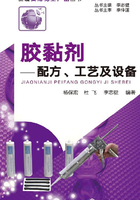
2.3 胶黏剂的固化过程
胶黏剂和被粘物之间通过各种机械、物理和化学的作用,产生黏附力,为使被粘物之间粘接牢固,胶黏剂必须以液态涂布于被粘物表面并且完全浸润。但是液态的胶黏剂填充在被粘物之间并没有抗剪切强度,如同两块玻璃中间的水,要把两块玻璃板拉开是十分困难的,但是一个很小的剪切力就可以把两者分开。因此,液态的胶黏剂浸润在被粘物表面后能通过适当的方法使胶黏剂变成固态才能承受各种负荷,这个过程即为胶黏剂的固化。胶黏剂的固化可以通过物理的方法,也可以通过化学的方法,使胶黏剂聚合成为固体的高分子物质。
2.3.1 热熔胶及热塑性高分子
热熔胶及热塑性高分子物质加热熔融之后就获得了流动性,许多高分子熔融体可以作为胶黏剂使用。高分子熔融体在浸润被粘表面之后经冷却就能发生固化。在配制热熔胶时必须解决胶黏剂的强度和熔融体黏度之间的矛盾。高分子物质必须有足够高的分子量才能具有一定的强度和韧性,但是熔融体的黏度也随着分子量的增高而迅速增大。提高温度当然能降低熔融体黏度,但是温度过高又会引起高分子的热降解,因此为了提高热熔胶的流动性和对被粘表面的黏附性,必须加入各种辅助成分。热熔胶可能包含下列各种成分:①基本树脂;②蜡;③增黏剂;④增塑剂;⑤填料;⑥抗氧剂。由于热熔胶只要将熔融体冷却即可固化,所以具有一系列优点:黏合速度快,便于机械化作业,无溶剂、安全、经济等。因此它在包装、装订、木材加工、制鞋等工业部门应用十分广泛。但是热熔胶也有耐热性较差、胶接时需要加热到较高的温度、对气候比较敏感、加热时易产生挥发性有机物等缺点。使用热熔胶时必须注意控制熔融温度和涂胶之后的晾置时间,如果聚合物是结晶性的,冷却速度也应加以控制。
另外,塑料的热封接和使用热熔胶有相似之处。热封接就是把塑料局部加热熔融并封接在一起。加热的方法有烙铁、热气、超声波、高频电磁场以及机械摩擦等。可以进行热封接的塑料有聚乙烯、聚氯乙烯、聚丙烯、聚苯乙烯、ABS塑料、聚甲醛、聚丙烯酸酯、乙酸纤维素、尼龙、聚碳酸酯、聚苯醚、聚砜等。
2.3.2 溶剂型胶黏剂
溶剂型胶黏剂将热塑性的高分子物质溶解在适当的溶剂中成为高分子溶液以获得流动性。在高分子溶液浸润被粘物表面之后溶剂挥发掉,就会产生黏附力。溶剂型胶黏剂固化过程的实质是随着溶剂的挥发,溶液浓度不断增大,最后达到一定的强度。溶剂型胶黏剂的固化速度决定于溶剂的挥发速度,一些难以挥发的溶剂要求很长的固化时间;但是溶剂的挥发速度过快,则涂刷时容易起皮,因此配胶时要选择适当的溶剂,也可将多种溶剂混合使用以调节溶剂的挥发速度。溶剂型胶黏剂的一个突出优点是固化温度比较低,这就使一些高温下容易分解的高分子物也可能作为溶剂型胶黏剂来使用,例如聚喹吖恶啉树脂,它的熔点超过了分解温度,因此不能制成热熔胶,但是它能够溶解于甲酚、四氯乙烷等溶剂中,可以配制成耐高温的溶剂型胶黏剂。多数溶剂型胶黏剂可以室温固化。溶剂型胶黏剂的缺点是胶接强度低,一般只能在非结构部件上应用,另外许多溶剂还有毒害和易燃的问题,严重污染环境,它将逐步被环境友好型的溶剂型胶黏剂取代。溶剂型胶黏剂在塑料胶接方面使用非常普遍。表2-3列出了一些常用的溶剂型胶黏剂的配方。
表2-3 常用溶剂型胶黏剂配方

用溶剂型胶黏剂胶接塑料,尤其是黏合薄的制品时,必须注意溶剂对被粘表面的腐蚀易造成被粘物变形的问题。有机玻璃、聚苯乙烯、聚碳酸酯等塑料制品在溶剂的作用下会产生细的裂缝,这是由于塑料本身的内应力引起的。采用快干型胶黏剂或者用聚合型胶黏剂可以减小产生裂缝的危险。外应力也能引起裂缝,所以黏合这些塑料时压力不能加得太高。
2.3.3 乳液胶黏剂
乳液胶黏剂是聚合物胶体在水中的分散体。胶体颗粒的直径通常是0.1~2μm,它的周围由乳化剂保护,目前用作乳液胶黏剂的高分子主要是聚乙酸乙烯酯及其共聚物和丙烯酸酯的共聚物。乳液胶黏剂的固化过程为乳液中的水逐渐渗透到多孔性的被粘材料中并挥发,使乳液浓度不断增大,最后由于表面张力的作用,使高分子的胶体颗粒发生凝聚。环境温度对乳液的凝聚有很大的影响,当环境温度足够高时,乳液凝聚形成连续的胶膜,若环境温度低于最低成膜温度,就形成白色的不连续胶膜,强度很差。每种高分子都有最低成膜温度,通常比玻璃化温度略低一些,因此在使用乳液胶黏剂时环境温度不能低于最低成膜温度。乳液胶黏剂通常以水为分散介质,具有固体含量高、胶接强度优良、无毒以及价格低廉等优点,它适用于胶接多孔性材料如木材、纸张、纤维素制品等。但是乳液胶黏剂也有耐水性较差、容易发生蠕变等缺点。
也有使用有机溶剂作为分散介质的乳液胶黏剂,称为非水乳液,例如氯丁二烯与丙烯酸的共聚物可以分散在脂肪烃类溶剂(如庚烷)中,成为固体含量高达50%(质量分数)的非水乳液胶黏剂。塑料溶胶与乳液相似,是用增塑剂作为高分子的分散介质,这种具有流动性的分散体系称为“塑料溶胶”。塑料溶胶也可以作为胶黏剂和密封剂来使用。在塑料溶胶的固化过程中发生增塑剂溶解于高分子固体中以及高分子颗粒的融结等现象,所以体积收缩率很低,粘接效果很好。
2.3.4 热固性树脂
热固性树脂是具有三向交联结构的聚合物,它具有耐热性好,耐水、耐介质优良,蠕变低等优点。目前结构胶黏剂基本上以热固性树脂为主体。热固性胶黏剂获得交联结构有两种方法:①把线型高分子交联起来,如橡胶的硫化;②由多官能团的单体或预聚体聚合成为三向交联结构的树脂。常用的热固性胶黏剂,如酚醛树脂胶黏剂和环氧树脂胶黏剂是第2种方法获得交联结构的典型。在一些结构胶黏剂的固化过程中,这两类交联反应可能同时存在。热固性树脂的性能不仅决定于配方,固化周期也十分重要,因为固化周期对于固化产物的微观结构有很大的影响。
官能团单体或预聚体进行聚合反应时,随着分子量的增大同时进行着分子链的支化和交联,当反应达到一定程度时体系中开始出现不溶、不熔的凝胶,这种现象称为凝胶化。胶液凝胶化后,胶层一般可获得一定的粘接强度,但在凝胶化以后的较长时间内粘接强度还会不断提高。由于凝胶化后分子运动变慢,因此这类胶黏剂在初步固化后适当延长固化时间或适当提高固化温度,以促进后固化的顺利进行对粘接强度是极其有利的。对于某一特定的胶种来说,设定的固化温度是不能降低的。温度降低的结果是固化不能完全,致使粘接强度下降,这种劣变是难以用延长固化时间来补偿的。对于设定在较高温度固化的胶种,最好采用程序升温固化,这样可以避免胶液溢流,不溶组分分离,并能减小胶层的内应力。
用固化剂固化的胶黏剂,固化剂用量一般是化学计量的,加入量不足时难以固化完全,过量加入则胶层发脆,均不利于粘接。为了保证固化完全,固化剂一般略过量一些。应用分子量较大的固化剂时,其用量范围可以稍大一些。用引发剂固化的胶黏剂,在一定范围内增大引发剂用量可以增大固化速度而胶层性能受影响不大。用量不足易使反应过早终止,不能固化完全;用量过大,聚合度降低,均使粘接强度降低。为了避免凝胶化现象对胶层的不利影响,可以使用复合引发剂,即将活性低与活性高的引发剂配合使用。加入引发剂后,再适当加入一些特殊的还原性物质(称为促进剂)可以大大降低反应的活化能,加大反应速率,甚至可以制成室温快固胶种,这就是氧化还原引发体系。由于还原剂在促进引发剂分解的同时降低了引发效率,因此在氧化还原引发体系中引发剂量应该加大。催化剂只改变反应速率,催化剂固化型胶黏剂在不加催化剂时反应极慢(指常温下),可以长期存放,加入催化剂后由于降低了固化反应的活化能而使固化反应变易,胶层可以固化。催化剂用量增大,固化速度变快,过量使用催化剂会使胶层性能劣化。在催化剂用量较少时适当提高固化温度也是可行的。
凝胶化的速度决定于官能团的反应活性以及多官能团单体的浓度和官能度。在合成树脂和胶黏剂的工艺中常常把凝胶化时间作为树脂工艺性能的一个指标。另外,在多官能团单体的浓度和官能度相同的情况下,可以通过测定凝胶时间来比较官能团的反应活性。相反,也可以根据凝胶点的反应程度来计算反应物的官能度。在凝胶化之后继续进行的反应大体上包括:①可溶性树脂的增长;②可溶性树脂分子间反应变成凝胶;③可溶性树脂与凝胶之间的反应;④凝胶内部进一步反应使交联密度提高。因此,热固性树脂固化产物不是结构均匀的整体,而是由交联密度乃至化学成分不同的区域所组成。同一种树脂采用不同的固化周期进行固化,将形成具有不同微观结构的产物,于是固化产物的性能也将有所差别。在使用热固性胶黏剂时,在一定的时间范围内延长固化时间和提高固化温度并不等效,对一种胶黏剂来说,降低固化温度难以用延长固化时间来补偿,降低固化温度往往以牺牲性能为代价。此外,为了获得性能优良的胶接接头,有时在胶黏剂和被粘物表面之间需要发生一定的化学作用。这种化学作用必须克服一定的能垒,因此只有在足够高的温度下才能进行。当然也不能认为在任何情况下提高固化温度都是有利的。在胶接两种膨胀系数相差很大的材料时,为了防止产生过高的热应力,宜采用较低的固化温度,最好选用常温固化的胶黏剂。有时过高的固化温度会引起胶黏剂的降解,或者使被粘物的性能发生变化,因此固化温度应该加以准确地控制。
有些热固性胶黏剂在固化过程中会产生小分子挥发性副产物,例如酚醛树脂固化时放出水,它会在胶层中形成气泡,在这种情况下固化时必须加以一定的压力,如果固化时不产生挥发性副产物,那么只要微微加压使被粘物保持接触即可。
以上只是简单讨论了胶黏剂的固化情况,对于某一特定的胶黏剂,有时应用了几种固化方式,这样可以获得更好的综合性能。例如,反应型热熔胶、反应型压敏胶等均有比普通品种更好的粘接性能。