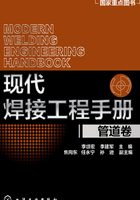
第3章 长输管道施工焊接管理
长输管道通常是指较长距离和较大管径输送油、气等介质的管道。长输管道输送距离长、焊缝多,任何一处焊缝存在质量问题,都会对管道的正常输送和安全运行产生很大的影响。西气东输一线管道工程主干线管径ф1016mm,长度4000km,满负荷运行管道内可储存天然气3×108m3。环焊缝(不包括钢管的螺旋缝或纵缝)约340000条,环缝总长度1085km,焊道总长度7600km。2000余名焊工参加西气东输一线管道工程的焊接,这2000余名焊工虽都取得西气东输管道工程焊工资格证书,但他们的技术水平、综合素质和责任心,肯定存在着较大的差异。如何使每一位焊工焊接的每一寸焊道均为合格焊道,这就需要科学的、严格的、细致的管理。
3.1 焊工管理
焊接工艺评定后,工程开工前,应组织焊工进行培训和考试。这里所说的焊工培训,是对具有一定技术水平的焊工进行的适用于某工程的专项性强化培训,培训时间一般不超过一个月。通常分为持证焊工的培训和无证焊工的培训。
3.1.1 焊工培训
(1)持证焊工的培训 持证焊工的培训,是指该焊工已持有该工程相应的合格项目,且在有效期内。这类焊工只需对其进行适用性培训,确保工程开工初期的焊接质量。培训时间一般为1~2周。
(2)无证焊工的培训 无证焊工的培训,该类焊工没有焊工资格证或焊工资格证上的项目不能满足本工程的需要,或该合格项目过期。这类焊工需经严格的培训,培训结束时应对其进行考试,考取与本工程相适用的焊工资格证后,方可从事本工程的焊接。
(3)工程焊接技术(要求)培训 工程开工前对焊工培训的另外一项重要内容是要求焊工掌握本工程的焊接技术要求、焊接的特殊性及强调哪些是应特别注意的问题。
(4)培训措施和方法 由于是工程开工前的适用性培训,培训的针对性一定要强。应采用与工程相同的焊接方法、焊接设备、钢管材质及规格、坡口形式和尺寸、焊接材料的型号和规格、预热要求、层间温度、焊接层数与道数、焊接工艺参数等。
由于长输管道的焊接基本上是采用流水作业,即不同的焊道是由不同的焊工焊接的。在培训过程中,要根据焊工的技术特点,安排好焊工的焊道次序。培训结束前要模拟工程现场的流水作业进行焊接,使每个焊接作业机组各焊道的焊工达到良好的配合状态。
3.1.2 焊工考试方法
长输管道焊工考试,一般考试管环缝水平固定(5G)焊口就可满足工程的要求;当在山区等地段施工存在20°以上的坡度时,应考试管45°固定(6G)焊口。
(1)由一名焊工完成一个完整的环焊缝 当管径小于ф500mm时,一名焊工应焊接一道完整的环焊缝。
(2)由两名焊工完成一个完整的环焊缝 当管径大于等于ф500mm时,可由一名焊工焊接一道完整的环焊缝;也可以两名焊工焊接一道完整的环焊缝,但每名焊工应完成从12点到6点180°范围内的所有焊道。
(3)多名焊工完成一个完整的环焊缝 当多名焊工焊接一道考试焊口时,通常是由1~2名焊工焊接根焊焊道,多名焊工(由填充焊道的数量确定填充焊道的焊工数量)焊接填充焊道,1~2名焊工焊接盖面焊道。根焊焊道的焊工考试合格后,可焊接根焊焊道和填充焊道;填充焊道的焊工考试合格后只能焊接填充焊道;盖面焊道的焊工考试合格后,可焊接填充焊道和盖面焊道。
3.1.3 焊工资格证管理
焊工证上合格项目的有效期为4年,满4年必须重新考试或办理免试。免试条件:第二次及以后的有效期满,焊工档案内容齐全、真实,焊接业绩优秀的焊工。
焊工中断受监察设备的焊接工作六个月以上,再从事受监察设备的焊接时,必须重新考试。
有下列情况之一的焊工应暂扣或吊销其焊工资格证。
①焊接操作技能不能满足工程的焊接质量要求。
②违反工艺纪律。
③发生重大质量事故。
④焊接一次合格率太低。
被吊销焊工资格证的焊工,必须经过严格的培训后,方可重新考试。
3.1.4 焊工档案管理
从事长输管道施焊的焊工均应建立焊工档案,焊工档案应包括下列内容。
①焊工基本情况:姓名、性别、年龄、文化程度、从事焊接时间、掌握的主要焊接方法、主要工作经历、主要焊接经历等。
②培训情况:培训班名称、培训内容、培训时间、培训地点等。
③考试情况
a.基础理论知识:试卷、考试时间、考试成绩等。
b.操作技能:考试时间、考试项目、合格项目。
④工作业绩:主要工程的焊绩记录,工程名称、施焊时间、施焊地点、施焊位置、焊口数量、焊接方法、焊接材料、焊接设备、对应合格证项目、无损检测方法、焊接一次合格率、二次以上返修情况、遵守工艺记录情况和质量事故情况等。
3.2 材料及设备管理
3.2.1 钢管管理
(1)钢管的验收 用于长输管道工程的钢管必须有质量证明书,质量证明书的项目齐全并符合标准和设计要求。钢管验收的项目应包括下列内容:质量证明书、钢号、钢管的外表质量、端部直径、端部圆度、管口与管轴线的垂直度、管壁厚度和坡口质量等。
(2)钢管的装卸和运输 钢管在装卸和运输过程中应注意保护坡口和防腐层。
(3)钢管的堆放和保管 钢管应堆放在管墩上,堆放场地雨后不应有积水。钢管的堆放高度一般不应超过3m。
3.2.2 焊接材料管理
焊接材料应设专人验收、保管、烘干和发放,并建立台账和认真做好各项记录。管道施工常用的焊接材料有:焊条、焊丝、焊剂、保护气体、切割用气体。
(1)焊接材料的验收 焊接材料必须有质量证明书,质量证明书的项目齐全并符合标准和设计要求。焊接材料验收的项目应包括下列内容:质量证明书、包装质量、外表质量、型号、规格、批号、生产日期等。对焊材质量有疑义的应进行复验。
(2)焊接材料的保管 焊条、焊丝、焊剂应存放在专用的焊材库内的货架上,焊材距地面和墙壁的距离不得小于300mm。焊材库内应保持干燥,相对湿度不应大于60%。在湿度较大的地区或季节,焊材库内应设除湿机,以保持相对湿度在60%以下。
焊接材料应按类别、型号、规格、生产厂家、生产日期、批号等分别存放,并有明确的标识。
(3)焊接材料的烘干 严格按焊材说明书的要求进行烘干,不同类别、不同型号的焊材应分别烘干。不得将焊条直接放入高温的烘箱,也不得将烘烤到高温的焊条从烘干箱内取出。当烘箱的温度自然降到200℃以下时,方可将烘箱内的焊条取出放入恒温箱内,随用随取。
纤维素焊条在包装良好的情况下,一般不需烘烤;当焊条的包装破损或受潮较严重时,才需要烘烤,但烘烤温度不应超过100℃。
(4)焊接材料的发放 同型号、同规格的焊材按生产日期的先后发放,先生产的先发放,后生产的后发放。
焊工应持焊材领用卡领用焊材。一次领出的焊材必须限量,不需烘干的焊材,限领数量为当天的用量;需要烘干的焊材的限领数量为4h的用量。经烘干的焊材,领出后必须放在焊材保温筒内随用随取。
(5)焊接材料的回收 当天或在规定时间内没有用完的焊材应及时回收,使用时应重新烘烤(不需烘烤的焊条除外),但重复烘烤次数不应超过2次。经2次重复烘烤仍没用完的焊材不得用于承压元件的焊接。
3.2.3 设备管理
焊接用设备应处于良好的工作状态,仪器、仪表等附件齐全、准确,且在定检期内。设备应有专职人员管理,定期进行保养和维修。
严格按照设备的操作规程进行操作,认真做好运转、保养和维修记录。
3.3 焊接过程控制
3.3.1 焊前技术要求
(1)技术交底 施焊前由焊接技术人员向焊工进行技术交底。
(2)监督内容 设专职质量管理员监督施焊的全过程,监督的主要内容有:钢管质量、坡口质量、清理情况、监测环境温度和湿度及风速、焊工资格、预热、后热、焊接设备、焊接材料、焊接工艺参数、层间清理、层间温度、焊接顺序、表面清理、焊缝标记等。
(3)坡口加工 当采用管道全位置自动焊时,要求坡口现场加工;其他焊接方法所用坡口可由管厂加工也可以现场加工。当现场加工坡口时,要求采用专用的坡口机加工。坡口加工后应采用专用的坡口测量工具,测量坡口的加工质量。每一道坡口至少测量4个点,且4个点应均布于整个圆周上,每一个点的所有尺寸均应满足要求。如发现有超差现象,应及时调整刀具或更换刀具,确保坡口尺寸的正确性和一致性。
(4)坡口质量及组装质量 坡口表面质量、坡口形式、坡口尺寸、组装间隙、错边尺寸等。
(5)坡口及两侧的清理情况 坡口及两侧易采用电动钢丝刷、手工钢丝刷和砂纸进行清理;当采用砂轮机进行清理时,应特别注意防止将坡口及钢管的内外表面损伤。
当天清理的坡口应当天焊接。清理后,坡口及坡口的内外两侧20mm范围内应见金属光泽,坡口的内外两侧100mm范围内应无污物。
3.3.2 环境监测
应设专人对焊接环境实施监测,监测点应距施焊点1m左右;当采用防风防雨篷时,应在篷内距焊接点约0.5m处测量。当天气变化不大时,一天内测量3次(施焊前、施焊过程中、施焊结束时);当天气变化较大时,应在天气变化时随时增加测量次数;测量内容包括温度、湿度和风速,每次测量后均应做好记录。
对焊接环境的要求,应根据标准、规范和工艺评定来确定。
(1)一般要求 雨、雪、雾等天气无有效的防护措施,不得施焊。
(2)对环境温度的要求 对环境温度的要求,标准中一般无明确的规定。低碳钢和较低强度的低合金钢通常对焊接环境温度无规定;高强钢一般规定施焊环境温度不低于0℃。当在特别寒冷的地区施工时,应在焊接试验和焊接工艺评定时模拟施工现场温度进行焊接试验,以确定施焊温度和施焊措施。
(3)对环境湿度的要求 标准对环境湿度的一般规定为环境的相对湿度不应大于90%,当环境湿度大于90%时应停止焊接。如果管道施工所用的焊接方法和焊接材料对空气的湿度比较敏感,通过焊接试验应限定更低的环境湿度;如果在湿度较大的地区,又必须在湿度较大的季节施工。自然环境湿度时常超过90%,应采用封闭性能较好的防护篷,采取有效的除湿措施,使防护篷内的湿度控制在90%以内。
(4)对风速的要求 当风速超过如下规定时,无有效防护措施不得施焊。
①纤维素焊条、自保护药芯焊丝焊接时,风速≤10m/s。
②除纤维素焊条外的其他焊条电弧焊焊接时,风速≤8m/s。
③气体保护焊时,风速≤2m/s。
3.3.3 预热、后热和焊后保温缓冷
预热、后热和焊后保温与钢管材质、管壁厚度、焊接方法、环境温度和焊后的使用条件等因素有关。
(1)预热
①预热温度 应按焊接工艺规程要求的预热温度加热,预热时的加热温度要比预热规定的最低温度高10~30℃,以保证焊接开始时的预热温度。但也不是预热温度越高越好,预热温度过高除消耗能源多,预热时间长影响焊接效率外,还会导致管材的性能发生变化和影响钢管防腐层的质量。
当施焊的环境温度过低,钢管的壁厚又较大时,在保证钢管性能和防腐层性能的情况下,可适当提高预热温度,但不宜超过预热上限温度50℃。
②预热宽度 管端的预热宽度为3倍的管壁厚度,且不小于100mm。预热宽度过窄,会造成管端轴向的温度梯度过大,降温速度过快。预热宽度过大会影响防腐层的性能。
③升温速度 加热时的升温速度不应过快,过快会造成管壁厚度方向的温度梯度过大,加热面的温度过高。管壁厚度在10mm以下的钢管,加热速度应控制在50℃/min以下;管壁厚度超过10mm时,加热速度应控制在50℃/(min·cm)以下。
④预热温差 在整个圆周上预热温度应力求一致,最大温差不应超过预热温度的15%。
⑤温度的测量 采用表面温度仪测量预热温度,各测温点应均布在整个圆周上。管径小于等于ф200mm时,测温点应不少于2个;管径在ф200~1000mm之间时,测温点应不少于4个;管径大于ф1000mm时,测温点应不少于6个。
(2)后热 对于长输管道,在通常的情况下不要求进行后热,只有当焊接环境温度较低、管壁厚度较大、焊接应力较高、钢管材质又具有较强的冷裂倾向时,才要求进行后热。后热的温度和后热时间由焊接工艺评定确定。一般后热温度应为200~300℃,后热时间0.5~1h,并进行保温缓冷。
(3)焊后保温缓冷 钢管材质具有较强的冷裂倾向特别是具有较强的延迟裂纹倾向时,在焊接环境温度又较低的情况下,应进行焊后保温缓冷。通常采用保温被进行保温,焊接结束时,立即盖好保温被,并应将管道的两端封好。焊缝的温度降到环境温度时,才可将保温被去掉,然后再进行表面清理和外观检查。
3.3.4 施焊工艺参数
一道环焊缝有时要采用两种或两种以上的焊接方法,两种或两种以上的焊材型号和焊材规格。保证每一层焊道焊接方法和焊接材料的正确,是保证工艺正确性的基础。
所有工艺参数(电源极性、焊接电流、电弧电压、焊接速度、送丝速度、气体种类、气体比例、气体流量、焊枪摆动幅度、焊枪摆动速度或频率、焊枪两侧停留时间等)必须在工艺规程限定的范围内,并且各参数间应有良好的配合。
3.3.5 层间清理及层间温度
(1)层间清理 每一层焊道焊完后,必须对其进行清理。焊条电弧焊应采用钢丝刷和砂轮机进行清理;非焊条电弧焊采用钢丝刷清理熔渣或氧化渣,砂轮机打磨焊道接头。采用砂轮机进行层间清理时,应注意不要损伤坡口和管表面。层间的熔渣和氧化渣必须清理干净,焊道接头应磨平。
(2)层间温度 采用下向焊或焊道厚度较薄的其他焊接方法,根焊道焊接完成后,要求尽快焊接后续焊道。根焊道完成后到后续焊道焊接前的间隔时间,一般规定不应超过10min。钢材的强度等级越高、管壁越厚、施焊环境温度越低,此间隔时间应严格控制。
当有预热要求时,层间温度不应低于预热温度的低限值。若管径较小、管壁厚度较大时,还应注意控制层间温度的高限值。
(3)焊接顺序 直径小于等于ф300mm的管环焊缝,同一焊层可由一名焊工焊接。每一层焊道焊接完成后,方可焊接后续焊道。
直径大于ф300~1000mm的管环焊缝,应由两名焊工同时对称焊接同一焊道。采用下向焊时,一名焊工从12点开始焊接,另一名焊工同时从3(或9)点开始焊接;当采用上向焊时,一名焊工从6点开始焊接,另一名焊工从3(或9)点开始焊接;两名焊工的焊接速度和焊接效率应基本一致。
直径大于等于ф800mm的管环焊缝,可由三名或四名焊工同时对称焊接同一焊道。各焊工应尽量均布在整个焊口上对称焊接。几名焊工的焊接速度和焊接效率应基本一致。
(4)表面清理及外观自检 焊缝焊接完成后,必须将焊缝及两侧的熔渣和飞溅清理干净。通常用钢丝刷进行清理熔渣和飞溅,当焊道接头处较高应采用砂轮机将其磨成与其他部位的焊道和母材圆滑过渡;如果飞溅较严重用钢丝刷无法去除时,可采用锉刀、扁铲、砂轮机等工具,但必须特别注意不应将管表面损伤。
表面清理完成后,焊工应对焊缝进行自检,如果存在非裂纹、非未熔合的表面缺陷,应对其进行修补;如果存在裂纹和未熔合等缺陷,必须制定返修工艺后,方可返修。
3.4 焊缝检查
3.4.1 外观检查
(1)焊缝表面及两侧的清理状况 焊缝表面的熔渣、氧化物,焊缝两侧的飞溅等必须清理干净。
(2)焊缝形状 焊缝应与母材圆滑过渡,整个焊道的宽度和余高应基本一致。
(3)焊缝尺寸 焊缝余高、焊缝余高差、焊缝宽度、焊缝宽度差均应在标准和设计规定的范围内。
(4)表面缺陷
①不允许存在的缺陷 焊缝表面不得有裂纹、未熔合、夹渣、气孔和焊瘤。
②其他缺陷 咬边、管表面的电弧擦伤、管表面的机械损伤及飞溅等的尺寸、数量及分布均应符合标准和设计规定。
(5)检查方法 对焊缝表面及焊缝两侧的管表面必须全面地进行仔细检查。测量焊缝余高时应测量最高处和最低处,当焊缝的余高基本一致时,应分别测量3点、6点、9点和12点的余高;测量焊缝宽度时应测量最宽处和最窄处,当焊缝的宽度基本一致时,同样应分别测量3点、6点、9点和12点的焊缝宽度。
焊接缺陷的检查方法:对焊接缺陷应全面检查,必须测量最大尺寸点。
(6)外观检查记录及检查报告
①焊缝尺寸记录点应不少于4点,对焊接缺陷应进行全面记录。
②外观检查后应签发外观检查报告,报告中至少应包括下列内容:对于合格焊缝报告中应注明焊缝编号、检查标准、“合格”字样和检验员签字;对于不合格焊缝报告中应注明焊缝编号、检查标准、缺陷性质、缺陷位置、缺陷尺寸、“不合格”字样和检验员签字。
3.4.2 无损检测
经外观检查合格的焊缝方可进行无损检测。无损检测后必须签发无损检测报告,无损检测报告应包括下列内容:焊缝编号、检测方法、检测标准、缺陷性质、缺陷位置、缺陷尺寸、质量等级和检测人员签字等。
对于不合格的焊缝应及时发出焊缝返修通知单。
3.4.3 焊缝标志
长输管道的所有环焊缝均应有焊缝标志,焊缝标志应包括下列要求。
①在整个一项管道工程中用统一的编号方式,且不应有相同焊缝编号。
②通常采用记号笔或喷印的方法进行标志,标志应位于介质流动方向下游1m处。
③当钢材的屈服强度值σs≤300MPa时,可采用打钢印的方法进行标志,标志应位于介质流动方向下游100mm处。
④焊缝标志的内容:施工标段编号、施工单位代号、作业机组编号、焊工编号(非流水作业时有此项,流水作业时无此项)。
⑤字迹应清楚正规。
3.5 焊缝的修补及返修
①焊工自检发现的非裂纹、非未熔合缺陷,且缺陷的深度小于等于1/3管壁厚度并不大于3mm,焊缝的表面温度又不低于规定的最低层间温度时,焊工可直接修补。
②焊缝存在下列情况之一,必须进行返修。
a.经外观检查发现的裂纹、未熔合缺陷。
b.经外观检查发现的非裂纹、非未熔合缺陷,但缺陷深度超过管壁厚度的1/3或深度大于3mm的缺陷。
c.焊接完成后,焊缝的表面温度低于规定的最低层间温度时的所有超标缺陷。
d.经无损检测发现的超标缺陷。
e.经强度试验或气密性试验发现的缺陷。
③焊缝的返修必须制定具有针对性的返修工艺,返修工艺应包括下列内容。
a.焊接方法、焊接设备。
b.焊接材料名称、型号、规格等。
c.焊工资格。
d.缺陷性质、尺寸及在焊缝中的位置。
e.缺陷的清除方法及缺陷清除后的检验方法。
f.预热方法及预热温度,后热方法及后热温度。
g.焊接工艺参数。
h.层间清理及层间温度。
i.焊后清理、外观检查及无损检测要求。
④焊缝的返修应由具有返修资格的焊工焊接,并应在质量员或监理的监督下进行。
⑤返修完成后应重新进行外观检查和无损检测。
3.6 焊接资料的归档
焊接是长输管道施工重要的环节之一,焊接的各个环节应具有可追溯性,所以应加强焊接资料的归档管理。焊接归档资料应包括下列内容。
①焊接工艺评定报告。
②焊接材料质量证明书。
③焊工资格表。
④焊接工艺规程。
⑤施焊记录。
⑥外观检查记录(报告)。
⑦无损检测报告。
⑧返修记录。
⑨焊缝力学性能检验报告。