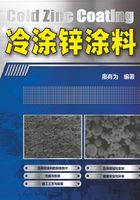
2.1 防腐蚀涂料概述
2.1.1 防腐蚀涂料体系
防腐蚀涂料指涂布于物体表面在一定条件下能形成薄膜而起保护、装潢或其他特殊作用(绝缘、防锈、防霉、耐热等)的一类液体或固体材料。因早期的涂料大多以植物油为主要原料,故又称作油漆。现在合成树脂已大部分或全部取代了植物油,故称为涂料。防腐蚀涂料作用主要是保护、装饰和掩饰产品的缺陷,从而提升产品的价值。产品一般采用复合涂装方式,体系依次分为底漆、中间漆和面漆。
(1)底漆
底漆的主要作用是防腐蚀、确保涂层与底材的附着力,并为后继涂层——中间漆或者面漆提供良好的附着基础。底漆主要有车间底漆、磷化底漆、环氧磷酸锌底漆以及富锌底漆。
(2)中间漆
中间漆的主要功能是增加漆膜厚度,以增强漆层体质。作为底/面之间的过渡层,在涂层配套正确的前提下,具有提高层间附着力的作用。中间漆主要有环氧封闭漆、环氧云铁中间漆以及厚浆型环氧中间漆等。国内最常用的是环氧厚浆涂料,而在桥梁、电站、港口和海上钢结构等防腐蚀工程中,却偏重于采用云母氧化铁环氧涂料和玻璃鳞片涂料。两者均以耐腐蚀的树脂为主要成膜物质,分别以云母氧化铁和玻璃鳞片为防锈颜料,再加入其他助剂而组成的厚浆型涂料。
(3)面漆
面漆主要有中低档的醇酸涂料、丙烯酸涂料、氯化橡胶涂料以及高档的聚氨酯面漆、氟碳面漆以及聚硅氧烷面漆。还有一些具有特种功能的防腐蚀涂料如防静电涂料、耐高温涂料等等。面漆主要作用是防止外界有害的腐蚀介质,如氧气、水汽、二氧化硫以及化工大气的影响。同时,面漆的美观装饰性也越来越受到重视。有时候,还要求最外层涂上一层清漆,如脂肪族聚氨酯清漆等,以获得更为致密的屏蔽漆膜。
2.1.2 防腐蚀涂料的特点
防腐涂料除了具有在严酷腐蚀环境下应用和长效寿命特点外,还有以下几个特点而区别于一般涂料品种。
(1)厚膜化
这是重防腐涂料重要标志之一。为此,现代重防腐涂料向高固体分、少溶剂、无溶剂化方向发展。涂层设计的目标是提高使用寿命,而使用寿命取决于腐蚀环境。这里使用寿命有两层含义:其一是指涂层运行使用至下一次维修时的间隔期限;其二是指一次性使用至涂层失去保护功能的期限。涂层的使用寿命是根据被保护对象本身的寿命、价值及维修的难易来确定的,ISO 12944-5对于涂层的使用寿命分为三个等级:低,2~5年;中,5~15年;高,15年以上。当然ISO 12944-5所说的使用寿命绝不是商业“承诺防腐寿命”,而仅是涂装设计一个技术参数,它的作用主要是为设计者制定一个比较合理的维修涂装时间表以做参考。
涂层的厚度对使用寿命非常重要,实验已经证明,在一定的腐蚀环境下,涂层配套确定之后,涂层厚度与保护寿命呈直线关系,如图2-1所示。

图2-1 涂层的平均寿命和厚度的关系
A—一道底漆加一道面漆;B—两道底漆加两道面漆;C—一道底漆加三道面漆;D—两道底漆加四道面漆;E—一道底漆加五道面漆(油基涂料和醇酸涂料,每道漆膜厚度是2.5μm)
Fick定律:腐蚀介质渗透达到涂层-金属界面的时间与涂层的厚度平方成正比,与扩散系数成反比,其数学表示式为:
式中,t为液体腐蚀介质渗透至涂层-金属界面的时间(t值越大间接表明防腐寿命越长);L为涂层干膜厚度;D为介质扩散系数(取决于涂层与介质结构、渗透压力、温度等参数)。
由此可见,重防腐涂装应尽量厚膜化(干膜200~1000μm),以提高涂层的使用寿命。
涂层厚度是根据腐蚀环境及使用寿命来确定的,三者的关系ISO 12944-5中有推荐要求,见表2-1。
表2-1 腐蚀环境、使用寿命和涂层厚度的关系

(2)高性能原材料的研发是重防腐涂料发展的关键
在防腐涂料的研究中,对于高性能的耐蚀合成树脂和新型的颜料、填料的研究与开发,国内外一直十分重视。一个重要的研究方向是在保持原有性能的基础上,克服其缺点并开发多方面功能。例如,聚合硅氧烷树脂的研发为克服丙烯酸树脂耐溶剂性差、不耐高温的缺点,采用有机硅氧烷原位、接枝聚合改性丙烯酸树脂的方法,大大提高了丙烯酸树脂的耐热性和耐溶剂性,即丙烯酸聚硅氧烷涂料。氟碳树脂的研发与应用已从高温干燥型发展到常温自然干燥型,设法降低VOC含量和改善重涂性是氟碳涂料的研究方向。导电聚苯胺防腐涂料的树脂本身导电且防腐性能优秀,属于本征型导电涂料。它克服了导电性与防腐性的矛盾,技术上比常规导静电涂料高出一个档次。聚脲防腐弹性体涂料和聚天门冬氨酸酯聚脲的性能与应用前景远优于聚氨酯。新型鳞片状金属锌粉替代目前广泛使用的球状锌粉,防腐性提高(阴极保护+屏蔽效应),锌粉用量可降1/3,制漆成本明显下降。
(3)表面处理是决定质量的首要因素
对于防腐工程表面处理的重要性怎么估计也不为过,如同一座高楼大厦不能建筑在沙滩上的道理一样。涂装前表面处理方法很多,如酸洗磷化、机械打磨、喷砂抛丸等。对于不同行业、不同的涂装对象可能采用不同的处理方法,但在重防腐领域,喷射除锈(俗称喷砂)迄今仍是最佳的工艺选择。其一,钢材表面清洁度达标有保证(Sa≥2.5);其二,表面粗糙度均匀(Rz=40~75μm)。而涂装前钢材表面粗糙度不仅增加了钢材表面积,还为漆膜附着提供了合适的表面几何形状,有利于漆膜与底材之间的粘接和漆膜厚度分布的均匀一致。刚喷砂后的钢材,表面能增大,处于活化态,3h之内喷涂防锈底漆,是涂料分子与金属表面极性基团之间相互吸引与粘接的最佳时期。
喷砂工艺应尽量标准化、规范化。如应尽量采用金属磨料,执行GB/T 18838.1《涂覆涂料前钢材表面处理 喷射清理用金属磨料的技术要求》(等同ISO 11124-1:1993),并可参考美国钢结构涂装协会(SSPC-SPCOM)所列出的喷射不同磨料所测得的粗糙度。喷砂后表面清洁度应执行GB 8923《涂装前钢材表面锈蚀等级和除锈等级》(等效采用ISO 8501-1:1988)。而表面粗糙度的检查应执行GB/T 13288—1991《涂装前钢材表面粗糙度等级的评定(比较样块法)》(参照采用ISO 8503—1985)和GB 6060.5《表面粗糙度比较样块 抛(喷)丸、喷砂加工表面》等标准。喷砂作业应尽量在喷砂房内进行,户外喷砂应采用带有布袋吸尘器的喷砂设备,以利于环境保护和劳动保护。
涂装前表面处理除了喷砂除锈外,喷砂前除油和除去可溶性盐等污染物同样是十分重要的前处理工序。一般施工者认为喷砂可以把它们清除,但是实际上只是把这些污染物的大部分深深地分散凿在钢材表面,形成更加隐蔽、危险性更大的污染。除油、除盐可采用高压喷射淡水(除油需加清洗剂)的工艺方法,可参照NACE No.5《高压淡水冲洗的清洁标准》(相对美国钢结构涂装标准SSPC-SP12)和GB/T 13312—1991《钢铁件涂装前除油程度检验方法(验油试纸法)》。
(4)涂层配套的正确性
钢结构工程重防腐涂装,一般分为底漆、中间漆和面漆。底漆的主要功能是防锈,增强与金属表面附着力;中间漆的主要功能是增加漆膜厚度,以增强漆层体质;而面漆除了装饰性功能之外,还有更多方面的功能要求。在选择涂料时,力求“底-中-面”三涂层配套正确,即要讲究其配套性。一般没有固定规律可循,大都是长期施工经验的总结。例如固化类型一致,如不宜将烘干型涂料喷在溶剂挥发型(自然干燥)涂料上面;不宜将强溶剂的面漆喷涂在弱溶剂的底漆上面等。
(5)推荐采用“底-面合一”施涂工艺
近年来,为适应重防腐涂装的需要,已有“底-面合一”的厚涂涂料出现,采用高压无气喷涂技术,一次可以喷涂几百微米,甚至几毫米,在大型钢结构工程中得到迅速广泛的应用。最常用的是高黏度环氧和聚氨酯涂料。这类漆固体含量一般在70%(体积分数)以上,甚至100%,施工时一般不加稀释剂,因此宜采用高压无空气喷涂机进行喷涂,也可刷涂。由于环氧树脂极强的粘接性能,使涂层牢固地附着在钢材表面,形成一道厚的防护涂层,有效地阻缓外界腐蚀性介质的浸入,其防护期可达10年以上。
(6)涂装现场管理是实现重防腐涂装设计目标的重要环节
涂装的目的在于涂层质量,而这是通过科学而严格的质量管理实现的。涂装工程质量管理是一项全员参与、贯穿全过程的系统工程。涂装工程质量管理包含很多的环节,其中最重要的部分之一是涂料生产厂家派出的涂料技术专业服务人员在现场对施工工艺的执行情况作出的检查、监督、指导和纠正。对整个施工质量的控制具有非常重要的意义。
2.1.3 防腐蚀涂料的新发展
(1)鳞片状金属颜料在涂料中的应用
由于鳞片状颜(填)料在漆膜中互相平行交错叠加,切断漆膜中的毛细孔,起到迷宫效应,能有效屏蔽和极大阻缓了外界水、氮、氯离子等腐蚀介质的渗透,提高涂层的抗腐蚀能力。目前,涂料工业中常用的鳞片状防锈颜料主要有云母氧化铁、玻璃鳞片等,属于非金属原料。考虑到片状金属具有良好的延展性、导热性、可加工性以及装饰效果独特,市场发展前景良好,除铝粉外,一些新型片状金属填料陆续投放市场,如鳞片状锌粉、鳞片状不锈钢粉等。
以鳞片状锌粉为防锈颜料,选用不同的基料(如硅酸乙酯、环氧树脂、氯化橡胶等)可以研制出种类繁多的水性、溶剂型、无机或有机片锌富锌涂料。这些涂料不仅抗腐蚀性能优于普通球锌富锌涂料,并且由于锌粉添加量的大幅度减低(例如:环氧富锌底漆,球锌不挥发分中锌含量在70%左右,换成片锌锌含量可减至50%左右,节省金属锌粉用量约1/3),成本不高于甚至低于球锌涂料。更由于其单位面积的涂覆量更大,施工涂层更薄,已经被国外公司大量用于集装箱辊涂用车间底漆。所以,鳞片状锌基涂料是未来富锌涂料的发展方向之一。
鳞片状不锈钢粉最早用于石油管道的厚浆型重防腐涂料中,由于其本身的耐酸、耐碱、耐磨、耐高温等特性,增强了涂层的耐化学品性、耐老化性以及耐磨、耐高温变化的性能。但是,传统的不锈钢鳞片的厚度太厚,其松装密度都在2.0g/cm3以上,这就造成了不锈钢鳞片在基料中的悬浮性不好,易沉淀。致使不锈钢鳞片通常只能应用在喷涂厚度达到数百微米乃至数千微米的场合,使其应用受到了限制。
近几年来,国外对不锈钢鳞片涂料的研究有了突破性的进展,其突破点在于采用新的工艺,开发出超薄型的不锈钢鳞片。例如:美国Novamet公司生产的超薄型不锈钢鳞片的松装密度在0.8g/cm3左右,片径在10~30μm,厚度在0.6μm以下。采用这种薄型的不锈钢鳞片,选择适合的基料树脂,开发出超薄型不锈钢鳞片涂料,喷涂厚度仅为数十微米,而防腐效果却能达到喷涂厚度为数百微米的防腐效果。电子显微镜放大的不锈钢鳞片结构如图2-2所示。

图2-2 不锈钢鳞片的电子显微镜扫描图片
(2)高固体分涂料和无溶剂涂料的应用
通常防腐涂料每道涂覆干膜厚度25~50μm,要达到较大的膜厚,必然增加涂覆次数,这不但费工费时,更带来大量的有机溶剂挥发而污染环境,不符合各国政府对涂料中挥发性有机化合物(volatileorganiccompounds, VOC)含量越来越严格的限制。而高固体分涂料和无溶剂涂料正由于其高固体分、低VOC、不含或少含溶剂,符合涂料工业环保、经济、节能、高效这一大方向而日益受到重视。
在高固体分涂料中,环氧树脂涂料应用最为广泛。传统的环氧树脂涂料,体积固体分为50%左右,而高固体分涂料的体积固体分至少达到68%以上。很多高固体分环氧涂料的体积固体分达到80%~90%,溶剂用量则大幅度地下降。
无溶剂涂料则是高固体分涂料发展的必然结果。由于其彻底解决了有机溶剂挥发排放问题,对环境保护和劳动保护以及防火安全等均有积极意义。
无溶剂涂料广义地讲是指不含有机溶剂或水的涂料,狭义地说是指不含可挥发到大气中的有机溶剂的液体涂料。传统的清油、熟桐油是属于广义的无溶剂涂料。现代无溶剂涂料是指采用活性溶剂作为溶解介质的液体涂料。在其成膜过程中,活性溶剂与树脂反应交联而成为涂膜的组成部分,不像一般溶剂那样绝大部分挥发逸出。
无溶剂涂料的特点包括:①厚膜化,一次可喷涂100~1000μm;②边缘覆盖性好,甚至对没有处理过的钢板边缘也有很强的覆盖能力,比溶剂型涂料效果更好;③涂层不收缩,内应力较小,无伸长力;④具有突出的物理机械性能、耐磨性与耐化学品性;⑤无溶剂挥发到大气中,对环境保护和劳动保护以及防火安全等均有积极意义。
当然,提高涂料固体分并不是单纯地靠减少或不用有机溶剂来达到,它涉及成膜树脂的低黏度化、活性稀释剂的应用以及新型助剂的应用等一系列新原料和新技术。
(3)水性涂料的应用
常用的重防腐涂料都是采用有机溶剂作为涂料体系的稀释物。现在,人们开始意识到有机溶剂的危害性,主要存在以下两方面。一方面考虑人类自身的健康。多年来,世界卫生组织(WHO)一直关注着这方面的研究。多项研究表明,如果没有有效的防护措施,长期吸入有机溶剂,会导致所谓的“涂料综合征”(paintersyndrome),主要表现在容易疲劳、记忆力下降以及神经系统方面的疾病。另一方面是有机溶剂对于环境造成的危害。有机溶剂挥发后,在紫外线的作用下容易分解,产生具有高活性的产物。这些高活性的产物会与大气中的工业污染物以及汽车尾气,如氮氧化物和硫氧化物反应,生成一些对环境有害的物质,如臭氧等。这些有害物会导致盐雾、酸雨,影响生物的新陈代谢,导致全球气温变暖。
正因为有机溶剂的这些危害性,从20世纪70年代开始,欧美等国相继出台了相应的强制性法规,限制涂料中挥发性有机化合物(VOC)的含量,降低对环境的危害。近年来,国内也越来越关注这类问题,低VOC含量的产品成为今后涂料发展的趋势。
水性涂料,顾名思义,是以水为主要溶剂,同时用水来稀释和清洗的涂料。因此水性涂料的VOC含量较低,通常在50g/L以下。水性涂料因为主要溶剂是水,因此具有以下优点:①水的来源广泛,净化容易;②在施工过程中无火灾危险;③基本不含苯类等挥发性有机溶剂;④水代溶剂,可节省大量资源;⑤涂装时使用过的工具直接用水进行清洗;⑥工件经除油、防锈等处理后,不需要完全干燥即可施工。
在工业重防腐涂料体系中,主要应用的水性涂料有水性无机富锌底漆、水性环氧涂料(包括水性环氧富锌底漆)以及水性丙烯酸涂料。