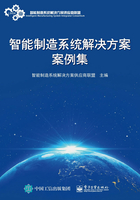
案例1 中压空气绝缘开关设备制造数字化车间—北京机械工业自动化研究所有限公司
北京机械工业自动化研究所有限公司(以下简称北自所)创建于1954年,是原机械工业部直属的综合性科研机构,1999年转制,现为国务院国资委监管的大型科技企业。北自所致力于制造业领域自动化、信息化、集成化、智能化技术的创新、研究、开发和应用,为客户提供包括开发、设计、制造、安装和服务的整体解决方案,是离散制造领域智能制造系统集成的卓越实践者和引领者。
北自所注册资金1.8亿元,年销售收入20亿元。业务覆盖智能工厂3个层级,从设备层、车间层到企业层;贯穿智能制造6大环节,从智能加工、智能装配、智能检测,到智能物流、智能监控、智能管理。主要包括自动化柔性物流与仓储系统,汽车、电子、电气自动装配线,金属带材自动化加工生产线,拉伸薄膜自动化生产线,水利、电力自动化控制系统,以及 MES、ERP 等信息化软件。因此,北自所有能力为客户提供单元设备—生产线/成套设备—数字化车间/智能工厂的整体解决方案。
第1章 简介
1.1 项目背景
自“十一五”开始,国家投入巨资对我国电网进行智能化改造,带动了中压空气绝缘开关设备制造行业的持续增长。现在我国已成为中压空气绝缘开关设备的生产大国,根据高压开关行业协会统计,2011年全行业共生产12~40.5kV中压真空断路器592 018台、12~40.5kV中压成套开关设备360 748台,占世界总产量的50%以上,但我国还不是中压空气绝缘开关设备制造的强国。
国外中压开关设备制造行业具有代表性的企业(如 ABB、西门子等公司)已广泛应用数字化车间的相关技术,对生产状态、物流状态、人员作业状态进行实时监控。通过利用现代物联网技术、数字化技术、信息化技术、多媒体技术等实现车间装备和制造过程的精细、实时、透明管控;采用自动化装配线生产方式,利用计算机系统进行控制,通过采用条码、RFID等数字化技术实现无纸化生产;在制造中不仅能监控生产过程,而且能收集产品的生产数据;配套物流系统也广泛实现自动化和数字化,大部分零部件采用自动化仓储及配送,实现各种零部件的统一管理与迅速成套。
近年来,我国中压开关设备制造业通过技术引进、合作生产、技术交流等多种途径,产品设计的能力已部分达到了国际先进水平,但受到制造能力和工艺水平的限制,无法成规模地进行生产制造,极大地阻碍了中压开关行业技术水平的整体提升。为提升国内中压开关设备生产行业制造水平,缩小国内开关行业与国际先进水平的技术差距,基于制造强国战略,由北京机械工业自动化研究所有限公司与天水长城开关厂有限公司(以下简称天水长开)共同建设的“中压空气绝缘开关设备制造数字化车间”项目,以“产品升级、装备升级、产能升级、管理升级”为发展目标,在中压开关设备生产行业建立了一个具有示范意义的数字化车间。
该项目于2012年11月开工,2015年6月建设完成并投入生产,并在2015年被工业和信息化部(以下简称工信部)批复为“国家智能制造专项”项目。2016年11月20日通过了财政部、工信部智能制造专项验收。
1.2 案例特点
本项目以《中国制造2025》中电力装备领域离散型智能制造的相关内容为目标。作为电力设备制造行业的数字化车间,涉及柔性制造生产线、智能化在线检测装置、物流及仓储系统、信息化生产管理等多个领域。具有多领域技术整合、创新应用融合的特点,是在中压开关设备制造行业实施智能制造系统集成,建设数字化生产制造平台的首次尝试。
在具体实施过程中,通过车间自动化生产和物流装备的研制与应用,为建立制造模型、管理模型、质量模型提供硬件基础,并在此基础上构建产品设计数字化、管理过程信息化、制造执行敏捷化的硬件平台。所建立的中高压开关设备智能制造系统对天水长开已有的ERP系统与底层生产设备信息系统进行了连接,其创新融合主要体现在3个方面。
(1)通过企业资源计划管理系统(ERP)、产品数据管理系统(PDM)、仓储管理系统(WMS)以及制造执行系统(MES)等,采用检验工序化、加工设备数控化、关键设备智能化、仓储物流自动化、车间管理信息化等相关技术纵向和横向的集成,实现了销售业务一体化、制造模型分线化、计划分层化、设备管理信息化、物料项目化、成本控制明晰化、主数据集中化、制造流程模型化、检验数据实时化。
(2)建成了3条空气绝缘开关元件装配检测分系统、3条空气绝缘开关设备装配检测分系统、开关设备箱壳制造分系统、开关设备母线制造分系统、开关设备二次线束制造分系统、开关元件主回路制造分系统、自动化仓储及物流分系统等11个生产制造分系统,实现了生产和物流的自动化和信息化。
(3)MES 系统采取独有的双架构模式,分管理平台和现场操作平台,管理平台采用B/S架构,基于浏览器方式访问系统,系统部署维护简单,客户端登录便捷;现场操作平台采用C/S架构,系统运行稳定、可靠,支持与终端设备接口的多样性与方便性。实现了对多品种柔性生产的自动支持及制造计划、备件计划、配套计划、返修计划等多种生产组织模式的统一管理。
第2章 项目实施情况
本项目由天水长开负责项目策划、筹资及组织验收,由北京机械工业自动化研究所有限公司负责整体规划及总包实施。
2.1 需求分析
2.1.1 项目实施单位和用户情况
项目实施团队是北京机械工业自动化研究所有限公司电气物理设备技术工程事业部(简称电物理事业部),设有专业配套的科研队伍,由工程物理、理论物理、机械工程、工业自动化、高压/高频电磁场技术、真空技术、测量/检测计算机技术、机械工程工业自动化等多方面技术人才构成强大的技术队伍,技术力量雄厚,具有较强的研究、设计、制造、安装调试、运行和实验的能力。团队在电器行业具有丰富的开发和研制经验,成功研制了中/低压断路器的壳体、主轴机器人焊接工作站、低压(塑壳、微型)断路器装配检测生产线与相关单台检测设备、真空断路器装配及检测自动化生产线、开关柜装配及检测自动化生产线、自动化仓储及物流系统、制造执行系统(MES)、企业ERP管理系统,为客户提供数字化车间的整体解决方案。目前客户主要有施耐德、ABB、GE、库柏耐吉、安徽森源、正泰电器、平高电气、西电宝鸡电气、青岛益和电气等国内外知名企业。
项目使用单位天水长城开关厂有限公司是国内规模最大的中压开关设备制造企业之一,兰州长城电工股份有限公司的龙头子公司,在国内中高压开关设备研发、制造及销售领域一直处于领先地位,各项技术经济指标在国内高压开关行业名列前茅。在国内火电、石化、冶金等大中型重点工程领域的市场占有率保持在30%以上,部分领域达到70%以上。2007年,天水长开入选中国机械500强,同年被中国机械工业联合会评选为中国机械工业优秀企业和中国机械工业最具影响力品牌,被中国电器工业协会评选为中国电器工业最具影响力企业。天水长开还被科技部等三部委认定为“国家创新型企业”,被国家知识产权局认定为“国家知识产权示范企业”。天水长开技术中心被国家发改委等五部委认定为“国家认定企业技术中心”。天水长开的技术创新成果、管理体系、生产制造技术等在国内同行业均处于领先地位。
2.1.2 行业生产现状
纵观国内电力工业,供给侧改革客观上要求改善供应方式,提高供给效率,增强系统运行灵活性和智能化水平。为全面增强电源与用户双向互动,提升电网互济能力,实现集中和分布式供应并举,传统能源和新能源发电协同,增强调峰能力建设,提升负荷侧响应水平,建设高效智能电力系统成为必然选择。因此《电力发展“十三五”规划(2016—2020年)》提出以“智能高效、创新发展”的原则升级改造配电网,推进智能电网建设,满足用电需求,提高用电质量,着力解决配电网薄弱问题,促进智能互联,推动装备提升与科技创新,加快构建现代配电网。国内开关行业纷纷开发技术先进的产品,满足市场需求。但由于受制造技术的限制,国内中压开关设备与国际同类产品相比仍然存在较大差距,国内中高压开关设备的高端市场,基本被国外企业(ABB、西门子等)所垄断。
作为国内具有示范效应的龙头生产企业,天水长开面临产品实物质量相对较低、生产效率相对低下、生产能耗相对较高等问题,迫切需要通过运用智能制造技术,提升产品质量、提高生产效率、降低生产能耗,进而扩大市场占有规模,在行业中继续发挥示范作用。
2.2 总体设计情况
2.2.1 项目总体技术架构
中压空气绝缘开关设备制造数字化车间占地面积2.3万平方米,由空气绝缘开关设备装配检测分系统、空气绝缘开关元件装配检测分系统、开关设备箱壳制造分系统、开关设备母线制造分系统、开关设备二次线束制造分系统、开关元件主回路制造分系统、自动化仓储及物流分系统、制造执行系统组成,主要系统结构图如图1所示。可实现12~24kV及40.5kV空气绝缘开关元件与成套设备由原材料、基础零件到完整成品的自动化、规模化生产。达到年产6万只灌封极柱、1.8万台真空断路器、1.5万套成套设备的生产能力。

图1 中压空气绝缘开关设备制造数字化车间主要系统结构图
2.2.2 项目总体实施路线
项目结合天水长开现有的三维CAD、PLM等系统,使产品信息贯穿于设计、制造、质量控制、物流等环节;针对高压开关设备生产制造的要求,通过建立产品模型、制造模型、管理模型、质量模型等数学模型,在贯穿设计、加工(处理)、装配检测、质量控制、物流、服务的各环节,建成一套完整的中高压开关设备智能制造系统。并在实施中运用离散型智能制造新模式,集产品设计智能化、钣金加工智能化、仓储物流智能化、车间调度管理智能化于一体,使总体技术达到国内领先水平。本项目使用ERP II实现企业管理信息化;应用MES实现车间管理信息化;将ERP和全套底层生产与物流自动化、智能化装备及系统纵向集成,实现检测与加工的数字化、关键设备智能化、仓储物流自动化。
2.3 实施步骤
2.3.1 项目阶段划分
根据项目实施中具体的工作内容,项目分为前期调研、方案设计、生产制造、现场联调、技术培训、试产验收等阶段,实施周期为两年。
2.3.2 项目建设内容和关键技术应用
1.项目建设内容
数字化车间包括8个相互关联的分系统,各分系统相互协同,发挥不同的作用,共同构成完整的智能化制造系统。各分系统的组成及功能说明如下。
1)空气绝缘开关设备装配检测分系统
该分系统包括两条12~24kV 及一条40.5kV 空气绝缘开关设备(铠装柜)自动化生产线,可完成铠装柜的拼柜、机构装配、一次元件安装、二次元件安装、仪表箱安装、耐压试验、终检测试等工序,实现开关设备由零部件到成品的全程流水线方式批量生产。
2)空气绝缘开关元件装配检测分系统
该分系统包括两条12~24kV 及一条40.5kV 空气绝缘开关元件(真空断路器)自动化生产线,可完成真空断路器的操作机构装配、一次主回路装配、机械磨合、机械特性测试、耐压测试、开关元件尺寸检测、终检测试等工序,实现开关元件由基础零件到完整成品的自动化生产。
3)开关设备箱壳制造分系统
开关设备箱壳制造分系统包括全自动钣金立体仓库、数控转塔冲剪复合单元、数控转塔冲床、数控折弯机、液压摆式剪板机、全自动折弯工作站。实现钣金材料集中化管理和钣金零部件自动化加工。
4)开关设备母线制造分系统
开关设备母线制造分系统包括全自动母线立体仓库、数控母线冲剪一体机、三工位母线加工设备、数控母线折弯一体机、数控母线圆弧加工中心、母线打磨加工设备、全自动母线清洗设备、间歇式废水处理设备、干式母线喷漆设备、超声波母线搪锡设备、母线热缩套管加工设备等。可完成母线零件的冲孔、切断、压花、铣角、打磨、折弯、清洗、搪锡、喷漆、热缩等多种不同工序的全流程加工制造。
5)开关设备二次线束制造分系统
二次线束制造系统主要由全自动电缆线束加工系统、SuperWORKS 工程软件、配线台案等工位器具组成,可将由导线CAE系统自动生成的开关设备内二次导线线束相关信息自动输入线号打印机、下线机,完成切线、剥线、线号打印、端头压接等工艺环节的全过程自动化加工,实现二次导线的自动化批量生产。
6)开关元件主回路制造分系统
开关元件主回路制造分系统包括极柱装配台、极柱灌封单元,以及多通道数字式局部放电综合分析仪、校准脉冲发生器及其附件、试验自动控制系统软件、高压试验系统、试验屏蔽室等,可完成固封主回路灌封以及局部放电检测等。
7)自动化仓储及物流分系统
自动化仓储及物流分系统包括一个四巷道3876货位的自动化立体仓库、四台巷道堆垛机,以及用于存放不规则物体的大件库和地堆区,可实现车间物料集中存储及自动输送。
自动化仓储及物流分系统通过仓库管理系统(WMS)配合先进的控制、总线、通信和信息技术,实现相关设备的协调动作,在充分利用储存空间的前提下,完成指定物料自动有序、快速高效的入库出库作业。
8)制造执行系统(MES)
MES 作为企业信息化建设的中间层,专注于制造执行过程的管控一体化,在企业总体信息流中起着承上启下的关键作用。本项目的MES系统由15个功能模块组成,即系统平台、基础数据管理、计划排程管理、配送及线边管理、物料管理、生产过程管理、在制品管理、质量管理、下线包装管理、设备管理、文档管理、数据平台、报表管理、系统接口及Andon系统。
MES可上接ERP、PDM等管理系统,下连生产线、专机设备等底层控制系统,实现上层指令的下达执行,以及底层数据的实时采集、反馈,综合管理制造过程计划、装配、物料、质量、设备运行监控等业务流程,实现制造过程物流、信息流的统一管理。
各子系统之间、子系统与ERP之间的信息关系如图2所示。
2.关键技术的应用
本项目数字化制造车间所依托的数字模型包括产品模型、制造模型、管理模型、质量模型。通过优化配置整合互联互通的产品全生命周期管理系统(PLM)、企业资源计划管理系统(ERP)和车间制造执行系统(MES),在统一数据平台的基础上,建立不同的数字模型,实现基于模型的数字化产品设计、信息化企业管理和敏捷化制造。

图2 各子系统之间、子系统与ERP之间的信息关系图
其中产品模型包括产品设计大纲,试验试制大纲,关键性能控制方法等,实现以数字化制造为纲的生产流程及物流配送载体的工艺要求,满足按工序装配方法的需求。
制造模型包括满足均衡生产的控制方法,提高按计划作业和按计划配送的保障策略,遵循制造对象的自动匹配原则和按合同要求匹配的柔性原则,实现以数字化制造为纲的库存策略,以及按节拍、节点、对象的配送方法,达到计划物料和采集对象相匹配、对应的容忍原则等。
与信息化管理所对应的管理模型包括基于生产线生产能力的最低资源匹配要求,基于缩短生产周期和降低生产成本的方法,生产计划的批次分解原则和基于资源提高物料配送能力的相关策略。在数字化制造前提下,以制造模型的优化为目标,对产品模型进行优化;以生产节拍为导向对制造模型进行优化;以质量数据比对分析为依据,对质量模型及时进行修正;以物流配送需求为前提,对管理模型进行修正的系统方法和信息化系统的实现机制与平台;以作业计划为纲,以全车间协调统一为前提,实现对产品模型、制造模型、管理模型、质量模型完整性和关联性的数据检查机制和发布机制。
质量模型包括产品检验大纲、测试方法、检验标准、检验报告格式,关键零部件质量、性能、参数控制,重点监测对象及预警机制,数据采集标准及比对分析,偏离调整分析和策略;以数字化制造为纲,按照产线工序节拍要求的数据匹配原则,建立数据存储架构等内容。在建立上述数字模型的基础上,安全可控智能制造手段所具有的先进、高效的优势得到充分发挥。
数字化车间的运行包含车间运行管控系统及底层的数字化设备。车间运行管控系统是实现智能化制造的核心,它包括制造执行系统(R-MES)、目视化管理、仓储管理(WMS)、设备监控等生产现场运行管控系统。运行管控系统从企业资源计划系统(CTCS-ERP)接收命令,下达到各个分系统生产单元或设备,并监控分系统和设备的运行状态,处理生产现场的各种问题,根据实际生产状态进行调度。底层的数字化设备包括智能化输送设备、在线检测设备、现场控制计算机、自动化仓储和运输设备等。通过设备配置的数字化接口和工业以太网,实现生产过程的监控和调度。
底层的数字化设备包括智能化输送设备、在线检测设备、现场控制计算机、自动化仓储和运输设备等。通过设备配置的数字化接口和工业以太网,实现生产过程的智能化监控和调度。本项目所有分系统中的生产线均配置智能检测装置,并在主要生产工位上配置精益电子看板。关键生产环节采用国产化设备或具有自主知识产权的核心技术,形成安全可控的智能制造体系。
第3章 实施效果
3.1 项目实施效果
3.1.1 企业提升效果
中压空气绝缘开关设备制造数字化车间立足于企业实际,结合企业需求,在实事求是、因地制宜的基础上,改善了工艺流程,提高了产品质量,提高了生产效率。数字化车间集产品设计的数字化、钣金加工的自动化、仓储系统的智能化、车间调度管理的信息化、断路器视觉检测的智能化于一体,实现天水长开的“三个升级”,即产品升级、产能升级、管理升级,并继续引领行业的发展。
1.产品升级
通过数字化车间项目的实施,建设先进的中压开关元件、设备装配生产线及配套系统,提高了产品稳定性和质量一致性,为实现近年来开发的具有自主知识产权,技术性能达到国内乃至国际领先水平的新一代产品的产业化生产创造了条件。通过产品升级拓展了其在中高压电气行业装备制造领域的市场。为天水长开“十二五”转型跨越式发展奠定坚实的基础。
2.产能升级
该项目的顺利实施提升了天水长城开关厂中压开关元件及开关设备的产能,项目投产后,天水长城开关厂在未增加人员的情况下,成套开关设备年生产能力从8000套提高到15 000套,开关元件年生产能力从8000台提高到18 000台。
3.管理升级
本项目通过数字化车间的建设,从车间的总体角度出发,对生产设备、物流设备、在线自动检测设备等引入数字化和智能化技术,并引入MES系统等先进的管控方法,可有效提高天水长开生产管理水平,降低生产人员劳动强度,实现人性化管理,并同时降低生产对工人技能的依赖程度,有利于人力资源管理。另一方面,项目设计中充分考虑环境保护和节能措施,有利于清洁生产和低碳生产管理。
天水长开是国内中压开关设备行业技术与品质的引领者,产品技术和制造技术备受国内同行业的关注,本项目研制的数字化车间在该公司首先投产后,在中压开关行业具有典型的示范作用,对促进区域电工电气产业集群化发展,打造国家西部电工电器城具有重要现实意义。
3.1.2 行业影响及作用
1.对中高压开关行业技术进步的带动作用
通过本项目的实施,研制并应用了新一代小型智能化中高压气体开关设备离散型智能制造系统,可实现清洁生产,降低生产耗能,提高劳动生产率,降低经营成本,并为节能和环保做出应有的贡献。
天水长开是国内中高压开关设备行业技术和品质的引领者,本项目为天水长开建成的中高压气体绝缘开关设备智能制造系统将成为中高压开关行业技术改造的典范,并在中高压开关行业技术改造中得到推广应用。
2.对电工电器行业的示范作用
我国电工电器大多数行业,如变压器、电机、继电器等的制造和开关行业极其相似,都是典型的以销定产模式,本项目实施的中高压开关设备智能制造系统,对电工电器行业的绝大多数企业具有示范作用。本项目通过科技成果展示、论文等形式向国内开关行业推介,将为我国电工电气行业技术改造发挥示范作用。
3.2 复制推广情况
天水长开数字化车间项目完成后,北自所以此为模板,又先后为西电宝鸡、青岛益和、中航宝胜、特变电工等企业提供了类似的数字化生产车间技术方案并付诸实施。中航宝胜于2017年以此申报工业和信息化部 “国家智能制造专项”项目并获批准。
第4章 总结
本项目利用长城电工天水长城开关厂有限公司现有的CAD、PLM等系统,使产品信息贯穿设计、制造、质量、物流等环节,实现了产品的生命周期管理。历时4年多,建成了3条空气绝缘开关元件装配检测分系统、3条空气绝缘开关设备装配检测分系统、开关设备箱壳制造分系统、开关设备母线制造分系统、开关设备二次线束制造分系统、开关元件主回路制造分系统、自动化仓储及物流分系统等11个生产制造分系统。通过企业资源计划管理系统(ERP)、产品数据管理系统(PDM)、仓储管理系统(WMS)以及制造执行系统(MES)等,采用检验工序化、加工设备数控化、关键设备智能化、仓储物流自动化、车间管理信息化等相关技术纵向和横向的集成,实现了销售业务一体化、制造模型分线化、计划分层化、设备管理信息化、物料项目化、成本控制明晰化、主数据集中化、制造流程模型化、检验数据实时化。该项目建成后,实现了12~24kV 及40.5kV 开关元件与成套设备由原材料、基础零件到成套产品的自动化、规模化生产。具备年产60 000只灌封极柱、20 000台中压开关元件、15 000套中压开关成套设备的能力。标志着天水长开在输配电设备智能制造成套数字化车间、仓储系统的智能化和断路器视觉检测的智能化于一体等方面已步入了一个新阶段。
该项目在装备行业层次较高、带动较强、示范效果较好,符合产业发展方向和国家产业政策,也是首个通过工信部新模式应用智能制造验收的项目,将对我国装备制造业的供给侧结构性改革以及智能化发展起到引领和促进作用;对我国电工电器行业转型升级和提质增效,乃至推动制造业整体智能化升级发挥重要作用。同时,也为我国实现制造强国战略目标奠定了坚实基础。