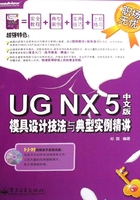
第5章 级进模设计的专业准备知识
级进模(又称连续模、跳步模),是指压力机在一次行程中,依次在模具几个不同的位置上同时完成多道冲压工序的冲模。整个制件的成型是在级进过程中逐步完成的,可使切边、切口、切槽、冲孔、塑性成型、落料等多种工序都在一副模具上完成。级进模可分为普通级进模和多工位精密级进模。
由于用级进模冲压时,冲裁件是依次在几个不同位置上逐步成型的,因此要控制冲裁件的孔与外形的相对位置精度就必须严格控制送料步距。为此,级进模有两种基本结构类型:用导正销定距的级进模与用侧刃定距的级进模。

图9-28 【冲裁组件设计】对话框
5.1 级进模的适用特点
级进模的特点和适用情况如下。
(1)当零件的形状异常复杂,经过冲制后不便于再单独重新定位的零件,采用多工位级进模在一副模具内连续完成最为理想,如椭圆形的零件,小型和超小型零件。
(2)对于形状特殊的零件,在使用简易冲模或复合模无法设计模具或制造模具的情况下,采用级进模却能解决问题。
(3)同一产品上的两个冲压零件,其某些尺寸间有相互关联,甚至有一定的配合关系,在材质、料厚完全相同的情况下,如果用两套模具分别冲制,不仅浪费原材料,而且还不能保证配合精度,若将两个零件合并在一副多工位级进模上同时冲裁,可大大提高材料利用率,并能很好的保证零件的配合精度。
但级进模的造价高,制造周期长,在使用时需要被加工的零件的产量和批量足够大,以便能够比较稳定而持久的生产,实现高速连续作业。同时,制件太大,工位数较多时,模具必然比较大,这时必须考虑到模具和压力机工作台的匹配性。
5.2 成型工艺设计
成型工艺设计中,首先要考虑被加工的零件共分为几个加工工序,各工序的加工内容及工序的优化组合,以及如何对工序组排序。
1.连续冲裁工序排样的基本原则
(1)各工序的先后应按复杂程度而定,一般有利于下道工序的进行为准,以保证制件的精度要求和零件的几何形状的正确。冲孔落料件,应先冲孔,再逐步完成外形的冲裁。尺寸和形状要求高的轮廓应布置在较后的工位上冲切。
(2)当孔到边缘的距离较小,而孔的精度又较高时,冲外轮廓时孔可能会变形,可将孔旁外缘先于内孔冲出。
(3)应尽量避免采用复杂形状的凸模,并避免形状有尖的凸角、窄槽、细腰等薄弱环节。复杂的型孔形应分解为若干个简单的孔形,并分成几步进行冲裁,使模具型孔容易制成。复杂制件的外形可通过多次局部冲裁,最后完成制件的外形要求。
(4)有严格要求的局部内、外形及位置精度要求高的部位,应尽量集中在同一工位上冲出,以避免步距误差影响精度。如果确实在一个工位完成这部分冲制有困难,需分解成两个工位,最好放在两个相邻工位连续冲制。
(5)对于一些在普通低速冲床上冲压的多工位级进模,为了使模具简单、实用、缩小模具体积或由于条件所限,甚至只能用侧刃做定距。为了减少步距的累积误差,凡是能合并的工位,只要模具能保证零件的精度,模具本身有足够的强度,就不要轻易分解、增加工位。尤其对于那些形状不易分解的零件,更不要轻率的增加工位。
(6)分段型切除余料排样中的条料,因冲切加工其强度逐渐变弱,在安排各工位的加工内容时要考虑条料宽度方向的导向。
(7)应保证条料载体与零件连接处有足够的强度与刚度。当冲压件上有大小孔或窄筋时应先冲小孔(短边),后冲大孔(长边)。
(8)凹模上冲切轮廓之间的距离不应小于凹模的最小允许壁厚,一般取为2.5t(t为共建材料厚度),但最小要大于2毫米。
(9)轮廓周边较大的冲切工艺尽量安排在中间工位,以使压力中心与模具几何中心重合。
2.弯曲工序排样的基本原则
(1)对于冲裁弯曲类零件,先冲孔再切除弯曲部位周边的废料进行弯曲,然后再切除其余废料。
(2)接近弯边的孔有精度要求时,应弯曲后再冲,以防止孔变形。
(3)为避免弯曲时载体变形和侧向滑动,对小件可两件组合成对称件弯曲,然后再剖分开。
(4)凡属于复杂的弯曲零件,为了便于模具制造并保证弯曲角度合格,应分解为简单弯曲工序的组合,经逐次弯曲而成,且不可强行一次弯曲成型。要力求用简单的模具结构来弯曲件的形状。对精度要求较高的弯曲件,应以整形工序保证零件质量。
(5)平板毛坯弯曲后变为空间立体形状,毛坯平面应离开凹模面一定高度,以使工序件能在进一步向前送进时不被凹模挡住,这一高度称为送进线高度。送进线高度应尽量小。
(6)对于一个零件的两个弯曲部分有尺寸精度要求时,则弯曲部分应当在同一工位一次成型。这样不仅保证了尺寸精度,而且能够准确的保持成批零件加工后的一致性。
(7)应保证零件弯曲线与材料碾压纹向垂直,当零件在互相垂直的方向或几个方向都要进行弯曲时,弯曲线必须与条料纹向成30°~60°的角度。
(8)尽可能以冲床行程方向作为弯曲方向,若要做不同于行程方向的弯曲加工,可采用斜碶滑块机构,对闭口型弯曲件,也可采用斜口凸模弯曲。
3.拉深工序排样的基本原则
(1)对于有拉深又有弯曲和其他工序的制件,应当先进行拉深,再安排其他工序。这是由于拉深过程中必然有材料的流动,若先安排其他工序,拉深时将使已定型的部位产生变形。
(2)凡属于多次拉深的多工位级进模,由于连续冲压的原因,其拉深工序的安排、拉深系数的选取应以安全稳定为原则。
(3)为了便于连续拉深模在试模过程中调整拉深次数和各次拉深系数的分配,应适当安排几个空位工位,作为预备工位。
(4)拉深件底部带有较大孔时,可在拉深前先冲较小的预备孔,改善材料的拉深性,拉深后再将孔冲至要求的尺寸。
(5)拉深过程中筒形件高度在逐步增加,使各工序件高度不一致,引起了载体变形,影响拉伸件质量。对此,可在每次拉深后设置一空位工位,减少带料的倾斜角度,改善拉深件质量。
4.含局部成型工序排样的基本原则
(1)由局部成型时,可视具体情况将其穿插安排在各工位上进行,在保证产品质量的前提下,有利于减少工位数。
(2)局部成型会引起条料的收缩,使周围的孔变形,因此不应安排在调料边缘区或工序件外形处,局部成型区周围的孔应在成型后再冲。
(3)轮廓旁的鼓包要先成型,以避免轮廓变形。若鼓包中心线上有孔,应在冲压鼓包前先在孔的位置上冲出直径较小的孔,以利于材料从中心向外流动,待压好鼓包后再冲孔到要求的尺寸。
(4)镦形前应将其周边余料适当切除,然后在镦形完成后再安排进行一次精确冲切余料。
5.3 毛坯排样
级进模的步距是确定条料在模具中每送进一次,所需要向前移动的固定距离。毛坯排样即是确定它们的步距。而步距的精度直接影响冲件的精度。设计级进模时,要合理的确定步距的基本尺寸和步距精度,步距的基本尺寸是模具中两相邻工位的距离。级进模任何相邻两工位的距离都必须相等。对于单排列的排样,步距基本尺寸等于冲压件的外形轮廓尺寸和两冲压件间搭边宽度之和,其步距基本尺寸S为:
S=L+M
式中:
L——冲压件外形轮廓尺寸;
M——搭边宽度。
但是,冲压件展开外形在沿送料方向每个冲压件外轮廓的排列往往相互交错。
对于双排或多排排样,可分为以下两种情况:
(1)一种情况是沿送料方向在同一轴线上进行双排或多排排样,则步距基本尺寸为:
S=L+l+2M
式中:
l——制件沿送料方向有一倾斜夹角方位的某个局部外形轮廓尺寸。
(2)另一种情况是与送料方向平行的多排排样,这时可参照对应单排排样考虑确定步距的基本尺寸。
多工位级进模在沿送料方向的冲裁搭边宽度,一般可参照冷冲模搭边值选取。但由于在分段切除余料的过程中是要将这个搭边按余料冲切去,所以在选取最小切除余料宽度时要保证凸模有必要的强度,否则在连续作业的情况下是很危险的。
步距的精度直接影响冲件的精度。步距精度越高,冲件精度也越高,但模具制造也就越困难。所以步距精度的确定必须根据冲压件的具体情况来定。
影响步距精度的因素很多,但归纳起来主要有:冲压件的精度等级、形状复杂程度、冲压件材质和厚度、模具的工位数,冲制时条料的送进方式和定距形式等。
5.4 废料的设计
废料是指连续模冲压时,条料内连接工序件并运载其稳定前进的这部分材料。在排样过程中,废料的设计是非常重要的,不仅决定了材料的利用率,而且关系到制件的精度和冲制效果,更是直接影响模具结构的复杂程度和制造的难易程度。废料与一般冲裁时条料的搭边不尽相同,搭边的作用主要是补偿定位误差,满足冲压工艺的基本要求,保证冲出合格的制件,还可使条料有一定的刚度,便于送进。而条料载体必须有足够的强度,要能够运载条料上冲出的零件,并且能够平稳的送进到后续工位。
废料的强度非常重要。废料发生变形,则整个条料的送进精度就无法保证,严重者会使调料无法送进模具造成事故。因此从保证废料强度出发,废料宽度应远远大于搭边宽度。但条料废料强度的增强,并不能单纯靠增加废料宽度来保证,重要的是要合理的选择废料形式。由于被加工件的形状和工序的要求不同,其废体的形式是各不相同的。废料形式主要有双侧载体、单侧载体、中间载体三种。
1.双侧载体
双侧载体是在条料的两侧设计废料,被加工零件连接在两侧废料的中间。双侧载体是理想的载体,可使工件到最后一个工位前条料的两侧仍保持有完整的外形,这对于送进、定位和导正都十分有利。采用双侧载体送进十分平稳可靠,但材料利用率较低。双侧载体可分为等宽双侧载体和不等宽双侧载体。
(1)等宽双侧载体一般应用于送进步距精度高,条料偏薄,精度要求较高的冲裁件多工位级进模或精度较高的冲裁弯曲多工位级进模。在废料两侧的对称位置可冲出导正销孔,在模具的相应位置设导正销,以提高定位精度。
(2)不等宽双侧载体宽的一侧成为主废料,窄的一侧称为副废料。一般在主废料上设计导正销孔。此时,条料沿主废料一侧的导料板前进。冲压过程中需在中途冲切去副废料,以便进行侧向冲压加工或其他加工。一般在冲切副废料之前应将主要冲裁工序都进行完毕,以确保冲制精度。
2.单侧载体
单侧载体是在条料的一侧设计废料,实现对工序件的运载。导正销孔多放在单侧载体上,其送进步距精度不如双侧载体高。有时可再借用一个零件本身的孔同时进行导正,以提高送进步距精度,防止废料在冲制过程中有微小变形,影响步距精度。与双侧载体相比。单侧载体应取更大的宽度。在冲切过程中,单侧载体易产生横向弯曲,无废料一侧的导向比较困难。
单侧载体一般应用于条料厚度为0.5毫米以上的冲压件,特别是对于零件一端或几个方向带有弯曲,往往只能保持条料的一侧有完整的外形场合,采用单侧载体较多。
在冲裁细长零件时,为了增强废料的强度,并不过分增加废料宽度,仍设计为单侧载体。但在每两个冲压件之间适当位置用一小部分连接起来,以增强调料的强度,称为桥接式载体,其中连接两工序间的部分称为桥。采用桥接式载体时,冲压进行到一定的工位或到最后再将桥接部分冲切掉。还可根据零件的特点设计为全桥接式载体,但必须在不影响零件要求的情况下才能使用。
3.中间载体
中间载体是指废料设计在条料中间,一般适用于对称零件,尤其是两外侧有弯曲的对称零件。它不仅可以节省大量的原材料,还利于抵消由于两侧压弯时产生的侧向力。对于一些不对称的单向弯曲的零件,也可采用中间载体将被加工的零件对称于中间载体排列在两侧,变不对称零件为对称性排列。既提高了生产效率,又提高了材料利用率,也抵消了弯曲时产生的侧向力。
5.5 条料的排样
在连续模设计中,要确定从毛坯板料到产品零件的转化过程,即要确定级进模各工位所要进行的加工工序内容,并在条料上进行各工序的布排,这一设计过程就是条料排样。条料排样的主要内容就是在冲切刃口外形设计的基础上,将各工序内容进行优化组合形成一系列工序组,并对工序组排序,确定工位数和每一个工位的加工工序;确定载体形式与毛坯定位方式;设计导正孔直径与导正销数量;绘制工序排样图。
条料排样图的设计是多工位的级进模设计的重要依据,使决定级进模优劣的主要因素之一。条料排样图设计的好坏直接影响模具设计的质量。条料排样图确定了,则零件的冲制顺序、模具的工位数及各工位内容、材料的利用率、模具步距的基本尺寸和定距方式、条料载体形式、条料宽度、模具结构、导料方式等都得到了确定。排样图设计错误会导致制造出来的模具无法冲制零件。因此,在设计条料排样图时,必须认真分析,综合考虑,进行合理组合和排序,拟出多种方案,加以比较、归纳以确定最佳方案。
在条料排样设计分析时要考虑到以下原则:
(1)要保证产品零件的精度和使用要求及后续工序的冲制需要。
(2)工序应尽量分散,以提高模具寿命,简化模具结构。
(3)要考虑生产能力和生产批量的匹配,当生产能力较生产批量低时,则力求采用双排或多排,使之在模具上提高效率,同时要尽量使模具制造简单,模具使用寿命长。
(4)高速冲压的级进模用自动送料机构送料时,用导正销精确定距。为保证条料送进的步距精度,第一工位安排冲导正孔,第二工位设导正销,在其后的各工位上优先在易窜动的工位设置导正销。
(5)要抓住冲压零件的主要特点,认真分析冲压零件形状,考虑好各工位之间的关系,确保顺利冲压,对形状复杂、精度要求特殊的零件,要采取必要的措施保证。
(6)尽量提高材料利用率,使废料达到最小限度。对同一零件利用多行排列或双行穿插排列,以提高材料利用率。另外在条件允许的情况下,把不同形状的零件合到一副模具进行冲裁,更有利于提高材料的利用率。
(7)适当设置空位工位,以保证模具具有足够的强度,并避免凸模安装时相互干涉,同时也便于试模调整工序时用。
(8)必须注意各种产生条料送进障碍的可能,确保条料在送进过程中通畅无阻。
(9)冲压件的毛刺方向:当零件提出毛刺方向要求时,应保证冲出的零件毛刺方向一致;对于带有弯曲加工的冲压零件,应使毛刺面留在弯曲件内侧;在分段切除余料时,不允许一个冲压件的周边毛刺方向不一致。
(10)要注意冲压力的平衡。合理安排各工序以保证整个冲压加工的压力中心与模具中心一致。
(11)级进模最适宜以成卷的带料供料,以保证能进行连续、自动、高速冲压,被加工材料的力学性能要充分满足冲压工艺的要求。
(12)工件和废料应保证能顺利排出,废料如连续,要增加切断工序。
(13)排样方案要考虑模具加工的设备和条件,考虑模具和冲床工作台的匹配性。
5.6 工艺力的计算
冲压力即冲压变形力,是为使板料产生变形而在模具运动方向所需要施加的力。它是冲压工艺设计中的一个重要参数,是选择设备和设计模具的重要依据。
1.冲压力与模具结构的关系
根据冲压力来选择设备吨位时,冲压力的计算与确定还应该考虑模具的结构类型。
● 单工序模
冲压力即为完成该道工序的工艺变形力。
● 级进模
冲压力是完成各道工序的工艺变形力(包括右废料切刀时的废料切断力)相叠加。
● 复合模
不应简单叠加,而应视具体复合情况分别处理。比如:在冲压行程中同时冲孔和落料的复合模,冲压力为冲孔力与落料力相叠加。而落料拉深复合模时,就不应该把落料力与拉深力叠加起来。因为在使用这类模具的冲压行程中,落料与拉深并不是同时进行,落料在先,拉深在后。
2.压力中心及计算方法
冲压力合力的作用点称为模具的压力中心。为使设备和模具不受偏心载荷,应把压力中心设计在模柄轴线位置上。如果压力中心不在模柄轴线上,设备的滑块就会承受偏心载荷,导致滑块、导轨和模具不正常磨损,降低设备、模具寿命甚至损坏模具。
求模具的压力中心等同于求凹模工作刃口作用力合力的作用点。采用空间平行力系得合力作用线的求解方法,即根据诸分力对某轴力矩之和等于其合力对同轴力矩的力学原理,可以求出压力中心。又因冲压力与工作刃口的周长或直径成正比,故对于简单几何形状之刃口,如圆形、三角形及方形等,其合力中心即为圆心或型芯,很容易确定。而对于形状较复杂的情况,压力中心的计算与确定由计算法(又称解析法)与作图法。
在实际生产中,可能出现冲模压力中心在加工过程中发生变化的情况,或者由于零件的形状特殊,从模具结构考虑不宜于使压力中心与模柄中心线相重合的情况,这时应注意使压力中心的偏离不致超出所选用压力机所允许的范围。
5.7 本章小结
本章重点介绍了级进模具设计方面的专业基础知识,主要内容包括:成型工艺设计、毛坯排样、废料的设计、条料的排样以及工艺力的计算。通过本章学习,读者将了解、熟悉级进模具设计的特点,掌握各种专业原理知识。