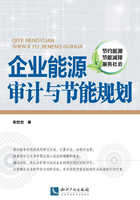
第二节 企业基本情况
2.1 企业简况
2.1.1 企业情况简介
某市煤焦化企业是由该企业实业有限公司于2008年8月以绝对控股的形式投资7.2亿元兴建设计“年产为95万吨捣固焦”项目企业。
2010年~12月工业增加值及综合能耗的核定结果为:工业总产值93283.37万元,工业增加值9914.95万元。
公司位于xx市工业园区北区,占地0.4平方公里,是xx市煤炭深加工与利用的大型煤化工企业之一,被列为2008年自治区经贸委和xx市重点工业项目单位。项目于2008年7月11日奠基,2009年12月26日两座焦炉全面投入试生产。现有固定资产5.5亿元,拥有员工588人,其中大专以上学历的有67人,并有各类技术人员和管理人员70人。
主要产品有:二级冶金焦、焦油、硫铵、粗苯等,产品主要销往北京、天津、唐山、包头等地区。2010年(审计期),主产品焦炭产量为934946.18吨,接近设计产量;生产副产品煤焦油39655.16t,粗苯10399.00t,外供焦炉煤气199856530.00Nm3。
该项目采用目前焦化行业比较成熟的2×72孔TJL4350D型、双联下喷、单热式废气循环、侧装煤捣固焦炉,炭化室高度4.3m;配套脱硫及硫回收、蒸氨、硫铵、洗脱苯等全套化产回收装置。循环系统产生的废水经过生化处理用于熄焦,除尘方面建立地面除尘站进行处理。整体工程技术成熟可靠,资源利用率高,环境效益好,设计规范,工艺科学合理,设备配置先进。在同行业中,科技含量处于国内前列地位。
2.1.2 地理位置及交通运输
某市煤焦化企业所处地理位置中心为:东经106°51′6″,北纬39°49′57"。
公司地处全国重要的焦煤产出地xx市境内,其位置所在的xx市工业园区北区,毗邻xx煤矿,南距海勃湾城区18公里,西侧靠近110国道、包兰铁路,且紧邻京藏高速(G6)公路。企业所在地地理位置优越,交通十分便利,原料产品进出运输极为方便。
2.2 主要产品生产工艺概况
2.2.1 主要产品生产工艺
本项目主要产品生产工艺为捣固炼焦。
炼焦采用炉外煤饼捣固侧装入炉高温干馏湿法熄焦工艺,焦炉采用TJL4350D型焦炉。TJL4350D型焦炉借鉴了化学工业第二设计院设计的双联、下喷、废气循环焦炉技术及TJL940E型捣固焦炉成功的经验,并根据非钢铁企业没有贫煤气的特点,采用了化学工业第二设计院设计的双联、下喷、废气循环、单热式捣固侧装煤焦炉,该焦炉具有国内先进水平。
主要产品生产工艺:当装煤机行至煤塔下方时,通过摇动给料器将煤捣实后装入装煤机的煤箱内,用18锤微移动捣固机分层捣实,然后将捣好的煤饼由装煤车从机侧装入炭化室。煤饼在炭化室内950℃~1050℃的高温下干馏,经过约22.5小时的干馏,即可成熟。成熟的焦炭由推焦车推出,经拦焦车导入熄焦车,然后由熄焦车送至熄焦塔喷水熄灭红焦。熄焦后的焦炭卸至凉焦台。
2.2.2 项目主要生产设备
本项目主要生产设备焦炉TJL4350D型焦炉,炉组规模为2×72孔炭化室。按设计每孔炭化室一次装入干煤量为23.67t,焦炉周转时间为22.5h,结焦率为75.8%,年工作日为365d,年消耗干煤量为1260683t,则年生产能力为:全年生产干全焦应达955598t。
2.2.3 主要产品生产工艺(流程)图
本项目主要产品生产工艺(流程)图如下图(图1-1)所示。

图1-1 生产工艺流程框图
2.2.4 焦炭及其附属产品生产工艺
本企业采用捣固焦工艺生产冶金焦及附属产品。
捣固炼焦技术是一种可根据焦炭的不同用途,配入较多的高挥发分煤及弱粘结性煤,在装煤推焦车的煤箱内用捣固机将已配合好的煤捣实后,从焦炉机侧推入炭化室内进行高温干馏的炼焦技术。
捣固炼焦的工艺过程:是在炼焦炉外采用捣固设备,将炼焦配合煤按炭化室的大小,捣打成略小于炭化室的煤饼,将煤饼从炭化室的侧面推入炭化室进行高温干馏。成熟的焦炭由捣固推焦机从炭化室内推出,经拦焦车、熄焦车将其送至熄焦塔,以水熄灭(湿法熄焦)后再放到凉焦台,由胶带运输经筛焦分成不同粒级的商品焦炭。
工艺流程说明:
该煤焦化有限公司采用的主要生产设备为TJL4350D捣固型机焦炉。该型焦炉炉体为双联火道、废气循环、宽炭化室、宽蓄热室、焦炉煤气下喷的单热式焦炉。熄焦采用湿法熄焦;装煤采用捣固侧装方式;装煤、推焦设有地面除尘站。
(1)备煤车间
备煤包括煤的堆存、配煤、粉碎和输送。
①煤场。煤场主要用于贮存各种炼焦煤。炼焦煤在煤场经过一段时间的贮存后,能够达到煤质均匀化和脱水的目的;同时保证焦炉连续、均衡生产,并稳定焦炭的质量。
所建煤场110000m2,设计容量为22万t,操作容量为10万t。按4种源煤计算,能满足焦炉15天的用煤量。
②地下受煤坑。通过传送带,将地下受煤坑的各种牌号炼焦用煤,根据配煤试验确定的配比进行配合,使配合后的煤能够炼出符合质量要求的焦炭,同时合理利用煤炭资源,降低生产成本。受配煤供给采用锥形斗嘴,操作稳定,仓壁配有仓壁振动器,可防止配煤斗嘴棚料,提高配煤的准确性。
③粉碎,粉碎机室是将配合后的煤进行粉碎处理,使其细度<3mm的煤达到80%以上,从而保证装炉煤的粒度均匀,达到提高焦炭质量的目的。
由受配煤传输带来的配合煤经除铁件后,进入粉碎机室进行粉碎。粉碎机为2台200t/h的反击式粉碎机,1用1备。
本工程设计采用地下受煤坑,备煤工艺采用先配合再粉碎的工艺流程。备煤系统分为卸料系统、备料系统及配煤粉碎系统。从精煤卸料开始至煤场为卸料系统;从煤场开始至配煤仓顶为备料系统;从配煤仓下电子自动配料秤开始至煤塔顶为配煤粉碎系统。炼焦所需的洗精煤运至煤场,由推土机或装载机进行推靠堆积,用旋臂式取料机取煤。配好的煤通过皮带机送到粉碎室,粉碎后的煤通过胶带机送入焦炉煤塔中,保证焦炉的正常生产。
备煤车间工艺流程见图1-2。

图1-2 备煤车间工艺流程简图
(2)炼焦、熄焦车间
炼焦采用炉外煤饼捣固侧装入炉高温干馏湿法熄焦工艺,焦炉采用TJL4350D型焦炉。TJL4350D型焦炉借鉴了化学工业第二设计院设计的双联、下喷、废气循环焦炉技术及TJL940E型捣固焦炉成功的经验,并根据非钢铁企业没有贫煤气的特点,采用了化学工业第二设计院设计的双联、下喷、废气循环、单热式捣固侧装煤焦炉,该焦炉具有国内先进水平。炉组规模为2×72孔。
熄焦塔高36米,顶部装有折流式捕尘器,可捕集熄焦时产生的大量焦尘等,除尘效率在80%以上。
炼焦工艺流程简述:
贮煤场的精洗煤由输煤皮带运至偏置于机侧装煤推焦机上方的贮煤塔备用,中途用电磁除铁器除掉煤中的铁块或铁器。通过摇动给料机连续均匀分层给料并由设于上方的多锤捣固机逐层夯实,然后从机侧将捣好的煤饼送入各炭化室中,煤饼在950℃~1050℃的高温下干馏成焦炭,成熟的焦炭由推焦车推出经除尘拦焦车导入熄焦车箱内,然后由熄焦车运至熄焦塔喷淋熄焦,熄灭后的焦炭被卸至凉焦台,凉焦台上的焦炭冷却后经刮板放焦机、皮带机将焦炭送往筛焦工段进行筛分处理。
原料煤在炭化室内干馏过程中产生的荒煤气汇集到炭化室顶部空间进入机侧上升管,在桥管处由循环氨水喷淋冷却,700℃左右的荒煤气在桥管及集气管内经循环氨水喷洒后温度降至82℃左右,荒煤气中焦油等同时冷凝下来。煤气和冷凝下来的焦油等同氨水一起经吸煤气管道进入冷凝鼓风工段,进入煤气净化系统。装煤过程逸散的荒煤气,由设在炉顶的消烟除尘车吸至车上燃烧室,完全燃烧后经过洗涤烟尘分离后,废气排入大气,洗涤用水排入粉焦沉淀池循环使用。出焦过程中产生的焦尘由设置在拦焦车上的集气罩将推焦烟气收集后,送到地面站布袋除尘器净化后排入大气。
焦炉加热用的回炉煤气经煤气总管、支管从焦炉下部进入各燃烧室,经焦炉煤气预热器预热至45℃左右送入地下室,再经下喷管进入燃烧室立火道与从废气交换开闭器进入蓄热室经预热的空气汇合燃烧。燃烧后的废气通过立火道顶部跨越孔进入下降气流的立火道,经过蓄热室热交换后再进入小烟道,经废气交换开闭器、分烟道、总烟道、烟囱排入大气。
上升气流的煤气和空气与下降气流的废气由液压交换传动装置定时进行换向。
(3)筛焦车间
焦炭按四级筛分(≥40mm,40~25mm,25~10mm,<10mm)。筛焦楼内设振动筛,按粒径大小进行筛分。筛焦楼内设有4个冶金焦仓和焦丁、焦末仓各1个。仓上使用可逆配仓胶带机布料及密封。
凉焦台上的焦炭放至胶带输送机送入筛焦楼内的三层振动筛筛分,筛上≥40mm,筛中40~25mm和25~10mm的焦炭,筛下<10mm,筛分后的焦炭分别进各自的贮仓,直接装车外售或送至焦场堆存;<10mm小焦及焦粉可外卖,也可破碎后掺混炼焦。
炼焦车间从装煤至筛焦整个过程的工艺流程简图如下面框图(图1-3)所示。

图1-3 炼焦车间工艺流程简图
(4)煤气净化车间
由焦炉来的荒煤气采用横管初冷却器两段冷却工艺,由设置于鼓风机前的蜂窝式电捕焦油器进一步脱除煤气中的焦油雾;煤气鼓风机后脱硫采用pds栲胶为复合催化剂的湿式氧化法脱硫工艺;脱氨采用泡沸伞式饱和器法硫铵工艺;煤气脱苯采用焦油洗油洗苯工艺。其煤气净化系统如下:
焦炉来荒煤气 →初冷器 → 电捕焦油器 → 煤气鼓风机 → 脱硫塔 → 泡沸伞式饱和器 → 终冷塔 → 洗苯 → 净化煤气自用或外送。
①冷凝鼓风及电捕。本工段包括焦炉荒煤气的间接冷却、电捕除焦油、煤气输送及焦油、氨水分离等工艺。
高温焦炉荒煤气经气液分离器分离后降至82℃左右,再依次进入并联操作的间接式横管初冷器进行一、二两段冷却,煤气冷却至22℃,接着,煤气入蜂窝式电捕焦油器,在高压直流电场作用下除去所含的焦油雾。而后,煤气进入煤气鼓风机加压送往脱硫工段。
从煤气气液分离器分离的循环氨水与焦油混合液进入机械化氨水澄清槽。其中,沉积的焦油渣由刮板机刮出落入渣箱,定期运往备煤系统掺入炼焦煤料中;循环氨水由澄清槽上部引至循环氨水中间槽,继续由循环氨水泵返送回焦炉系统用于冷却出炉的高温荒煤气;剩余氨水经蒸氨后的蒸氨废水送入生化污水处理站处理;焦油从澄清槽下部经液位调节器控制流入焦油中间槽作为产品送往油库。
在煤气间接式初冷器中冷却产生的煤气冷凝液和喷洒冲洗液首先进入冷凝液中间槽,然后溢流至冷凝液贮槽。该冷凝液的一部分送进混合液槽中,与一定量的焦油混合后用作煤气初冷器的喷洒液,以清除煤气初冷器内冷却横管外壁上的积萘,提高初冷器冷却煤气的效果;其余冷凝液则送入循环氨水与焦油混合液系统。
②脱硫工段。本工段包括煤气的脱硫、脱硫液的再生、硫泡沫沉淀分离和熔硫、硫磺产品的贮存及剩余氨水的蒸馏等工艺过程。
从煤气鼓风机来的煤气,首先进入煤气预冷塔底部;来自冷鼓工段的氨水则从预冷塔顶部进入、喷洒,与煤气逆流接触将其冷却。然后煤气进脱硫塔与塔顶喷淋的再生脱硫母液逆液接触,经过脱硫的煤气自脱硫塔上部引出送往硫铵工段。
脱硫液从脱硫塔底部流经液封槽进入反应槽,由此用泵送再生塔底与压缩空气混合一起自下而上顺流接触,氧化再生。再生后的脱硫液由再生塔上部流出,经液位调节器返回脱硫塔循环再用。
由脱硫液再生产生的硫泡沫浮于再生塔顶扩大部分,利用位差自流入硫泡沫槽,通过加热、搅拌、澄清分层后,清液经碱液漏斗返回反应槽,浓缩的硫泡沫则直接流入熔硫釜熔硫。熔融硫冷却盘,自然冷却后即为产品硫磺,入仓待售。
在生产过程中,为了避免脱硫液积累过量铵引起的降低脱硫效率,需排出少量废液,送生化污水处理站处理。
③蒸氨工段。脱硫过程中的剩余氨水引入蒸氨塔内进行蒸氨,蒸出浓氨气经冷凝冷却后制得含氨18%~20%的浓氨水,送入脱硫液槽,兑入脱硫液中,作为补充碱源。
对蒸氨废气选用目前国内较先进的氨裂解处理技术。在裂解炉内,氨气在触媒的作用下,通过控制炉温可将蒸氨废气中的氨还原成氢气、氮气和一氧化碳气,并将这部分混合气体返回煤气管道中,不仅防止了对大气的污染,而且还可增加煤气量,是一项回收能源、化害为利的控制措施,该技术成熟、可靠。
④硫铵工段。由脱硫工段送来的煤气经煤气预热器预热至70℃后进入喷淋式饱和器上段的喷淋室,在此煤气与循环母液充分接触,使其中的氨被硫酸吸收。煤气经饱和器内的除酸器分离酸雾后送至洗脱苯工段。
在饱和器母液中不断有硫铵晶体生成,用结晶泵将其连同一部分母液送至结晶槽,然后经离心分离、干燥、称重、包装后外售。离心分离出的结晶母液返回饱和器循环使用。
⑤洗脱苯工段。来自硫铵工段的粗煤气,首先进入煤气隔板式终冷却器,冷却后从洗脱塔底部入塔,由下而上经过洗苯塔填料层,与塔顶喷淋的循环洗油逆流接触,煤气中的苯被循环洗油吸收,进一步脱除煤气中的焦油和萘;再经过塔的捕雾段脱除雾滴后离开洗苯塔,其中部分净煤气送焦炉作回炉煤气及脱苯管式炉燃料,剩余部分外送。
由洗苯装置送来的含苯富油,首先进入粗苯冷凝冷却器,与脱苯塔来的粗苯蒸气间接接触换热到60℃左右,然后进入贫富油换热器,与脱苯塔底来的热贫油间接换热到120℃~130℃进入管式炉,在管式炉中通入400℃过热蒸汽,富油被加热到180℃~185℃进入脱苯塔,其中1%~2%的富油进入再生器;再生器底部聚合的残渣定期排出;再生器顶部蒸出的气体进入脱苯塔。另外,98%~99%的富油进入脱苯塔蒸馏。所得粗苯外售,脱苯后的贫油返回洗苯塔循环使用。
脱苯塔顶部出来的粗苯蒸气,经粗苯冷凝冷却器进入油水分离器,分离出来的粗苯流入回流槽,在此用泵抽出部分粗苯送到脱苯塔顶回流,多余部分流入计量槽,计量后放入粗苯贮槽,用液下泵装入汽车槽车外售。
脱苯塔底热贫油自流通过贫富油换热器,经间接换热后流入脱苯塔的贫油槽。再经泵抽出,送进一段、二段贫油冷却器,在此用循环水和低温水将贫油冷却到27℃—30℃,送至洗苯装置的洗苯塔顶进行喷洒,吸收煤气中的苯,洗油循环使用。
从脱苯塔侧线引出的萘油,自流入萘油再生残渣槽。
为了减轻终冷循环水中污染物的积累和对设备的腐蚀,从其下段循环泵出口引出部分污水,送生化污水处理站处理。
2.2.5 产出情况
2010年该煤焦化有限公司主要产品产量如下表(表1-5)所示。
表1-5 2010年产品产量结构表

**说明:“产品合计”中的实物量为产品总量的焦炭折合值。
由于金融危机的波及,市场需求的低迷,该煤焦化生产线的运行也受到一定影响,所以焦炭产品产量只是接近设计产量。
2.2.6 主要工艺(工序系统)能耗情况
(1)在审计期内本项目主要工序(生产系统)的能源消费量如下表(表16)所列。
表1-6 该煤焦化有限公司2010年能源消费流向表

由上表可以看出,本项目主要工序(生产系统)的能源消费量当量值为1160073.26tce。
(2)在审计期内本项目产品产量结构如下表(表1-7)所列。
表1-7 该煤焦化有限公司2010年产品产量结构表

由上表可以看出,本项目2010年产品产量(外供总量)折合标准煤当量值为1009442.18tce。
(3)主要工序(生产系统)能耗
根据GB21342—2008《焦炭单位产品能源消耗限额》可知:
主要工序(生产系统)能耗=能源消费量- 外供总量
= 1160073.26tce-1009442.18tce
= 150631.08tce
即主要工序(生产系统)能耗为150631.08tce(不含辅助系统和附属系统能源消耗)。
2.3 分类能源系统配备能源流向
某市煤焦化企业2010年1~12月消耗的能源有洗精煤、电力、焦炉煤气、柴油、水等。电力主要由电网提供并通过一系列的变电输送到各个车间;焦炉煤气来自本厂炼焦工段,用于焦炭生产、附属产品的生产和办公生活供热等;外购的柴油,主要用于堆运配煤;水主要来自自建水源井及园区水网(园区水网为补充备用),用水分为生产用水和生活环境用水,生产用水为熄焦用水,全部为污水生化处理水,生活环境用水分为洗浴用水及单位食堂宿舍用水、冬天取暖用水、地面绿化喷灌用水等。如下页图(图1-4)所示。

图1-4 该煤焦化有限公司能源系统流向图
2.3.1 电力系统配备
本项目采用双回路供电,从园区35KV变电站10KV侧引入两路电源,向企业供电。用电规格:10KV,380V,220V,24V,50Hz。如下图(图1-5)所示。

图1-5 该煤焦化有限公司电力系统简图
2.3.2 供热系统
热媒采用冷鼓工序横管冷却器上段热水(以锅炉蒸汽补热),供水温度70℃/55℃热水,室内采暖系统根据建筑物特点采用双管上供下回式或采用水平串联式系统(散热器、管材选择:散热器有一部分为四柱型铸铁散热器,其他部分多采用彩钢散热器;室内管材采用焊接钢管,DN≤32丝接,DN>32焊接)。供热系统简图见下图(图1-6)。

图1-6 供热(采暖)系统简图
2.3.3 水系统
公司水源为自建水源井和园区自来水管网(千钢东水源水库),以互补形式供应厂区自来水,新水供量为80m3/h,用于生产、生活、淋浴、绿化及锅炉房补水。湿法熄焦用水全部为污水生化处理后的复用水。
水源井的位置在公司的南部。
企业生产主要耗水工序——熄焦所用的水,由设计循环流量为100m3/h的场内污水处理车间提供。完全可以保证生产所需。如下图(图1-7)所示:

图1-7 企业水循环系统简图
2.3.4 主要生产配能用能设备列表
表1-8 主要供配电变压器汇总表

表1-9 主要设备配套电机汇总表

续表

注1.*为工信部公告([2012] 第14号)《高耗能落后机电设备(产品)淘汰目录(第二批)》包含设备,此处有51台,总功率为1868Kw。
注2.上表中电机凡同一设备上超过一台的,均为一用一备,或一用多备;再按80%的同时系数计算,所以企业实际运行电机总功率应在5000Kw以下。(另有少数非主要、小功率电机未予录入)
表1-10 堆运配煤用车装备

2.4 企业能源流向概况简介
企业在审计期内消耗的能源主要为精煤、电力、柴油、水,另有来自自产的焦炉煤气和水蒸气。其中精煤为焦炭生产的主要原料;电力主要用于生产及辅助生产过程机械设备的运转动力;焦炉煤气主要用于炼焦、化产、锅炉系统、职工食堂等,除作为化产原料外主要为炼焦生产、采暖、职工洗浴等提供热量;水主要为生产用蒸汽、办公、生活、绿化及消防用水,循环处理后的生化水用于熄焦。
2.4.1 精煤
企业在审计期内精煤(干)消耗量为1256379.36t,此为企业主产品——焦炭生产的原料用煤。考虑到风侵、堆失等环节漏损,这个消耗量已将近0.3%(尤其xx地区行风天数多、风速大,露天储煤损失更为严重)贮煤损失包括在内。精煤(湿)的低位发热量以该煤焦化有限公司质计部当年(2010年)的“发热量检测报告”为依据——“6461kcal/kg”。换算后可得精煤折标系数为0.923kgce/kg。

图1-8 精煤流向简图
2.4.2 电力
该公司审计期内总用电量为3410.80万kWh。其中已包括建筑面积为5847.5m2的办公、生活区等照明的年用电和食堂、浴室用电及线变损等,这部分用电合计不到总耗电的10%。
公司配电主要采用380/220V两个电压等级,少部分动力电为10KV。共六台变压器,供生产、办公、生活区用电。由10KV线路入厂,分三个变电室,每个变电室装两台变压器,向周围生产车间或办公室或生活区辐射供电,形成供电网,其中1#变电室承担全厂高压用电分配。
电力流向图见图1-5。
2.4.3 供热(汽)
经现场考察该公司供热主要分为生产用热和冬季采暖系统用热、洗浴、办公等生活用热。
生产用热,一部分来自炼焦余热的回收利用,如烟道余热对锅炉入水通过在烟道中盘水管的预热、焦炉煤气余热(未冷却前的高温煤气可免去反应所需的加热过程)在化产反应过程中的直接利用等;另一部分来自锅炉蒸汽。
生活热源来自蒸汽锅炉。
企业装有三台“WNS20—1.25—Y(Q)”卧式锅炉,夏季一开一待一备,冬季两开一待。每台锅炉的额定蒸发量为20t/h,夏季用气量小,实际蒸发量达到10t/h就能满足生产和生活的需要。
热力流向图见图1-6。
2.4.4 用水情况
企业在审计期内用水量为1086704m3,其中包括生产用水1054809t(辅以循环生化水),生活、绿化用水为31895m3。生产用水日均用水量为2889.89m3/d;生活、绿化等用水,日均用水量为87.38m3/d(3.64m3/h)。
供水水源为自建水源井、园区水网(千钢东水源水库)及全厂污水回收经处理后的生化水。水的循环利用率达到96.49%以上。除熄焦的汽化排水外,全厂污水全部进入生化循环系统,经生化处理后重复利用。已实现地面污水的0排放。
水源井的位置在企业的南部。
水流向图见图1-7。
2.4.5 燃油
燃油主要为柴油,供厂内7台210马力装载机和1台240马力的推土机堆运配煤使用,审计期内共消耗柴油1131t,折标准煤1647.98tce。已含0.5%的购入贮存环节损失(为5.66t,折标准煤8.24tce)。
燃油流向图见下图(图1-9)。

图19 柴油流向简图
另有少量汽油,年用量为5t,用于业务联系小车。