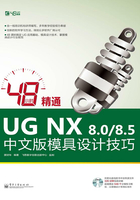
第4部分 模具种类与结构
模具按照成型材料的不同可分为不同的种类,如金属成型模具、陶瓷成型模具、玻璃成型模具、塑料成型模具等。其中塑料成型模具占有很大比重,同时也是本书研究的重点。下面将上述列举的模具种类与结构一一作简要介绍。
课堂讲解——模具种类与结构
课时区间1:金属成型模具
常见的金属成型模具有冲压模具、锻压模具、挤压模具、压铸模具等。
1. 冲压模具
冲压模具按工艺性质可分为冲裁模具、弯曲模具、拉深模具、成型模具和立体压制模具;按模具的导向方式可分为导柱模具、导板模具、导筒模具和无导向模具;按机械化程度可分为手工操作模具、半自动模具和全自动模具。
冲压模具的结构由两部分组成,即上模部分和下模部分。
如图1-11所示为典型的冲裁模具,如图1-12所示为典型的连续级进冲压模具。

图1-11 典型冲裁模具

图1-12 连续级进冲压模具
2. 压铸模具
压铸模具是用在压铸机上生产压铸件的永久模具,如图1-13所示为顶杆顶出机构压铸模具。

图1-13 顶杆顶出机构压铸模具
3. 挤压模具
用于铸锭塑性变形,使之成为具有一定形状和尺寸要求的工艺装置。挤压模具有型胚模具和型材模具之分。
如图1-14所示为型材模具。

图1-14 型材挤压模具
4. 锻压模具
锻压模具是实现模锻工艺的工艺装置。模锻工艺是金属毛胚在外力作用下发生变形充满模膛,获得所需形状、尺寸并具有一定机械性能的模锻件的锻造生产工艺,如图1-15所示为典型的阀体锻压模具。

图1-15 阀体锻压模具
课时区间2:陶瓷成型模具
陶瓷是以天然或人工合成的无机非金属物质为原料,经成型和高温烧结而制成的固体材料和制品。陶瓷模具由于成型方法繁多,因此种类也比较多。按成型方法,陶瓷模具可分为可塑成型模具、注浆成型模具、压制成型模具、特种成型模具等,模具种类主要根据胚料性能和含水量来进行选择。按材质可分为石膏模具、新型多孔模具、金属模具等。
典型的陶瓷压制成型模具如图1-16所示。

图1-16 陶瓷压制成型模具
课时区间3:玻璃成型模具
玻璃成型方法可分为两种:人工成型和机械成型。人工成型方法是一种原始的成型方法,它需要制造者有丰富的经验和熟练的操作手法,至今仍然在使用。如今占主导地位的机械成型法使玻璃制品的成型实现了机械化,一般空心制品的成型机多以压缩空气或液压为动力。
如图1-17所示为用人工吹制法制造空心玻璃瓶的过程。

图1-17 人工吹制成型过程
用于玻璃制品成型的工艺装置,称为玻璃成型模具。按成型方法分,玻璃模具可分为压制模具、吹制模具和混合成型模具,如图1-18所示为典型的瓶罐类机械吹制模具。

图1-18 瓶罐类机械吹制模具
课时区间4:塑料成型模具
塑料成型模具的种类较多,主要有塑料注射成型模具、塑料压缩成型模具、热固性塑料的传递成型模具、挤塑成型模具、塑料吹塑成型模具及热成型模具等。
1.塑料注射成型模具
塑料注射成型模具的分类方法较多,按塑料件所用的材料,可分为热塑性塑料注射成型模具和热固性塑料注射成型模具;按塑料注射机的类型,可分为卧式、立式和直角式注射模具;按其在塑料注射机上的安装方式,可分为移动式注射模具和固定式注射模具;按模具的型腔数量,可分为单型腔塑料注射模具和多型腔塑料注射模具。通常塑料注射成型模具是按其总体结构上的某些特征进行分类的,如图1-19所示。

图1-19 塑料注射成型模具的基本组成
塑料注射成型模具有若干典型结构,分别如下。
● 单分型面塑料注射模具:单分型面塑料注射模具也称为二板式塑料注射模具,如图1-20所示是塑料注射模具最简单的一种,由动模和定模构成。其型腔一部分设在动模上,一部分设在定模上,主流道设在定模上,分流道和浇口设在分型面上,开模后塑件连同流道凝料一起留在动模一侧。动模一侧设有推出机构,用以推出塑件及流道凝料。这类模具的特点是结构简单,对塑件成型的适应性很强,应用十分广泛。

图1-20 塑料注射模具基本结构
1—定模板;2—导套;3—导柱;4—型腔;5、17—推板;6—定位圈;7—浇口套;8—凸模;9—水道;10、21、23—销钉;11、22、24—螺钉;12—水嘴;13—凸模固定板;14—垫板;15—支块;16—推杆;18—推杆固定板;19—盖板;20—密封垫;25—动模板
● 多分型面注射模具:多分型面注射模具是对有两个以上分型面的注射模具的统称。这类模具可分为双分型面模具和三分型面(包括垂直分型面和水平分型面)注射模具,以双分型面注射模具最为常见。双分型面塑料注射成型模具又称为三板式塑料注射成型模具,如图1-21所示。双分型面塑料注射成型模具用途广泛,主要用于设点浇口的单型腔或多型腔注射模具、侧向分型抽心机构设在定模一侧的注射模具及因塑件结构特殊需要顺序分型的注射模具。

图1-21 多分型面塑料注射模具基本结构
1—定模板;2—导柱;3、5—双联导套;4—活动模板;6—镶件;7—定位圈;8—浇口套;9—点浇口废料;10—分流锥;11—分浇口套;12—镶件固定板;13、23、29—销钉;14、30—螺钉;15—拉板螺钉;16—水嘴;17—大型腔;18—型心固定板;19—动模垫板;20—橡皮密封圈;21—压板;22—推板;24—推杆;25—螺母;26—托簧板;27—弹簧;28—塑料制品;31—支块
多分型面注射模具与单分型面注射模具相比,在动模和定模之间增加了一个可移动的活动模板4(又称浇注板),其浇注系统凝料和制品一般是从不同分型面上取出。开模时,活动模板4与定模板1首先沿A-A分型面定距分型,其分型距离由定距拉板螺钉15控制,以便取出这两块板之间的浇注系统凝料。随着开模的继续,沿B-B面分型,然后在注射机推出机构作用下,连接推杆24推动塑件从型芯上脱出。闭模时,A-A和B-B分型面自动闭合,推板22在弹簧27的作用下复位,完成一次注射过程。
● 带有活动镶块的注射模具:塑件带有内侧凸、凹槽或螺纹,在模具上需要设置活动型芯、螺纹型芯、型环或哈夫块等,这种注射模具就称为带有活动镶块的注射模具,如图1-22所示的模具,塑件内壁带有凸台,模具采用活动镶块9成型。开模时,塑件与流道凝料同时留在活动镶块9上,同动模一起运动,当模具的动模与定模打开一定距离后,注射机上的顶出机构推动推板 1,从而推动推杆 3,使模具的活动镶块9随同塑件一起推出模外,然后用手工或其他装置使塑件与镶块分离。再将活动镶块重新装入动模,在镶块装入动模前推杆3由于弹簧4的作用已经复位。型芯座8上的锥孔(面)保证镶块定位准确可靠。

图1-22 带有活动镶块的注射模具
● 自动卸螺纹注射模具:当成型带有内、外螺纹的塑件时,模具可采用自动卸螺纹装置,如图1-23所示。在模具结构设计中,设置可转动的螺纹型芯和螺纹型环,利用注射机的往复运动或旋转运动,或设置专门的驱动装置(如电机、液压马达及传动装置)与模具连接,开模后带动螺纹型芯或型环转动,使塑件脱出。螺纹型芯的旋转由注射机开合模的丝杆带动,使其与塑件分离。为了防止螺纹型芯与制品一起旋转,一般要求塑件外形具有防转结构,自动卸螺纹注射模具就是利用塑件顶面的凸出图案来防止塑件随着螺纹型芯转动而转动,以便塑件与螺纹型芯分开。开模时,在A-A分型面处先分开,与此同时,螺纹型芯7由注射机的开合螺杆带动而旋转,从而开始拧出塑件(塑件设计时,开合螺杆的螺距大于制品螺纹的螺距),此时B-B分型面也随螺纹型心的拧出而分型,塑件暂时还留在型腔内不动。当螺纹型芯在制品内尚有一个螺距时,定距螺钉4拉着支撑板5,使分型面B-B加速打开,塑件即被带出凹模。继续开模,塑件全部脱离型芯和凹模。

图1-23 自动卸螺纹注射模具
1—推板;2—推秆固定板;3—推杆;4—弹簧;5—支架; 1—定模座板;2—衬套;3—动模板;4—定距;6—支架;7—动模板;8—型芯座;9—活动镶块;5—支撑板;6—支架;7—螺纹型芯;8—注射机合模螺杆10—导桩;11—定模座板(型腔)
● 侧向分型抽芯的注射模具:当塑件带有侧孔或侧凹时,在机动抽芯分型的模具里设有斜导柱、斜滑块或哈夫块等侧向分型抽芯机构,如图1-24所示的模具主要用于成型有侧孔或内凹的塑件,哈夫块的运动方向与模具开模方向垂直。开模时,固定在定模板2上的斜导柱3作用于哈夫块4,使哈夫块4外移,并脱离塑件5的环形槽。与此同时,注射机的顶出系统顶动推板17,推板17推动推杆14,将型腔镶件固定板10顶起,使塑件5脱离型芯8。

图1-24 侧向分型抽芯的注射模具
1—楔紧块;2—定模板;3—斜导柱;4—哈夫块;5—塑料制品;6—定位圈;7—浇口套;8—型芯;9—型腔镶块;10—型腔镶件固定板;11—水嘴;12—动模固定板;13—支块;14—推杆;15—型芯固定板;16—动模垫板;17—推板
● 定模设置推出机构的注射模具:有时因塑件的特殊要求或受塑件形状的限制,开模后塑件将留在定模上。由于注射模具的顶出机构位于模具的动模一边,所以注射模具的推出机构宜设在动模一侧,开模后让塑件留在动模内,以便脱出塑件。当塑件留在定模上时,则应在定模一侧设置推出机构,如图1-25所示为塑料衣刷注射模具,由于塑件形状特殊,开模后塑件留在定模上。在定模一侧设置推件板 7,开模时由设在动模一侧的拉板8带动,使塑件从型芯11上拉脱下来。

图1-25 定模设置推出机构的注射模具
1—支架;2—支撑板;3—成型镶件;4、6—螺钉;5—动模板;7—推件板;8—拉板;9—定模板;10—定模座板;11—型芯;12—导柱
● 无流道注射模具:在成型过程中,使用无流道注射模具(又称无流道凝料注射模具),可使模具浇注系统中的塑料始终保持熔融状态,这是一种成型后只需取出塑件而无流道凝料的注射模具,如图1-26所示为无流道注射模具。塑料从喷嘴21进入模具后,在流道中给以加热保温,使其仍保持熔融状态,每一次注射完毕,只有型腔内的塑料冷凝成型,没有流道冷凝料,取出塑件后又可继续注射,这就大大节省了塑料用量,提高了生产效率,有利于实现自动化生产,保证塑件质量。但无流道注射模具结构复杂,造价高,模温控制要求严格,因此仅适用于大批量生产。

图1-26 无流道注射模具
1—动模座板;2、13—垫板;3—推板 ;4—推杆固定板;5—推杆;6—支撑板;7—导套;8—动模板;9—型芯;10—导柱;11—定模板;12—凹模;14—二级喷嘴;15—热流道板;16—加热器孔;17—定模座板;18—绝热层;19—主流道衬套;20—定位圈;21—喷嘴
2.塑料压缩成型模具
压缩成型过程实际上是热固性塑料进一步缩聚、交联固化的过程。在模具中进行缩聚反应时,需要对模具加热,加热温度一般为180~200℃。最初的压缩模具是每模一腔,先把模具加热,然后把原料放入模具的凹模内,用凸模加压、加热,使原来为粉状或颗粒状的原料熔化、流动、聚合而硬化。所用的压机为手动螺杆压机或简单的液压机,压机上装有电加热板,把模具装料后放入压机中加压。这种原始的模具形式称为手工操作移动式模具,精度低,寿命不长,劳动强度大。
塑料压缩成型模具可分为移动式模具、有卸模架的移动式模具、固定式模具、半固定式模具等。
● 移动式模具:如图1-27所示为移动式模具,结构最为简单,但现在已经很少应用,只用于试验及新产品试制的场合,正式生产中已几乎被淘汰。

图1-27 移动式压缩模具
1—上模板;2—上凸模固定板;3—上凸模;4—型腔套;5—型芯;6—下凸模;7—手柄;8—下凸模固定板;9—螺钉;10—下模板
● 有卸模架的移动式模具:移动式模具在脱模时比较困难。在小批试制中可以改用如图1-28所示的带卸模架的移动式模具。在脱模时,用卸模架把塑件脱出。

图1-28 有卸模架的移动式模具
1—上模体;2—下模体;3—底板 ;4—卸模架
● 固定式模具:固定式模具是把上模连同加热板固定在普通压机的动梁上,下模固定在工作台上。脱模时,由压机的下推杆通过推板机构把塑件脱出凹模,如图1-29所示。

图1-29 固定式模具
1—上加热板;2—上模板;3—调整板;4—下加热板5—导柱;6—导套;7—下模板;8—尾轴;9—调整钉;10—顶板;11—推杆固定板;12—支撑板;13—推杆;14—型腔;15—导套;16—凸模;17—导柱
● 半固定式模具:上模固定在压机上,下模增设一组导轨,把工作台接长。装料时,把下模沿导轨拉出,压缩时推进、定位。脱模时,可以在装料位置上用卸模架或其他卸模工具,脱出塑件。
3.传递成型模具
传递成型也称为压注成型,是用于热固性塑件模塑加工的又一重要方法,用于传递成型的模具,称为传递模具俗称挤胶模。
在传递成型过程中,先将塑料原料置于加料室内经初步受热塑化后,通过压机驱动压料柱塞施压。熔料在高温高压下转变成黏流态,并以一定速度通过浇注系统进入封闭的模腔内,经保温保压后,塑料发生交联固化,当达到最佳性能时,开模取出制件。
典型的柱塞式传递模具如图1-30所示,它分为上模、下模和柱塞三部分。加料腔为一圆筒,设在上模的中央。开模时制件与浇注系统连在一起,从上、下模之间的分型面取出。

图1-30 柱塞式传递模具
1—压料柱塞;2—加料腔;3—上凹模;4—上模底板;5—上模板;6—下模板;7—下凹模;8—加热板;9—推杆;10—支架;11—下模底板;12—压机模板;13—挡钉;14—推板;15—推杆固定板;16—支柱;17—型芯;18—浇注系统
4.挤塑成型模具
挤塑成型模具,也叫挤出成型机头或模头,属塑料制品成型加工的又一大类重要装备。挤塑是将塑料喂入挤塑机料斗,并进入旋转的螺杆与机筒之间进行输送、压缩、熔融、塑化、定量,通过处于挤塑机头部的模具和定型装置,生产连续型材的加工工艺过程。
挤塑模具可分为棒材模、管材模、平缝模、线缆包覆模、型胚模等,如图1-31所示为无分流锥棒材模具的典型结构,棒材模具通常由成型模和定型模两部分组成。

图1-31 无分流锥棒材模具
1—锥形环;2—螺栓孔;3—口模体;4—加热圈;5—流道体;6—栅板;7—流道法兰;8—机筒法兰;9—连接螺钉;10—机筒;11—螺杆
5.吹塑成型模具
热塑性塑料的吹塑是一种中空制品成型的方法,它用来成型各种工业及日常生活用品,如瓶、桶、双壁箱和双壁座椅等。吹塑成型由两个步骤构成,即用挤塑或注塑的方法成型型胚和用压缩空气再辅以其他机械力吹胀型胚,使它紧贴于型腔壁,并迅速地冷却定型为制品。
中空吹塑模具的整体结构可分为两种类型:组合式结构和镶嵌式结构,如图1-32所示为典型的镶嵌式中空吹塑模具。

图1-32 镶嵌式中空吹塑模具
1—模口嵌件;2—模体;3—排气槽;4—模底嵌件;5—导柱;6—堵头
6.热成型模具
热成型方法虽然很多,相应的模具也各异,但就成型压力来看,主要来自片材两面的压力差。这种压力既可由真空形成,也可由压缩空气达到。由抽真空形成负压的热成型模具,简称为吸塑成型模具。将压缩空气吹入模腔形成正压的热成型模具,简称为压空成型模具。
如图1-33所示为带型刃的压缩空气热成型模具。面板4既是吹气板也是加热板,闭模时将片材夹住,从型腔内通入低压空气,使塑料片紧贴面板加热软化,然后改由上方通入0.8MPa的经预热的空气使制品成型。塑件冷却定型后加热板下降,切除余料再吹气脱模。

图1-33 带型刃的压缩空气热成型模具
1—压缩空气管;2—加热板;3—热空气室;4—面板;5—空气孔;6—底板;7—通气孔;8—工作台;9—型刃;10—加热棒