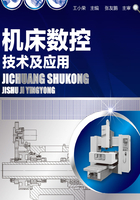
第1章 数控机床概述
1.1 数控机床产生与发展
1.1.1 数控机床的产生
科学技术和社会生产的不断发展,对机械产品的质量和生产率提出了越来越高的要求。机械加工工艺过程的自动化是实现上述要求的最重要措施之一。它不仅能够提高产品的质量,提高生产效率,降低生产成本,还能够大大改善工人的劳动强度。
许多生产企业已经采用了自动机床、组合机床和专用自动生产线。采用这种高度自动化和高效率的设备,尽管需要很大的初始投资以及较长的生产准备时间,但在大批量的生产条件下,由于分摊在每一个工件上的费用很少,经济效益仍然是非常显著的。但是,在机械制造工业中,并不是所有的产品零件都具有很大的批量,单件与小批生产的零件(批量在10~100件)约占机械加工总量的80%。尤其是在造船、航天、航空、机床、重型机械以及国防部门,其生产特点是加工批量小、改型频繁、零件的形状复杂而且精度要求高,如果采用专用化程度很高的自动化机床加工这类零件就显得很不合适,因为生产过程中需要经常改装与调整设备,对于专用生产线来说,这种改装与调整甚至是不可能实现的。近年来,由于市场竞争日趋激烈,为在竞争中求得生存与发展,就必须频繁地改型,并缩短生产周期,满足市场上不断变化的需要。因此,即使是大批量生产,也改变了产品长期一成不变的做法。频繁地开发新产品,使“刚性”的自动化设备即使在大批生产中也日益暴露其缺点。已经使用的各类仿形加工机床部分地解决了小批量、复杂零件的加工。但在更换零件时,必须制造靠模和调整机床,这不但要耗费大量的手工劳动,延长了生产准备周期,而且由于靠模误差的影响,加工零件的精度很难达到较高的要求。为了解决上述这些问题,满足多品种、小批量的自动化生产,迫切需要一种灵活的、通用的、能够适应产品频繁变化的柔性自动化机床。
数字控制(Numerical Control,简称NC或数控)机床就是在这样的背景下诞生与发展起来的。它极其有效地解决了上述矛盾,为单件、小批生产精密复杂零件提供了自动化加工手段。
数控机床的工作原理是:将加工过程所需的刀具与工件之间的相对位移量以及各种操作(如主轴变速、松夹工件、进刀与退刀、开车与停车、选择刀具、供给切削液等)都用数字化的信息代码来表示,并将数字信息送入专用的或通用的计算机,计算机对输入的信息进行处理与运算,发出各种指令来控制机床的伺服系统或其他执行元件,使机床自动加工出所需要的工件。数控机床与其他自动机床的一个根本区别在于,当加工对象改变时,除了重新装夹工件和更换刀具之外,只需要更换加工程序,不需要对机床作任何调整。
1952年,美国帕森斯公司(Parsons)和麻省理工学院(MIT)合作研制成功世界上第一台三坐标数控铣床,用于加工直升机叶片轮廓检查用样板。这是一台采用专用计算机进行运算与控制的直线插补轮廓控制数控铣床,专用计算机采用电子管元件,逻辑运算与控制采用硬件连接的电路。1955年后,该类机床进入实用化阶段,在复杂曲面的加工中发挥了重要作用。
我国从1958年开始研制数控机床,在研制与推广使用数控机床方面取得了一定成绩。近年来,由于引进了国外的数控系统与伺服系统的制造技术,使我国数控机床在品种、数量和质量方面得到了迅速发展。目前,我国已有几十家机床厂能够生产不同类型的数控机床和加工中心。我国经济型数控机床的研究、生产和推广工作也取得了较大的进展,它必将对我国各行业的技术改造起到积极的推动作用。目前,在数控技术领域中,我国和先进的工业国家之间还存在着不小的差距,但这种差距正在缩小。随着工厂、企业技术改造的深入开展,各行各业对数控机床的需要量将会有大幅度的增长,这将有力地促进数控机床的发展。
1.1.2 计算机数控系统的特点
随着电子技术和计算机技术的不断发展,数控系统经历了逻辑数字控制阶段(NC阶段)和计算机数字控制阶段(CNC阶段)。NC阶段数控系统发展经历了电子管时代、晶体管时代、小规模集成电路时代。自1970年小型计算机用于数控系统,数控系统发展进入CNC阶段,这是第四代数控系统。从1974年微处理器用于数控系统,数控系统发展到第五代,经过几年的发展,数控系统从性能到可靠性均得到很大的提高。自20世纪70~80年代,数控系统在全世界得到了大规模的发展和应用。从20世纪90年代开始,PC机的发展日新月异,基于PC平台的数控系统应运而生,数控系统发展进入第六代,但目前市场上流行的和企业普遍使用的仍然是第五代数控系统。
数控系统中引入了微型计算机(简称微机),使它在质的方面完成了一次飞跃。计算机数控(Computer Numerical Control,简称CNC)系统有许多优点。
(1)柔性好
硬件数控系统的许多功能是靠硬件电路来实现的。若想改变系统的功能,必须重新布线,但计算机数控系统能利用控制软件灵活地增加或改变数控系统的功能,更能适应生产发展的需要。
(2)功能强
可利用计算机技术及其外围设备,增强数控系统及数控机床的功能。例如,利用计算机图形显示功能,检查编程的刀具轨迹,纠正编程错误,还可检查刀具与机床、夹具碰撞的可能性等;利用计算机网络通信的功能,便于数控机床组成生产线等。
(3)可靠性高
计算机数控系统可使用磁带、软盘和网络等许多输入装置,避免了以往数控机床由于频繁地开启光电阅读机而造成的信息出错的缺点。与硬件数控相比,计算机数控尽量减少硬件电路,显著地减少了焊点、接插件和外部连线,提高了可靠性。此外,计算机数控系统一般都具备自诊断功能,可及时指出故障原因,便于维修或预防操作失误,减少停机时间。这一切使得现代数控系统的无故障运行时间大为提高。
(4)易于实现机电一体化
由于计算机电路板上采用大规模集成电路和先进的印制电路排版技术,只要采用数块印制电路板即可构成整个控制系统,而将数控装置连同操作面板装入一个不大的数控箱内,可与机床结合在一起,减少占地面积,有利于实现机电一体化。
(5)经济性好
采用微机数控系统后,系统的性能价格比大为提高。现在不但大型企业,就是中小型企业也逐渐采用CNC数控机床了。
1.1.3 数控机床的应用范围
数控机床确实存在一般机床所不具备的许多优点,但是这些优点都是以一定条件为前提的。数控机床的应用范围正在不断扩大,但它并不能完全代替其他类型的机床,也不能以最经济的方式解决机械加工中的所有问题。数控机床通常最适合加工具有以下特点的零件。
①多品种小批量生产的零件。图1-1表示了三类机床的零件加工批量与综合费用的关系。从图中可以看出,零件加工批量的增大对于选用数控机床是不利的。其原因在于:数控机床设备费用高昂,与大批量生产采用的专用机床相比,其效率还不够高。通常,采用数控机床加工的合理生产批量在10~200件之间,目前有向中批量发展的趋势。

图1-1 零件加工批量与综合费用的关系
②结构比较复杂的零件。图1-2表示了三类机床的被加工零件复杂程度与零件批量大小的关系。通常数控机床适宜于加工结构比较复杂、在非数控机床上加工时需要有昂贵的工艺装备的零件。

图1-2 数控机床适用范围示意图
③需要频繁改型的零件。它节省了大量的工艺装备费用,使综合费用下降。
④价格昂贵、不允许报废的关键零件。
⑤需要最短生产周期的急需零件。广泛推广数控机床的最大障碍是设备的初期投资大,由于系统本身的复杂性,又增加了维修费用。如果缺少完善的售后服务,往往不能及时排除设备故障,将会在一定程度上影响机床的利用率,这些因素都会增加综合生产费用。
考虑到以上所述的种种原因,在决定选用数控机床加工时,需要进行反复对比和仔细的经济分析,使数控机床发挥它的最好经济效益。
1.1.4 数控机床和数控系统的发展
现代数控机床及其数控系统,目前主要向高速、高精度化方面发展。
要提高机械加工的生产率,其中最主要的方法是提高速度,但是这样做会降低加工精度。现代数控机床在提高加工速度的同时,也在进行高精度化。目前可在0.1μm的最小设定单位时,进给速度达到24m/min。要做到这一点,就要对机械和数控系统提出更高的要求。
(1)机械方面
例如,机床主轴要高速化,就要提高主轴和机床机械结构的动、静态刚度;采用能承受高速的机械零件,如采用陶瓷滚珠轴承等。
(2)数控系统方面
主要是提高计算机的运算速度。现代数控系统已从16位的CPU,发展到普遍采用32位的CPU,并向64位的CPU发展。主机频率由5MHz提高到20~33MHz。有的系统还制造了插补器的专用芯片,以提高插补速度;有的采用多CPU系统,减轻主CPU负担,进一步提高控制速度。
(3)伺服系统方面
①采用数字伺服系统 使伺服电动机的位置环、速度环的控制都实现数字化。FANUC15系列开发出专用的数字信号处理器,位置指令输入后,它与从脉冲编码器检测来的位置信息以及从电动机测速装置检测来的速度信息一起,在专用的微处理器芯片内,进行控制位置、速度控制等运算,最后向功率放大器发出指令,以达到对电动机的高速、高精度控制。
②采用现代控制理论提高跟随精度 当数控系统发出位置指令后,由于机械部分不能很快响应会产生滞后现象,影响了加工精度。现代控制理论中有各种算法能够实现高速和高精度的伺服控制,但是,由于它们的计算方法太复杂,以往的计算机运算速度不够,很难实现。现在计算机的运算速度和存储容量都加大很多,有时还可采用专用芯片的办法,使复杂的计算能够在线实现,使得滞后量减少很多,从而提高了跟随精度。
③采用高分辨率的位置编码器 一般交流伺服电动机轴上装有回转编码器(脉冲发生器),用来检测电动机的角位移。显然,编码器的分辨率越高,则电动机转动角位移就越精确。现代高分辨率位置编码器绝对位置的测量可达163840p/r。
④实现多种补偿功能 数控系统能实现多种补偿功能,提高数控机床的加工精度和动态特性。数控系统的补偿功能主要用来补偿机械系统带来的误差。
a.直线度的补偿。随着某一轴的运动,对另一轴加以补偿,以提高工作台运动的直线度。
b.采用新的丝杠导程误差补偿方法。用几条近似线表示导程误差,仅对其中几个点进行补偿。此法可减少补偿数据的设定点数,使补偿方法大为简化。
c.丝杠、齿轮间隙补偿。
d.热变形误差补偿,用来补偿由于机床热变形而产生机床几何位置变化引起的加工误差。
e.刀具长度、半径等补偿。
f.存储型补偿。这种补偿方法,可根据机床使用时的实际情况(如机床零件的磨损情况等)适时地修正补偿值。
提高数控系统的可靠性,可大大降低数控机床的故障率。新型数控系统大量使用大规模和超大规模集成电路,还采用专用芯片提高集成度以及使用表面封装技术等方法,减少了元器件数量和它们之间的连线和焊点数目,从而大幅度降低系统的故障率。
此外,现代数控系统还具有人工智能(AI)故障诊断系统,用它来诊断数控系统及机床的故障,把专家们所掌握的对于各种故障原因及其处置方法作为知识库储存到计算机的存储器中,以知识库为依据来开发软件,分析查找故障原因。只要回答显示器提出的简单问题,就能和专家一样诊断出机床的故障原因,提出排除故障的方法。
由于CNC系统使用的计算机容量越来越大,运算速度越来越快,使得CNC系统不仅能完成机床的数字控制功能,而且还可以充分利用软件技术,使系统智能化,给使用者以更大的帮助。例如,将迄今为止必须由编程员决定的零件的加工部位、加工工序、加工顺序等由CNC系统自动决定。操作者只要将加工形状和必要的毛坯形状输进CNC系统,就能自动生成加工程序。这样数控加工的编程时间将大为缩短,即使经验不足的操作者也能进行操作。CNC系统如何与人工智能技术相结合,尚待研究开发。除了上述故障诊断和编程方面的应用外,还有更大的领域留待我们去探索。
越来越多的工厂希望将多台数控机床组成各种类型的生产线或者DNC(Direct Numeri-cal Control直接数字控制)系统。这就要求CNC系统提高联网能力。一般CNC系统都具有RS232远距离串行接口,可以按照用户的格式要求,与同一级计算机进行多种数据交换。为了满足不同厂家、不同类型数控机床联网功能要求,现代数控系统大都具有MAP(制造自动化协议)接口,现在已实现了MAP3.0版本,并采用光缆通信,以提高数据传送速度和可靠性。