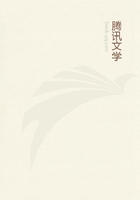
第32章
It is absolutely necessary, then, when workmen are daily given a task which calls for a high rate of speed on their part, that they should also be insured the necessary high rate of pay whenever they are successful.This involves not only fixing for each man his daily task, but also paying him a large bonus, or premium, each time that he succeeds in doing his task in the given time.It is difficult to appreciate in full measure the help which the proper use of these two elements is to the workman in elevating him to the highest standard of efficiency and speed in his trade, and then keeping him there, unless one has seen first the old plan and afterward the new tried upon the same man.And in fact until one has seen similar accurate experiments made upon various grades of workmen engaged in doing widely different types of work.The remarkable and almost uniformly good results from the correct application of the task and the bonus must be seen to be appreciated.
These two elements, the task and the bonus (which, as has been pointed out in previous papers, can be applied in several ways), constitute two of the most important elements of the mechanism of scientific management.They are especially important from the fact that they are, as it were, a climax, demanding before they can be used almost all of the other elements of the mechanism; such as a planning department, accurate time study, standardization of methods and implements, a routing system, the training of functional foremen or teachers, and in many cases instruction cards, slide-rules, etc.(Referred to later in rather more detail on page 129.)The necessity for systematically teaching workmen how to work to the best advantage has been several times referred to.It seems desirable, therefore, to explain in rather more detail how this teaching is done.In the case of a machine-shop which is managed under the modern system, detailed written instructions as to the best way of doing each piece of work are prepared in advance, by men in the planning department.These instructions represent the combined work of several men in the planning room, each of whom has his own specialty, or function.One of them, for instance, is a specialist on the proper speeds and cutting tools to be used.He uses the slide-rules which have been above described as an aid, to guide him in obtaining proper speeds, etc.Another man analyzes the best and quickest motions to be made by the workman in setting the work up in the machine and removing it, etc.Still a third, through the time-study records which have been accumulated, makes out a timetable giving the proper speed for doing each element of the work.The directions of all of these men, however, are written on a single instruction card, or sheet.
These men of necessity spend most of their time in the planning department, because they must be close to the records and data which they continually use in their work, and because this work requires the use of a desk and freedom from interruption.Human nature is such, however, that many of the workmen, if left to themselves, would pay but little attention to their written instructions.It is necessary, therefore, to provide teachers (called functional foremen) to see that the workmen both understand and carry out these written instructions.
Under functional management, the old-fashioned single foreman is superseded by eight different men, each one of whom has his own special duties, and these men, acting as the agents for the planning department (see paragraph 234 to 245 of the paper entitled "Shop Management"), are the expert teachers, who are at all times in the shop, helping and directing the workmen.Being each one chosen for his knowledge and personal skill in his specialty, they are able not only to tell the workman what he should do, but in case of necessity they do the work themselves in the presence of the workman, so as to show him not only the best but also the quickest methods.
One of these teachers (called the inspector) sees to it that he understands the drawings and instructions for doing the work.He teaches him how to do work of the right quality; how to make it fine and exact where it should be fine, and rough and quick where accuracy is not required, the one being just as important for success as the other.The second teacher (the gang boss) shows him how to set up the job in his machine, and teaches him to make all of his personal motions in the quickest and best way.The third (the speed boss) sees that the machine is run at the best speed and that the proper tool is used in the particular way which will enable the machine to finish its product in the shortest possible time.In addition to the assistance given by these teachers, the workman receives orders and help from four other men; from the "repair boss" as to the adjustment, cleanliness, and general care of his machine, belting, etc.; from the "time clerk," as to everything relating to his pay and to proper written reports and returns; from the "route clerk," as to the order in which he does his work and as to the movement of the work from one part of the shop to another; and, in case a workman gets into any trouble with any of his various bosses, the "disciplinarian" interviews him.
It must be understood, of course, that all workmen engaged on the same kind of work do not require the same amount of individual teaching and attention from the functional foremen.The men who are new at a given operation naturally require far more teaching and watching than those who have been a long time at the same kind of jobs.