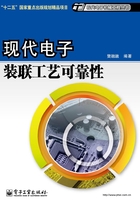
1.2 现代电子装联工艺可靠性
1.2.1 电子装联工艺的变迁和发展
1.电子装联工艺的基本概念
电子装联工艺是将构成产品的各单个组成部分(元器件、机电部件、结构件、功能组件和模块等)组合并互连制成能满足系统技术条件要求的完整的产品过程,也有人习惯将电子装联工艺称为电子组装技术。
电子装联工艺过程通常分两步。第一步完成内部组装,即解决形成各个结构成分和电路元器件布置等的基本问题;第二步完成外部组装,即根据最佳满足各个装置和仪器的使用条件及技术要求来解决成形、组装中的一般问题。
电子设备系统是由若干装配单位逐步积累而成的结构。制作最简单的装配单位的根基是基础元件(电路元件),它是最低的、不可分割的结构等级。基础元件包括通用电路元件或分立元件。在微电子设备中,微型电路也是基础元件。
装配等级由组装单位的尺寸和复杂程度表征。在采用分立元件的电子设备中,结构的最小装配单位是简单的部件、小单元、组件或典型的替换元件,把这样的装配单元称为第一结构层次。当利用微型电路作为基础元件时,第一级结构层次的功能将大为复杂化。微型电路的集成度可以使组装的结构等级变得更高。由第一结构层次的部件装配的分单元、单元是第二结构层次。而第三结构层次等构成单一单元或包括分单元、单元的机架。装在设备的机架(机柜、机箱)上的一组单元,单一单元或一组安装好的机架便构成装置,它是最高装配单位即第四结构层次。
2.微电子设备的基础元件
按照工艺原理,集成电路分为厚膜集成电路、薄膜集成电路和半导体集成电路。当用薄膜集成电路和半导体集成电路组成微电子设备的部件和单位时,微型电路(集成电路)是最小的结构成分而同分立电路一样加以利用,因为它们的元件封装密度高(元件电气上相连),且结构上是一个尺寸可以和分立元件相比拟的统一整体。
当从个别电路集成过渡到整个装置集成时,便可能进一步缩小设备的体积和提高设备的工作速度,这是因为集成电路的可靠性高,故设计制造有高集成度的电子设备在经济上是适宜的。
3.电子装联工艺的变迁和发展
电子设备结构的发展分为5个阶段,或正如人们所说的5代,每一代的特点都体现在基础元件的结构上。在评价电子设备结构的质量或可靠性时,基础元件成为决定性的因素。
●第一代是用电子管和榫接电路元件制成的电子设备;
●第二代是用半导体器件、小型榫接元件和印制布线制成的电子设备;
●第三代是用经封装了的集成电路和印制电路板制成的电子设备;
●第四代是用高集成度的微型电路组件或模块、多层电路板及HDI-PCB制成的电子设备;
●第五代是在内藏无源元件(R、C、L)和有源芯片的基板上再贴装复杂的SoC、SiP、MCM等系统芯片包构成的新封装。
电子设备组装的完善应看成是电子技术和工业生产技术水平所体现的质量发展史,电话、电报通信技术,特别是无线电通信技术则应看成是现代无线电电子技术的起源,而首批工业用真空三极管的出现可称为广泛普及电子设备的起点。
20世纪30年代大批生产的无线电通信和无线电广播用的无线电收发设备中,所采用的无线电元件的外形尺寸大,它们之间用单股铜导线进行电气安装,而元件的固定和接触连接在多数情况下是用可拆卸零件来实现的。零件在底盒内随意布置和电子管的外露安装不要求对元件采取专门的散热措施。当时的组装结构有两大缺点,即工艺性差及可靠性低。
20世纪40年代“指型”电子管、“橡实型”电子管和“弹丸型”电子管的出现,组装密度又获得了明显的提高。在成批生产电阻器(合成可变电阻器、金属膜固定电阻器)和电容器(可变的和固定的金属化纸介电容器与陶瓷电容器)的同时,工业部门还掌握了一些安装电气元件(信号灯头、熔丝座、安装板、连接接线板等)的生产。此时,改进工业用无线电元件(改善参数及缩小外形尺寸)常常是完善电子设备组装的根本途径,但尺寸的缩小是靠提高电路元件的布置密度来实现的。
电子设备复杂性的日益增加,使设备中的电子管和电路元件数目过分地增多。对于一个中等复杂程度的电子系统而言,设备的体积占数十个机架,总重量达数吨,而功耗达数千瓦。它消耗相当大的电能,使设备的内部发热增大,使所用散热系统的重量和体积均已不能适应电子设备组装密度的需要,这对系统的结构设计似乎造成了不可克服的困难。因此,设备的电路和结构设计的完善性决定了整个设备系统的工作可靠性。进一步要求缩小体积,减小重量,降低功耗,是提高可靠性和改善工艺性的根本出路。
20世纪50年代随着大批量生产半导体器件和印制板安装技术的全面掌握,微小型化成了电子设备组装发展的新方向。
20世纪60年代薄膜技术和半导体材料的发展为制作厚膜和薄膜集成电路及半导体集成电路奠定了基础。随着微电子学的发展,结构设计方法也发生了变化。假如在制作第一、二代电子设备时为了减小设备的外形尺寸、减轻重量和降低成本而力求减少各级电路、电子管和其他电路元件的数量,那么,在第三代和第四代电子设备中则力求无限制地增加等效电路元件的数量,也就是无限制地提高集成度。因为电子元件的外形尺寸已大大减小,重量和相对成本已显著降低,而它们的可靠性也得到了明显的提高。
1.2.2 现代电子装联工艺可靠性问题的提出
现代电子装联工艺可靠性问题是伴随着微电子封装技术和高密度组装技术的发展而不断积累起来的。
(1)在由大量分立元器件构成的分立电路时代,电路的功能比较单一。产品预期的主要技术性能和可靠性特性主要由设计的质量和完善性所决定。产品的制造难度也并不很高,由于组装的空间比较大,焊点形状比较单一,焊点数也不是太多,因此,装联工艺可靠性并不占有特别的地位。
(2)随着电子产品复杂程度的不断增加,各种小型化元器件和小规模的IC器件在各种类型的收音机、录音机、录放像机、通信机、雷达、制导系统、电子计算机及宇航控制设备等中大量应用。因此,此阶段电子设备复杂程度的显著标志是所需的元器件数量大量增加。一般说来,电子设备所用的元器件数量越多,其可靠性问题就越严重,为保证设备或系统能可靠地工作,对元器件可靠性的要求就非常突出、非常苛刻。
(3)随着世界经济发展的国际化,电子设备的使用环境日益严酷,从实验室到野外,从热带到寒带,从陆地到深海,从高空到宇宙空间,经受着不同的环境条件的考验。温度、湿度、海水、盐雾、冲击、振动、宇宙粒子、各种辐射等对电子元器件所构成的综合影响导致产品失效的可能性增大。因此,设计加固技术越来越重要,甚至构成了确保电子设备系统在严酷环境中工作可靠性的关键因素。
(4)随着现代半导体封装技术的日新月异的发展,多芯片封装(SoP)、系统级封装(SiP)、多芯片模块(MCM)等的应用,使得电子设备技术全面跨入了第四代,如图1.5所示。

图1.5 半导体封装技术的发展
各种超大规模的模组化芯片封装技术不断涌现,诸如:
① SoC:把多种芯片的电路集成在一个大的硅圆片上,导致由单个小芯片级封装转向硅圆片级封装。
② SiP:把多个芯片置于单一封装中,构成系统级封装。各芯片通过三维堆叠封装集成在一起,实现较高的性能密度和集成度。SiP还允许无源元件和其他元件(如滤波器和连接器)在同一个封装中集成。SiP的最终目标是在一个封装体内组装入系统的整个功能,这样有利于小型化、薄型化和轻量化,具有开发周期短,交货期快等特点,提高了电气特性,降低了噪声和耗电,如图1.6所示。

图1.6 半导体封装的系统化动向
③ MCM:20世纪90年代初随着LSI设计技术和工艺技术的进步,以及深亚微米技术和微细化芯片尺寸等技术的应用,即将多个LSI芯片组装在一个多层布线的外壳内,形成了MCM多芯片封装器件。近年来,MCM技术通过FOP(堆叠封装)的形式,将2~4个裸片装在球栅阵列封装基板上,出现了多芯片模块(MCM),如图1.7所示。

图1.7 三维安装芯片包(POP)
过去所说的MCM是指在一块基板上组装多个半导体芯片和元器件,近些年来半导体制造商开始由供应组装了多个芯片的存储器转向供应组装有多个芯片的SiP。
SoC、SiP、MCM模组化微芯片技术的应用,导致了传统的电路设计技术发生了历史性的变革,设计和工艺的技术界限越来越模糊了。传统的电路设计技术功能越来越退化(未来的电路设计功能更多地是选用合适的芯片级功能模块及其接口类型),而微组装工艺技术却得到了极大的发展。未来电子装备的可靠性越来越取决于微电子组装工艺技术的发展。例如:
●SiP使用的技术要素最基本的是CSP中所使用技术的组合。
●作为新加入的要素技术是芯片薄化加工技术、芯片积层技术、芯片积层中的互连技术。
●SiP安装形态目前包括:在印制板上平面配置芯片的形态(主要使用BGA),在印制板上直接积层芯片的形态(主要使用CSP),最近也使用了倒装芯片连接方式。
●芯片堆叠最具经济效益的是4~5个芯片的堆叠。“聚合物中芯片”工艺不采用金丝球焊,而是将芯片减薄后嵌入到薄膜或聚合物基中,如图1.8所示。

图1.8 三维安装接合断面及熔化状态
(5)电子设备的安装密度不断增加。从第一代电子管进入第二代晶体管,后又从小、中规模集成电路进入到大规模和超大规模集成电路,电子产品正朝小型化、微型化,立体化封装方向发展。其结果导致装置安装密度的不断增加,从而使内部温升增高,散热条件恶化。而电子元器件将随环境温度的增高,降低其可靠性,因而元器件(特别是功率芯片)的可靠性引起了人们的极大重视。
(6)将无源元件R、C、L(甚至IC裸芯)内藏于PCB基板中,然后再将未封装的IC芯片或IC封装贴装或绑接到内藏无源元件的基板表面,完成全部组装过程,如图1.9所示。

图1.9 前后并行的组装模式雏型
HDI-PCB技术、内藏元器件基板技术,以及SoP、SiP及MCM等的结合,驱动了电子设备技术迈入了第五代。它改变了传统的由前决定后的串行组装模式,而迈入了前后并行的微组装模式的新时代。传统的产品可靠性管理和评估模式将面临着严重的挑战。由于有源和无源芯片封装的高集成化,系统安装的高密度化和立体化,焊接点的微细化和不可视化,导致了微组装工艺可靠性问题将变得异常突出。
1.2.3 现代电子装联工艺可靠性的研究对象和现实意义
1.现代电子装联工艺技木的划界及其可靠性
1)电子装联工艺技木的划界
电子装备技术从20世纪20年代末开始应用以来已经历了80余年的发展,跨越了4个发展阶段,现进入了第五个发展时代。从产品后工序(装联工序)本身的技术发展态势来看,其所经历的发展阶段,大致可用图1.10来描述。

图1.10 电子装联工艺技术的划代
2)现代电子装联工艺技术的内涵
从图1.10所示电子装联工艺技术的划代来看,现代电子装联工艺技术的内涵主要是以PCB板级组装为对象。图1.11示出了在现代电子设备中典型的板级组装的安装层次。

图1.11 系统板级组装层次
随着电子设备和安装技术高密度化程度的不同,具体的安装层次也有所差异。例如,将未封装的IC裸芯片直接搭载在PCB上时(裸芯片安装),在IC片内导体图形的配线是最精密的,最前端的IC布线间的间距(L/S)约为0.09μm。但是,当由多个IC、LSI及其他元器件等集合构成超精密图形连线时,它还不能成为人们能操作的系统。只有最终配上键盘、开关等后才能达到人们能操作的尺寸,此时布线的间距就可能扩大了上万倍。
3)现代电子装联工艺可靠性的研究对象
随着高密度面阵列封装器件(μBGA、CSP、FCOB等)和微型元器件(0201、01005、EMI等)在工业中的大量应用,“微焊接”技术对高密度组装的可靠性的影响越来越大。其特点是:
●由于焊点的微细化,人手不可能直接接近,基本上属于一种“无检查工艺”。因此,必须要建立确保焊点接触可靠性的保证系统(对制造系统的要求)。焊点内任何空洞、异物等都会成为影响接续可靠性的因素(对接合部构造的要求)。
●在再流过程中由于热引起的BGA、CSP或PCB基板的变形翘曲均会导致焊点钎料空缺,并把大量残留应力留在钎料连接上,造成早期故障。因此,研究芯片封装和PCB在再流焊接过程中的变形规律及其抑制措施,对提高产品的可靠性有着特殊的意义。
●在封装芯片与基板的二级互连微焊接过程中,控制其冶金物理过程,以确保生成的金属间化合物层(也称合金层或IMC)的厚度和成分均在焊点可靠性要求的范围之内。
●在已焊好的BGA、CSP球阵封装的二级互连微焊接焊点中,为避免在应用过程中因IMC层厚度及金相组织发生变异,导致微焊点因可靠性蜕变而失效,研究和掌握其蜕变机理及其对策,对延长焊点的工作寿命有重大的现实意义。
●研究微焊点在各种恶劣环境中工作的可靠性问题及其加固措施。
●分门别类地深入研究各类芯片封装的微焊点与PCB焊盘互连工艺的优化,及其对焊点可靠性的影响程度。
●研究组装工作环境因素对微焊点可靠性影响的统计学规律。
●研究球阵封装芯片二级互连焊盘的表面处理类型,对“微焊点”焊接质量及可靠性蜕变的诱导作用。
●焊盘设计:包括形状、大小和掩膜界定,对于可制造性和可测试性(DFM/DFT),以及满足制造成本和可靠性等方面的要求都是至关重要的。
●推进“微焊接工艺设计”。所谓“微焊接工艺设计”,就是用计算机模拟焊接接合部的可靠性设计,从而获得实际生产线的可靠性管理措施和控制项目;对生产线可能发生的不良现象进行预测,从而求得预防不良现象发生原因。
●0201、01005元件的推出,蜂窝电话制造商就把它们与CSP一起组装到电话中,PCB尺寸由此至少减小一半,间距可小至100μm。处理这类封装相当麻烦,要减少后工艺缺陷(如桥接和立碑)的出现,焊盘尺寸优化和元器件间的间距是关键。
2.研究现代电子装联工艺可靠性的现实意义
电子组装的可靠性依赖于各个元器件的可靠性,以及这些元器件界面间的力学、热学及电学的可靠性。这些接触界面,表面贴装焊接层不但提供了电气连接,还提供了电子元器件到PCB基板的机械连接,同时还有元器件严重发热时的散热功能。一个单独的焊点很难说可靠还是不可靠,但是电子元器件通过焊点连接到PCB上时,这个焊点就变得唯一了,也就具有了可靠性的意义。
钎料中的晶粒结构本来就是不稳定的。SnPb钎料的重结晶温度是在其共晶温度之下的。晶粒尺寸随着时间的增加而增大。晶粒结构的生长减少了细晶粒的内能。这种晶粒的增长过程是随着温度的升高及在循环载荷中输入的应变能的增加而增强的。晶粒的生长过程到达某个特定点,便会显露出累积疲劳损伤的迹象。这种迹象在对焊点进行加速试验时,比焊点在工作环境中使用时表现得更为明显。
污染物,像铅的氧化物及助焊剂残留物,绝大多数滞留在晶粒的边界处。随着晶粒的生长,这些污染物的浓度在晶粒边界处增长,因此会延缓晶粒的生长。当其消耗掉钎料约25%的疲劳寿命后,在晶粒边界的交叉处就可以看到微空穴;当消耗掉约40%的疲劳寿命后,微空穴变成微裂痕;这些微裂痕相互聚结形成大裂痕,最后会导致整个焊点的断裂。
焊点常常连接的是特性不相同的材料,导致整体热膨胀不匹配。作为主要材料的钎料,在特性上与焊接结构材料有很大的不同,导致局部热膨胀不匹配。热膨胀不匹配的严重性以及由此造成的可靠性隐患,依赖于电子组装工艺的设计参数和工作使用环境。
当今国内外由制造因素导致的电子产品失效中,约有80%是出自焊接的质量问题。而在焊点的失效中,面阵列封装器件(如BGA、CSP、FCOB等)焊点的失效又占整个焊接质量缺陷的80%左右。显然解决面阵列封装器件(如BGA、CSP、FC0B等)的焊点失效问题,是改善现代电子产品制造质量和工作可靠性的重中之重。