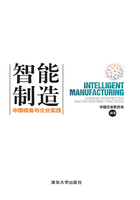
第一节 基于智能广度的三类模式
智能化的广度是指智能化的应用范围是局部还是系统,局部的智能化是指某个环节、工序或车间的智能化,系统智能化是指企业从需求到生产再到物流和销售整个产业链条的智能化,具体表现就是整个企业或工厂的智能化。根据智能化广度可以将中国企业智能制造划分为单点模式、车间模式和工厂模式三类模式。这三类模式的广度依次递进,表征了企业智能制造的不同发展阶段。
一、单点模式
智能制造中的单点模式主要指以单一智能设备为基础的模式,这种模式通过机器人、智能机床等方式,企业最方便地获得柔性生产及节约成本的目的。在我国,新松机器人、沈阳机床的很多客户都是采用这类方式开始对其生产系统进行智能化改造的,通过购置以台为单位的智能制造设备,企业可以大大提高某些生产环节的效率,同时对客户的需求进行更加快速的反应。而在国外,以德国为例,其与智能制造相关的厂商主要分为两类,其中一类便是提供基础设施的,如库卡集团的主要工作是为智能制造提供基础工具和解决方案的支持。库卡集团是由焊接设备起家的全球领先机器人及自动化生产设备和解决方案的供应商之一,客户主要分布于汽车工业领域。库卡为纯工业机器人公司,业务包括工业机器人和系统集成。其独一无二的6D鼠标编程操作机构,使得机器人的操作和示教犹如打游戏一样轻松方便。库卡工业机器人的用户包括通用汽车、克莱斯勒、福特汽车、保时捷、宝马、奥迪、奔驰、大众、哈雷-戴维森、波音、西门子、宜家、沃尔玛、雀巢、百威啤酒以及可口可乐等众多知名跨国企业。
2013年11月5日,库卡推出了低碳环保型绿机器人KRQUANTEC系列,高效高性能搬运、去毛刺应用机器人等产品和先进解决方案,展示了库卡机器人在工业自动化中广泛的应用和机器人领域中的领导地位。通过大量先进的智能制造装备的开发,库卡作为工业机器人世界四大家族之一,创造了机器人行业的众多第一,第一台取消并连杆,摆脱平行四边形局限的单连接机器人,第一台采用户PC控制WINDOWS界面的机器人,第一台工作半径达3.5米的机器人等。库卡最知名的产品是汽车行业的自动流水线,其在奔驰、大众、宝马、福特等大型汽车生产线上的机器人占有率高达95%甚至98%以上,推动了这些客户在生产某些环节的智能化改造,提升了客户的智能化水平。
二、车间模式
相对于单点模式来说,车间模式是对多个单点进行整合,形成类似于一条完整的智能制造生产线的形式,并以此为企业带来智能化的生产模式。国内外有很多企业在进行这方面的尝试,这其中既包括那些为生产制造企业提供解决方案的服务商,也包括一些所谓的智能工厂。
以吉林通用为例。该企业为了适应自动化、数字化和信息化发展趋势,下大气力对企业进行“三化”改造,依托“八大工艺”基础,建立无人化、柔性生产线和数控中心。2006年以来,累计投入约5.2亿元资金,建设世界一流的机械加工、冲压、铝铸和铝锻生产线,新购各种数控装备687台,建立数控中心,以提升产品质量和生产效率,为企业进行自动化、数字化和信息化改造奠定基础。从2006年开始,吉林通用着手打造柔性生产线,淘汰了132台老式专用设备,新上了102台新式通用设备。通用设备采用后,只需切换设备工装,就可以实现生产不同规格型号的产品,既降低了设备总投资,又提高了设备利用效率,更提高了柔性制造能力。2009年以来,又先后建立了4条“无人式”自动冲压生产线,靠机器解放了人力,极大降低了员工劳动强度,提升了内制式生产的智能化水平,有效满足了差异化、个性化的市场需求。
从表面上看吉林通用的改造已经实现了智能工厂的雏形,但由于其改造的范畴并没有涉及从前端的物流管理到后端的客户服务的全过程,在组织和管理层面的改变也相对较少。而在国外,在车间模式下进行的智能化改造也有大量可供参考的案例。Intel公司近年来开始对其生产工厂进行智能化改造,希望形成适应时代发展的“智慧工厂”,其核心是在已经成熟的“Level 8”自动化系统基础上,部署下一代制造执行系统,使其从设备和材料处理到生产全过程实现自动化预测和最佳化处理。
可以看到,以上模式中,企业的智能化改造更多的是集中在自动化的范畴之内,通过对整条生产线或车间的更新换代,来提高生产效率,实现传统无法完成的一些工作。
三、工厂模式
广度最大的一种智能制造模式就是工厂模式,这类模式将智能制造融入到了从研发、采购、物流、生产、销售、售后的全价值链之中,从前端和后端共同实现智能制造对于需求的快速反应,以信息为核心建立起企业全新的运行模式。在我们的调研中,安庆石化和青山工业公司进行了有益探索。
安庆石化公司改变传统的先工程项目建设再开展信息化建设的传统方式,在开展500万吨/年常减压蒸馏装置等10套炼油装置、3套化工装置,以及9万标立/时PSA装置等系统工程改造和建设中,将信息化建设作为一个独立单元与工程建设有机结合,推进工程项目和信息平台同步设计、同步实施、同步投用。在炼油化工工艺、自动检测、运营管理和数据挖掘等方面,实现信息化和工业化的深度融合,探索建设智慧型石化企业。
青山工业公司则是将智能制造融入了库存管理之中,在这一价值链环节上形成了智能制造的基础。为了达到精益生产要求,青山公司推行生产车间零库存的管理方式。在前述分拣配送精准的基础上,生产车间实行“批清批结”的管理制度。具体做法是每一批配送到生产线上的零部件物料是准时准量的,生产车间必须保证整个工单都合格后才能操作系统做下线完工,不允许出现待返修产品在现场长时间停留,以此来保证生产的平顺化和现场的零库存。同时,青山公司推行零部件直送方式。依靠ERP系统下达直送订单,并且对物料交付数量、状态等的准确率要求达到100%,到货时间点的误差为≤正负半小时,同时直送零部件不允许出现剩余库存,即订单数量和消耗需求是一一匹配对应的,保证物料的准时、准地、准量交付。
而国外领先企业则致力于智能制造解决方案的探索。如ABB拥有全面的智能技术,为智能制造提供了产品和解决方案。在造纸行业、智能电网与城市、智能制造与生产、智能家居与楼宇等领域的智能化改造和智能设备研发中均处于领导地位。而西门子致力于成为面向整个产品开发与生产实施以及后续服务的整个过程的整合型供应商,覆盖从产品设计和生产规划直至生产工程以及后续服务的整个过程,即提供智能制造与数字化企业平台。西门子的转型战略专注于数字化,通过“数字化企业平台”将虚拟和现实世界进行融合,实现从车间到公司管理层的双向信息流和数据协同优化,它为制造业的未来提供了卓越的范例。而IBM创造性地将工厂智能化建设分为四个层次:从IT基础设施(Network, Servers)建设到现场仪表和过程控制(Field Control, Sensors)建设,从生产执行(MES)系统建设到企业应用(ERP, CRM)系统的建设。
以上三家国外企业的案例中,都可以看到数据在智能制造的工厂模式中的重要作用,这也将成为未来智能制造领域的必争之地。