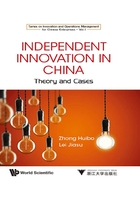
2.3 The Republic of Korea: Introduction and innovation
The Republic of Korea has become an important economic force in the world today. According to the report of the 2005 World Competitiveness Yearbook published by the International Institute for Management Development (IMD) in Switzerland, the national competitiveness and scientific competitiveness of the Republic of Korea ranked second and fifteenth in the world in 2004, respectively. Moreover, the Republic of Korea was the sixth or seventh power regarding IPR in the world. In the early 1960s, the Republic of Korea was a “poor” agricultural country and GDP per capita was less than $100. They could not even produce bicycles. But in 1962, after the implementation of the first five-year plan for economic growth, the Republic of Korea achieved rapid economic growth and created the “Miracle on the Han River.” The Republic of Korea has been known as one of the “Four Asian Tigers” since then. In 1996, the Republic of Korea joined the Organization for Economic Co-operation and Development (OECD) as one of the main representatives of a new industrialized economy. The economic aggregate of the Republic of Korea reached the 11th position in the world in 2004 with GDP per capita over $14,000. The emphasis on independent innovation is an important reason for the Republic of Korea's making such remarkable achievements.
2.3.1 The characteristics of Korean independent innovation
(1) More attention to the actual effect of technology introduction
First, the introduction of technology into Korean enterprises has a clear purpose. Regarding the introduction of high-speed railway (HSR) technology, the Korean side clearly required the French side to transfer all HSR technology, including the technology of the vehicle, the contact line, the control device along with their operation maintenance technology, etc. In addition, the Republic of Korea had the right to use related IPR and to open up to the international market and produce 50% of the total cost. Second, the Republic of Korea paid attention to the introduction of non-trade technology, that is to obtain technology by sending personnel abroad to receive training, visit, and exchange technological information. An example is through the cooperative R&D between Samsung and Sony, many of Samsung's electronical products are more advanced than Sony's. Korean enterprises require the partners to train technical personnel, which, together with “learning by doing,” rapidly improved the level of R&D ability of the Korean personnel.
(2) The implementation of the technology that has been introduced, with the help of technology alliances
The introduction of key industrial technology into the Republic of Korea has always been as follows: First, the government spends large amounts of money on introducing the most advanced foreign technology, and then organizes manpower and financial resources for scientific research. For example, the investment of the Korean government and local organizations in the CDMA reached 6 trillion wons, as did the introduction of high-speed rail technology. It laid a good technical foundation for independent innovation in the future. Especially, after the introduction of technology, Korean enterprises established a technology alliance, which was guided by the government through the invitation for bids, to tackle key problems jointly. The technology alliance avoided the situation in which a single enterprise might have no competence and gave up the project halfway. Like the CDMA project, the public-private partnership (PPP) and the internal and external collaboration were established. Thus, the Republic of Korea quickly mastered the core technology of CDMA, applied for a number of patents, and achieved a leading international position.
(3) Timely establishment of technology-oriented enterprises and research institutes in foreign countries
This helps to obtain foreign technology with the help of local technical forces. For example, major large Korean companies have established research institutes or branches and subsidiaries in the Silicon Valley in the US. These enterprises hire American engineers to design and develop by offering them higher wages.
2.3.2 The measures of Korean independent innovation
(1) The government's powerful S&T policy
The Republic of Korea is a small-sized country with restricted natural resources. Almost all of its energy is imported. Thus, the Korean people have a strong sense of crisis, just as a Korean pet phrase goes, “we must have the S&T to support the future survival of the Republic of Korea.” Therefore, in the 1960s and the 1970s, the Republic of Korea introduced a lot of advanced technologies from the US and Japan, and paid more attention to implementation and absorption. For every $1 cost of technology introduction there would be an $8 matching fund in order to implement the technology. At the same time, the Korean government adopted a series of supporting measures concerning law, policy, funding, talent training, etc.
The first measure is legal protection. Since the 1960s, the Republic of Korea has officially announced the Science and Technology Promotion Act, the Science Education Act, the Technology Development Promotion Law, the Technology Assessment Law, etc. In 2001, the Republic of Korea announced the Framework Act of Science and Technology containing 29 kinds of laws, which covers all aspects of the S&T development, and provides legal guarantees for the S&T development as well as technological innovation.
The second measure regards clear strategies of S&T. After considering the situation, the Korean government launched appropriate technological strategies to advance with the times. In 1989, it issued the “five-year plan for the development of cutting-edge industry,” which focused on the research and innovation of seven industries, including microelectronics, new materials, biological engineering, and optical fiber. In 1991, it launched the G7 project, lasting for 10 years. Its goal was to catch up with the S&T level of seven Western countries in the 21st century. In 2001, it made the Basic Plan of Science and Technology for five years (2002-2006) to develop the fields of 6T, namely IT (information technology), BT (biotechnology), NT (nanotechnology), ST (space technology), ET (environmental engineering technology), and CT (culture technology). In 2004, it launched the “ten new-generation growing power engineering projects,” focusing on the development of ten high-tech industries, such as digital broadcasting, the intelligent robot, the new-generation semiconductor, and the future type of cars.
The third measure is to foster a rapid increase in investments in R&D. In 1962, investment in Korean R&D was 2.1 billion wons, only 0.28% of the GDP. It was only $320 million in 1980, 0.56% of the GDP. The investment in R&D has increased rapidly since 1980. It was $14.4 billion (2.53%) in 2002, $16.4 billion (2.64%) in 2003, and $19 billion (2.82%) in 2004. Now, the proportion of investment in Korean R&D as a share of the GDP is lower than that in Japan but much higher than that in the US, Germany, France, UK, and other developed countries.
The fourth measure is the preferential policy for the technology development in enterprises. The policy includes the reserve fund system of technology development, the fee and tax relief system of technology and talent development, the tax relief system of new technology promotion investment, etc. In order to ensure the implementation of its tax support policy, the Republic of Korea has modified the relevant regulations. Therefore, the technical development organizations (enterprises, institutes, etc.) have become the object of legal support, such as making full use of government procurement policy. The new regulation claims that government departments are allowed to make preferential procurement of domestic products even if their price is higher than similar foreign products and state-owned enterprises have to purchase domestic products preferentially. The government purchases the new technology developed by small and medium enterprises (SMEs) and subsidizes pilot-scale experiments and industrialization. The relevant laws and regulations claim that public authorities should purchase the products of SMEs according to their department budget and annual plans. In addition, there is a flexible use of tax policy. According to the type of enterprise, the reserve fund system of technology development is set up; related enterprises can extract the reserve fund for technological development at 3%, 4%, and 5% of their total income; and this fund can be included in the cost. There are also many other policies, for example, exemption from income tax for full-time researchers and from other taxes for the expenses of personal R&D, the deduction and exemption of turnover tax and income tax of new technological development, the exemption from income tax when transferring technology to local people or enterprises and half deduction of income tax when transferring to foreign enterprises, special tax preferences for venture investment, etc.
The fifth measure is an emphasis on scientific and technological talent. The Republic of Korea proposed to cultivate 10 universities to rank among the world's top 100 research universities before 2012; the Republic of Korea has introduced the system of “special national researcher” to cultivate 10,000 core researchers, focused on R&D of the tenth generation new power growth technology, and has had vast investment in core research. The national management system is set up for outstanding scientists who have the hope of receiving a Nobel Prize, offering them the chance to take charge of large-scale national research projects and obtain research funding. For this type of scientists, physical protection is provided, which is equivalent to “national senior level” of ministerial officials. The country spares no effort in the promotion and development of reserve talents in S&T. The Presidential Science Scholarship is set up to encourage outstanding senior high school students to apply for famous domestic and foreign universities in the attempt to cultivate world-class scientists. Domestic students can receive a scholarship of around 80,000 yuan during their university studies; the students admitted to a famous foreign university can receive a $50,000 scholarship. For winning in an international competition such as the Science Olympiad, the President meets the “scientific geniuses”who have won prizes in person, along with their parents and teachers. The winner can also be exempted from military service. For the investment of foreign high-tech enterprises, the government encourages them to set up research centers in the Republic of Korea. These centers employ Korean masters and doctors of science and engineering, while the government pays their salaries.
(2) Enterprises as the main force of independent innovation
Korean enterprises, especially the large ones, are the mainstay of independent innovation. Concerning investment in R&D, the Republic of Korea has experienced a transition from government leadership to enterprise leadership. The proportion of the investment by government and enterprises was 77% and 23% in 1970, 52% and 48% in 1980. The proportion of R&D investment in the top 30 listed Korean companies was an average of 3.15% of their sales revenue. Korean enterprises have begun to set up R&D institutions since the 1980s, which increased rapidly later. The number of these enterprises was 100 in 1983, 1,000 in 1991, more than 5,000 in 2000, and more than 10,000 in 2004. Some large companies even have more than one R&D institution. For example, Samsung has 42 research institutes, and the number of research personnel increased from 12,000 in 1997 (accounting for 22% of the total number of employees) to 24,000 in 2004 (36%). Employees with a master's degree or a doctorate increased from 5,000 in 2000 to 24,000 in 2004. R&D expenditures increased year by year, with 1.6 trillion wons in 1999, 2.4 trillion in 2001 and 3.7 trillion in 2003 (8.5% of the sales revenue). Hyundai has 14 research institutes, and the total R&D expenditure was 2.5 trillion wons in 2004 (5% of the sales revenue) and more than 3 trillion wons (6% of the sales revenue) in 2005. LG has 27 research institutes; the sum of its R&D expenditure was 2.4 trillion wons in 2004 and 3.4 trillion wons in 2005. Because of the focus on technological innovation, Samsung, Hyundai, and LG became members of the “100 most valuable brands in the world” in 2005 as investigated by the American magazine Business Weekly and global brand management consulting companies, among which Samsung ranked 20th, Hyundai ranked 84th, and LG ranked 97th.
(3) The Republic of Korea obtains numerous achievements from independent innovation, and quickly becomes a country with excellent scientific and technological abilities
According to the report of the Technical Standards Institute of the Ministry of Commerce, Industry and Energy (MOCIE), 22 kinds and 113 Korean technologies have been adopted as the international standard in the IT field alone. The 1997 Asian financial crisis damaged the Korean economy heavily, but the Republic of Korea was the first to get out of trouble. The Korean automobile, shipbuilding, semiconductor, and information technology (IT) industries started later than in China, Seoul's first subway began construction ten years after Beijing's, but now, the Republic of Korea has an overall leading position in these fields. It has become the largest shipbuilding country (40% of the world's shipbuilding market), and the sales share of mobile phones is 22% of the world's. Korean products are exported around the world. The technological innovation promotes Korean economic and social development, which in turn, promotes technological innovation. Now, the Republic of Korea has a high level of urbanization; the rural population accounts for only 7.5% of the total population. The income of farmers is equivalent to 70% of the income of city residents. The Gini coefficient is about 0.32. Koreans have a higher level of education nationwide (the college admission rate was 89% in 2004, which is said to be the highest in the world). In the United Nations' 2004 e-government appraisal, the Republic of Korea ranked fifth in the world and first in Asia. In 2003, the Korean comprehensive ranking in informationization was seventh in the world. The popularizing rate of the broadband network (ADSL) has reached 70% (first in the world), and 61 out of 100 people use the Internet (fourth in the world).
2.3.3 Typical cases of Korean independent innovation
Korean independent innovation has its own unique model. The first step is the introduction of key technology that is vital to the national economy and to people's livelihood in the industries with a high relationship with technology. With the support of the government, the technology is implemented and adopted until core technology has been mastered so that innovative activities can be carried out. Thus, the Republic of Korea has reached world class in key industries such as telecommunications, railway, electronics, etc.
(1) CDMA
CDMA technology was first developed by Qualcomm in the 20th century. It was the most advanced mobile communication technology in the world. But, it was not industrialized and commercialized in the United States. The future of this technology seemed risky and uncertain. However, in 1993 the Korean government introduced this technology based on a detailed investigation and a full demonstration, and it made a great effort to industrialize it. The government and enterprises made such an effort at implementation, adoption, and re-innovation that they achieved great success.
First, the government gave strong all-around support. The government as the policy maker played a dominant role in the process of developing the CDMA further. It listed the CDMA as one of the projects of “national policy,” clearly putting forward the goal of creating a world-class industry and first-class products. Therefore, the government formulated and implemented a series of policies and measures for the development of the CDMA, including technological development, standardization, service operator license, etc. The government concentrated on manpower and material resources to support R&D institutions, and on enterprises to carry out technology implementation, adoption, and re-innovation. This policy guaranteed the further development of the CDMA.
Second, key problems are solved by PPP and internal & external collaboration. The Republic of Korea introduced only 7 out of 53 CDMA patent technologies developed by Qualcomm; the rest were developed independently. In the early development, the cooperative research between the Korean side and Qualcomm was engaged mainly in the design and development of the terminal and the MTSO. Meanwhile, with the guidance of an official institution, Electronics and Telecommunications Research Institute, Samsung, LG, and Hyundai worked cooperatively to tackle key problems. The united development system of public-private interacting and risk-sharing focused on the development of business application technology; this accelerated the implementation and adoption of imported technology, overcame technical difficulties, and cultivated creative talents. In the meanwhile, the minister of the National Intelligence Service often investigated and guided them face-to-face, so as to find and solve problems; the directors of research institutes participated in R&D together with the researchers which inspired their morale and guaranteed smooth development.
Third, strengthening the R&D organization, management, and coordination. The National Intelligence Service takes charge of and guides R&D activities; the project management group made up of the government, R&D institutions, and enterprises supervised the process and the quality of the R&D; the R&D personnel of TDX SPC exchange was absorbed to participate in the CDMA project, so that their experience and knack could be used in the R&D of the CDMA; production enterprises and service operators were also encouraged to participate in the project, which was able to combine R&D with production and service, resulting in a more rapid process of industrialization and commercialization; the competitive relationship between the project of the GSM terminal supervised by MOCIE made the CDMA project under the pressure of “who is better and faster,” improved the efficiency of its development, and shortened its development cycle greatly. After the commercialization of the CDMA, the government introduced a competitive mechanism and selected five companies to develop commercial service. The government selected synchronous IMT-2000 operators proactively, which formed good conditions for the sustainable development of the CDMA industry.
Fourth, investment in capital and talent increases and the products of CDMA technology enter the international market. According to incomplete statistics, the investment of the Korean government and local organizations in the CDMA reaches 6 trillion wons. The number of R&D personnel is more than 1,000. The human input of the enterprises' R&D accounts for 15%-20% of the total. The government supports enterprises to open up foreign markets. It makes an effort to expand the exportation of its products. At the same time, the PPP promotes CDMA diplomacy, persuading other countries to adopt the CDMA, so as to expand the market. In overseas marketing, the Republic of Korea has gone from the exportation of simple mobile phone equipment to network design and commercial service operation.
(2) The high-speed railway (HSR)
The Republic of Korea started building an HSR through the introduction of French technology and put it into commercial operation in December 2004. It became the fifth country to have an HSR following Japan, France, Germany, and Spain. Korean HSR technology came mainly from the French company, Alstom. In order to maximize the creation of opportunities for domestic firms, the Republic of Korea only introduced the core technology for the vehicle system, instead of the road and power system technology. During the construction of the HSR, the Republic of Korea required the high-speed train system vendor, Alstom, to transfer all the technology, and provide a training plan, a maintenance manual, and the maintenance technology for the entire core system. The Korean Train Express (KTX) engineering symbolized the world's largest technology transfer (100%) of manufacturing technology. Local manufacturing accounted for 50%, the Republic of Korea mastered the full set of HSR system technology including research, production, use, maintenance of train tracks, catenaries, and the trains. The French National Rail Company spent 20 years to pioneer the process of the European HSR, but the process took just a few years in the Republic of Korea who claimed that the train technology was its own technology after the opening of the Gyeongbu Line and the Honam Line, and thought that the technology would no longer depend on foreign technology after 2007. By then, the whole train system would be independently manufactured by Korean technology; the country's next target is exporting the technology following the steps of Japan, France, and Germany.
First, signing the agreement under the conditions of innovation and market access. The Republic of Korea introduced HSR technology not only to meet its own needs, but also to target the international market. Therefore, achieving localization and opening up the international market was the primary condition for introducing the technology. In June 1994, the Republic of Korea and the French company, Alstom, signed a technology transfer contract with favorable conditions. It was explicitly stipulated that all the French HSR technology should be transferred, including the core technology and operation maintenance technology including the vehicles, the contact line, and train control devices; the contract also allowed the Republic of Korea to use related IPR, open up international markets, and realize the localization rate of over 50% at the total cost. This laid good foundation for Korean development of the HSR based on French technology. Therefore, on the basis of France's providing advanced technology, the Republic of Korea developed more advanced HSR technology through secondary development, and implanted it as an export-oriented industry.
Second, learning and mastering the core technology as soon as possible, so as to create the conditions for secondary development. After signing the contract, the Republic of Korea sent a large number of engineering and technical personnel to France to receive training and learn the system interface technologies of power, signal, construction, and track systematically. The Republic of Korea also sent equipment technicians to France to accept on-the-job training with technology transfer. The quality supervisors of the Korean Rail Network Authority (KR), which took charge of the Korean HSR project, went to France to participate in the supervision of the quality, test, and test run of the car manufacturing; in the meanwhile, the Korean community and Alstom designed a rail facility system together. In the four-year period from 1994 to 1998, the Republic of Korea has gained as many as hundreds of thousands of pages of technical data of the design, manufacture, and testing; the number of technicians accepting training in France and the Republic of Korea was about 2,000, which laid a good technical foundation for secondary development.
Third, developing Korean HSR technology. Completing the basic implementation and adoption of French technology, the Republic of Korea focused on developing Korean HSR system technology with the combined strength of domestic R&D institutions and enterprises. The government listed it into the “G7” plan (a high-tech plan aiming at catching up with the West and supported with capital and talent). 129 R&D institutions and enterprises participated in it. In order to realize the goal of reaching a localization rate of over 50% for the main local facilities (including train control devices of the power locomotives, equipment dedicated to passenger cars, contact line and automatic control system, interlock, CTC system, etc.), which was agreed upon in the contract, for the total of 44 train engine units, the Republic of Korea won the right for 34 train engine units to be produced domestically. Therefore, the localization plan and schedule were formulated. The KR was responsible for examination and approval, supervision, and accounting supervision. The enterprises failing to complete the domestic indicators would be punished by 20% of the total cost. French technicians were invited to stay in the factory to guide the production. The total number of French technicians that stayed in Korea was more than 1,000; they ensured the progress and quality of production as well as the achievement of the localization rate (55.4%) of the main system equipment and devices. At the same time, because of innovative R&D, a large capacity of induction motors and other new equipment was developed successfully, such as the high-speed train system with a top speed of 352 km per hour.
(3) The iron and steel industry (POSCO)
The development of the Korean iron and steel industry has experienced three stages: “copying imitation” in the 1970s, “creative imitation” in the 1980s, and “innovation” after the 1990s.
First, the introduction, implementation, and imitation of advanced foreign technology (the 1970s). The Korean iron and steel industry insisted on introduction in the early days. The Republic of Korea had no technology of its own, and had to learn from others; the purpose was to build factories and form capacity quickly, so as to meet the demand of the domestic market. Therefore, the Republic of Korea imported advanced steel equipment from Japan and sent some technicians to Japan's Nippon Steel & Sumitomo Metal and NKK to receive training. These technicians quickly mastered the equipment operation and production technology. At the same time, POSCO, formerly Pohang Iron and Steel Company, had also recruited Japanese experts to guide them. The mastering of automatic control and product quality technology solved the problems appearing at the beginning of the operation. Relying on Japanese equipment, technology, and their strong entrepreneurial spirit, No.1 Pohang Blast Furnace with a production of 1.03 million tons was completed in 1973, followed by No. 2 to No. 4, which made POSCO's annual capacity reach 8.5 million tons. And it became the 11th largest steel mill in the world; some technical indexes and the production efficiency exceeded that of many developed countries, except Japan. During the implementation and adoption of Japanese technology, Korean enterprises also made improvements on the equipment and process.
Second, the emphasis on the introduction of technology and independent development at the same time (the 1980s). POSCO's development aroused vigilance of developed countries; the Republic of Korea was confronted with a block on its technology import. Therefore, when Korean companies continued to purchase advanced foreign equipment selectively, they collected and analyzed paper data, sent a delegation abroad to study, carried out technical exchanges and personnel exchanges, and held technical seminars, all favoring the mastering of the intelligence and information of the world's advanced technology. At the same time, the Republic of Korea intensified its cultivating of independent development power, integrating resources and research as well as developing advanced technology. Therefore, the enterprise technology research institutes, the industry research institutes, and other research institutes, along with Pohang University of Science and Technology, were set up. These institutions formed the R&D and talent training system combining industry-university-research; the Republic of Korea strengthened its amateur training system, continuously encouraged study both at home and abroad; moreover, the country recruited a large number of senior technical personnel, and enhanced its enterprise R&D forces; the people devoted to R&D were rewarded handsomely. As a result, the Republic of Korea made the leap from a pure imitation stage to the stage of partial innovation in the field of iron and steel. The localization rate of equipment increased from 12.5% to 63.1%. The enterprise production scale expanded unceasingly, and the product price was the most competitive in the world. The quality of the hot rolling products reached its highest level ever.
Third, entering the new age of technological innovation (after the 1990s). In order to support the sustainable development of enterprises, POSCO accelerated its innovation and formulated the medium- and long-term technology development strategy and plan; the research focus transferred from solving the existing problems to meeting the future development demand; while continuous improvement of production efficiency and product quality went on, the adjustment of product structure, reduction of the cost, the development of the next generation of iron and steel technology and basic technology R&D were the focus. Therefore, POSCO devoted more energy to innovation: The first was a widespread collection, sorting, and analysis of foreign information; talents and funds sharply tilted towards the high technology R&D projects; internal and external resources were integrated to tackle key problems together. The second was to establish an efficient innovation system, to cultivate a large number of innovative talents and integrated technology development capability, and to achieve technological results with independent IPR. At the end of the 1990s, POSCO's production capacity exceeded that of Nippon Steel and became the world's largest steel enterprise; besides its price advantage, the quality and variety of its products had reached the level of Japan's. The third was the formulation of the “medium- and long-term technology development plan” in the 21st century, centering on traditional technology and strategic product technology, selecting 12 strategic projects for R&D, and focusing on developing special high-performance steel.
(4) Samsung
Samsung was the OEM of a small, black and white television made by the Japanese company Sanyo based on the “imitation strategy,” which meant that Sanyo provided Samsung with product technology, design, and parts. Samsung was the production workshop of Sanyo for organizing production. Even in the early 1980s, Samsung had also depended on the imitation strategy to open the dynamic RAM (DRAM) market. But according to the technical agreement signed with foreign companies at that time, it was very difficult for Samsung to obtain basic assembly technology other than the key technologies; Samsung had to obtain this from various other channels on the one hand, while on the other hand, the implementation, adoption, and improvement of the key techniques came from within the company. Through imitative improvement, Samsung was finally able to produce black and white televisions that meet the demand of the Korean people. Following the television, Samsung developed the 14-inch color TV (1976), the microwave oven (1979), the home video recorder (1984), the IM DRAM (1986), the portable video machine (1989), etc. Since then, Samsung has begun to implement the strategy of “keeping up with the technology leader.” After years of actively learning, adopting, and training, in the late 1980s and mid-1990s, the technology development ability and the technical level of Samsung's products had caught up with the world's most advanced companies. The gap had been narrowed significantly. In some fields, Samsung was close to or even equal to them, so was the speed of product launching. At that time, Samsung had made great achievements in electronics and had strong development ability.
Chairman of Samsung Lee Kun-hee put forward the grand blueprint of “making Samsung a world-class enterprise” in 1993. Samsung was eager to enter the high-end electronics market; the technology it needed was also more advanced. However, Samsung couldn't be completely independent of external companies, so it acquired and caught up with advanced technology in a variety of ways. On the one hand, it merged with other high-tech enterprises; on the other hand, it formed alliances with enterprises occupying the cutting-edge technology position and shared technology. As a result, in fewer than 40 years, Samsung climbed up the growth ladder of “imitator, follower, leader, and world-class enterprise.” Its market expanded from low-end to high-end and spread out across the board. In the late 1990s, Samsung was fully able to guide the market demand with the most advanced technology, meet the high-end market demand, and win a plurality of firsts in the world. Samsung's success enlightens the industry in the following ways.
First, technology accumulation in the proper path of technology acquisition. i) Reverse breaks. Samsung imported components and parts with advanced technology which could not be produced by itself. After the introduction, not satisfied being just an OEM, Samsung began to decompose, learn, imitate, improve, and innovate. ii) Samsung employed foreign researchers of Korean origin to research and develop domestically. Every enterprise can do this at any stage, but this is especially suitable for the start-ups. iii) Samsung had the ability to introduce technology from small companies in advanced countries. Because the technical barriers of large companies were seriously high, the acquisition of high-end technology from them was impossible. Thus, purchasing advanced technologies from small companies that needed cash flow was a feasible solution.
Second, great expenditure on R&D and super government support. Samsung's turnover in 1997 was $15.3 billion, its gross profit$4.8 billion, but its investment in R&D was more than $1 billion every year. However, industrial investment depended on borrowing money, so that the debt to asset ratio was as high as 223% in 1997. At the same time, the government supported local key enterprises like Samsung and Hyundai with the strength of the whole country. The government provided guarantee for the huge loan of these enterprises. The numbers were several times the enterprises' net assets.
(5) Hyundai
The development of Hyundai has experienced five stages: i) The initial stage of assembly (1962-1966). The Kia, Hyundai, and other enterprises began to assemble cars using foreign technology. ii) The early stage of improvement and localization (1967-1971). The government focused on supporting the auto industry to enter into the stage of localization. The auto industry formed a distinctive production management model and an industrial development pattern. iii) The stage of developing domestic cars and preparing for exportation (1972-1976). In 1972, Hyundai began to invest independently in the development of domestic cars and the construction of the car factory with an annual production capacity of 80,000. In this stage, the localization level had a substantial increase, production technology went from simple assembly to independent development. iv) The stage of mass production and experimental exportation (1977-1981). The mass production system of the auto industry formed basically. Headed by Hyundai, each manufacturer also adjusted the strategic focus from the domestic market to the international market. v) The stage of consolidating the export base and promoting internationalization (1982-present). The Korean auto industry entered the international market on a large scale. The export quantity in 2004 was 2.3 million, the automobile has become Korea's leading export industry. The development of the Korean auto industry is a typical example with all the characteristics of Korean independent innovation.
First, introduction of technology and independent innovation into Korean auto enterprises. The technological innovation of Korean auto enterprises has experienced three stages. The importation of technology was the main content of the initial period of the development of the auto industry. In this stage, cars were mainly produced by SKD (semi-complete knock down) assembly. Then, the auto industry worked with Toyota and began to produce independently according to the CKD (complete knock down) method. In the 1970s, adoption and improvement was the theme. The government required that each company should select a vehicle model and develop the complete domestic car. In 1976, the localization rate of the major Korean auto enterprises was above 85%. At the same time, the auto production capacity increased (especially the production capacity of automobile parts). The auto enterprises spared no effort in cultivating their ability for independent innovation; Hyundai was a successful example. Its main products were cars and commercial vehicles. In 1974, Hyundai started to introduce the technologies of engine assembly, gearbox, and rear axle construction from the Japanese company Mitsubishi, while at the same time, they invited Italian companies to design the model and the body of the car. From the beginning of the 1980s, the Korean auto industry stepped into the independent development stage. In this stage, Korean car companies put product development in the most important position, emphasized the development of their own cars, built strong product development institutions, and trained developers. These enterprises invested a lot of development funds in cooperating with foreign enterprises. In 1986, the cost of R&D in Hyundai and Daewoo accounted for 4% of the sales and reached the level of advanced countries (3%-5%). Hyundai had more than 2,000 R&D personnel, and Daewoo about 500. The high input of production equipment and scientific R&D resulted in the development of various types of vehicles from the three companies of Hyundai, Daewoo, and Kia successfully, including various systems and all kinds of parts and components, such as the body, the chassis, the engine, etc., thus they entered into the stage of independent development.
Second, the support of the government for the independent development of the auto industry. In the process of developing the auto industry, the government provided the enterprises with powerful protection and support. Under relatively restricted conditions, the Korean auto industry achieved scale economy by mergers and rapid expansion. Through the introduction of technology and persistent localization, the Republic of Korea realized the leapfrogging development of industrial technology and developed an independent and completely national auto industry system. The government provided the enterprises and market with protection in many aspects. The government reduced the production cost of local cars and encouraged automobile exportation through a variety of subsidies and preferential measures. From 1962 to 1990, the Republic of Korea formulated a series of regulations and policies for fostering the development of the auto industry. At the same time, the government set up all kinds of tariff and non-tariff barriers to limit the importation of foreign cars, so that domestic auto enterprises were free from foreign competition.