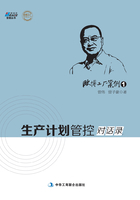
五、第五层觉知:执行过程中要频繁地进行总结
(一)变革前的问题
变革前的工作习惯
没有关注改善动作的效果,没有每天关注数据,所以,每天数据有没有变化,不确定!动作改善有没有效果,不确定!凭感觉评估每个人工作的好坏!
(二)变革后的动作

:降低停工待料工时激励方案是一个临时的考核方案,它把停工待料工时的降低直接与奖罚挂钩。如停工待料工时每线每周低于8小时,整个攻关小组的成员每人奖励50元。停工待料工时再降低,奖励金额更高。
(三)在执行过程中遇到的问题及措施

:总装车间停工待料一方面是外购物料造成的,另一方面是前工序的自制件造成的,而前工序的自制件跟模具有非常大的关系。
:主要是模具,注塑车间受模具的影响比较大。
:所以重点要抓自制件模具异常的处理。
曾副总:模具异常得到处理后,计划部门内部的抵抗成了主要矛盾。

:企业方的人员觉得欧博项目组的老师推行的模式能解决问题,但是他们原有的模式同样可以解决问题,只是以前没有做到位而已。以为ERP告诉他们欠什么,就等于他们都知道了,欠料问题就解决了,但是他们不知道ERP发现欠料问题只是一个开始,把欠料追回来的过程才是最麻烦和最艰难的。
:他们原有的排查欠料的模式根据ERP进行,但是他们没想到最关键的问题是,通过ERP发现欠料以后,ERP本身不能帮企业把物料追回来。而企业方的人以为ERP告诉他们欠什么,就等于他们都知道了,欠料问题就解决了,但是他们不知道ERP发现欠料问题只是一个开始,把欠料追回来的过程才是最麻烦和最艰难的。
所以,很多公司以为上了ERP,公司就没问题了,物料就没有问题了。其实, ERP只能发现问题而不能解决问题,没有人的反复排查、检查、跟进、施压,就是知道欠料,也只能眼睁睁看着它,最后只好去调整计划而不是调整前工序的生产。所以,说到底,企业人员经常有认识上的误区,以为有系统模式就能自动解决问题。
:当时企业方坚持按原有的模式做,欧博项目组的老师没办法,只好同意以两周为限,如果异常停工工时增加了就必须按照欧博的要求做。欧博项目组的老师也马上给企业老板打电话,把想法明确说了。当时,企业老板也在犹豫,他不知道到底该不该用欧博的方法,也不知道原有的方式能不能做到。但企业管理人员都反对欧博的做法,这位老板也犹豫了,于是决定让管理人员试一下,并最终同意以两周为限按原有的方式实验一下。结果停工待料工时在8月高达到1507小时,比调研的时候还高。
企业老板看到这个情况,马上痛下决心,停止争论,坚决按欧博老师的要求做,甚至直接将PMC交由欧博老师代管。我们的计划模式算是真正开始执行了。但接下来的事情是否就万事大吉了呢?

:事情讲到这里,我们能看到真相了。其实,任何一种计划模式、排查模式,从技术层面、知识层面来说都不难,大家都能做到、都有能力做到。但阻碍我们的真正障碍来自于哪里呢?来自于我们的习性,来自于我们的随性和自以为是的毛病。克服这种毛病,我们只有坚持,别无他法。
:好了,我们最后把这个案例总结一下,把这个过程梳理得更清晰些。
SS公司这个案例主要讲的是为计划的达成提前所做的物料排查,这里共有五层排查。
第一层排查是提前一个半月进行的月计划排查。例如,3月10日安排4月26日至5月25日这一个月的总装计划,这个计划制订出来后,物控部、仓库就进行排查。他们要排查的内容是:未来要生产的产品的物料情况,采购处于怎样的状态,前车间处于什么状态,还没有采购的物料要安排采购计划,需要自制件的,相应的前车间的生产计划要安排下去。
第二层排查就是提前半个月进行的旬排查。为什么做了月排查还要做旬排查?很简单,因为月排查的东西生产以后,过了一个月,情况发生了变化,我们要继续跟进、跟踪。所以我们在4月12日又要对4月26日至5月5日这10天将要组装的东西进行排查。
4月26日后面要生产的东西还没开始,但已在3月10日做了月排查,又在4月12日进行了旬排查。也就是说,4月26日以后要生产的东西现在已进行了两次排查。那么4月26日要生产的东西还有两层排查,哪两层排查呢?
第三层排查是仓库实物备料的排查。为什么要进行实物备料排查呢?实物备料主要是防止账目上的备料产生误差。因为企业的账物卡准确性不高,所以我们要通过提前的5天仓库实物备料排查,来看还缺哪些物料,以此决定前车间应该怎么办,采购应该怎么办。那么就在4月18日左右进行4月26日至4月31日要总装的产品的物料准备,通过仓库实物备料对物料情况再进行排查。
第四层排查3天实物领料排查。也就是4月22日车间领料的时候,连续3天边领料边排查、边报欠边追欠。仓库把物料发给车间,车间领的时候,要每天领、每天报欠、每天追欠,这是3天实物领料排查。
这些都是在4月26日生产之前进行的一些排查,已有四层排查。还有一层排查,就是根据出货的情况再进行一次排查,这实际上是第五层排查。
我要补充的第一点是,排查的目的主要是发现问题并提前解决问题,然后让4月26日的计划能够准确、顺利地达成。
第二点是我们在企业里实施的动作,看起来都不复杂,但难在人的执行。欧博项目组的老师6月进驻企业,动作推行下去,7月就有了效果,但企业方的人员认为效果是有,但太麻烦,马上集体反对。我记得当时的项目组长特意给我打电话,说企业方一致认为他们原来的方法也不错,我们的动作有效果但太麻烦,企业方要回到他们以前的模式,问我怎么办,我告诉他要坚持、抗住。但企业方的压力太大,最后没办法还是妥协了。结果8月停工待料工时增加,且效率马上降低了。
事实证明,我们的做法麻烦但能解决问题。我经常说,管理其实很简单,但管理很麻烦。简单是什么意思?就是这件事情谁都会做。麻烦是什么意思?就是要一次次反复去做。大家并不是做不到,只是因为跟自己的习惯相矛盾,所以这个时候要过习惯这个坎,要让不习惯变成习惯。
当然,这个过程中还遇到了物控员的一些问题。前面的那位物控员当时撂担子,我们的老师把他的工作担起来,也就是要让他们知道这件事情是可以做到的。我记得这个项目做完以后,这位物控员表现非常好,还非常感谢我们欧博的老师。因为按照我们的方式做了以后,他也发现,排查的工作量并不大,并且的的确确能够解决问题,能够给企业带来效率的提升。所以,我们做管理不要怕麻烦。