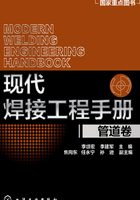
第5章 弯头
5.1 概述
弯头(elbows)是流体输送管道中不可或缺的重要组成部件,主要用于安装空间位置受限制,管线密集度大的管道输送站场、油气田集输站场、炼化、化工、船舶及发电装置等管线集中场合,用于改变流体的流动方向及管线的走向。
弯头与弯管的主要区别如下。
①弯头是标准件,弯头的曲率半径分为1DN、1.5DN、3DN,角度分为:30°、45°、90°、180°四个标准值;弯管是非标准件,其曲率半径一般≥3DN,弯曲角度为0°~180°区间任意值。
②弯头两端一般没有直管段,弯管至少一端应有直管段才能加工。
③两者的制造工艺不尽相同。有时人们对弯管和弯头不加以区分,统称为弯头。
常用弯头成形方法见表1-5-1。
表1-5-1 常用弯头成形方法

弯头采用的原材料包括金属管和金属板。弯头按加工方式分为:推挤弯头(分为热推挤、冷推挤)、压制弯头(分为钢管压制弯头、钢板压制焊接弯头);按曲率半径分为:短半径弯头(1DN)、长半径弯头(1.5DN)和3DN半径弯头;按焊缝有无分为:无缝弯头和焊接弯头;按弯曲角度分为30°、45°、90°和180°弯头以及等径弯头和异径弯头。一般情况下,应优先采用长半径弯头,而短半径弯头多用于安装位置空间尺寸受限制的场合。当选用短半径弯头时,其最高工作压力不宜超过同规格长半径弯头的0.8。有时为了缓和流体在变向处的冲刷、摩擦和动能,就会采用R=3DN的弯头。
弯头的基本尺寸应符合GB/T 12459《钢制对焊无缝管件》、GB/T 13401《钢板制对焊管件》、SY/T 0609《优质钢制对焊管件规范》、SY/T 0510《钢制对焊管件规范》的要求;结构强度及其他尺寸计算应遵循GB 50251《输气管道工程设计规范》、GB 50253《输油管道工程设计规范》、ASMEB31.8《输气和配气管道系统》等设计规范。
5.2 推挤弯头
推挤弯头是借助普通压力机、液压机或弯头推制机,并利用专用模具装置对管材进行挤扩或挤弯的工艺方法,分为热推挤弯头和冷挤压弯头。
5.2.1 热推挤弯头
热推挤弯头的工作原理如图1-5-1所示,就是在专用的弯头推制机上,把一段段金属管坯套在专用的芯棒上,在外力作用下推动金属管坯沿芯棒向前移动,在芯棒开始变形区域对金属管进行加热,使金属管坯按芯棒的形状扩变成需要的弯头。由于管坯受推力和芯棒阻力的共同作用,使管坯产生周向扩张和轴向弯曲变形,从而使小直径的管坯推扩成较大直径的弯头。

图1-5-1 热推挤弯头工作原理
由于管坯内侧比外侧加热温度高,在推挤过程中内侧金属向两侧流动,使金属得到重新分布,因此只要选择合适的管坯,就能够推挤出管壁厚度与原管坯壁厚大致相等且壁厚均匀一致的弯头。
采用芯棒热推挤工艺推挤弯头时,弯头弯曲角度应小于或等于180°。
管坯除了采用火焰加热外,还可以采用特制的中频感应加热圈进行加热(见图1-5-2),加热温度:碳钢为750~850℃,不锈钢约为900℃。理想的加热温度应该是出口端温度较高,始扩段温度较低,中间逐渐过渡。

图1-5-2 热推挤弯头
管坯尺寸的确定和推挤力的计算见表1-5-2。
表1-5-2 芯棒热推挤弯头工艺参数的确定

在热推挤弯头时,为了降低单位热挤压力、减小管坯与芯棒之间的摩擦、延长芯棒的使用寿命、提高弯头内表面质量,应对管坯内表面进行润滑处理。润滑处理方法为:用40#~50#机油混合石墨粉搅拌均匀,然后均匀涂抹在管坯的内表面上,能保证热推挤过程中有良好的润滑作用。
芯棒是热推挤弯头装置中最关键的零件,按其结构形式分为单半径芯棒和双半径芯棒两种,单半径芯棒形状简单,加工方便,使用较为广泛;双半径芯棒变形阻力小,推挤容易,有利于金属的重新分配,因其形状复杂,不易加工制造,故生产中使用较少。但考虑到为使芯棒更有利于金属材料的流动,一般根据生产实际对单半径芯棒进行试验修正后使用。在生产中,由于受温度、材料、环境等的影响,要根据实际生产的前几个弯头的检测尺寸对芯棒进行修磨,以提高产品的一次合格率。芯棒的结构形式及尺寸见表1-5-3。
表1-5-3 芯棒的结构形式及尺寸

注:D—弯头外径;t—弯头壁厚;D0—管料外径;t0—管料壁厚;ρ—弯头中心层弯曲半径;d—芯棒出口端直径(即弯头内径);d0—芯棒起始端直径(即管料内径);L1—芯棒直段长度;R0—单半径芯棒中心层弯曲半径(或双半径芯棒后弯曲段中心层弯曲半径);—双半径芯棒前弯曲段中心层弯曲半径;R1—双半径芯棒后弯曲段内侧半径;R2—双半径芯棒后弯曲段外侧半径;
—双半径芯棒前弯曲段内侧半径;
—双半径芯棒前弯曲段外侧半径;c—双半径芯棒两半径圆心距。
芯棒在热推挤过程中要求高温、耐磨损,因此要选用适合的芯棒材料。对于碳钢弯头,当管坯内径大于65mm时,通常采用2Gr13材料制造芯棒;当管坯内径小于65mm时,则采用Cr25Ni20Si2材料制造芯棒;对于不锈钢和耐热钢弯头,无论管内径多大,皆采用Cr25Ni20Si2材料制造芯棒。
由于不同直径、不同壁厚、不同曲率半径的弯头需要的芯棒不同,而且热推挤后的弯头大都需要采用专用的整形胎进行整形处理,因此热推挤弯头适用于大批量、连续生产,特别对于大口径弯头的生产,由于芯棒重量、体积很大,不论是对芯棒的安装、修磨、加热都需要较长的时间。
热推挤弯头采用无缝钢管或直缝钢管作为原材料,若使用直缝钢管推挤弯头时,其焊缝应放置在内弧受压位置或按GB/T 13401的要求。
5.2.2 冷挤压弯头
冷挤压弯头是利用金属受力时的可流动性,在室温下将钢管料坯压入带有弯曲形槽的型模内,形成两端没有直管段的弯头或一端带有直管段的弯曲件。
冷挤压弯头一般需配备普通压力机和挤压弯曲模具,挤压弯头模具如图1-5-3所示,由压柱1、导向套2、两个对中合并的弯曲模4组成。挤压弯曲时,把管坯放在导向套中定位,通过压力机压下压柱,压柱推压管坯,强迫管坯进入弯曲模中挤压弯曲成形,管坯在挤压弯曲过程中不仅受弯曲力矩的作用,还受轴向力和与轴向力方向相反的摩擦力作用,使中性层向外侧偏移,从而大大改善了弯曲外侧的壁厚减薄量和横截面圆度,为弯头成形质量提供了有利的变形条件。

图1-5-3 冷挤压弯头示意图
1—压柱;2—导向套;3—管坯;4—弯曲模
冷挤压弯头适用于较小弯曲半径的弯头,可弯制的最小相对弯曲半径R/D≈1.3,弯头的横截面圆度小于3%,外侧的壁厚减薄率小于9%。弯头挤压装置结构简单,不需要专门设备,生产效率较高,这是冷挤压弯头的显著优点。但冷挤压弯头一般要求管材的相对壁厚t/D>0.06,否则钢管会由于钢性差而丧失稳定性,导致管件的内弧侧起皱或使管件扭曲。
当要求挤压相对壁厚t/D<0.06的管材时(需要管材有较好的塑性),需要增加通球扩定径工序,即在挤压成形的半成品管内依次放入表面光滑的实心钢球,钢球直径从小到大,再从大到小,用压柱依次把钢球压入,挤出即可,钢球表面应涂刷40#~50#机油,以增加挤压时的润滑作用。
为了降低单位冷挤压力、延长模具使用寿命、提高弯头表面质量,应对管坯表面进行润滑处理。润滑处理方法为:在管坯表面涂刷40#~50#机油,再均匀涂抹上一层石墨粉,能保证加工过程中有良好的润滑作用。
5.3 钢管压制弯头
在石油化工、锅炉制造业、造船业等工业中,常用到不同材料、不同规格的弯头,这些弯头的截面中心层弯曲半径一般为管子外径的1倍或1.5倍。
压制弯头就是采用模具和弯头外形相同和相近的上、下模压制成形。在压制过程中,为了提高管子的塑性变形和减小变形抗力,对于碳钢弯头和合金钢弯头,一般都是采用热压成形,但对于不锈钢弯头,由于不锈钢始锻温度区间小,同时不锈钢中的合金元素在高温加热过程中易烧损,因此一般都是采用冷压成形。
图1-5-4所示为在压力机上使用模具压制90°弯头的示意图,图1-5-4中1是下模,是弯头外圆弧面的造型模腔,图中4是上模,是弯头内圆弧面的造型模腔,上下模压合后,就组成了压制弯头的外形轮廓。为了防止管子弯曲时横截面变为椭圆形和内侧壁出现折皱,压制前管内放入了芯子5,芯子是由两半组成并放在管子内径正中,其上端起压制弯头内圆弧面的作用,下端起压制弯头外圆弧面的作用,图中3称为马蹄模,是控制弯头管口圆度、保证管口不起皱的重要工具,马蹄模装在管口处并插入管节内,马蹄模的“豁口”贴合在芯子平台面上,压制时可以驱动芯子下压,使芯子底圆弧面与管子的外圆弧面贴合,管子的外圆弧面又与下模贴合。马蹄面同上模配合,可使管子内弧两侧部分形成所要求的圆弧面。

图1-5-4 在压力机上使用模具压制90°弯头示意图
1—下模;2—弯头;3—马蹄模;4—上模;5—芯子
钢管压挤分为内支承和无支承压挤两种形式,内支承(见图1-5-4)使用在薄壁、半径较小的场合;而无支承(见图1-5-5)使用在厚壁、半径较大的场合。

图1-5-5 管内无支承热压挤弯头
为了保证管口的圆度,提高弯头的质量,对压制成形的弯头要进行整形处理。
当压制90°弯头时,其管坯尺寸(见图1-5-6)可按表1-5-4中公式计算。

图1-5-6 压制弯头
表1-5-4 模具压制弯头工艺参数的确定

表1-5-5 单位校正力p值

在热压挤弯头时,为了降低单位热挤压力、减小管坯与模具之间的摩擦、延长模具的使用寿命、提高弯头外表面质量,应对模具表面进行润滑处理。润滑处理方法为:用40#~50#机油混合石墨粉搅拌均匀,然后均匀涂抹在模具的内表面上,能保证热推挤过程中有良好的润滑作用。在压挤开始前和压制过程中,应用压缩空气吹扫下模具内的杂物和脱落的氧化皮,以减少压制时对弯头外壁的损伤。
钢管压制弯头的角度一般不宜超过90°,适用于电厂、钢厂、核电站等使用弯头壁厚较厚的场合。
5.4 钢板制热压弯头
钢板制热压弯头是长输油气管道中重要的压力管道元件之一,用于改变流体的走向,常用在大口径管道阀室、站场等相对狭窄的场所。
5.4.1 钢板制热压弯头的基本原理
由于钢板制热压弯头通常用于高压、厚壁、大口径管道,在室温下很难进行冷压成形,根据高温时金属变形抗力较小的特点,钢板制热压弯头采用热压成形,以钢板为原料,经过扇形钢板坯料切割、炉内高温加热、大型机械手抓取转运至大型压力机,再经压力机配合弯头上、下模具持续下压高温的钢板坯料,迫使热金属在上下模具所预留的空间内做外缘内外翻边流动(即内弧侧拉伸流动、外弧侧压缩流动)而最终成形弯头半片,然后利用专用设备对弯头半片进行整形、铣削坡口、组对、点焊,最后由专用的焊接设备将两组对好的弯头片焊接成形,形成弯头坯料,弯头坯料经热处理、管端坡口、检测检验等工序最终成形为符合外观尺寸和力学性能要求的弯头产品。
5.4.2 钢板制热压弯头的特点
与上面三种弯头采用钢管作为坯料的变形特点不同,由于采用了钢板作原材料,切割成形的初始坯料为扇形结构(或近似扇形),加热的扇形料坯在弯头模具上热压制时,其变形过程实质是外缘翻边变形,其外弧边为压缩类翻边、内弧边为伸长类翻边,中间轴线不变形。压缩类翻边在翻边变形区内产生压应力,易起皱。伸长类翻边在翻边变形区内产生拉应力,易破裂。其应变分布及大小决定于产品的结构形状(如弯头管径、曲率半径等)。变形程度E用下式表示。
E=D(α-sinα)/(2R-Dα)(-π/2≤α≤π/2)
式中 R——弯头曲率半径,mm;
D——弯头外径,mm;
α——弯头截面水平半圆角度(中间轴线为0,外弧为正,内弧为负)。
由公式和图1-5-7知:外弧侧受压缩向内弧方向翻边,钢板受挤压而壁厚增厚,容易起皱,起皱的程度和坯料加热温度、钢板厚度有关;内弧侧受拉伸向外弧方向翻边,钢板受拉伸壁厚减薄,容易破裂。由于外弧侧受压缩,内弧侧受拉伸,原材料下料时需根据弯头的曲率半径、角度、厚度增加外弧侧的长度,减小内弧侧的长度,以提高材料利用率。

图1-5-7 钢板制热压弯头
钢板压制弯头采用上下两半片弯头在内弧边缘和外弧边缘进行焊接的形式组对在一起,如图1-5-7(b)所示,形成双焊缝焊接结构弯头。
5.4.3 钢板压制弯头用设备及模具
钢板压制弯头用设备包括:原料切割机(或采用氧气+乙炔人工切割)、坯料加热炉、锻压操作机(或大型叉车)、大型压力机、弯头上下压模、母线切边机、上、下弦焊接机、管端切割机、管端坡口机等,当弯头需要热处理时,还需热处理加热炉、淬火槽、冷却水循环及冷却设备、回火炉等。
(1)原料切割机 原料切割机是一种大型数字控制自动化切割机,通过输入图纸图形给切割机数据库,该设备就可以按图形的尺寸进行精确切割下料,排除了人为干扰因素,保证了下料尺寸的统一性和准确性。
(2)坯料加热炉 坯料加热炉是用于对坯料进行加热的大型加热炉,此种加热炉由于炉膛容积大、要求温度高,大多采用燃气或原油加热,底盘采用固定或移动形式,炉门采用垂直升降隔热门,炉体采用高温耐火砖+保温材料+钢架结构,一般设计的最高加热温度在1000℃以上,以保证适应不同材质对加热温度的需求。
(3)锻压操作机 锻压操作机是把要加热的坯料放入高温炉内,加热完毕后再从高温炉内取出放入模具上的一种设备,适用于底盘采用固定形式的坯料加热炉和底座不移动的压力机,该设备可180°旋转、垂直升降,具有移动速度较快、前端耐高温等特点,能够快速、安全地把高温坯料进行转移,减少了坯料运转时温度的过多损失。
(4)大型压力机 大型压力机是给坯料压制变形时提供动力的设备,由于大口径、高钢级、厚壁弯头压制变形所需的压力很大,国内现有的大型压力机大都在3000t以上,大都采用四柱导向、大工作台面、多液压缸、大行程、下台面移动的形式。
(5)弯头上下压模 弯头上下压模是弯头基础成形的核心部件,在压力机的作用下,通过上、下模的合模压制,扇形的坯料就变形为弯头的基础坯料。上模和下模配合压制,使扇形坯料发生塑性变形,形成和弯头形状相当的半片弯头坯料。模具一般用铸钢铸造,通过热处理后,再经过机械加工制成,最后经过反复磨削修理而成。
(6)母线切边机 经过热压制完成的半片弯头坯料,用母线切割机进行加工余量的切割和焊接坡口的加工。该设备分为切割和坡口两个加工工序,切割一般采用氧气+乙炔的方法切除多余的加工余量,然后采用铣刀按标准要求加工焊接坡口。
(7)上下弦焊接机 两个铣好坡口的半片经过对焊组成一个完整的弯头,对焊弯头采用X形坡口形式,采用双面埋弧焊焊接,焊缝位置如图1-5-7(b)所示,即在弯头的最外弧和最内弧处,焊接时需在外弧、内弧的内外四个位置进行焊接,而且不同弯头焊接时运行的曲率弧线不同,上下弦焊接机就是为适应钢板制弯头的焊接而设计制造的专用设备,该设备由弯头固定机构、旋转驱动机构、焊接机构组成,分为上弦焊接机和下弦焊接机。上弧焊接时,把点焊好的弯头固定在上弦焊接机上(此时弯头内弧向下),焊接机构固定,依靠旋转机构带动弯头转动进行焊接,上弦焊接机可一次焊接完成外焊缝的外侧焊道和内焊缝的内侧焊道;同样下弦焊接机焊接时(此时弯头外弧向下)可一次焊接完成外焊缝的内侧焊道和内焊缝的外侧焊道。
(8)管端切割机 组对好的弯头其管端的平整度一般相差很大,且有不小的加工余量。管端切割机就是按照画的切割线把弯头两端口的多余部分切割下来的设备。一般采用氧气+乙炔的切割方法,分为弯头转动+割枪固定和弯头固定+割枪转动两种方式,前者是把弯头安装在一旋转转台上,使切割线在一平面内,把割枪嘴对准切割线,旋转转台,切割管端,用于口径较小、壁厚较薄的弯头。后者是把弯头安装在一固定平台上(有的平台可以旋转90°或平移),弯头一端或两端有与端口平面平行的转盘,转盘上固定有割枪,旋转转盘就可以切割管端,用于口径较大、壁厚较厚的弯头。
(9)热处理加热炉 热处理加热炉用于弯头淬火时加热,该设备要求加热温度高,温度偏差小,有时可以和坯料加热炉共同使用。
(10)淬火槽及淬火介质 淬火槽是存放冷却介质的大型容池,用于弯头淬火时的急冷,冷却介质一般为水,有时为了增强冷却效果,采用较高浓度的盐水。淬火槽中的冷却介质一般采用循环流动的方式,和冷却水循环系统及冷却设备连接在一起,进行有效降温。
热处理炉、管端坡口机与弯管用辅助设备的作用相同。
钢板制弯头的加工极限条件包括:加热炉加热温度极限、压力机极限、弯头成形极限。
加热炉加热温度极限是指加热炉实际的最高加热温度值(这里包括坯料加热炉和热处理加热炉),扇形坯料热压时其加热温度一般需达到奥氏体区温度,而热处理加热炉也需要达到热处理需要的最高温度,因此加热炉的加热温度极限直接限制着不同规格、不同材质钢板制弯头加工生产。
压力机极限是指压力机的最大工作压力和工作台面的最大尺寸及行程。压力机的压力及工作台面尺寸决定了所能加工弯头的最大直径、曲率半径和壁厚,最大行程表征了压力机的最大开口尺寸,决定了压力机所能加工弯头的最大直径。因此压力机的选用必须根据设计要求的最大弯头直径、壁厚、半径选择。
弯头的成形极限是指成形时弯头所能达到的最小相对曲率半径和最小相对壁厚,由GB/T 13401知:钢板制弯头的曲率半径分为1D、1.5D、3D,实践经验知:1D弯头的最小相对壁厚t/D≥0.01,否则成形时内弧会开裂或减薄严重,外弧严重起皱。
5.4.4 制造工艺
(1)钢板压制对焊弯头的工艺流程(见图1-5-8)

图1-5-8 钢板压制对焊弯头的工艺流程
(2)原材料检验及验收 钢板的厚度、规格根据需要直接定制,进厂后按照验收程序及标准验收,检验合格后投入生产线。
(3)下料 钢板制弯头的板坯料是一扇形,采用专用的等离子数控切割机将钢板按图纸尺寸和形状切割。
(4)加热压制 用专用机械操作机(或机械手)将切割好的弯头坯料送进加热炉中,多片叠放在一起,两片间适当间隔开,然后加热至规定温度,打开炉门,用专用机械操作机(或机械手)取出,送入专用压力机的弯头模具中,清扫上表面的氧化皮,启动压力机,压制钢板成半片弯头形状,从模具中取出半成品弯头。
(5)切边、铣边 取出后的弯头坯料,应先按弯头周长的一半加切割余量划线,然后装卡在专用的母线切边机上,先用气割切割多余的部分,再用铣刀按图纸要求尺寸加工两轴向坡口。
(6)弯头片组对 将两个弯头片组成一对,组对时内外表面应对齐,并保证弯头周长尺寸,然后进行间隔均匀点焊。
(7)焊接 把组对好的弯头分步安装固定在专用的弯头上、下弦焊接机上,按焊接工艺卡要求对组对好的弯头片进行焊接。
(8)端部切割 按图纸要求划线,使用切割工具沿弯头毛坯各管口的线切割,去掉毛坯余量。
(9)热处理(要求时) 为了恢复和改善材料的力学性能,将弯头坯件放入加热炉进行热处理,使对焊弯头达到技术条件要求的力学性能指标。
(10)清理、检验及包装 热处理后还需要进行除锈、无损探伤、坡口、坡口磁粉探伤、防腐、尺寸及外观检验,包装标识。