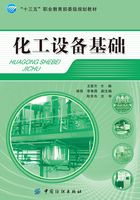
第二节 开孔与补强
一、开孔类型及对容器的影响
1.开孔类型
为了实现正常的操作和安装维修,需要在设备的筒体和封头上开设各种孔。如物料进出口接管孔,安装安全阀、压力表、液面计的开孔,为了容器内部零件的安装和检修方便所开的人孔、手孔等。
2.开孔对容器的影响
开孔会造成容器的整体强度削弱,设备结构的连续性被破坏,使孔边局部区域内出现应力集中。应力集中会影响压力容器的安全,因此,需要尽量降低应力集中,孔周围的应力集中现象有如下特点。
(1)开孔附近的应力集中具有局部性,其作用范围极为有限。
(2)开孔孔径的相对尺寸(d/D)越大,应力集中系数越大,所以开孔不宜过大。
(3)被开孔壳体的d/D越小,应力集中系数越大,将开孔四周壳体厚度增大,则可以明显地降低应力集中系数。
(4)增大接管壁厚也可以降低应力集中系数,因此可以用增厚的接管来缓解应力集中程度。
(5)在球壳上开孔,应力集中程度较圆筒上开孔低,因此,在椭球封头上开孔优于在筒体上开孔。
二、对容器开孔的限制
综上所述,压力容器开孔后会引起应力集中,从而削弱容器强度。为降低开孔附近的应力集中,必须采取适当的补强措施。根据国家标准GB 150 —2011《压力容器》规定,按等面积补强准则进行补强时,开孔尺寸按以下限制开孔。
(1)当圆筒内径Di≤1500mm时,开孔最大直径d≤Di/2,且d≤520mm;当圆筒内径Di>1500mm时,开孔最大直径d≤Di/3,且d≤1000mm。
(2)凸形封头或球壳上开孔时,开孔最大直径d≤Di/2。
(3)锥壳上开孔时,开孔最大直径d≤Di/3,Di为开孔中心处锥壳内径。
(4)在椭圆形或碟形封头的过渡区开孔时,孔的中心线宜垂直封头表面。
若开孔直径超出以上范围,应按特殊开孔处理。GB 150 —2011《压力容器》还规定,壳体开孔满足下列全部条件时,可不另行补强(可不采取专门的补强措施)。
(1)设计压力不超过2.5MPa。
(2)两相邻开孔中心的间距(对曲面间距以弧长计算)应不小于两孔直径之和的两倍。
(3)接管外径不超过89mm。
不另行补强的接管外径及其最小壁厚如表2-9所示。
表2-9 不另行补强的接管外径及其最小壁厚
此外,开孔还应注意满足下列要求。
(1)尽量不在焊缝上开孔。如果必须在焊缝上开孔时,则在以开孔中心为圆心,以1.5倍开孔直径为半径的圆中所包含的焊缝,必须进行100%的无损探伤。
(2)在椭圆形或碟形封头过渡部分开孔时,其孔的中心线应垂直于封头表面。
三、补强结构
为了保证压力容器在开孔后能安全运行,常采用补强圈补强、厚壁接管补强和整体锻件补强来降低开孔附近的应力集中。三种开孔补强常见结构如图2-5所示。
图2-5 三种开孔补强结构图
1.补强圈补强
补强圈补强是在开孔周围焊上一块圆环状金属来补强的一种方法,也称贴板补强,焊在设备壳体上的圆环状的金属称为补强圈。补强圈可以是一对夹壁焊在器壁开孔周围,由于施焊条件的限制,也可以采用把补强圈放在容器外部进行单面补强,如图2-5(a)、(b)所示。补强圈补强结构简单、价格低廉、使用经验成熟,广泛用于中压、低压容器上。但它与补强管补强和整体锻件补强相比存在以下缺点。
(1)补强圈所提供的补强金属过于分散,补强效率不高。
(2)补强圈与壳体之间存在一层空气,传热效果差,在壳体与补强圈之间容易引起热应力。
(3)补强圈与壳体焊接时,焊件刚性大,焊缝在冷却时易形成裂纹,尤其是高强度钢,对焊接裂纹比较敏感,更易开裂。
(4)由于补强圈没有和壳体或接管金属真正熔合成一个整体,因而抗疲劳性能差。
由于存在上述缺点,采用补强圈补强的压力容器必须同时满足以下条件。
(1)壳体材料的标准抗拉强度不超过540MPa,以免出现焊接裂纹。
(2)补强圈的厚度不超过被补强壳体的名义壁厚的1.5倍。
(3)被补强壳体的名义壁厚不大于38mm。
此外,在高温、高压或载荷反复波动的压力容器上,最好不要采用补强圈补强。
2.厚壁接管补强
厚壁接管补强也称补强管补强,即利用在补强有效区内的接管管壁多余金属截面积,补足被挖去的壳壁承受应力所必需的金属截面积,如图2-5(d)~(f)所示。这种结构由于用来补强的金属全部集中在最大应力区域,因而能比较有效地降低开孔周围的应力集中。图2-5(f)所示的结构比图2-5(d)、(e)效果更好,但内伸长度要适当,如过长,补强效果反而会降低。补强管补强结构简单、焊缝少、焊接质量容易检验、效果好,已广泛使用于各种化工设备,特别是高强度低合金钢制造的化工设备一般都采用此结构补强。对于重要设备,焊接处还应采用全焊透结构。
3.整体锻件补强
整体锻件补强是在开孔处焊上一个特制的整体锻件,结构如图2-5(g)~(i)所示。它相当于把补强圈金属与开孔周围的壳体金属熔合在一起。补强金属是全部集中在应力最大的部位,而且它与被开孔的壳体之间采用的都是对接接头,受力状态较好,因此,整体锻件补强的补强效果最好,同时能使焊缝及热影响区远离最大应力点的位置,故抗疲劳性能好。若采用密集补强的方式,并加大过渡圆角半径,则补强效果更好。整体锻件补强的缺点是机械加工量大,锻件来源较补强接管困难,因此多用在有较高要求的压力容器和设备上。
四、标准补强圈及其选用
1.标准补强圈
为了使补强设计和制造更为方便,中国对常见的补强圈及补强管制定了相应的标准,补强圈标准为JB/T 4736—2002,补强管标准为HG/T 21630 —1990。标准补强圈的直径和厚度是按等面积补强法计算而得出的。
2.标准补强圈结构
根据内侧焊接坡口的不同,补强圈分为A、B、C、D、E、F六种结构,如图2-6所示。
(1)A型适用于无疲劳、无低温及大的温度梯度的一类压力容器,且要求设备内有较好的施焊条件。
(2)B型适用于中压、低压及内部有腐蚀的工况,不适用于高温、低温、大的温度梯度及承受疲劳载荷的设备。δ取管子名义壁厚的0.7倍,一般δnt=δn/2(δnt为接管名义厚度;δn为壳体名义厚度)。
(3)C型适用于低温、介质有毒或有腐蚀性的操作工况,采用全焊透结构,要求当δn≤16 mm时,δnt≥δn/2;当δn>16mm时,δnt≥8mm。
图2-6 标准补强圈结构
(4)D型适用于壳体内不具备施焊条件或进入设备施焊不便的场合,采用全焊透结构,要求当δn≤16mm时,δnt≥δn/2;当δn>16mm时,δnt≥8mm。
(5)E型适用于储存有毒介质或腐蚀介质的容器,采用全焊透结构,要求当δn≤16mm时,δnt≥δn/2;当δn>16mm时,δnt≥8mm。
(6)F型适用于中温、低温、中压容器及盛装腐蚀介质的容器,要求当δn≤16mm时,δnt≥δn/2,当δn>16mm时,δnt≥8mm,且接管公称直径DN≤150mm。
补强圈焊接后,补强圈和器壁要求很好地贴合,使其与器壁一起受力,否则起不到补强作用。为检验焊缝的紧密性,在补强圈上设置有一个M10的螺纹孔,如图2-6所示。当补强圈焊接后,可以由此通入0.4~0.5MPa的压缩空气,并通过在补强圈焊缝周围涂上肥皂液的方法检查焊接质量。
3.标准补强圈的选用
若需采用补强圈补强,可采用以下程序来选择标准补强圈。
(1)确定补强圈的尺寸。
(2)由设备的工艺参数决定补强圈的结构。
(3)补强圈材料选取与被补强壳体材料相同。
五、人孔、手孔及接管
1.人孔和手孔
为了设备内部构件的安装和检修方便,需要在设备上设置人孔或手孔。当容器的内径为450~900mm时,一般不考虑设置人孔,可开设1~2个手孔;内径大于900mm时至少应设置一个人孔;设备内径大于2500mm时,顶盖与筒体上至少应各开设一个人孔,常见的常压快开人孔如图2-7所示,常见受压人孔如图2-8所示。
图2-7 常压快开人孔
图2-8 受压人孔
2.接管
化工设备上使用的接管大致可分为两类,一类是通过接管与供物料进出的工艺管道相连接,这类接管一般都是带法兰的接管,直径较粗;另一类接管是为了控制工艺操作过程,在设备上需要装设一些接管,以便和压力表、温度计、液面计等相连接。此类接管直径较小,可用带法兰的短接管,也可用带内、外螺纹的短管直接焊在设备上。