶压力用塔顶线上的调节阀来调节,如图2-15(a)所示;②如果塔顶气体仅含有部分不凝气时,则压力调节阀应装在回流罐出口不凝气线上,如图2-15(b)所示。这两种方案的优点是压力调节快捷、灵敏,可调范围也大,缺点是所需调节阀的口径较大,而且在气相介质有腐蚀性时,需用价格昂贵的耐腐蚀性材质的调节阀。

图2-15 精馏塔的其他压力控制方案
(4)反应器的控制方案
化学反应器是化工生产中的核心设备,反应器控制的好坏直接关系到生产的产量与质量。化学反应器的质量指标一般指反应的转化率或反应生成物的规定浓度。如果转化率不能直接测量,就只能选取几个与它有关的参数,经过运算去间接控制转化率。在成分仪表尚属薄弱环节的条件下,通常采用温度为质量的间接控制指标构成各种控制系统,必要时再附以压力和处理量等控制系统,即可保证反应器正常操作。
第一种温控方案为通过控制进料温度来完成,如图2-16所示。物料经过进料换热器(加热或冷却)进入反应器,通过改变换热负荷来改变进入反应器的物料温度,从而达到控制反应器内物料温度的目的。该方案又分为两种情况:①换热介质来自公用工程;②换热介质来自反应器出料,即进行了热集成。其中第二种方案采用旁路调节方式,与图2-13所示的换热器温控方案类似。

图2-16 反应器温控方案Ⅰ
第二种温控方案是控制反应器夹套传热量,如图2-17所示。由于大多数反应器均有传热面,以引入或移去反应热,所以用改变引入传热量多少的方法就能实现温度控制。当反应器内温度改变时,可用改变加热剂或冷却剂流量的方法控制釜内温度。这种方案结构比较简单,使用仪表少,但温度滞后严重。特别是当聚合反应过程中物料黏度大、热传递较差、混合又不易均匀时,较难达到严格的温度要求。

图2-17 反应器温控方案Ⅱ
第三种温控方案是控制反应段间进入的冷气量。在多段固定床反应器中,可将部分冷的原料气不经预热直接进入段间,与上一段反应后的热气体混合,从而降低了下一段入口气体的温度,如图2-18所示。这种控制方案中,反应通常是经过多段的催化剂分步完成的。往中间的催化剂层加入一部分冷料,可以在有效降低反应温度的同时降低副反应的发生。比如在硫酸生产中,用SO2氧化成SO3,由于冷的那一部分原料气少经过一段催化剂层,所以原料气总的转化率有所降低。另一种情况是在合成氨工业中,当用H2与N2变换NH3,原料气就是分三部分进入催化剂层的,其目的就是使该反应远离平衡点,以加快转化速率。

图2-18 反应器温控方案Ⅲ
2.1.5 控制系统操作要点
(1)控制器操作要点
负反馈准则要求控制系统开环总增益为正。设置控制器正反作用的目的是保证控制系统成为负反馈。组成控制系统的各环节增益的正负由该环节输入输出之间的关系确定。当该环节的输入增加时,其输出也增加,则该环节增益为正,反之输出减小,该环节增益为负。开环总增益是组成开环各环节的增益之积。
确定控制器正反作用的步骤如下。
①根据功能安全准则,从工艺安全性要求确定控制阀的气开和气关型式,气开阀增益为正,气关阀增益为负。
②根据过程的输入和输出关系,确定过程增益的符号。
③根据检测变送环节的输入输出关系,确定检测变送环节增益的符号。
④根据负反馈准则,为保证开环总增益为正,确定控制器正反作用。
(2)串级控制的操作要点
串级控制系统主、副被控变量的选择
①根据工艺过程的控制要求选择主被控变量;主被控变量应反映工艺指标。
②副被控变量应包含主要扰动,并应包含尽可能多的扰动。
③主、副回路的时间常数和时滞应错开,即工作频率错开,防止共振现象发生。
通常,主被控对象的时间常数与副被控对象时间常数之比在3∶1或以上,防止副环工作频率进入谐振频率,造成共振现象。
④主、副被控变量之间应有一一对应关系。
⑤主被控变量的选择应使主对象有较大的增益和足够的灵敏度。
⑥应考虑经济性和工艺的合理性。
串级控制系统主、副控制器控制规律的选择
串级控制系统有主、副两个控制器。选择控制器控制规律应根据控制系统要求确定。
①选择主控制器控制规律。根据主控制系统是定值控制系统的特点,为消除余差,应采用Ⅰ控制规律;通常串级控制系统用于慢对象,为此,可采用D控制规律;据此,主控制器的控制规律通常为PID。
②选择副控制器控制规律。副控制回路既是随动控制又是定值控制系统。因此,从控制要求看,通常可无消除余差的要求,即可不用Ⅰ;但当副被控变量是流量,并有精确控制该流量要求时,可选用Ⅰ;当副对象时间常数小,为削弱控制作用,需选用大比例度的P控制作用,有时也可加入积分或反微分;当副回路容量滞后较大时,宜加入微分;当副环包含积分环节时,由于积分环节提供一90°相位差,使副环相位滞后减小,有利于提高系统控制品质。因此,通常,副控制器的控制规律选PI。
串级控制系统主、副控制器正反作用的选择
串级控制系统主、副控制器正反作用的选择应满足负反馈准则。因此,对主环和副环都必须满足总开环增益为正。假设主、副检测变送环节的增益都为正,具体选择步骤如下。
①根据安全运行准则,选择控制阀的气开和气关型式(气开型,Kv为正;气关型,Kv为负)。
②根据工艺条件确定副被控对象的特性。操纵变量增加时,副被控变量增加,Kp2为正;反之为负。
③根据负反馈准则,确定副控制器正反作用(正作用,Kc2<0;反作用,Kc2>0)。
④根据工艺条件确定主被控对象的特性。副被控变量增加时,主被控变量增加,Kp1为正;反之为负。
⑤根据负反馈准则,确定主控制器正反作用(正作用,Kc1<0;反作用,Kc1>0)。确定主控制器正反作用时,只需要满足Kc1Kp1Km1>0。
⑥根据负反馈准则确定在主控方式时主控制器正反作用是否要更换。当副控制器是反作用控制器时,主控制器从串级方式切换到主控方式时,不需要更换主控制器的作用方式。当副控制器为正作用控制器时,主控制器切换到主控时,为保证主控制系统为负反馈,应更换原来的作用方式。
串级控制系统中控制器的参数整定和系统投运
从整体看,串级控制系统是一个定值控制系统,控制品质的要求与单回路控制系统控制品质的要求一致。从副回路看,应要求能够快速、准确地跟踪主控制器输出变化。串级控制系统控制器参数整定有逐步逼近法、两步法和一步法等。逐步逼近法先断开主回路,整定副控制器参数,其次,闭合主回路,整定主控制器参数,最后,再整定副控制器参数、主控制器参数,直到控制品质满足要求。由于每次整定都向最佳参数逼近,因此,称为逐步逼近法。两步法是主控制器手动情况下,先整定副控制器参数,整定好后,主控制器切自动,整定主控制器参数。一步法是根据副被控对象的特性,按表2-1设置副控制器参数,然后整定主控制器参数。逐步逼近法用于对主、副被控变量都有较高控制指标的场合,两步法和一步法用于对副被控变量的控制要求不高的场合。
表2-1 副控制器比例度的经验数据

参数整定时应防止共振现象出现,一旦出现共振,应加大主控制器或副控制器的比例度,使副、主回路的工作频率错开,以消除共振。
串级控制系统的投运与参数整定的方法有关。两步法整定参数的系统投运步骤如下:
①设置主控制器为“内给”,“手动”,设置副控制器为“外给”,“手动”;
②主控制器手动输出,调整副控制器手动输出使偏差为零时,将副控制器切“自动”;
③整定副控制器参数,使副被控变量的响应满足所需性能指标,例如,衰减比指标;
④调整主控制器手动输出使偏差为零时,将主控制器切“自动”;
⑤整定主控制器参数,使主被控变量的响应满足所需性能指标,例如,衰减比指标、余差等。
串级控制系统的投运宜先副后主,由于设置副环的目的是提高主被控变量的控制品质,因此,对副控制器参数整定的结果不应作过多限制,应以快速、准确跟踪主控制器输出为整定参数的目标。当工艺过程对副被控变量也有一定控制指标要求时,例如,精确流量测量等,可采用逐步逼近法整定参数,使副被控变量也能够满足所需控制指标。
(3)复杂控制系统
在单回路控制系统的基础上,再增加计算环节,控制环节或者其他环节的控制系统称为复杂控制系统
随着生产的发展、工艺的革新必然导致对操作条件的要求更加严格,变量间的相关关系更加复杂,为适应生产发展的需要,产生了复杂控制系统。在特定条件下,采用复杂控制系统对提高控制品质,扩大自动化应用范围起着关键性作用。做粗略估计,通常复杂控制系统约占全部控制系统的10%,但是,对生产过程的贡献则达80%。
复杂控制系统的分类
常用的复杂控制系统有串级控制系统、比值控制系统、均匀控制系统、分程控制系统、选择控制系统、前馈控制系统等。
比值控制系统
凡是用来实现两个或者两个以上的物料按照一定比例关系关联控制,以达到某种控制目的的控制系统,称为比值控制系统。可分为单闭环比值控制系统、双闭环比值控制系统和变比值控制系统。
均匀控制系统
用来解决前后被控量供求矛盾,保证它们的变化不会反应过于剧烈的一种控制方案。
前馈控制系统
根据扰动或者设定值的变化按补偿原理而工作的控制系统,其特点是当扰动产生以后,被控量还未变化以前,根据扰动作用的大小进行控制,以补偿扰动作用对被控变量的影响。
分程控制系统
一般而言,通过对一只调节阀的操作便能够实现对一台调节器的输出工作,如果通过一只调节器对两个或者是两个以上的调节阀进行控制,并且是通过对信号的分析根据不同的需求去对不同的阀门进行操作,这种控制方式就是分程控制。分程控制经常应用于DCS系统中,在化工行业获得了较为广泛的应用。在分程控制的作用下,将一个调节器的信号进行分段处理,信号被分为若干段以后,每段信号对应一个执行器进行控制工作,通过执行器的分段连续共同完成一个较为复杂的任务。例如在化工生产中,受到原料的物理或者是化学属性的影响,需要对其进行严密的控制,这就借助于分程控制。例如对于氮气而言,需要利用密封的方式对其进行储存,且氮气的压力需要维持在一定的范围内。在化工生产中,一些材料是通过利用氮气的压力作为动力进行传送的,在对氮气压力的维持下,实现了原料传送的稳定性。