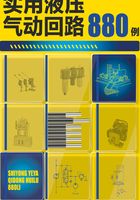
第4章 调速回路
在液压传动系统中,调速回路主要是用来调节执行元件工作速度。调速回路对系统的工作性能起着决定性的影响。调速方式包括:节流调速回路、容积调速回路、容积节流调速回路。
4.1 节流调速回路
4.1.1 进油节流调速回路
4.1.1.1 进油节流调速回路Ⅰ(图4-1和表4-1)

图4-1 进油节流调速回路Ⅰ
表4-1 进油节流调速回路Ⅰ

4.1.1.2 进油节流调速回路Ⅱ(图4-2和表4-2)

图4-2 进油节流调速回路Ⅱ
表4-2 进油节流调速回路Ⅱ

4.1.1.3 进油节流调速回路Ⅲ(图4-3和表4-3)

图4-3 进油节流调速回路Ⅲ
表4-3 进油节流调速回路Ⅲ

4.1.1.4 进油节流调速回路Ⅳ(图4-4和表4-4)

图4-4 进油节流调速回路Ⅳ
表4-4 进油节流调速回路Ⅳ

4.1.1.5 进油节流调速回路Ⅴ(图4-5和表4-5)

图4-5 进油节流调速回路Ⅴ
表4-5 进油节流调速回路Ⅴ

4.1.1.6 进油节流调速回路Ⅵ(图4-6和表4-6)

图4-6 进油节流调速回路Ⅵ
表4-6 进油节流调速回路Ⅵ

4.1.1.7 进油节流调速回路Ⅶ(图4-7和表4-7)

图4-7 进油节流调速回路Ⅶ
表4-7 进油节流调速回路Ⅶ

4.1.1.8 进油节流调速回路Ⅷ(图4-8和表4-8)

图4-8 进油节流调速回路Ⅷ
表4-8 进油节流调速回路Ⅷ

4.1.2 回油路节流调速回路
4.1.2.1 回油路节流调速回路Ⅰ(图4-9和表4-9)

图4-9 回油节流调速回路Ⅰ
表4-9 回油节流调速回路Ⅰ

4.1.2.2 回油节流调速回路Ⅱ(图4-10和表4-10)

图4-10 回油节流调速回路Ⅱ
表4-10 回油节流调速回路Ⅱ

4.1.2.3 回油节流调速回路Ⅲ(图4-11和表4-11)

图4-11 回油节流调速回路Ⅲ
表4-11 回油节流调速回路Ⅲ

4.1.2.4 回油节流调速回路Ⅳ(图4-12和表4-12)

图4-12 回油节流调速回路Ⅳ
表4-12 回油节流调速回路Ⅳ

4.1.2.5 回油节流调速回路Ⅴ(图4-13和表4-13)

图4-13 回油节流调速回路Ⅴ
表4-13 回油节流调速回路Ⅴ

4.1.2.6 回油节流调速回路Ⅵ(图4-14和表4-14)

图4-14 回油节流调速回路Ⅵ
表4-14 回油节流调速回路Ⅵ

4.1.3 旁油路节流调速回路(图4-15和表4-15)

图4-15 旁油路节流调速回路
表4-15 旁油路节流调速回路

4.1.4 进回油同时节流的调速回路(图4-16和表4-16)

图4-16 进回油同时节流的调速回路
表4-16 进回油同时节流的调速回路

4.1.5 双向节流调速回路
4.1.5.1 双向节流调速回路Ⅰ(图4-17和表4-17)

图4-17 双向节流调速回路Ⅰ
表4-17 双向节流调速回路Ⅰ

4.1.5.2 双向节流调速回路Ⅱ(图4-18和表4-18)

图4-18 双向节流调速回路Ⅱ
表4-18 双向节流调速回路Ⅱ

4.2 容积调速回路
容积调速回路是通过改变回路中液压泵或液压马达的排量来实现调速的。其主要优点是没有溢流损失和节流损失,所以功率损失小,且其工作压力随负载变化,所以效率高,系统温升小,适用于高速、大功率系统。
4.2.1 变量泵和液压缸组成的容积调速回路
4.2.1.1 变量泵和液压缸组成的容积调速回路(开式)Ⅰ(图4-19和表4-19)

图4-19 变量泵和液压缸组成的容积调速回路(开式)Ⅰ
表4-19 变量泵和液压缸组成的容积调速回路(开式)Ⅰ

4.2.1.2 变量泵和液压缸组成的容积调速回路Ⅱ(图4-20和表4-20)

图4-20 变量泵和液压缸组成的容积调速回路Ⅱ
表4-20 变量泵和液压缸组成的容积调速回路Ⅱ

4.2.2 变量泵和定量马达组成的容积调速回路
4.2.2.1 变量泵和定量马达组成的容积调速回路Ⅰ(图4-21和表4-21)

图4-21 变量泵和定量马达组成的容积调速回路(闭式)Ⅰ
表4-21 变量泵和定量马达组成的容积调速回路(闭式)Ⅰ

4.2.2.2 变量泵和定量马达(液压缸)组成的容积调速回路Ⅱ(图4-22和表4-22)

图4-22 变量泵和定量马达(液压缸)组成的容积调速回路Ⅱ
表4-22 变量泵和定量马达(液压缸)组成的容积调速回路Ⅱ

4.2.3 定量泵和变量马达组成的容积调速回路(图4-23和表4-23)

图4-23 定量泵和变量马达组成的容积调速回路
表4-23 定量泵和变量马达组成的容积调速回路

4.2.4 变量泵和变量马达组成的容积调速回路
4.2.4.1 变量泵和变量马达组成的容积调速回路Ⅰ(图4-24和表4-24)

图4-24 变量泵和变量马达组成的容积调速回路Ⅰ
表4-24 变量泵和变量马达组成的容积调速回路Ⅰ

4.2.4.2 变量泵和变量马达组成的容积调速回路Ⅱ(图4-25和表4-25)

图4-25 变量泵和变量马达组成的容积调速回路Ⅱ
表4-25 变量泵和变量马达组成的容积调速回路Ⅱ

4.2.4.3 变量泵和变量马达组成的容积调速回路Ⅲ(图4-26和表4-26)

图4-26 变量泵和变量马达组成的容积调速回路Ⅲ
表4-26 变量泵和变量马达组成的容积调速回路Ⅲ

4.2.5 变量泵和流量阀组成的容积调速回路(图4-27和表4-27)

图4-27 变量泵和流量阀组成的容积调速回路
表4-27 变量泵和流量阀组成的容积调速回路

4.3 容积节流调速回路
4.3.1 限压式变量泵调速阀容积节流调速回路(图4-28和表4-28)

图4-28 限压式变量泵-调速阀容积节流调速回路
表4-28 限压式变量泵-调速阀容积节流调速回路

4.3.2 压力反馈式变量泵节流阀容积节流调速回路(图4-29和表4-29)

图4-29 压力反馈式变量泵-节流阀容积节流调速回路
表4-29 压力反馈式变量泵-节流阀容积节流调速回路

4.3.3 差压式变量泵节流阀容积节流调速回路(图4-30和表4-30)

图4-30 差压式变量泵-节流阀容积节流调速回路
表4-30 差压式变量泵-节流阀容积节流调速回路

4.3.4 不带压力调节的比例容积节流调速回路(图4-31和表4-31)

图4-31 不带压力调节的比例容积节流调速回路
表4-31 不带压力调节的比例容积节流调速回路

4.3.5 带压力调节的比例容积节流调速回路(图4-32和表4-32)

图4-32 带压力调节的比例容积节流调速回路
表4-32 带压力调节的比例容积节流调速回路

4.3.6 采用变频器控制的调速回路(图4-33和表4-33)

图4-33 采用变频器控制的调速回路
表4-33 采用变频器控制的调速回路

4.4 有级调速回路
4.4.1 多泵数字逻辑分级调速回路(图4-34和表4-34)

图4-34 多泵数字逻辑分级调速回路
表4-34 多泵数字逻辑分级调速回路

4.4.2 单泵数字逻辑有级调速回路(图4-35和表4-35)

图4-35 单泵数字逻辑有级调速回路
表4-35 单泵数字逻辑有级调速回路

4.5 调速回路应用实例
4.5.1 磨蚀系数试验台液压系统
磨蚀系数是表示煤岩对金属磨蚀性的指标,磨蚀系数试验台是一种用于测量矿石磨蚀系数的专用工程机械,可用于测量各种矿石的磨蚀系数。
使用比例控制技术和PLC可以实现对磨蚀系数试验台的自动控制,可有效地提高系统参数的控制精度,从而提高磨蚀系数的测量精度。
(1)磨蚀系数试验台工作原理
液压缸在液压力的作用下推动滑块往复运动,同时马达带动轮盘旋转,而重锤的重力使试棒始终与矿石接触摩擦,通过改变液压缸的往复速度、马达的旋转速度、重锤的质量,可以测出不同工况下试棒所走的路程和工作过程中试棒消耗的质量及其磨蚀的体积消耗,然后通过公式计算煤岩的磨蚀系数。磨蚀系数试验台原液压系统原理如图4-36所示。

图4-36 磨蚀系数试验台原液压系统原理图
1—柱塞泵;2、3—三位四通电磁换向阀;4—液压缸;5—叶片马达;6、7—单向节流阀;8、9—行程开关;10—单向阀;11—电机;12—粗过滤器;13—溢流阀;14、15—压力表和压力表开关
影响磨蚀系数精度的主要参数如下。
①往复缸的速度 是磨蚀过程中最重要的控制参数之一。在磨蚀过程中,要求液压缸换向平稳,并应有良好的速度稳定性。
②马达的旋转速度 马达旋转速度的稳定性,严重影响磨蚀系数的测量精度。在磨蚀过程中,马达的旋转速度容易受到负载变化的影响,从而影响磨蚀系数的测量精度。
③正压力 正压力是系统中重要的控制参数。正压力的稳定性直接影响磨蚀系数的测量精度。但是,由于原系统采用继电器-接触器控制系统,接线复杂,故障率高,调试和维护困难。速度受负载影响很大,且不能够自动调节。重锤提供的压力随系统运动的振荡产生振荡,很难保持恒定的力,容易使测量结果产生误差。
(2)电液比例控制系统
结合比例控制技术和PLC的优点,进行自动化改造。改造后的液压系统原理如图4-37所示。设备由3个比例控制回路进行控制,即往复缸速度电液比例控制回路(B)、马达速度电液比例控制回路(C)、恒压电液比例控制回路(A)。

图4-37 改造后的液压系统原理图
1、2—液压泵;3~6—过滤器;7、8—电机;9、10—溢流阀;11、12、17、34—单向阀;13~16、21、22—压力表及开关;18—先导式比例减压阀;19、27、32—放大器;20、31—三位四通电磁换向阀;23、29—液压缸;24—压力传感器;25—定差减压阀;26—比例方向阀;28—或门型梭阀;30、36—速度传感器;33—电液比例调速阀;35—背压阀;37—液压马达
①往复缸速度电液比例控制回路 见图4-37中B回路。该回路由定差减压阀25、比例方向阀26、放大器27、或门型梭阀、液压缸29、速度传感器30组成。应用电液比例方向阀和速度传感器构成的闭环控制系统,可以方便地为液压缸提供很好的速度控制。比例方向阀在控制液压缸运动速度的过程中,供油压力或负载压力的变化会造成阀压降的变化和对阀口流量的影响,使液压缸的运动速度偏离调定值,对磨蚀系数试验台正常工作产生不利影响。为了解决阀口受Δp(减压阀口正常工作时形成的压差)干扰的问题,尤其是要消除负载效应的影响,本系统选用二通进口压力补偿器,其目的就是保证Δp为近似定值,不随负载压力的波动而改变,从而保证通过比例阀的流量与输入的电信号成正比变化,实现了液压缸往复运动速度的精确控制。
②马达速度电液比例控制回路 见图4-37中C回路。该回路由三位四通换向阀31、放大器32、电液比例调速阀33、单向阀34、背压阀35、速度传感器36、液压马达37组成。用比例调速阀和速度传感器构成的闭环控制系统,能够很好地控制马达的旋转速度,使系统能够运行平稳。
电液比例调速阀用来调节马达的旋转速度,速度的大小由一个速度传感器测得,把测得的数据反馈到PLC中,由PLC输出一个控制信号来调节电液比例调速阀的开口度,从而调节马达的进油量,使马达的速度稳定在所要求的数值。在回油路上安装有背压阀,主要作用是产生回油路的背压,改善马达的振动和爬行,防止空气从回油路吸入。加背压后可以使回路液压阻尼比和液压固有频率增大,因此动态刚度得到提高,从而使运动平稳性提高。
③恒压电液比例控制回路 见图4-37中A回路。该回路由单向阀17、先导式比例减压阀18、放大器19、三位四通换向阀20、压力表及开关21与22、液压缸23、压力传感器24组成。采用比例控制的恒压系统提供恒定的正压力,并采用压力传感器测量系统的输出压力,能够很好地控制液压缸的输出压力,使系统压力能够稳定。比例减压阀是系统中的重要元件,控制比例减压阀的比例电磁铁是位移调节型电磁铁,并带有电感式位移传感器。由PLC来的电信号通过电磁铁直接驱动阀芯运动,阀芯的行程与电信号成比例;同时,电感式位移传感器检测出阀芯的实际位置,并反馈至PLC的AD模块进行转换。在PLC中,实际值与设定值进行比较,检测出两者的差值后,以相应的电信号输给电磁铁,对实际值进行修正,构成位置的反馈闭环。
根据磨蚀系数试验台回路的循环情况,写出该液压系统的电磁铁动作顺序,见表4-36。
表4-36 电磁铁动作顺序表

注:“+”表示电磁阀线圈通电。
4.5.2 盾构机刀盘驱动液压系统
盾构机是专用于地下隧道工程挖掘的技术密集型重大工程装备。盾构法以其施工安全可靠、机械化程度高、工作环境好、进度快等优点广泛用于隧道施工中,尤其是在地质条件复杂、地下水位高而隧道埋深较大时,只能依赖盾构。
盾构机刀盘驱动系统是盾构设备的关键部件之一,是进行掘进作业的主要工作装置。盾构的刀盘工作转速不高,但由于刀盘直径较大而且施工地质构造复杂,要求刀盘驱动系统具有功率大、输出转矩大、输出转速变化范围宽、抗冲击、刀盘双向旋转和脱困等功能,同时,在满足使用要求的条件下,具有减小装机功率、节能降耗等工作特点。刀盘驱动系统还必须具有高可靠性和良好的操作性。
为了适应复杂多变的地质条件,刀盘驱动系统可采用液压驱动、变频电动机驱动和双速电动机驱动3种形式。通常大直径隧道掘进机要求的转速高,宜选择电驱动(变频电动机驱动和双速电动机驱动),以获得良好的特性曲线。中、小直径的软土隧道掘进机通常要求速度较低,扭矩较大,宜选用液压驱动。
刀盘驱动液压系统采用变量泵-变量马达闭式容积调速回路,系统主泵采用两台用于闭式回路的斜盘式双向比例变量柱塞泵,主泵同时集成了补油泵、闭式回路控制回路和主泵变量控制回路。系统的马达采用一台轴向柱塞变量马达,变量液压马达通过变速箱与小齿轮驱动主轴承大齿轮,带动刀盘产生旋转切削运动。驱动装置可以实现双向旋转,转速在0~9.8r/min范围内无级可调,还可实现刀盘脱困功能。
(1)刀盘转速控制和旋转方向控制
主泵的变量形式为电液比例变量,如图4-38所示,泵的输出流量根据输入比例电磁阀电信号的大小实现无级可调,从而满足刀盘旋转速度的变化要求。电液比例控制的结构比较复杂,但可控性能好,可组成不同形式的反馈。刀盘驱动系统主泵的变量机构采用调节器设定泵的流量从而调节马达的转速,通过马达转速传感器反馈刀盘马达实际转速,如果与给定信号产生偏差,利用偏差信号改变泵的排量使刀盘马达转速与设定值相同。刀盘正向旋转时,比例电磁铁a通电,比例换向阀左位工作,液压泵正向输出油液,伺服缸右腔压力推动伺服缸活塞左移,活塞杆推动变量机构改变柱塞泵的斜盘倾角,改变泵的排量,从而改变液压泵的输出流量。当比例电磁铁a电流增加时,比例换向阀的阀芯与阀体开口增大,通过阀的压力降减小,伺服缸右腔压力增高,活塞继续左移,斜盘倾角增加,主泵输出流量增加。比例电磁铁a、b都不带电时,泵不输出流量,马达停止转动。为了克服盾构机在掘进过程中的滚转现象,保持盾构机的正确姿态,必须通过刀盘反向旋转来调整,马达反转时,使比例电磁铁b带电,液压泵反方向输出流量,并随着输入电流的增加而流量增大。因此,通过控制比例电磁铁a、b通电状态可以实现刀盘的双向旋转,控制比例电磁铁输入电流的大小,实现刀盘转速的调节。

图4-38 主泵工作原理图
1—主泵;2—二位三通换向阀;3、4—溢流阀;5—蓄能器
(2)刀盘的脱困和系统的安全控制
主泵变量机构还加入了二级压力切断装置,当主泵的任何一个出口压力超过设定值时,变量机构使泵的排量接近于零,输出的流量只补充泵的泄漏,实现泵的超压卸载,这种方式不存在溢流能量损失,系统效率高。卸载压力一级为28MPa,为系统正常工作时的安全压力,由溢流阀3设定;另一级为脱困时用,压力为35MPa,由溢流阀4设定。当二位三通换向阀2通电时,刀盘为脱困工况。所选择的主泵还集成有补油泵和闭式回路控制,通过集成使系统结构简单,减少了管路、降低了泄漏,便于维护和使用。补油泵有3个作用,即为闭式回路补油、强制冷却和控制主泵变量机构变量。补油泵首先用来补充液压泵、液压马达及管路等处的泄漏损失,并通过更换部分主油路油液来控制系统中油液的温度。系统中的补油压力为主泵的吸油口压力,补油泵的排量为76L/min。补油泵通过2个单向阀分别向系统中回油管路补油。刀盘驱动液压系统变量控制机构的控制油分别通过单向阀引自泵的2个油口和补油泵,使控制油始终接有压力和流量,当泵处于正、反向转换时,泵处于零排量工况,没有压力油输出,此时,控制油来自补油泵,补油泵控制油压力由顺序阀设定。此时,外控顺序阀由于主油路没有压力而关闭,此时利用补油泵的压力驱动变量机构,保证主泵换向。
系统中采用2个先导溢流阀实现缓冲,当马达制动时,由于惯性,会产生前冲,此时泵已停止供油,因此在马达排油管路会产生瞬时高压,使液压系统产生很大的冲击和振动,严重时造成损坏,因此在回路设置溢流阀可以使系统超压时,溢流阀打开,回油至马达进油管路,减缓管路中的液压冲击,实现马达制动。
系统选用2台主泵进行工作,正常掘进工作时,2台主泵同时工作,当有1台主泵出现故障时,系统还可以继续用单泵工作,保证盾构机工作的可靠性。
(3)刀盘的两级速度范围控制
盾构机掘进时要求满足在软、硬岩不同的地质工况下的掘进。在软土层中掘进时,由于地层自稳性能极差,要求刀盘转速低,应控制在1.5r/min左右,此时要求刀盘输出转矩大;硬岩挖掘时,刀盘转速高,而转矩小。为了满足上述要求,盾构机在软土掘进时需增大马达排量,降低马达转速;硬岩掘进时降低排量。系统可以实现软岩掘进时,转速范围0~2.96r/min,转矩1114kN·m;硬岩掘进时,转速0~9.87r/min,转矩334kN·m。
刀盘驱动液压系统的执行元件为用于闭式回路的斜轴式双向压力控制比例变量柱塞马达,马达变量为外控式,其工作原理如图4-39所示。马达的排量通过变量机构实现无级可调,通过系统中比例减压阀输入液控压力信号控制马达排量无级变化,马达的排量随着控制压力的增高而减小。

图4-39 马达工作原理图
(4)刀盘驱动液压系统的节能控制
刀盘驱动液压系统采用变量泵-变量马达容积调速回路,通过改变液压泵和液压马达的排量来调节执行元件的运动速度,系统的调速范围宽。该回路液压泵输出的流量与负载流量相适应,没有溢流损失和节流损失,回路效率高。刀盘驱动控制系统需要马达实现低速大转矩和高速小转矩,因此调节马达的排量极其有利。如果用变量泵和定量马达组成液压调速系统,在高速小转矩时,泵将运行在低压大流量场合;在低速大转矩时,泵将运行在高压小排量场合,因而泵及整个液压系统都需要按高压、大流量参数选择,系统效率不高。若采用变量马达,可以让马达在小排量工况下运行来满足高速小转矩要求;马达在大排量工况下运行来达到低速大转矩要求。这样,泵基本上处于高压下运行,充分发挥了泵的能力。这种系统中泵和系统本身的流量都比较小,系统成本降低,回路效率高。
4.5.3 阀控-变频液压电梯
液压电梯的装机功率一般是曳引电梯的2~3倍,节能成为液压电梯技术的热点。
液压电梯能量回收方式主要有回馈电网式、机械式、液压蓄能式、变频调速式和变频-蓄能式五种,其中变频-蓄能式节能效果最好。
阀控调速、变频(variable voltage variable frequency,VVVF)调速、活塞拉缸和蓄能器节能技术有机结合起来的开式油路的阀控-变频节能液压电梯系统,在一定程度上降低了液压电梯的能耗。
(1)系统组成及节能原理
图4-40是双缸直顶式液压电梯结构示意图,图4-41是该系统在双缸直顶式液压电梯中的应用原理图。该系统的能量回收原理是,在电梯下降过程中,一部分势能会转换成液压能,将压力能储存在蓄能器中;另一部分势能经过节流阀产生了节流能量损失,最终转化为热能。在电梯上升过程中。采用容积调速,减少节流能量损失,同时蓄能器中的压力油释放出来,补充给液压泵,使上升过程中液压泵消耗电动机的能量减少,达到节能目的。

图4-40 双缸直顶式液压电梯结构示意图

图4-41 开式阀控-变频液压电梯系统原理图
1—油箱;2—液压泵;3—主电动机;4—过滤器;5、18—单向阀;6—电磁溢流阀;7—二位三通换向阀;8、11、17—电液比例调速阀;9、10—桥式整流板;12、13—电磁单向阀;14—手动下降阀;15、16—活塞缸;19—溢流阀;20—蓄能器;21—截止阀;22—交替单向阀
(2)工作过程及特点
①工作过程 开式阀控-变频液压电梯(见图4-41)的工作过程如下。
电梯上行。微机控制器接到电梯上行指令后,电磁溢流阀6得电,主电动机3旋转,泵启动,泵经过滤器和交替单向阀22从油箱吸油,再经过过滤器4、单向阀5、二位三通换向阀7、桥式整流板9和10(控制双缸同步)、电磁单向阀12和13进入到活塞缸15和16,轿厢上升。在电梯上升的过程中,通过检测到的电梯位置信息向微机控制器输入,然后经过微机处理后,把信号反馈给变频器,使液压泵按照给定的速度指令正向转动,电梯轿厢按照预定的速度曲线完成加速-减速-匀速-减速,再到平层运行阶段。当电梯到达选定楼层,微机控制器接到停止信号后电磁溢流阀6断电,同时变频器停止向电动机供电,液压泵2停转,单向阀5、12、13在两端压差作用下关闭,电梯轿厢停留在平层位置。在上行过程中,如果蓄能器内的压力油提供的驱动力矩大于负载阻力矩与系统摩擦力矩之和,主电动机需工作在正向回馈制动状态。反之,则主电动机需工作在正向电磁驱动状态。
电梯下行。微机控制器接到电梯下行指令后,电磁溢流阀6、二位三通换向阀7、电磁单向阀12和13得电,液压缸下腔的油液经过电磁单向阀12和13、桥式整流板9和10、换向阀7、电液比例调速阀17、单向阀18、交替单向阀22,最后到达蓄能器20,轿厢下降。双缸联动的手动下降阀14(应急阀)用于突然断电液压系统因故障无法运行时,通过手动操作使液压电梯以较低的速度下降。电梯轿厢在下降时,将检测到的液压电梯位置信号输入到微机处理器,然后将速度调节指令反馈到电液比例调速阀17,通过调节阀口的开度来控制电梯按照规定的速度曲线运行。当电梯到达指定层后,微机控制器接收到信号,使电磁单向阀12和13断电,两缸处于自锁状态,电梯停留在平层位置。
各电磁铁的通断情况见表4-37。
表4-37 电磁铁动作表

②特点 开式阀控-变频液压电梯的特点如下。
a.系统采用了变频调速、阀控调速和蓄能器作液压配重技术来节能。
b.电梯上行采用变频调速技术实现了系统的变转速容积调速,使之成为“功率传感”系统。
c.电梯下行采用阀控调速技术减少系统额外功率输入,并将负载部分势能以压力能的形式存储在蓄能器中,降低了系统装机功率。
4.5.4 组合机床液压系统爬行的处理
爬行是液压系统速度失控的一种形式。
(1)故障现象
130B型组合机床工作原理如图4-42所示,机床进给动力滑台由单活塞缸带动,其工作循环为快进→工进→快退→原位停止,执行元件(单活塞杆液压缸)快速运动时工作正常,转为工进时即开始出现爬行现象。油箱油液状况正常,液压缸工作压力无明显变化,排气后故障未消除。

图4-42 130B型组合机床工作原理图
(2)故障维修过程
①油液中混有空气导致爬行故障的处理 液压系统混入空气时可从以下两种情况进行考虑。
a.液压泵连续进气。
故障现象:压力表显示值较低,液压缸工作无力,油面有气泡,甚至出现油液发白和液压泵“尖叫”的现象。
故障原因:液压泵吸油侧油管接头螺母松动而吸气;密封元件损坏或密封不可靠而进气;油箱内油液不足,油面过低,吸油管在吸油时因液面波浪状导致吸油管端间断性露出液面而吸入空气;吸油过滤器堵塞使吸油管局部形成气穴现象等。
故障排除:较大进气部位通过直接观察较易找到;微小渗漏部位须经检查方能查出,可将液压泵吸油侧和吸油管段部分清洗干净后,涂上一层稀润滑脂,重新启动液压泵,涂有润滑脂的各部位没有被吸而成皱褶状或开裂,则表明没有封闭不严的部位,反之则表明形成皱褶状或开裂处为进气部位;找到进气部位时根据具体情况或拧紧管接头或更换密封圈等易损件;若油面过低应及时加油,若噪声过大则应检查并清洗滤油器。
b.液压系统内存有空气。
故障现象:压力表显示值正常或稍偏低,液压缸两端爬行,并伴有振动及强烈的噪声,油箱内无气泡或气泡较少。
故障原因:这种故障的原因主要有3种,一是液压系统装配过程中存有空气;二是系统个别区域形成局部真空;三是液压系统高压区有密封不可靠或外泄漏处,工作时表现为漏油,不工作时则进入空气。
故障排除:第一种情况往往发生在新设备上,通过排气后可消除爬行;第二种情况新老设备上均可能出现,或为新设备的设计、装配不合理导致某一区域内油液阻力过大,压降过大,或为老设备的杂质堆积,由于流经狭窄缝隙而产生较大的压降,尤其在流量阀中节流孔处易出现这种情况,通过清洗相关元件可消除故障;第三种情况通过直接观察有无漏油情况来判断。
②滑动副摩擦阻力不均导致爬行故障的处理 这种故障包括以下几种情况。
a.导轨面润滑条件不良导致爬行故障。
故障现象:压力表显示值正常,用手触摸执行元件有轻微摆振且节奏感较强。
故障原因:执行元件低速运动时润滑油油楔作用减弱,油膜厚度减小,这时润滑油如选择不当或因油温变化导致润滑性能差、润滑油稳定器工作性能差或压力与流量调整不当、润滑系统油路堵塞等均可使油膜破裂程度加剧;导轨面刮点不合要求、过多或过少等都会造成油膜破裂形成局部或大部分的半干摩擦或干摩擦,从而导致爬行,而后一种情况主要发生在新设备上。
故障排除:机床若属润滑条件不良,应为由于温度变化而改变了润滑油的性能、润滑油路压力与流量调整不当、润滑油路的堵塞等因素。主要排除措施:用手搓捻润滑油检查滑感,观察油槽内润滑油流速,检查润滑系统压力、流量情况,检查润滑油稳定器工作情况等;如发现问题则或更换润滑油,或调整其压力或流量,或清洗润滑孔道系统,从而恢复润滑性能,直至执行元件运动平稳。
b.机械憋劲。
故障现象:压力表显示值较高或稍高,爬行部位及规律性较强,甚至伴有抖动现象。
故障原因:运动部件几何精度发生变化、装配精度低均会导致摩擦阻力不均,容易引起液压缸爬行,例如液压缸活塞杆弯曲、液压缸与导轨不平行、导轨或滑块的压紧块(条)夹得太紧、活塞杆两端螺母旋得太紧、密封件过盈量过大、活塞杆与活塞不同轴、液压缸内壁或活塞表面拉伤,这些情况都是引起这类故障的原因,有的表现为液压缸两端爬行逐渐加剧,如活塞杆与活塞不同轴;有的表现为局部压力升高,爬行部位明显,如液压缸内壁或活塞表面拉伤等。
故障排除:对损坏部位进行修复处理并正确安装调整有关元件。
4.5.5 调速阀使用应注意的问题
(1)启动时的冲击
对于图4-43(a)所示的系统,当调速阀的出口堵住时,其节流阀两端压力p2=p3,减压阀芯在弹簧力的作用下移至最左端,阀开口最大。因此,当将调速阀出口迅速打开,其出油口与油路接通的瞬时,p3压力突然减小,而减压阀口来不及关小,不起控制压差的作用,这样会使通过调速阀的瞬时流量增加,使液压缸产生前冲现象。为此有的调速阀在减压阀上装有能调节减压阀芯行程的限位器,以限制和减小这种启动时的冲击。也可通过改变油路来克服这一现象,如图4-43(b)所示。

图4-43 调速系统
图4-43(a)所示节流调速回路中,当电磁铁1DT通电,调速阀4工作时,调速阀5出口被二位三通换向阀6堵住。若电磁铁3DT也通电,改由调速阀5工作时,就会使液压缸产生前冲现象。如果将二位三通换向阀换用二位五通换向阀,并按图4-43(b)所示接法连接,使一个调速阀工作时另一个调速阀仍有油液流过,那么它的阀口前后保持了一较大的压差,其内部减压阀开口较小,当换向阀换位使其接入油路工作时,其出口压力也不会突然减小,因而可克服工作部件的前冲现象,使速度换接平稳,但这种油路有一定的能量损失。
(2)最小稳定压差
节流阀、调速阀的流量特性如图4-44所示。由图可见,当调速阀前后压差大于最小值Δpmin以后,其流量稳定不变(特性曲线为一水平直线)。当其压差小于Δpmin时,由于减压阀未起作用,故其特性曲线与节流阀特性曲线重合,此时的调速阀相当于节流阀。所以在设计液压系统时,分配给调速阀的压差应略大于Δpmin,以使调速阀工作在水平直线段。调速阀的最小压差约为1MPa(中低压阀为0.5MPa)。

图4-44 节流阀、调速阀的流量特性
(3)方向性
调速阀(不带单向阀)通常不能反向使用,否则,定差减压阀将不起压力补偿器作用。在使用减压阀在前的调速阀时,必须让油液先流经其中的定差减压阀,再通过节流阀。若逆向使用,如图4-45所示,则由于节流阀进口油压p3大于出口油压p2,那么p2A1+p2A2<p3A+Fs,即定差减压阀阀芯所受向右的推力永远小于向左的推力,定差减压阀阀芯始终处于最左端,阀口全开,定差减压阀不工作,此时调速阀也相当于节流阀使用了。

图4-45 调速阀逆向使用的情形
特别提醒:调速阀如果装反便失去稳定压差功能,液压缸运动速度会受负载变化影响,不能平稳。
(4)流量的稳定性
在接近最小稳定流量下工作时,建议在系统中调速阀的进口侧设置管路过滤器,以免阀阻塞而影响流量的稳定性。流量调整好后,应锁定位置,以免改变调好的流量。
特别提醒:压力阀、流量阀调整好后,都应锁定位置避免漂移。