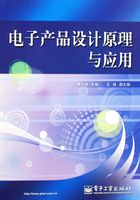
1.3 电子设备的设计与生产过程
电子设备的寿命周期可分为4个阶段:构思与初步设想、设计与研制、制造与生产及运行与维修。由前3个阶段可体现出产品的制造费用和用户的购置费用,最后1个阶段则体现了产品的使用价值,即产品的使用效果和使用期。用户的要求是以最低的购置费用在尽可能长的时间内得到可靠的使用效果,产品设计制造者的目标应是最大限度地满足用户的要求,达到产品的性能指标,并符合其使用条件。
1.3.1 电子设备设计制造的依据
(1)产品的性能指标
产品性能指标包括电性能指标和机械性能指标,前者主要有电信号幅度的标量(如灵敏度和输出功率等)、电信号频率的标量(如频率的精度和准确度和稳定度等)和电信号的波形标量(如调制度、非线性失真和噪声抑制等);后者主要有各类移动、旋动及传动的精度(如随动系统的跟踪度、定位系统的精度和细度等)及其结构强度。此外,不同产品尚有一些特殊的性能指标及运输和储存条件。
(2)产品的环境条件
产品的环境条件主要指气候条件、机械作用力条件、化学物理条件(如金属的腐蚀、非金属的老化、酸碱粉尘、盐雾侵蚀及生物霉菌等)和电磁污染条件(各种干扰信号的侵入和辐射)。
(3)产品的使用要求
产品的使用要求主要包括对产品体积、重量、操作控制和维护的要求。
(4)产品可靠性和寿命要求
产品可靠性和寿命要求主要包括产品的无故障工作时间长,承受过负荷的能力强。
(5)产品制造的工艺性和经济性要求
产品制造的工艺性和经济性要求既易于组织生产又造价低廉。设计应根据产品的用途性质(军用、民用、高可靠性及一般可靠性)、使用场合和产品自身的级别,参照国内、外同类型先进产品型号,进行设计方案的论证;应致力于性能价格比的提高,不要盲目追求高性能和高精度指标,使得制造工艺复杂,成本增高。
1.3.2 电子设备设计制造的任务
1.预研究阶段
预研究工作的任务是在产品设计前突破复杂的关键技术课题,为确定设计任务书、选择最佳设计方案创造条件;或根据电子技术发展的新趋向,寻求把近代科学技术的成果应用于产品设计的途径,有计划地研究新结构、新工艺和新理论,以及采用新材料和新器件等先行性技术课题,为不断在产品设计中采用新技术,创造出更高水平的新产品奠定基础。该阶段的工作,一般按拟定研究方案和试验研究两道程序进行。
(1)拟定研究方案
拟定研究方案是为了明确目的,确定研究工作方向和途径,其主要工作内容有:①搜集国内、外有关技术文献、情报资料,必要时调查研究实际使用中的技术要求;②编制研究任务书,拟定研究方案,提出专题研究课题,明确其主要技术要求;③审查、批准研究任务书和研究方案。
(2)试验研究
试验研究是为了通过研究探索工作解决关键技术课题,得出准确数据和结论。在试验研究中,应善于利用现有的技术基础进行新的科学试验,善于利用模拟或代用的方法取得试验数据。主要内容有:①对已确定各专项研究课题进行理论分析和计算,探讨解决的途径,减少盲目性;②设计和制造试验研究需要的零件、部件、整件及必要的专用设备和仪器;③展开试验研究工作,详细观察、记录和分析试验的过程与结果,掌握第一手资料。④整理试验研究的各种原始记录,进行全面分析,编写预先研究工作报告。
当预研究工作结束时,应达到的目标是:出具整理成册的各种试验数据记录、各项专题的试验研究报告等原始资料,以及预研究报告书。
2.设计性试制阶段
凡自行设计或测绘试制的产品,一般都要经过设计性试制阶段。其任务是根据批准的设计任务书,进行产品设计,编制产品设计文件和必要的工艺文件,制造样机,并通过对样机全面试验,检查鉴定产品的性能,从而肯定产品设计与关键工艺。一般工作程序如下所述。
(1)论证产品设计方案,下达设计任务书
其主要工作内容有:①搜集国内、外有关产品的设计、试制、生产的情报资料及样品;②调研使用的需要情况及实际使用中的技术要求和经验,确定试制产品目标;③会同使用部门编制设计任务书草案,提出产品设计方案,论证主要技术指标,批准下达设计任务书。
(2)进行初步设计和理论计算
其主要工作内容有:①进行理论计算,按计算结果,对产品或整个体系的各个部分合理分配参数;②通过必要的试验,进一步落实设计方案,提出线路、结构及工艺技术关键的解决方案;③编制初步设计文件;④对需用的人力、物力进行概算。
(3)进行技术设计
技术设计的主要工作有:①根据对技术指标的修正意见,进一步调整分配产品的部分参数;②拟定标准化综合要求;③编制技术设计文件;④对结构设计进行工艺性审查,制定工艺方案。
(4)进行样机制造
样机制造的主要工作有:①编制产品设计工作图纸与必要的工艺文件;②设计制造必要的工艺装置和专用设备;③通过试验掌握关键工艺和新工艺;④制造零部件、整件与样机;⑤对样机进行调整,进行性能试验和环境试验,对是否可提交现场试验做结论。
(5)现场试验与鉴定
主要工作有:①现场试验检查产品是否符合设计任务书规定的主要性能指标与使用要求,通过试验编写技术说明书;②组织鉴定,对能否设计定型作出结论。
(6)设计性试制结束时应达到的条件
设计性试制工作结束时,应达到下列条件:①具备产品设计方案的论证报告、初步设计文件和技术设计文件;②具备产品设计工作图纸及技术条件;③具备产品工艺方案及必要的工艺文件;④具备整理成册的各种试验的原始资料、试验方法与规程;⑤具备必要的专用工艺装置、设备及其设计图纸;⑥具备结构的工艺性审查报告、标准化审查报告及产品的技术经济分析报告;⑦具备一定数量的样机及现场试验报告;⑧具备产品需要的原材料、协作配套件及外购件汇总表。
3.生产性试制阶段
(1)主要内容
生产性试制主要内容有:①修改产品设计文件,修改与补充生产工艺文件;②培训人员,调整工艺装置,组织生产线,补充设计制造工艺装置和专用设备;③按照设计文件和工艺文件,使用工艺装置和专用设备制造零件并进行装配和调试,考查各种文件及装置的适用性及合理性;④做好原始记录,统计分析各种技术定额;⑤拟定正式生产时的工时及材料消耗定额,计算产品劳动量及成本。
(2)生产性试制工作结束应达到的条件
生产性试制结束应达到下列条件:①具备修改过的产品设计文件及工艺文件;②具备满足成批生产需要的工艺装置、专用设备及其设计图纸;③根据需要,选定标准样机与样件;④初步确定成批生产时的流水线和劳动组织;⑤具有符合技术条件的小批量生产产品,提出产品成本概算。
4.产品的鉴定与定型
鉴定的目的在于对一个阶段工作作出全面的评价和结论。在审查时,一般应邀请使用部门、研究设计单位和有关单位的代表参加。重要产品的鉴定结论应报上级机关批准。
① 申请设计定型的产品其主要性能稳定,经现场试验(或试用)符合设计指标和使用要求,主要配套产品和主要原料可在国内解决,具备了规定的产品设计文件和技术条件;
② 申请生产定型的标准是具备生产条件,生产工艺经过中、小批量考验,生产的产品性能稳定,产品经试验后符合技术条件,具备生产与验收的各种技术文件。
1.3.3 整机制造的内容和顺序
(1)原材料和元器件检验
理化分析和例行试验工厂为保证产品质量,对进厂的原材料、辅助材料和外购元器件都要进行入厂质量检验。例如,原材料的理化分析,关键(或主要)元器件的例行试验。这些工作由检验部门根据供应部门提供的元器件和原材料进行。
(2)主要元器件的老化
筛选是剔除早期失效的元器件和提高元器件的上机率,对主要元器件(特别是半导体器件)应进行老化筛选,其主要内容有高低温冲击、高温储存及带电负荷等。
(3)零件部制造
电子整机所用的零件分通用零件(包括标准零件)和专用零件两种。一般通用零件和标准零件都是外购,专用零件则由本厂自制。民用电子产品的专用零件数量不多,而军用和专用电子产品的专用零件数量较多。因此,整机厂都具有一定的机械加工设备和技术力量,特别是模具制造力量。
(4)通用工艺处理
它包括对已制造好的零件、机箱、机架、机柜、外壳、印制板、旋钮和度盘等,进行电镀、油漆、丝网漏印、化学处理及热处理加工,以便提高这些零件的耐腐蚀性,并增强外观的装饰性。
(5)组件装校
一般专用组件的装校都由专业车间进行,也可由总装车间承担。无论采取哪种方式,其目的都是使组件具有完整的独立功能。组件装配完毕之后,须对其进行调整和测试,以求得性能达标。
(6)总装
总装包括总装前的准备、总装流水、调试、负荷试验和检验包装。
① 准备加工在流水线生产和调试以前进行。先将各种原材料和元器件等进行加工处理的工作称为预加工(装配准备)。某些不便在流水线上操作的器件,由于事先做了预加工也可减少在流水线上安排的困难。典型的预加工包括导线的剪切、剥头及浸锡,元器件引脚的剪切、浸锡及预成形、插头座连接、线扎的制作、标记打印、高频电缆,以及金属隔离线的加工等。
② 总装流水整机总装是在装配车间(亦称总装车间)完成的。总装应包括电气装配和结构安装两大部分,而电子产品则是以电气装配为主导、以其印制电路板组件为中心而进行焊接和装配。流水作业操作是目前电子产品总装的主要形式。由于采用传送板或传送带顺序移动加工产品,极大地提高了劳动效率。
③ 一般在产品总装完成后都要进行调试和负荷试验,调试和负荷的时间和方式根据产品而定。
④ 根据技术条件和使用要求,在总装完成后必须进行检验和必要的例行试验,将完全符合标准的产品再包装和入库。