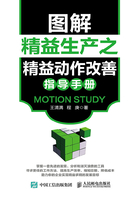
第一章 动作改善与变革
1.1 七大浪费与动作改善
在现场,浪费现象随处可见,如堆积如山的原材库存在报废的风险;可见或者不可见的不符合客户要求的不良品;原材料不断在不同区域无价值地转移,从待检区、检验合格区、仓库货架、生产线暂存区,最后到达生产线。现场有大量的浪费不可怕,可怕的是现场员工对待浪费的态度居然是熟视无睹,或是改善活动进行一半就知难而退。员工对待浪费的态度决定了企业的改善能力,如员工能将浪费看成是“企业提升现场管理能力的改善机会”,将浪费看成是“员工学习如何发现浪费、如何分析浪费原因和如何制定改善措施的培训机会”,将浪费看成是“管理者和一线员工的日常工作”,认为浪费无论大小,必须被根除,则必定能在工厂内部营造出持续改善的氛围,从而打造企业的现场改善能力。在浪费改善过程中,员工往往不缺少改善的能力和技能,而缺少正确的态度和发现浪费的问题意识。
1.七大浪费

图1-1 七大浪费
浪费在工作现场有不同的表现形式,丰田方式创始人大野耐一将其总结为典型的七大浪费,如图1-1所示。
(1)过量生产
过量生产指产品制造过早或者多余。过量生产是浪费的罪魁祸首,会引发其他浪费,因为有了过量生产才会有库存,有了库存,就会出现等待或者重复搬运,库存存放时间长就容易产生不良品,为了处理不良品就需要二次加工。
(2)搬运
产品从一个位置被转移到另一个位置。搬运的动作分解为放置、堆积、移动、整理等动作,这些动作都是浪费动作。搬运浪费一般都是由于布置不合理造成的。
(3)库存
过多的库存被摆放在仓库或者生产区域,包括原材料库存、半成品库存和成品库存。
(4)等待
处于一种停滞的状态,不进行任何操作。造成原因有作业不平衡、作业安排不当、等待物料、品质不良、机器修理等。
(5)过度加工
过度加工指的是在设计、品质及加工过程中的投入超过客户需求,从而造成企业资源的浪费,也叫过分加工的浪费。产品的开发设计或加工中,由于企业未能正确掌握客户需求,未能正确认识自己的生产能力及技术,以至于做出多余的或无效的工作。当然,如果是出于策略,如刻意增加一些效果,营造物超所值的印象,则另当别论。
(6)动作
这指在作业或者操作过程中花费比正常动作所需要的更长时间,或是动作本身就是多余的操作。常见的浪费动作有转向、反转、寻找、堆叠、移动、困难操作、重复动作、动作幅度大等。
(7)不良品
任何不良品的产生都是不良浪费,都会造成材料、机器、人工等浪费。原因可能是工序能力不足、生产现物管理方式或管理观念错误。
经现场长期实践摸索,增加第八种浪费——人才浪费,人才浪费是指没有充分利用人的能力,如安排的工作量不充足、没有充分调动员工的积极性或者应有的能力水平。
2.动作改善
对大多数人而言,浪费简单到“一听就懂,一说就会”,但在现场中消除浪费却很难实施,原因可能是现场人员对很多浪费都已经司空见惯,或者是发现浪费却不知如何改善,或者是制订了改善计划但是得不到实施部门的配合。为了消除现场浪费,企业需要培养现场人员正确理解浪费的能力、发现浪费的能力、提出改善方案的能力以及实施改善的能力,如图1-2所示。员工只有具备这些能力,才能很好地开展动作改善活动。

图1-2 发现浪费的能力
(1)正确理解浪费的能力
消除浪费的第一步是正确认识什么是浪费,如果员工连浪费都没有正确理解,就不可能做下一步或者下下一步的工作。如果一开始就错了,后面也会跟着错下去。
(2)发现浪费的能力
发现浪费的能力需要员工花费大量时间不断地训练才能产生。这种能力使员工从一系列操作动作中,辨认出哪些动作是多余浪费动作,哪些动作可以简化处理或者哪些动作操作不合理。
(3)提出改善方案的能力
发现了浪费并不等于完成了工作,有时候员工需要将发现的现象用另一种形式表达出来,让领导或者其他部门了解自己的改善方案,进一步判断改善想法的合理性及后续改善跟进工作的可实现性。只有自己了解而没有办法将改善想法展示出来,是没有办法实现同级别沟通、寻求上层领导协助的。
(4)实施改善的能力
改善分为自己改善和其他部门完成改善。如果是自己可以实施的改善就根据自己的能力来完成;如果需要其他部门配合完成,员工就需要跨部门进行沟通、商议、寻求支持、制订计划、跟进与确认改善工作。